Introduction to PCB Assembly
Printed Circuit Board (PCB) assembly is a crucial process in the manufacturing of electronic devices. It involves the placement and soldering of electronic components onto a PCB to create a functional circuit. There are two main types of PCB assembly: Surface Mount Technology (SMT) and Through Hole Technology (THT). In this article, we will focus on Through Hole PCB Assembly, its advantages, disadvantages, and the process involved.
What is Through Hole PCB Assembly?
Through Hole PCB Assembly, also known as Through Hole Technology (THT), is a method of assembling electronic components onto a PCB by inserting the component leads through holes drilled in the board and soldering them to pads on the opposite side. This technique has been used for decades and is still widely used today, especially for larger components and in applications where mechanical strength is important.
Advantages of Through Hole PCB Assembly
-
Mechanical Strength: Through hole components are physically secured to the board by their leads, which provides excellent mechanical strength and durability. This makes through hole assembly ideal for applications that are subject to vibration, shock, or other physical stresses.
-
Ease of Repair: Through hole components are easier to replace or repair than surface mount components. The leads can be desoldered and removed without damaging the board or nearby components.
-
Visual Inspection: Through hole solder joints are visible on both sides of the board, making visual inspection easier and more reliable than with surface mount assembly.
-
Compatibility with Older Components: Many older electronic components are only available in through hole packages, making through hole assembly necessary for certain applications.
Disadvantages of Through Hole PCB Assembly
-
Size and Weight: Through hole components are generally larger and heavier than surface mount components, which can be a disadvantage in applications where space and weight are critical factors.
-
Higher Cost: Through hole assembly typically requires more manual labor and specialized equipment than surface mount assembly, which can increase the overall cost of production.
-
Limited PCB Real Estate: The holes required for through hole components take up valuable space on the PCB, limiting the number of components that can be placed on a given board size.
-
Slower Assembly Speed: Through hole assembly is generally slower than surface mount assembly, as each component must be inserted and soldered individually.
The Through Hole PCB Assembly Process
The through hole PCB assembly process involves several steps, each of which must be performed with precision and care to ensure a high-quality finished product.
Step 1: PCB Design and Fabrication
The first step in the through hole PCB assembly process is the design and fabrication of the PCB itself. This involves creating a schematic diagram of the circuit, laying out the components and traces on the board, and generating the necessary files for manufacturing. The PCB is then fabricated using a variety of processes, including etching, drilling, and plating.
Step 2: Component Preparation
Before the components can be assembled onto the PCB, they must be prepared for insertion. This typically involves cutting and forming the component leads to the proper length and shape, and possibly applying a coating or finish to improve solderability.
Step 3: Component Insertion
Once the components are prepared, they are inserted into the holes on the PCB. This can be done manually or using automated insertion machines, depending on the volume and complexity of the assembly.
Step 4: Soldering
After the components are inserted, they are soldered to the pads on the opposite side of the board. This is typically done using a wave soldering machine, which applies molten solder to the entire board in a single pass. Alternatively, selective soldering or hand soldering may be used for smaller or more complex assemblies.
Step 5: Cleaning and Inspection
After soldering, the assembled PCB is cleaned to remove any flux residue or other contaminants. It is then inspected visually and/or using automated optical inspection (AOI) equipment to ensure that all solder joints are properly formed and that there are no defects or missing components.
Step 6: Testing and Finishing
Finally, the assembled PCB is tested to verify that it functions as intended. This may involve functional testing, in-circuit testing, or other methods depending on the complexity and requirements of the circuit. After testing, the PCB may undergo additional finishing processes such as conformal coating, potting, or labeling before being packaged and shipped to the customer.
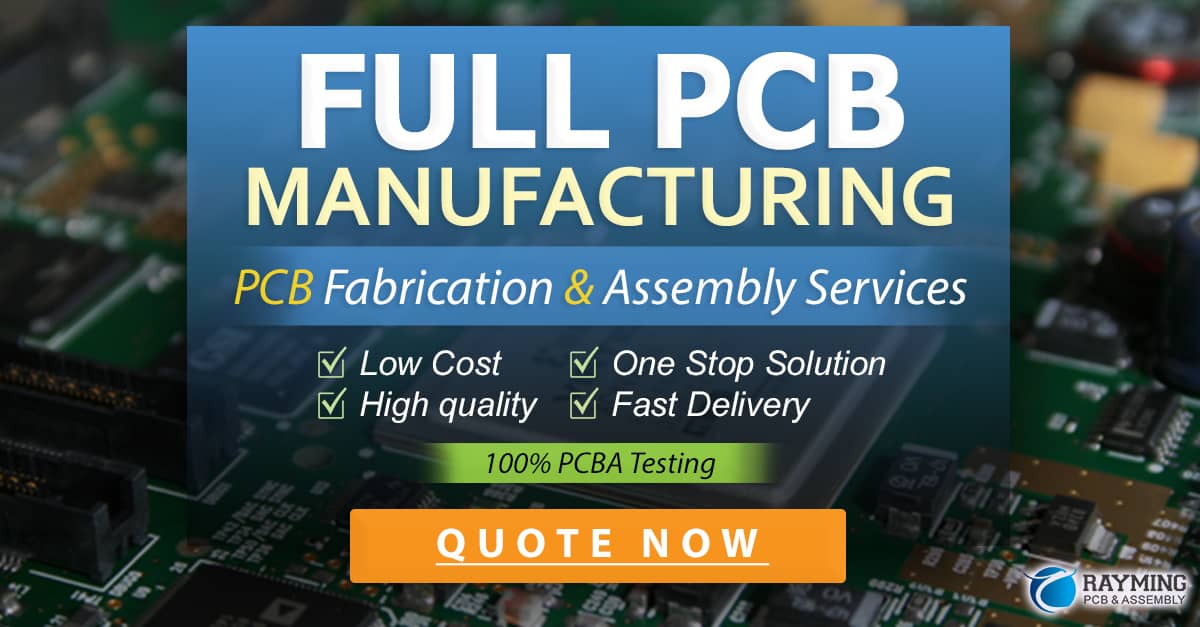
Factors Affecting Through Hole PCB Assembly Quality
There are several factors that can affect the quality and reliability of through hole PCB assemblies. These include:
-
Component Quality: The quality of the components used in the assembly can have a significant impact on the overall quality and reliability of the finished product. It is important to use components from reputable suppliers and to ensure that they meet the necessary specifications and quality standards.
