Introduction
SMT (Surface Mount Technology) assembly is a key process in PCB (Printed Circuit Board) manufacturing where electronic components are mounted directly onto the surface of a PCB. As electronics continue getting smaller and more complex, the use of SMT has become ubiquitous across consumer electronics, telecommunications, automotive, aerospace, medical devices and more. This article provides a comprehensive overview of SMT assembly service – examining the SMT assembly process, its benefits, key considerations when choosing an SMT assembly service provider, and more.
What is SMT Assembly?
SMT assembly is the process of mounting and soldering small electronic components onto the surface of a PCB. Some key aspects:
- Components are small, lightweight SMT components like resistors, capacitors, ICs rather than through-hole components with leads.
- High-speed pick and place machines position components precisely onto PCB pads.
- Solder paste is screen printed onto the PCB, then re-flowed to form solder joints holding components in place.
- SMT enables miniaturization, automation, and higher component density compared to through-hole assembly.
Some advantages of SMT:
- Smaller components: SMT components take up less space, enabling denser PCBs.
- Automation: SMT is highly automated for faster assembly.
- Lower costs: Smaller components plus automation means lower assembly costs.
- Improved performance: Shorter connections yield better electrical performance.
- **Double-sided mounting:**Components can be placed on both sides of a PCB.
SMT assembly services provide the equipment, expertise and quality processes to handle SMT production from prototyping to high volume manufacturing.
SMT Assembly Process Overview
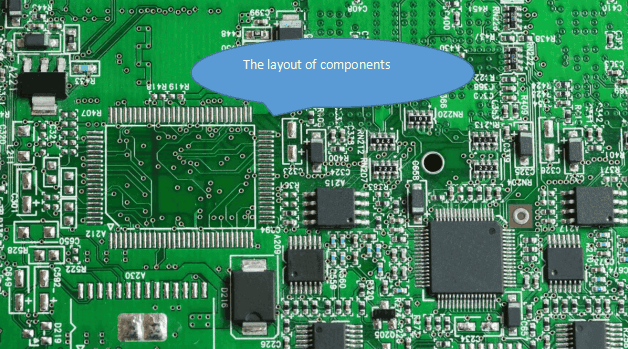
The typical SMT assembly process contains the following key stages:
- Solder Paste Printing – Solder paste is precisely printed onto all the PCB pads that require soldering.
- SMT Pick and Place – SMT machines place components onto the solder paste deposits on the PCB.
- Reflow Soldering – The PCB passes through a reflow oven to heat the solder paste, bonding components to pads.
- Inspection and Testing – Optical and electrical testing ensures components are properly soldered and there are no defects.
- Conformal Coating – A protective coating may be applied to shield components from moisture, dust etc.
Let’s look at some of these stages in more detail:
Solder Paste Printing
Solder paste is a mixture of solder particles and flux which enables SMT soldering. It is printed onto PCB pads through an aperture in a stencil using squeegees to efficiently deposit a precise amount of solder paste. Highly accurate solder paste printing is critical for effective SMT assembly.<div style=”text-align:center”><img src=”https://www.researchgate.net/profile/Waleed-Khan-32/publication/343698426/figure/fig1/AS:974794241720320@1607303727114/Typical-stencil-printing-process-a-Solder-paste-printing-b-PCB-board-after-solder.png” alt=”Solder Paste Printing” width=”400″> <p style=”font-size:12px;”>Solder paste printing process (Image source: ResearchGate)</p> </div>
SMT Pick and Place
SMT pick and place machines use vacuum nozzles to pick components from reels and precisely place them onto the solder paste deposits on the PCB. Pick and place systems are highly flexible and can place thousands of components per hour. They use software files indicating exactly which component goes where.<div style=”text-align:center”><img src=”https://www.researchgate.net/profile/Waleed-Khan-32/publication/343698426/figure/fig2/AS:974794242641920@1607303727115/Typical-SMT-component-placement-process-a-SMT-pick-and-place-machine-b-PCB-board-after.png” alt=”SMT Pick and Place” width=”500″> <p style=”font-size:12px;”>SMT pick and place process (Image source: ResearchGate)</p> </div>
Reflow Soldering
After solder paste and components have been applied, the board moves into the reflow oven. Heating profiles melt the solder particles, causing solder joints to form between pads and component leads, bonding the components to the PCB. Different heating methods like IR, convection or vapor phase can be used.<div style=”text-align:center”><img src=”https://www.researchgate.net/publication/322580472/figure/fig3/AS:669399249305600@1536620518885/Illustration-of-the-reflow-soldering-process-a-Temperature-profile-of-the-reflow-b_Q320.jpg” alt=”Reflow Soldering” width=”500″> <p style=”font-size:12px;”> SMT reflow soldering process (Image source: ResearchGate)</p> </div>
Inspection and Testing
Automated optical inspection (AOI) systems use cameras to visually inspect the assembled PCBs. Any defects like missing components, tombstoning or misalignment can be detected. PCBs also undergo electrical testing to verify all connections and functionality.
Conformal Coating
A protective polymer coating may be applied on the assembled PCB to shield against moisture, dust, chemicals or mechanical damage during product use.
This sequence of SMT production stages enables efficient assembly of complex, high quality PCBs suitable for all types of electronic devices.
