What is a VFD Schematic?
A VFD schematic is a diagram that represents the electrical connections and components of a Variable Frequency Drive. It provides a visual representation of how the various parts of the VFD are interconnected and how they function together. A VFD schematic is essential for understanding the operation of a VFD and for troubleshooting any issues that may arise.
Components of a VFD Schematic
A typical VFD schematic consists of the following main components:
- Rectifier: Converts AC input power to DC power
- DC Bus: Stores the DC power from the rectifier
- Inverter: Converts the DC power back to AC power with variable frequency and voltage
- Control Circuit: Manages the operation of the VFD and interfaces with external controls
- Output Filter: Removes high-frequency harmonics from the output waveform
Here is a table summarizing the main components of a VFD schematic:
Component | Function |
---|---|
Rectifier | Converts AC input to DC |
DC Bus | Stores DC power |
Inverter | Converts DC to variable frequency AC |
Control Circuit | Manages VFD operation |
Output Filter | Removes high-frequency harmonics |
Types of VFD Schematics
There are several types of VFD schematics, each with its own unique features and applications. The most common types of VFD schematics are:
1. Pulse Width Modulation (PWM) VFD Schematic
PWM VFDs use a fixed DC bus voltage and vary the output frequency and voltage by modulating the width of the output pulses. PWM VFDs are the most common type of VFD and are used in a wide range of applications, from small fans to large industrial motors.
2. Current Source Inverter (CSI) VFD Schematic
CSI VFDs use a variable DC bus current and a fixed output frequency. They are typically used in high-power applications, such as large compressors and pumps, where a constant output frequency is required.
3. Voltage Source Inverter (VSI) VFD Schematic
VSI VFDs use a variable DC bus voltage and a fixed output frequency. They are similar to CSI VFDs but are more commonly used in medium-power applications, such as conveyors and mixers.
4. Matrix Converter VFD Schematic
Matrix converter VFDs do not have a DC bus and instead use a matrix of Bidirectional Switches to directly convert the input AC power to output AC power with variable frequency and voltage. Matrix converter VFDs are relatively new and are used in applications where a compact size and high efficiency are required.
Here is a table comparing the different types of VFD schematics:
Type | DC Bus | Output Frequency | Output Voltage | Typical Applications |
---|---|---|---|---|
PWM | Fixed | Variable | Variable | Small to large motors |
CSI | Variable current | Fixed | Variable | High-power motors |
VSI | Variable voltage | Fixed | Variable | Medium-power motors |
Matrix Converter | None | Variable | Variable | Compact, high-efficiency applications |
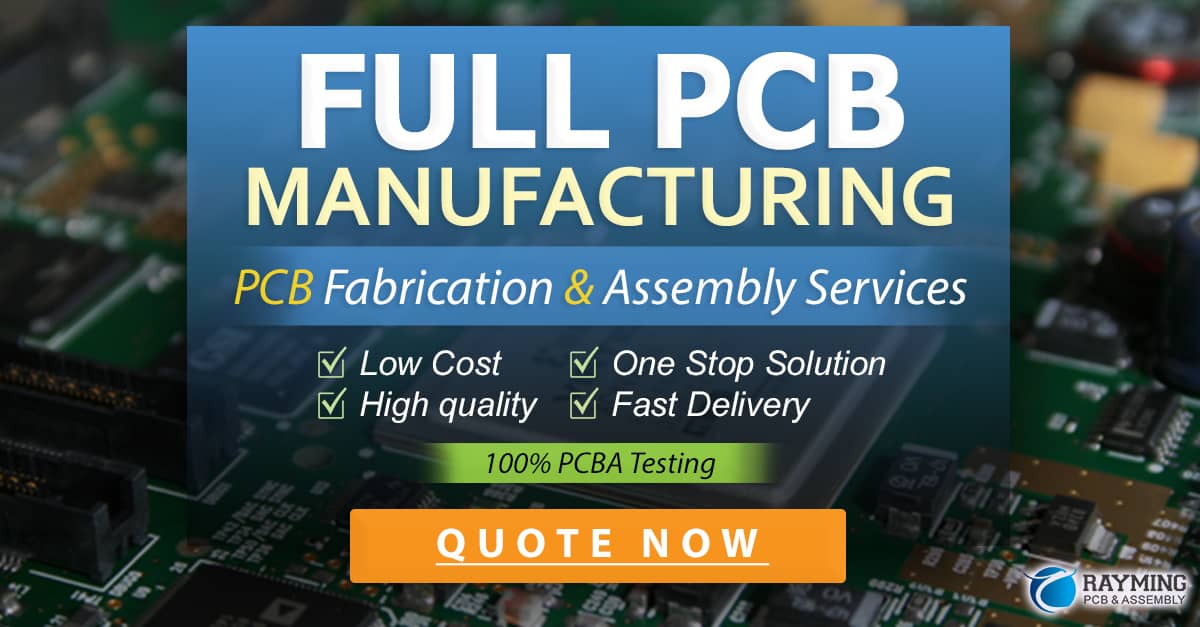
How to Build a VFD
Building a VFD from scratch can be a complex and time-consuming process, but it can also be a rewarding learning experience. Here are the basic steps to build a simple PWM VFD:
- Design the power circuit, including the rectifier, DC bus, and inverter
- Select the appropriate components, such as diodes, capacitors, IGBTs, and gate drivers
- Design the control circuit, including the microcontroller, sensors, and user interface
- Assemble the components on a printed circuit board (PCB) or breadboard
- Write the firmware for the microcontroller to generate the PWM signals and control the VFD
- Test and debug the VFD using a motor and a load
- Optimize the performance and efficiency of the VFD by tuning the parameters and adding features such as overcurrent protection and soft starting
Here is a table summarizing the steps to build a VFD:
Step | Description |
---|---|
1 | Design power circuit |
2 | Select components |
3 | Design control circuit |