-
PCB Quality: The quality of the PCB itself is also critical to the success of the assembly. The board must be properly designed and fabricated, with clean, well-defined holes and pads, and no defects or contaminants that could interfere with the soldering process.
-
Soldering Process: The soldering process must be carefully controlled to ensure that the solder joints are properly formed and that there are no defects such as bridging, insufficient fill, or cold joints. This requires careful selection of solder alloy, flux, and process parameters such as temperature and dwell time.
-
Cleaning and Inspection: Proper cleaning and inspection are essential to ensure that the assembled PCB is free of contaminants and defects that could affect its performance or reliability. This may require specialized equipment and trained personnel to perform effectively.
-
Handling and Storage: Proper handling and storage of the assembled PCBs is also important to prevent damage or contamination that could affect their quality or reliability. This may include the use of static-dissipative materials, moisture-barrier packaging, and controlled storage environments.
Applications of Through Hole PCB Assembly
Through hole PCB assembly is used in a wide variety of applications across many industries. Some common examples include:
-
Aerospace and Defense: Through hole assembly is often used in aerospace and defense applications where high reliability and durability are critical. Examples include avionics, communications equipment, and military vehicles.
-
Medical Devices: Through hole assembly is also used in many medical devices, such as patient monitors, diagnostic equipment, and surgical instruments, where reliability and safety are paramount.
-
Industrial Equipment: Through hole assembly is commonly used in industrial equipment such as process control systems, automation equipment, and test and measurement devices, where ruggedness and long-term reliability are important.
-
Consumer Electronics: Although surface mount assembly is more common in modern consumer electronics, through hole assembly is still used in some applications such as power supplies, audio equipment, and certain types of connectors.
Conclusion
Through hole PCB assembly is a widely used and proven method for assembling electronic components onto printed circuit boards. While it may not be as fast or space-efficient as surface mount assembly, it offers several advantages in terms of mechanical strength, ease of repair, and compatibility with older components. By understanding the through hole assembly process and the factors that affect its quality and reliability, engineers and manufacturers can ensure that their through hole assemblies meet the necessary performance and durability requirements for their intended applications.
Frequently Asked Questions (FAQ)
1. What is the difference between through hole and surface mount PCB assembly?
Through hole assembly involves inserting component leads through holes drilled in the PCB and soldering them to pads on the opposite side, while surface mount assembly involves placing components directly onto pads on the surface of the board and soldering them in place. Through hole assembly is generally stronger and easier to repair, while surface mount assembly is faster, more space-efficient, and better suited to high-volume production.
2. Can through hole and surface mount components be used on the same PCB?
Yes, it is possible to use both through hole and surface mount components on the same PCB, in a process known as mixed assembly. This can be useful in situations where certain components are only available in through hole packages, or where the mechanical strength of through hole assembly is required for certain parts of the circuit.
3. What are some common defects that can occur in through hole PCB assembly?
Some common defects that can occur in through hole PCB assembly include insufficient hole fill, bridging between adjacent solder joints, cold solder joints, and component misalignment or damage. These defects can be caused by issues with the PCB design, component quality, soldering process, or handling and storage of the assembled boards.
4. How can the quality and reliability of through hole PCB assemblies be improved?
There are several ways to improve the quality and reliability of through hole PCB assemblies, including:
- Using high-quality components from reputable suppliers
- Ensuring that the PCB is properly designed and fabricated with clean, well-defined holes and pads
- Carefully controlling the soldering process to ensure proper joint formation and minimize defects
- Implementing effective cleaning and inspection procedures to detect and correct any issues
- Using proper handling and storage procedures to prevent damage or contamination of the assembled boards
5. What are some emerging trends in through hole PCB assembly?
While through hole assembly is a mature technology, there are still some emerging trends and innovations in this area. These include the use of advanced soldering techniques such as selective soldering and laser soldering, the development of new solder alloys and fluxes for improved performance and reliability, and the integration of through hole assembly with other manufacturing processes such as 3D printing and embedded components. As electronic devices continue to evolve and become more complex, through hole assembly will likely remain an important tool in the PCB assembly toolkit for many years to come.
0 Comments