Benefits of Using SMT Assembly Services
Electronics companies can derive many benefits by leveraging the expertise and capabilities of a full-service SMT assembly provider.
Speed and Agility – Get prototypes produced in days vs weeks by using the provider’s operations and inventory of components. Rapid turnaround on design revisions.
High Quality – Experience lower defects and higher first pass yield thanks to assembly expertise, optimized processes, and inspection.
Cost Savings – Avoid capital outlay for SMT equipment and inventory. Gain from economies of scale in high volume production.
Supply Chain Simplicity – Work with a single provider to coordinate everything from sourcing components to final delivery.
Focus on Core Competency – Offload PCB assembly activities so internal teams can focus on design and product innovation.
Ramp to Volume – Seamlessly scale from prototypes to mass production with access to same assembly lines and engineering support.
One-stop Service – Full assembly service including soldering, testing, inspection, conformal coating etc.
For complex, high mix or quick-turn assembly, leveraging an experienced SMT assembly service provider delivers tremendous advantages.
Key Considerations for Choosing an SMT Assembly Partner
Here are important factors to evaluate when selecting an EMS partner for SMT assembly services:
Technical Capabilities
- SMT equipment: Look for the latest high-speed pick-and-place and soldering equipment like Yamaha, Juki, Fuji, Panasonic, Heller. This ensures high accuracy and throughput.
- Quality processes: Seek ISO certified facilities with robust quality control and continuous improvement practices.
- Engineering expertise: Evaluate depth of engineering skills, especially for solving complex assembly issues.
- Supply chain: Look for in-house sourcing and stocking of a wide range of components to avoid procurement delays.
Production Capacity
- Prototyping: Evaluate speed of prototyping services, especially for quick-turn needs.
- Volume production: Assess production capacity and scalability to meet high-volume production.
- Manufacturing sites: Look for distributed geographic sites to derisk supply chain.
Customer Focus
- Design for manufacturing (DFM): Find a partner who provides DFM analysis to refine PCB designs for optimal manufacturing outcomes.
- Customer collaboration: Assess processes for engineering collaboration and customer access to production data and inventory.
- Quality: Evidence of comprehensive testing, inspection and quality control.
- Continuous improvement: Ongoing initiatives to improve quality, reduce costs and development times etc.
Selecting an assembly partner with advanced technical capabilities, sufficient capacity, and strong customer orientation enables companies to meet program needs from prototyping to full-scale production.
SMT vs Through Hole Assembly
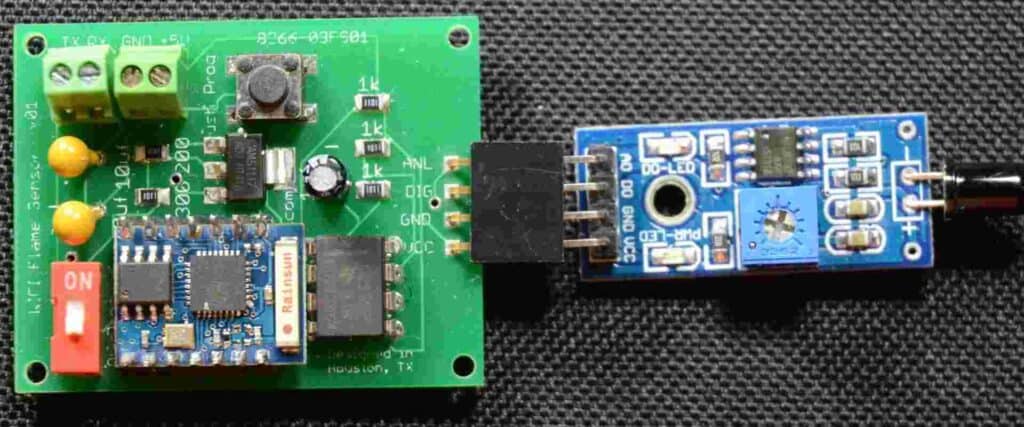
SMT assembly offers many advantages over traditional through-hole assembly:<div class=”table-wrapper”>
Parameter | SMT Assembly | Through Hole Assembly |
---|---|---|
Component size | Smaller component footprint | Larger footprint due to leads |
PCB size | Allows greater miniaturization | Larger PCB area required |
Component density | Very high | Moderate |
Process automation | Highly automated | Less automated |
Solder joints | Only on bottom side | Can be wave soldered on bottom side |
Electrical performance | Superior due to shorter traces | Inferior due to longer component leads |
Reworkability | Typically requires hot air stations | Easier to de-solder and replace |
Flexibility | Only one-sided component mounting | Allows through-hole components to be used |
Cost | Lower assembly cost | Higher assembly cost |
</div>
SMT is preferable for miniaturized, high density PCBs where automated assembly provides quality and cost benefits. However, through-hole assembly allows for easier rework so may be better for very low volume or prototyping needs. The best solution depends on the specific technical and commercial considerations.
Example SMT Assembly Applications
SMT assembly is ubiquitous across all types of electronics devices including:
Consumer Electronics – Mobile phones, tablets, laptops, wearables, home automation etc. Densely packed, miniature designs are only possible with SMT.
Automotive – Engine control units, infotainment systems, ADAS components. Quality and reliability requirements make SMT assembly critical.
Telecommunications – Switches, routers, base stations. High complexity drives use of advanced SMT automation.
Aerospace/Military – