Yes, India has a well-developed printed circuit board (PCB) manufacturing industry catering to both domestic electronics production and exports. Homegrown PCB fabrication has been thriving in India for over 30 years driven by high electronics consumption and recent government initiatives to boost indigenous electronics hardware manufacturing under programs like Digital India and Make in India.
This article provides an overview of PCB manufacturing capability established within India. Topics covered include:
- History and Growth of Indian PCB Industry
- Manufacturing Clusters
- Capability Breakdown
- End Applications and Volume Forecasts
- Government Sector Dependence
- Quality Considerations
- Challenges Faced
- Recent Developments
- Key Players
- Future Outlook
Let’s analyze the Indian PCB landscape.
History and Growth of Indian PCB Industry
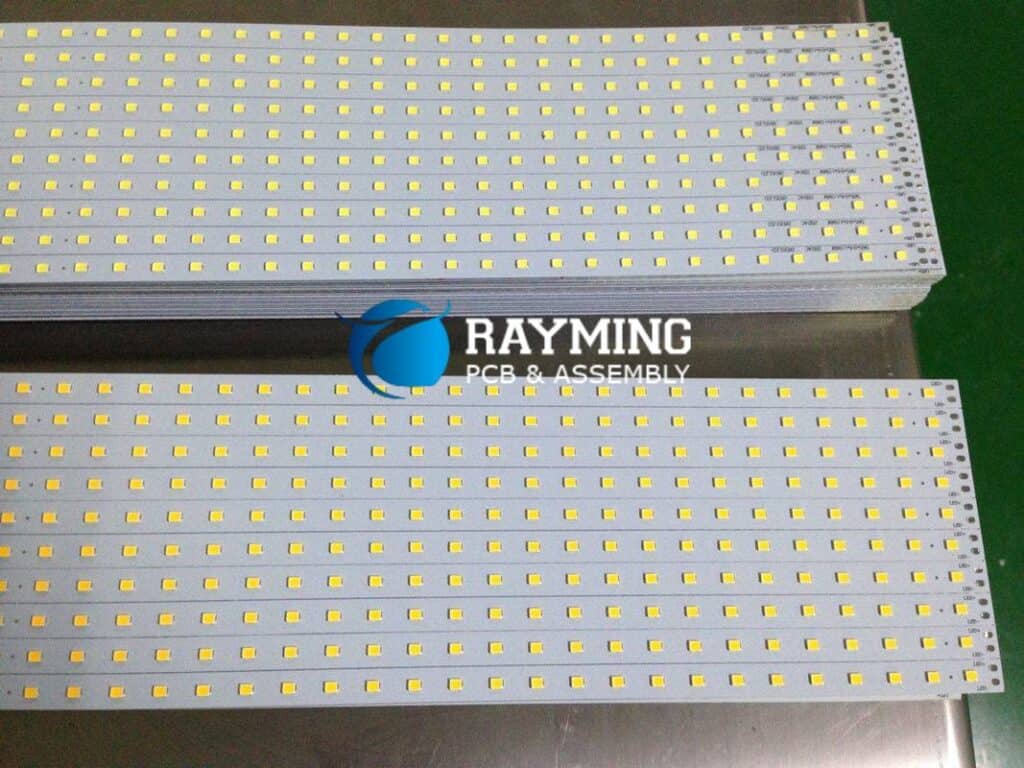
The Indian PCB manufacturing industry traces its origins to the late 1980s and early 1990s as India began Making color TVs, telephone exchanges, radio receivers and other electronics domestically. This created the initial demand for indigenous PCB production. Early manufacturers included Miltronics, e-Tek, AT&S, etc.
Capacity grew slowly but steadily over 1990-2010 period before acceleration this past decade with several new entrants plus large investments in advanced technology by established players as volumes have ballooned. From an estimated $2.2 Billion in 2015, industry revenues now exceed $3.5 Billion as of 2022. The sector is projected to continue rapid growth at a 25% CAGR fueled by surging domestic appliance, mobile device, automotive, industrial electronics and telecom equipment PCB consumption.
Both state initiatives around developing local electronics manufacturing ecosystems plus growing expertise in technical PCB capabilities has fueled expansion.
Manufacturing Clusters
PCB fabrication plants have concentrated into key geographic clusters:
Bangalore – Leads in volume across India with over 25% of PCB production centered in the southern city alongside the broader electronics system design talent pool. Home to Microland, AT&S, TT Electronics facilities among others.
Manesar – Northern India hub houses plants from Japanese manufacturers Meiko and Kawasaki Microelectronics catering heavily to appliance and telecom infrastructure demand.
Pune – Maharashtra based manufacturing including major Defense and Aerospace PCBs by Hindustan Aeronautics Limited (HAL). Also houses consumer electronics board shops.
Chennai – Emerging new plants from Channel Electronics, Advanced Circuitry International (ACI) here with more growth on horizon.
Andhra Pradesh – State government financial support has attracted Green Circuits, Rush PCB and others to set up in Vasanthapuram. Incentives driving expansion.
Capability Breakdown
What types of PCBs can be manufactured competitively within India spanning technology sophistication and volumes?
Entry Level Boards – Basic single or double sided PCBs on FR-4/CEM-1 substrates for cost sensitive domestic appliance controls and lighting applications. Constitute ~35% of production.
Mid Volume Multilayer Boards – 4 to 8 layer boards for TVs, office equipment and communications hardware. Run volumes from 10,000 to 50,000 units per application. Make up ~45% share.
High Density Interconnects – More advanced PCBs with 6+ layers, 100 micron line/space geometries, blind/buried vias, and tighter tolerances are emerging, including RF boards. Represent ~15% but quickly rising.
High Volume Consumer Boards – High layer count boards >14 layers at high volumes of 500,000+ units annually for mobile phone PCBs manufactured competitively, aligning to global standards. Estimated 5% but immense growth potential.
So while higher technology PCB capabilities are clearly developing, majority of boards fabricated presently remain for mid complexity electrical systems across industrial machinery, white goods, instrumentation equipment, power conversion and similar Indian end use equipment. Telecom infrastructure and defense systems constitute most critical application sector PCB demand.
End Applications and Volume Forecasts
Top applications for domestically manufactured PCBs as of 2022 include:
[Table]
Application | Estimated Volume | Growth Rate |
---|---|---|
Industrial Electronics | $530M | 18% |
Lighting Equipment | $450M | 22% |
Home Appliances | $420M | 20% |
Telecom Infrastructure | $400M | 30% |
Office Equipment | $390M | 12% |
Defense Systems | $350M | 25% |
Automotive | $320M | 38% |
Medical Equipment | $290M | 42% |
Solar Inverters | $270M | 20% |
Railway/Transportation | $240M | 45% |
Positive indicators as indigenous electronics equipment manufacturing accelerates across categories with PCBs following. Domestic production minimizes supply chain exposures.
Government Sector Dependence
The defense and aerospace industries remain heavily reliant on imported PCBs given highly complex requirements – over 90% as of estimates. Recent Ministry of Defense decisions however require progressive domestic sourcing minimums ramping from 20% to 60% over coming decade. This makes indigenous defense PCB capabilities vital strategic priority benefiting local manufacturers.
Beyond defense, telecom infrastructure like switches and radio access networks also follow strict Indian government tendering requiring local sourcing minimums on electronics hardware boosting demand. Positive policy catalysts.
Quality Considerations
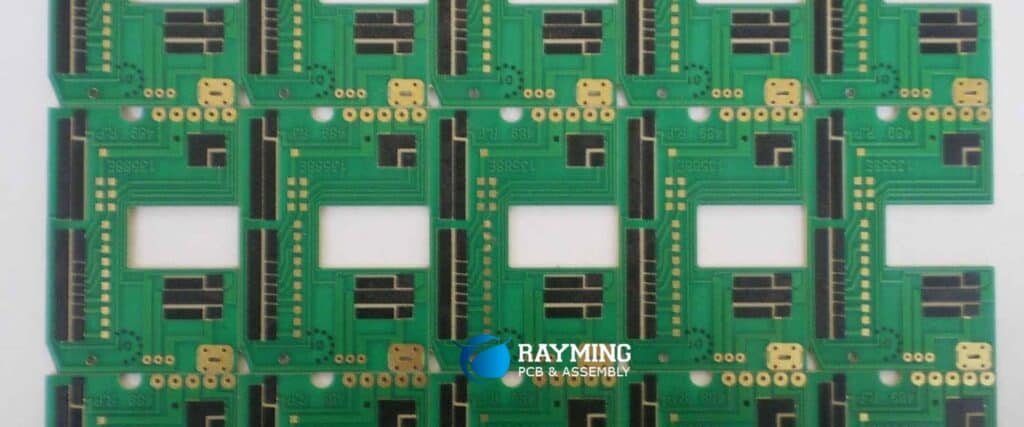
International PCB quality standards like IPC Class 2 and Class 3 per IPC-A-600 specifications have been well adopted by Indian board shops through quality process improvements over past decade. Investments in new owned fabrication facilities rather than outdated second hand equipment has supported this.
However consistency challenges still crop up:
- Relative Immaturity in rigorous process control adoption compared to overseas veteran manufacturers with years of refined institutional knowledge
- Some lingering issues around supply chain raw materials impurity control
- Reliability quantification through disciplined testing lags expectations set by digital design services groups out of India
But leading PCB makers are prioritizing longevity testing, process capability index tracking, and formal DfX practices to instill confidence. Gold and silver level performance recognition through the EPIP industry association helps align best practices too.
Challenges Faced
Barriers needing navigation include:
Inconsistent Infra Supply – Sporadic power and water availability plagues operations continuity and PCB waste.
Limited Specialty Materials – Niche substrates, prepregs, foils involving low Dk glasses, PTFE, ceramic composites largely imported today driving costs up. But should expand through make in India raw materials initiatives.
Complex Defense/Aerospace Certification – Navigating complex certification regimes across defense agencies takes times but investments are being made.
Cost Competitiveness – Prevailing global price pressures makes profitability tougher for local companies. But import circumvention through policy helps insulates against offshore knee-jerk pricing dynamics. Value based procurement practices help too.
Recent Developments
Positive momentum by industry and government bodies helps tackle limitations and boost competitiveness:
- Cluster-based PCB parks with common effluent treatment plus solar infrastructure by state agencies
- IIT workforce training programs specializing in PCB fabrication engineering
- Import duties raised forcing local substitutions
- Joint R&D projects improving material reclamation and process capabilities
- Subsidies and capital loans incentivizing capacity growth
These improve the landscape for ambitious manufacturers despite some lingering infra hurdles.
Key Players
Major Indian PCB companies with large existing or emerging advanced PCB manufacturing capability spanning defense, industrial, communications and high reliability applications include:
AT&S India – Wholly owned subsidiary of European firm AT&S focused on high density interconnect and IC substrate boards. Key supplier across defense, aerospace, telecom infrastructure to Global OEMs.
TT Electronics (formerly IRC) -Privately held company becoming prominent in industrial, railway and defense boards.
Rush PCB – Fast growing firm specializing in automotive boards but broad capability. Global exports presence too.
Green Circuits – End-to-end PCB solutions company focused on rapid prototyping through volume production using latest equipment.
Vintek Circuit India – Expanding PCB producer for mission critical applications including flex-rigid solutions.
Bharat Electronics Limited (BEL) – Major state-owned company involved in high mix defense electronics PCB research, development and manufacturing at scale aligning to government security priorities.
And at least 50 other MSME companies comprise the fabric of high mix regional production. Joint ventures with multinationals setting up Indian arms also continues.