4 | Assemble components |
5 | Write firmware |
6 | Test and debug |
7 | Optimize performance |
Example VFD Schematic
Here is an example schematic of a simple PWM VFD:
[Insert VFD schematic diagram here]
This schematic shows the main components of the VFD, including the rectifier (D1-D4), DC bus capacitors (C1-C2), inverter IGBTs (Q1-Q6), gate drivers (U1-U3), and microcontroller (U4). The input AC power is rectified by the diode bridge and filtered by the capacitors to create a smooth DC bus voltage. The microcontroller generates PWM signals to drive the IGBTs, which switch the DC bus voltage to create a variable frequency and voltage AC output. The gate drivers provide isolation and amplification of the PWM signals to ensure reliable switching of the IGBTs.
FAQ
1. What is the difference between a VFD and a soft starter?
A VFD and a soft starter are both used to control the starting and stopping of AC motors, but they work in different ways. A soft starter gradually ramps up the voltage applied to the motor during starting to reduce the inrush current and torque, while a VFD can control the speed and torque of the motor during both starting and continuous operation by varying the frequency and voltage of the power supply.
2. Can a VFD be used with any type of motor?
VFDs are designed to work with AC induction motors, which are the most common type of motor used in industrial applications. However, VFDs can also be used with other types of motors, such as permanent magnet synchronous motors (PMSMs) and brushless DC motors (BLDCs), with some modifications to the control algorithm.
3. What are the advantages of using a VFD?
Using a VFD to control an AC motor has several advantages, including:
- Energy savings by controlling the speed and torque of the motor to match the load requirements
- Smooth starting and stopping of the motor, reducing mechanical stress and increasing equipment lifetime
- Improved process control by allowing precise speed and torque regulation
- Reduced maintenance costs by eliminating mechanical speed control devices such as gearboxes and clutches
4. What are the disadvantages of using a VFD?
Some of the disadvantages of using a VFD include:
- Higher initial cost compared to other motor control methods
- Increased complexity and potential for failure due to the additional electronic components
- Potential for electromagnetic interference (EMI) and harmonics to affect nearby equipment
- Need for proper grounding and shielding to ensure reliable operation and prevent damage to the VFD and motor
5. How do I select the right VFD for my application?
Selecting the right VFD for your application involves considering several factors, such as:
- The type, power rating, and voltage of the motor
- The speed and torque requirements of the load
- The environmental conditions, such as temperature, humidity, and altitude
- The available power supply and required input/output voltages and frequencies
- The required control features, such as serial communication, PID control, and safety functions
It is recommended to consult with a VFD manufacturer or supplier to determine the best VFD for your specific application and to ensure proper installation and configuration.
Conclusion
VFD schematics are essential diagrams that represent the electrical connections and components of a Variable Frequency Drive. Understanding VFD schematics is crucial for designing, troubleshooting, and maintaining VFD systems. There are several types of VFD schematics, each with its own unique features and applications, including PWM, CSI, VSI, and matrix converter VFDs. Building a VFD from scratch can be a complex process, but it can also be a rewarding learning experience. By following the basic steps and using the right components and tools, it is possible to create a functional and efficient VFD for a wide range of applications.
0 Comments