Introduction to Ball Grid Array (BGA) Packaging
Ball Grid Array (BGA) is a type of surface-mount packaging used for integrated circuits (ICs) that utilizes a grid of solder balls to provide electrical connections between the IC and the printed circuit board (PCB). BGA packages offer numerous advantages over traditional packaging methods, such as higher pin counts, smaller footprints, and better thermal and electrical performance. In this article, we will explore the basics of BGA packaging, its advantages and disadvantages, and its applications in various industries.
What is a Ball Grid Array (BGA)?
A Ball Grid Array (BGA) is a surface-mount package that uses an array of solder balls to connect the IC to the PCB. The solder balls are arranged in a grid pattern on the bottom side of the package, allowing for a high density of interconnects in a small area. The IC is mounted on a substrate, which is typically made of a laminate material such as bismaleimide triazine (BT) or polyimide. The substrate has conductive traces that connect the IC to the solder balls.
Advantages of BGA Packaging
BGA packages offer several advantages over traditional packaging methods, such as:
- Higher pin counts: BGA packages can accommodate a large number of interconnects in a small area, allowing for higher pin counts compared to other packaging methods.
- Smaller footprint: BGA packages have a smaller footprint compared to other packages with the same pin count, saving valuable PCB space.
- Better thermal performance: The solder balls in a BGA package provide a low-resistance thermal path, allowing for better heat dissipation from the IC.
- Improved electrical performance: BGA packages have shorter interconnects and lower inductance and capacitance compared to other packaging methods, resulting in better signal integrity and reduced noise.
Disadvantages of BGA Packaging
Despite its many advantages, BGA packaging also has some disadvantages:
- Difficulty in inspection: The solder joints in a BGA package are hidden beneath the package, making visual inspection difficult.
- Complexity in rework: Reworking a BGA package requires specialized equipment and skills, making it more complex and costly compared to other packaging methods.
- Thermal mismatch: The difference in the coefficient of thermal expansion (CTE) between the BGA package and the PCB can cause stress on the solder joints, leading to reliability issues.
BGA Package Construction
Substrate Materials
The substrate is a critical component of a BGA package, as it provides the mechanical support and electrical connections between the IC and the solder balls. The most common substrate materials used in BGA packages are:
- Bismaleimide Triazine (BT): BT is a laminate material that offers good mechanical and electrical properties, as well as excellent moisture resistance. It is widely used in BGA packages for high-performance applications.
- Polyimide: Polyimide is a polymer material that offers high temperature resistance and good electrical properties. It is often used in BGA packages for automotive and aerospace applications.
- Ceramic: Ceramic substrates offer excellent thermal conductivity and dimensional stability, making them suitable for high-power and high-frequency applications.
Solder Ball Materials
The solder balls in a BGA package are typically made of a lead-free solder alloy, such as tin-silver-copper (SAC) or tin-silver (SnAg). The solder ball size and pitch (distance between the centers of adjacent solder balls) are determined by the package size and the number of interconnects required. Common solder ball sizes range from 0.3 mm to 0.8 mm in diameter, with pitches ranging from 0.5 mm to 1.27 mm.
Die Attachment and Wire Bonding
The IC die is attached to the substrate using a die attach adhesive, which is typically an epoxy-based material. The adhesive provides mechanical support and helps dissipate heat from the die. The electrical connections between the die and the substrate are made using wire bonding, where fine gold or copper wires are bonded between the bond pads on the die and the bond fingers on the substrate.
Overmolding and Marking
After wire bonding, the BGA package is overmolded with an epoxy molding compound to protect the die and the wire bonds from environmental factors such as moisture and mechanical damage. The molding compound also provides additional mechanical support to the package. Finally, the package is marked with the necessary identification information, such as the part number, lot number, and pin 1 indicator.
BGA Package Types
There are several types of BGA packages, each with its own unique features and applications:
Plastic BGA (PBGA)
Plastic BGA (PBGA) packages use a plastic substrate, typically made of BT or polyimide. They are the most common type of BGA package and are widely used in consumer electronics, such as smartphones, tablets, and laptops. PBGA packages offer a good balance of cost, performance, and reliability.
Ceramic BGA (CBGA)
Ceramic BGA (CBGA) packages use a ceramic substrate, which offers excellent thermal conductivity and dimensional stability. They are often used in high-power and high-frequency applications, such as RF and microwave devices. CBGA packages are more expensive than PBGA packages but offer better performance and reliability.
Tape BGA (TBGA)
Tape BGA (TBGA) packages use a flexible tape substrate, typically made of polyimide. They are thinner and lighter than other BGA packages, making them suitable for applications where space is limited, such as smartwatches and wearable devices. TBGA packages also offer better electrical performance due to the shorter interconnects.
