In the electronics industry, the terms “PCB assembly” and “PCB manufacturing” are often used interchangeably, but they actually refer to distinct processes within the overall PCB (Printed Circuit Board) production cycle. Understanding the difference between these two processes is crucial for effective communication, project planning, and ensuring successful electronic product development.
This comprehensive guide will delve into the intricacies of PCB assembly and PCB manufacturing, exploring their definitions, steps involved, and the key differences between them. By the end of this article, you will have a clear understanding of these processes and their significance in the electronics manufacturing ecosystem.
What is PCB Manufacturing?
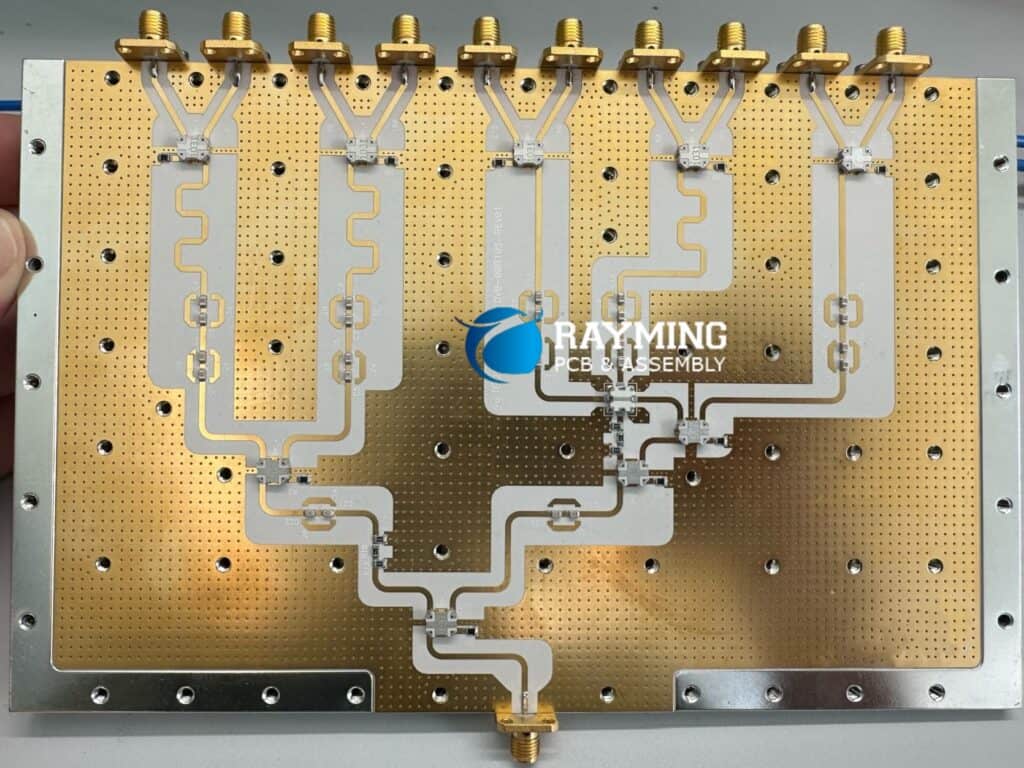
PCB manufacturing, also known as PCB fabrication, is the process of creating the bare printed circuit board itself. It involves transforming a PCB design into a physical entity by selectively depositing conductive materials onto a non-conductive substrate, typically a fiberglass-reinforced epoxy laminate.
The PCB manufacturing process consists of several steps, each playing a critical role in ensuring the quality and functionality of the final product. Here’s a breakdown of the key stages involved:
1. Design and Data Preparation
The PCB manufacturing process begins with the design phase, where the electronic circuit is laid out using specialized computer-aided design (CAD) software. The resulting design files, commonly known as Gerber files, contain all the necessary information about the layers, traces, pads, and drill holes required for fabrication.
2. Tooling and Panelization
Once the design files are ready, they undergo a tooling process, which involves creating production tools like photoplots or direct imaging tools. Additionally, the design is panelized, meaning multiple PCB images are arranged on a single panel to optimize material usage and production efficiency.
3. Inner Layer Imaging and Etching
In this stage, the individual inner layers of the PCB are fabricated. The layer patterns are imaged onto a copper-clad laminate using photolithography or direct imaging techniques. The unwanted copper is then etched away, leaving behind the desired circuit patterns.
4. Lamination and Drilling
The imaged and etched inner layers are stacked together with prepreg (pre-impregnated composite materials) and pressed under high temperature and pressure to form a solid laminated core. Next, the laminated core undergoes a drilling process to create the necessary holes for component mounting and layer interconnections.
5. Outer Layer Imaging and Etching
Similar to the inner layers, the outer layer patterns are imaged and etched onto the laminated core’s surface, creating the final copper circuit patterns.
6. Plating and Surface Finishing
To enhance conductivity and facilitate component mounting, the drilled holes are plated with conductive materials, typically copper or tin-lead. Additionally, various surface finishes, such as solder mask, silkscreen, and surface finishes (e.g., ENIG, HASL), are applied to protect the copper traces and provide visual references for component placement.
7. Electrical Testing and Inspection
Before shipping the bare PCBs, they undergo rigorous electrical testing and inspection processes to ensure compliance with design specifications and quality standards. This includes testing for short circuits, open circuits, and other potential defects.
The PCB manufacturing process is highly specialized and requires sophisticated equipment, skilled personnel, and strict quality control measures. The final output of this process is a bare printed circuit board, ready for the next stage: PCB assembly.
What is PCB Assembly?
PCB assembly, also known as PCB population or board stuffing, is the process of mounting and soldering electronic components onto the bare printed circuit board. It is the bridge between the physical PCB and the fully functional electronic product.
The PCB assembly process typically involves the following steps:
1. Component Preparation
Before assembly, the necessary electronic components (e.g., resistors, capacitors, integrated circuits) are procured and prepared for mounting. This may involve processes like component sorting, kitting, and labeling.
2. Solder Paste Printing
A stencil is aligned with the bare PCB, and solder paste is applied onto the component pads through the stencil apertures. This step ensures that the correct amount of solder paste is deposited in the right locations for component attachment.
3. Component Placement
Using highly automated pick-and-place machines or manual assembly techniques, the electronic components are precisely placed onto the PCB, adhering to the solder paste deposits.
4. Reflow Soldering
The assembled PCB is passed through a reflow oven, where the solder paste melts and solidifies, creating permanent electrical and mechanical connections between the components and the PCB pads.
5. Inspection and Testing
After soldering, the assembled PCBs undergo various inspection and testing processes to verify proper component placement, solder joint integrity, and functional performance. This may include visual inspections, automated optical inspection (AOI), in-circuit testing (ICT), and functional testing.
6. Conformal Coating (Optional)
In certain applications, such as harsh environments or high-reliability products, a conformal coating may be applied to the assembled PCB to protect it from moisture, contaminants, and environmental stresses.
7. Final Assembly and Packaging
Depending on the product requirements, additional assembly steps may be performed, such as attaching heat sinks, installing connectors, or enclosing the PCB in a suitable housing or enclosure. Finally, the assembled product is packaged and prepared for shipping.
The PCB assembly process requires specialized equipment, trained personnel, and strict quality control measures to ensure reliable and consistent product quality. The output of this process is a fully assembled and functional electronic product, ready for deployment or integration into larger systems.
Key Differences between PCB Manufacturing and PCB Assembly
While PCB manufacturing and PCB assembly are closely related processes, there are several key differences between them:
Aspect | PCB Manufacturing | PCB Assembly |
---|---|---|
Process | Creating the bare printed circuit board | Mounting and soldering components onto the bare PCB |
Output | Bare PCB | Fully assembled and functional electronic product |
Expertise | Requires specialized knowledge in PCB fabrication techniques and materials | Requires expertise in component handling, soldering processes, and assembly techniques |
Equipment | Utilizes specialized PCB manufacturing equipment (e.g., drilling machines, plating lines, imaging systems) | Employs assembly equipment (e.g., pick-and-place machines, reflow ovens, AOI systems) |
Quality Control | Focuses on dimensional accuracy, layer registration, and electrical integrity | Emphasizes proper component placement, solder joint quality, and functional testing |
Materials | Primarily deals with PCB substrates, copper foils, and surface finishes | Handles electronic components, solder pastes, and conformal coatings |
Facility Requirements | Requires clean room environments and specialized chemical handling | Requires ESD-controlled environments and temperature/humidity control |
Supply Chain | PCB manufacturers typically work with PCB designers and OEMs | Assembly houses work with PCB manufacturers and component suppliers |
It’s important to note that while these processes are distinct, they are interdependent and complementary. PCB manufacturing provides the foundation for PCB assembly, and the assembled product’s functionality and reliability depend on the quality of both processes.
In some cases, PCB manufacturers may offer assembly services as well, providing a one-stop solution for both bare PCB fabrication and assembly. Conversely, some assembly houses may have in-house PCB manufacturing capabilities for prototyping or low-volume production.
Frequently Asked Questions (FAQs)
- Can I manufacture and assemble PCBs myself? While it is possible to manufacture and assemble PCBs on a small scale or for prototyping purposes, it is generally not recommended for large-scale production or complex designs. Both PCB manufacturing and assembly processes require specialized equipment, skilled personnel, and strict quality control measures to ensure reliability and consistency. Unless you have the necessary resources and expertise, it is advisable to outsource these processes to professional PCB manufacturers and assembly houses.
- Can the same company handle both PCB manufacturing and assembly? Yes, some companies offer integrated solutions that cover both PCB manufacturing and assembly services. These companies typically have separate facilities or production lines dedicated to each process. By working with a single provider, you can streamline the supply chain and benefit from improved communication and coordination between the manufacturing and assembly teams.
- What factors should I consider when choosing a PCB manufacturer or assembly house? When selecting a PCB manufacturer or assembly house, consider factors such as their expertise and experience in your specific product or industry, quality control measures, certifications (e.g., ISO, IPC), production capabilities (e.g., layer count, component handling), lead times, pricing, and customer support. Additionally, evaluate their ability to handle your desired production volume, whether it’s prototyping, low-volume, or high-volume manufacturing.
- Can PCB assembly be automated or done manually? Both automated and manual PCB assembly processes are common in the industry. Automated assembly, which utilizes pick-and-place machines and reflow ovens, is typically faster and more consistent for high-volume production. However, manual assembly may be preferred for low-volume or prototype runs, or for products with unique or irregular component shapes or placements. Many assembly houses offer both automated and manual assembly services to cater to different product requirements.
- How important is testing and inspection in PCB assembly? Testing and inspection are critical steps in the PCB assembly process to ensure product quality and reliability. Thorough inspections and functional testing help identify defects, such as incorrect component placement, solder joint issues, or functional failures, before the products are shipped. Neglecting these steps can lead to costly rework, product failures, and customer dissatisfaction. Reputable assembly houses prioritize testing and inspection to maintain high quality standards and deliver reliable products.
Conclusion
Understanding the distinction between PCB manufacturing and PCB assembly is essential for effective communication, project planning, and successful electronic product development. While PCB manufacturing focuses on creating the bare printed circuit board itself, PCB assembly involves mounting and soldering electronic components onto the bare PCB to create a fully functional product.
These processes require specialized expertise, equipment, and quality control measures to ensure the reliability and functionality of the final product. While they are distinct processes, they are interdependent and complementary, with the quality of the assembled product relying on the precision and accuracy of both PCB manufacturing and assembly.
By recognizing the key differences between these processes and their respective requirements, you can make informed decisions when selecting PCB manufacturers and assembly houses, streamline your supply chain, and ensure successful electronic product development and manufacturing.
Remember, effective communication and collaboration between all stakeholders involved in PCB manufacturing and assembly are crucial for achieving high-quality, reliable, and cost-effective electronic products that meet your design specifications and market demands.
0 Comments