Why is PCB Testing Important?
PCB testing is essential for several reasons:
-
Quality Assurance: Testing helps identify defects, short circuits, open circuits, and other issues that may affect the PCB’s performance.
-
Reliability: Thorough testing ensures that the PCB will function as intended, even under varying environmental conditions and over an extended period.
-
Cost Savings: Detecting and fixing issues early in the manufacturing process saves time and money by avoiding costly rework or product recalls.
-
Compliance: PCB testing helps ensure that the board meets industry standards and regulations, such as IPC (Institute of Printed Circuits) and UL (Underwriters Laboratories).
Types of PCB Testing
There are various types of PCB tests, each focusing on different aspects of the board’s functionality and quality. Some of the most common types include:
1. Visual Inspection
Visual inspection is the first step in PCB testing, where technicians examine the board for any visible defects, such as:
- Incorrect component placement
- Solder bridges or Cold Solder Joints
- Damaged or missing components
- Contamination or foreign objects
This process can be done manually or using automated optical inspection (AOI) systems.
2. Automated Optical Inspection (AOI)
AOI is a computerized visual inspection method that uses high-resolution cameras and advanced image processing software to detect defects on the PCB. The system compares the captured images with a reference image of a perfect PCB to identify any discrepancies. AOI is faster and more accurate than manual visual inspection, making it suitable for high-volume production.
3. In-Circuit Testing (ICT)
In-circuit testing involves using a specialized fixture, known as a bed of nails, to make contact with specific points on the PCB. The test system then measures the electrical characteristics of each component and compares them to the expected values. ICT can detect:
- Short circuits
- Open circuits
- Incorrect component values
- Missing or wrong components
ICT is an efficient way to test the board’s functionality and component placement accuracy.
4. Flying Probe Testing
Flying probe testing is an alternative to ICT for low-volume production or prototypes. Instead of using a fixed bed of nails, flying probe testers use movable probes to make contact with the PCB. The probes can move freely across the board, testing various points as needed. Flying probe testing offers more flexibility than ICT but is slower and less suitable for high-volume production.
5. Functional Testing
Functional testing involves powering up the PCB and testing its functionality under real-world conditions. This type of testing ensures that the board performs as intended and meets the design specifications. Functional testing may include:
- Power consumption measurement
- Signal integrity testing
- Stress testing under varying environmental conditions (temperature, humidity, vibration)
- Electromagnetic compatibility (EMC) testing
Functional testing is crucial for validating the PCB’s overall performance and reliability.
6. Boundary Scan Testing
Boundary scan testing, also known as JTAG (Joint Test Action Group) testing, is a method that uses a special interface to access and test the interconnections between integrated circuits (ICs) on the PCB. This technique allows for testing of complex boards with high-density components, such as Ball Grid Arrays (BGAs) and chip scale packages (CSPs).
Boundary scan testing can detect:
- Short circuits
- Open circuits
- Stuck-at faults
- Delay faults
This testing method is particularly useful for boards with limited physical access to test points.
PCB Testing Best Practices
To ensure effective and efficient PCB testing, consider the following best practices:
-
Design for Testability (DFT): Incorporate testability features into the PCB Design, such as test points, boundary scan architecture, and built-in self-test (BIST) capabilities.
-
Develop a Comprehensive Test Plan: Create a detailed test plan that covers all aspects of PCB testing, including test coverage, test sequences, and acceptance criteria.
-
Use Appropriate Test Equipment: Invest in high-quality test equipment that is suitable for your specific testing needs and production volume.
-
Maintain Proper Documentation: Keep accurate and up-to-date records of test procedures, results, and any issues encountered during testing.
-
Implement Continuous Improvement: Regularly review and analyze test data to identify areas for improvement in the PCB design, manufacturing process, and testing procedures.
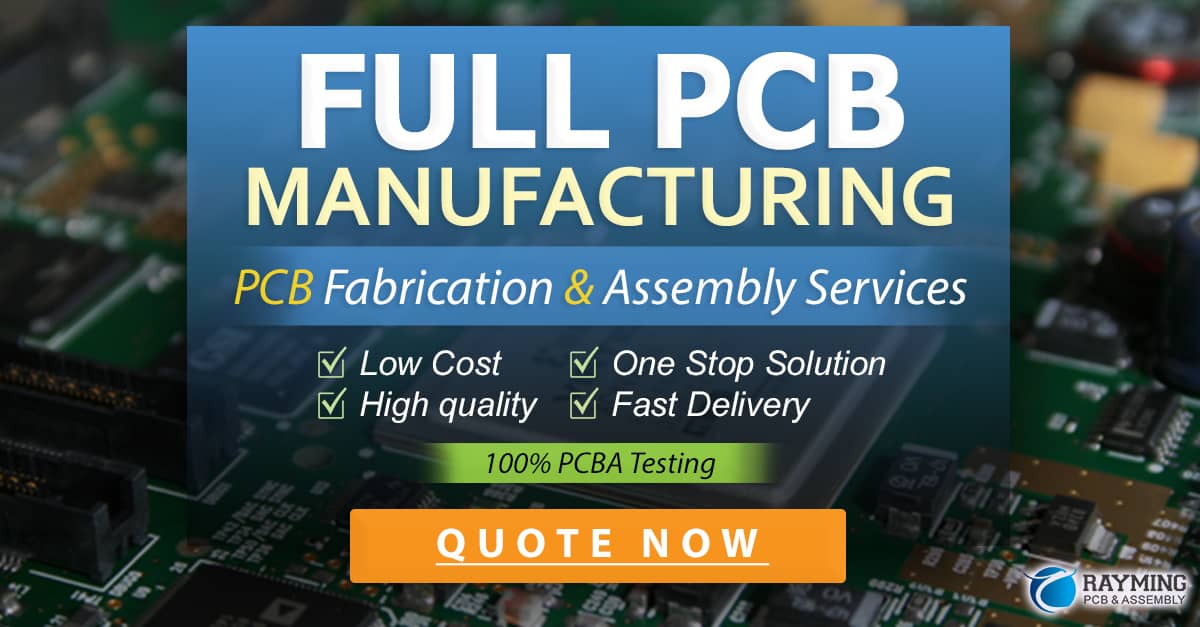
FAQ
- What is the difference between ICT and flying probe testing?
-
ICT uses a fixed bed of nails to make contact with specific points on the PCB, while flying probe testing uses movable probes. ICT is faster and more suitable for high-volume production, while flying probe testing offers more flexibility but is slower.
-
How does boundary scan testing work?
-
Boundary scan testing uses a special interface (JTAG) to access and test the interconnections between integrated circuits (ICs) on the PCB. It can detect short circuits, open circuits, stuck-at faults, and delay faults, even on boards with limited physical access to test points.
-
What are some common defects that visual inspection can detect?
-
Visual inspection can detect incorrect component placement, solder bridges, cold solder joints, damaged or missing components, and contamination or foreign objects on the PCB.
-
Why is functional testing important?
-
Functional testing is crucial for validating the PCB’s overall performance and reliability under real-world conditions. It ensures that the board performs as intended and meets the design specifications.
-
What are some best practices for effective PCB testing?
- Some best practices include designing for testability (DFT), developing a comprehensive test plan, using appropriate test equipment, maintaining proper documentation, and implementing continuous improvement based on test data analysis.
Conclusion
PCB testing is a vital aspect of the Electronics Manufacturing process, ensuring the quality, reliability, and functionality of the final product. By understanding the various testing methods and implementing best practices, manufacturers can effectively identify and address issues early in the production cycle, saving time, money, and resources. As technology advances and PCBs become more complex, staying up-to-date with the latest testing techniques and equipment is essential for maintaining a competitive edge in the industry.
0 Comments