Cavity-Down BGA (CDBGA)
Cavity-Down BGA (CDBGA) packages have the IC die mounted in a cavity on the bottom side of the substrate, with the active side of the die facing down. This configuration allows for better thermal performance, as the die is in direct contact with the PCB. CDBGA packages are often used in high-power applications, such as graphics processing units (GPUs) and application-specific integrated circuits (ASICs).
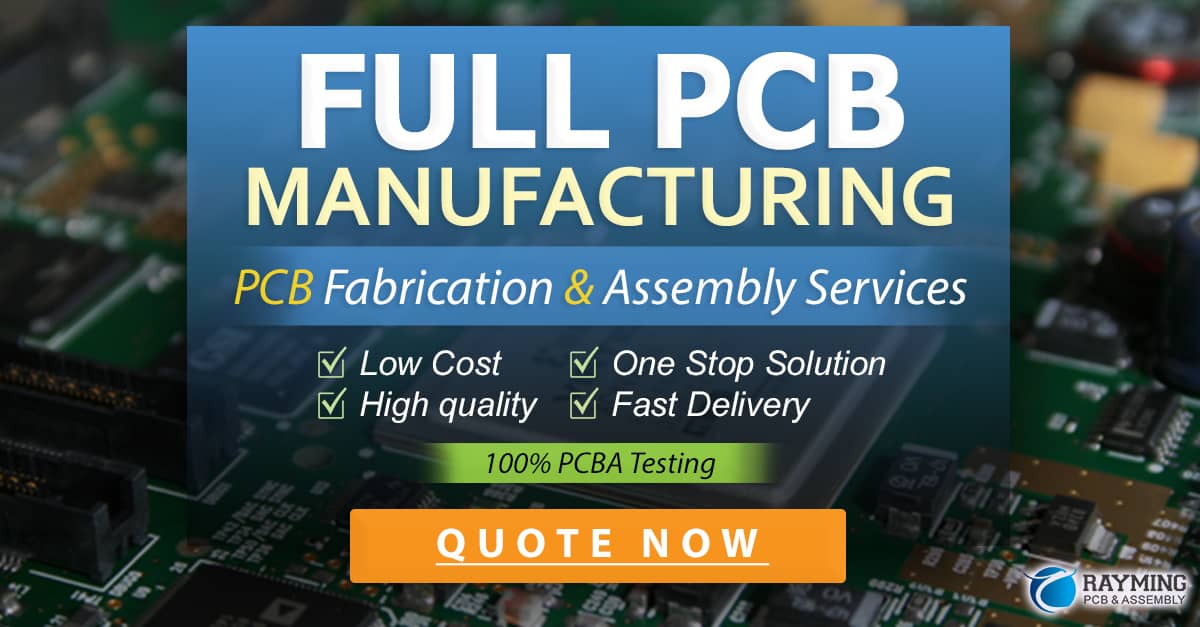
BGA Package Design Considerations
Designing a BGA package requires careful consideration of several factors, such as:
Thermal Management
Thermal management is critical in BGA packages, as the high pin count and small size can result in high power densities. The package design must ensure that the heat generated by the IC is efficiently dissipated to the PCB and the environment. This can be achieved through the use of thermal vias, heat spreaders, and thermal interface materials.
Signal Integrity
Signal integrity is another important consideration in BGA package design, as the high-speed signals can be affected by factors such as crosstalk, reflections, and ground bounce. The package design must minimize these effects through proper layout and routing of the signal traces, as well as the use of ground and power planes.
Mechanical Reliability
The mechanical reliability of a BGA package depends on the strength and durability of the solder joints. The package design must ensure that the solder joints can withstand the stresses caused by thermal cycling, mechanical shock, and vibration. This can be achieved through the use of underfill materials, which fill the gap between the package and the PCB, and provide additional mechanical support to the solder joints.
Manufacturing and Assembly
The manufacturing and assembly processes for BGA packages are more complex compared to other packaging methods, due to the small size and high pin count. The package design must take into account the capabilities and limitations of the manufacturing and assembly processes, such as the minimum solder ball size and pitch, and the placement accuracy of the package on the PCB.
Applications of BGA Packages
BGA packages are widely used in a variety of applications, such as:
Consumer Electronics
BGA packages are extensively used in consumer electronics, such as smartphones, tablets, laptops, and gaming consoles. The high pin count and small size of BGA packages enable the integration of complex functionalities, such as multi-core processors, high-speed memory, and wireless connectivity, in a compact form factor.
Automotive Electronics
BGA packages are increasingly being used in automotive electronics, such as advanced driver assistance systems (ADAS), infotainment systems, and electric vehicle powertrain control modules. The high reliability and temperature resistance of BGA packages make them suitable for the harsh operating conditions in automotive environments.
Industrial and Medical Electronics
BGA packages are used in industrial and medical electronics, such as industrial automation systems, medical imaging equipment, and patient monitoring devices. The high performance and reliability of BGA packages enable the development of advanced and mission-critical systems in these fields.