Future Outlook
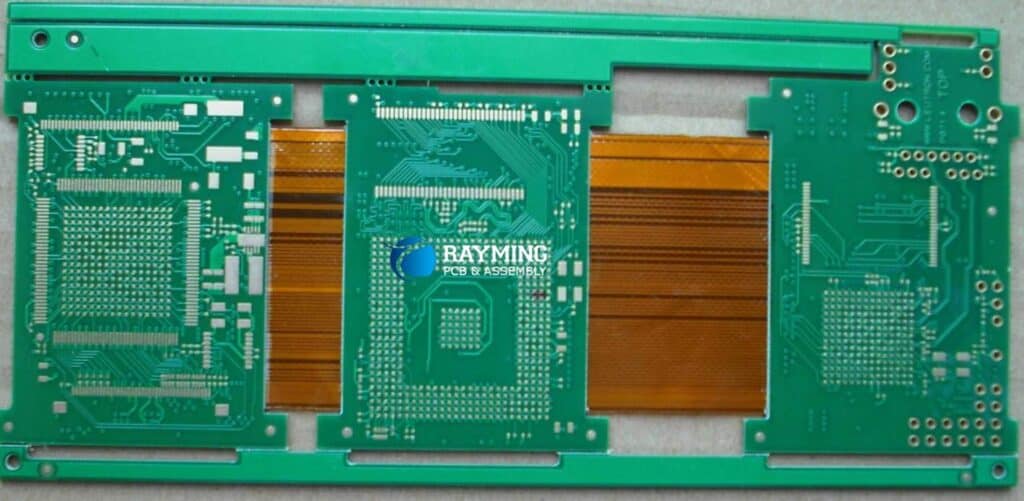
The PCB fabrication industry within India is primed for strong continued expansion as electronics manufacturing accelerates under favorable convergence of growing local demand, policy prioritization of local production independence, and competitive quality/capability maturation by manufacturers. With projections for 25-30% sustained annual industry growth, PCB manufacturing is entering a golden period and central role in the Indian manufacturing renaissance.
Frequently Asked Questions
Q: Why has establishing indigenous PCB manufacturing capability become imperative for India strategically?
A: Electronics components dependency otherwise undermines defense systems integrity, surveillance resilience and critical infrastructure security given potential single points of compromise or coercion risk through foreign PCB supply chains. Developing comprehensive trusted fabrication ecosystem mitigates this.
Q: What innovations are emerging in sustainable green PCB manufacturing practices from Indian companies?
A: Use of soluble salts to replace traditional alkaline etchants, eliminating copper waste streams. Also momentum in ESDM industry toward establishing responsible electronics waste collection systems for end of life product recycling – printing deposition waste reclamation improves with this.
Q: Which next generation semiconductor packaging techniques pose the biggest challenges for local PCB maker readiness?
A: High I/O density fan-out panel level packaging and ABF substrates plus heterogenous 2.5D and 3D integration using silicon bridges demands extremely specialized materials engineering and fabrication expertise buildout farther down the roadmap. But steady progress expected leveraging global partnerships.
Q: Why should PCB manufacturers consider adopting statistical process controls more rigorously?
A: Analyzing process capability indices allows quantifying manufacturing repeatability between batches and diagnosing stability deltas – particularly important for higher performance materials like ceramics and for upcoming reliability driven defense sector expectations. This helps mature right alongside design services groups.
Q: Outside defense systems, which commercial application segments appear most primed for “Designed in India” PCB innovation?
A: Telecom 5G infrastructure as well as high density solar microinverter designs are strong candidates benefiting the supply chain localization strategies overall. Medical electronics segments as well around diagnostic imaging systems, patient monitors seeking security. Leveraging frugal engineering strengths too in these segments.
So in summary, Made in India PCB production is undoubtedly thriving and on strong trajectory to advance the nations strategic electronics aspirations!
0 Comments