Aerospace and Defense Electronics
BGA packages are used in aerospace and defense electronics, such as avionics systems, satellite communications, and military radars. The high reliability and ruggedness of BGA packages make them suitable for the extreme operating conditions in aerospace and defense environments.
Future Trends in BGA Packaging
As the demand for higher performance and smaller form factors continues to grow, BGA packaging technology is evolving to meet these challenges. Some of the future trends in BGA packaging include:
3D Packaging
3D packaging involves stacking multiple IC dies vertically in a single package, enabling higher integration density and shorter interconnects. BGA packages are well-suited for 3D packaging, as they provide a high-density interconnect platform for the stacked dies.
Advanced Substrate Materials
New substrate materials, such as glass and silicon, are being explored for BGA packages. These materials offer better electrical and thermal performance compared to traditional laminate materials, enabling the development of high-speed and high-power applications.
Embedded Components
Embedded components, such as capacitors and resistors, are being integrated into the substrate of BGA packages. This integration reduces the package size and improves the electrical performance by reducing the interconnect length and parasitic effects.
Wafer-Level Packaging
Wafer-level packaging involves packaging the IC dies at the wafer level, before singulation into individual packages. This approach enables higher throughput and lower cost compared to traditional packaging methods. BGA packages can be fabricated using wafer-level packaging techniques, such as wafer-level chip-scale packaging (WLCSP) and fan-out wafer-level packaging (FOWLP).
Conclusion
Ball Grid Array (BGA) packaging is a crucial technology for the development of high-performance and compact electronic systems. BGA packages offer numerous advantages over traditional packaging methods, such as higher pin counts, smaller footprints, and better thermal and electrical performance. However, BGA packages also present some challenges, such as difficulty in inspection and complexity in rework.
The design of BGA packages requires careful consideration of several factors, such as thermal management, signal integrity, mechanical reliability, and manufacturing and assembly. BGA packages are widely used in a variety of applications, such as consumer electronics, automotive electronics, industrial and medical electronics, and aerospace and defense electronics.
As the demand for higher performance and smaller form factors continues to grow, BGA packaging technology is evolving to meet these challenges. Future trends in BGA packaging include 3D packaging, advanced substrate materials, embedded components, and wafer-level packaging. These advancements will enable the development of even more complex and compact electronic systems in the future.
Frequently Asked Questions (FAQ)
1. What is the difference between a BGA package and a QFN package?
A BGA package uses a grid of solder balls to provide electrical connections between the IC and the PCB, while a QFN (Quad Flat No-leads) package uses a flat lead frame with exposed pads on the bottom side of the package. BGA packages offer higher pin counts and better thermal performance compared to QFN packages, but are more complex and costly to manufacture and assemble.
2. Can BGA packages be reworked?
Yes, BGA packages can be reworked, but it requires specialized equipment and skills. The rework process involves removing the defective package from the PCB, cleaning the PCB pads, and soldering a new package in place. However, the rework process can be complex and costly, and may affect the reliability of the solder joints.
3. What is the minimum solder ball size and pitch for BGA packages?
The minimum solder ball size and pitch for BGA packages depend on the package size and the manufacturing capabilities. Typical solder ball sizes range from 0.3 mm to 0.8 mm in diameter, with pitches ranging from 0.5 mm to 1.27 mm. However, smaller solder ball sizes and pitches are being developed for advanced BGA packages.
4. How does underfill material improve the mechanical reliability of BGA packages?
Underfill material is an epoxy-based material that is dispensed between the BGA package and the PCB after soldering. The underfill material fills the gap between the package and the PCB, and provides additional mechanical support to the solder joints. This helps to reduce the stress on the solder joints caused by thermal cycling, mechanical shock, and vibration, improving the mechanical reliability of the package.
5. What are the challenges in designing BGA packages for high-speed applications?
Designing BGA packages for high-speed applications requires careful consideration of signal integrity and power integrity. The high-speed signals can be affected by factors such as crosstalk, reflections, and ground bounce, which can degrade the signal quality and cause errors. The package design must minimize these effects through proper layout and routing of the signal traces, as well as the use of ground and power planes. Additionally, the package design must ensure that the power delivery network can supply the required current to the IC without causing voltage drops or noise.
Package Type | Substrate Material | Applications | Advantages | Disadvantages |
---|---|---|---|---|
Plastic BGA (PBGA) | BT, Polyimide | Consumer electronics | Low cost, good performance | Limited thermal and electrical performance |
Ceramic BGA (CBGA) | Ceramic | High-power, high-frequency devices | Excellent thermal and dimensional stability | High cost |
Tape BGA (TBGA) | Polyimide tape | Space-limited applications | Thin, lightweight, good electrical performance | Limited thermal performance |
Cavity-Down BGA (CDBGA) | BT, Polyimide | High-power applications | Improved thermal performance | Complex manufacturing process |
0 Comments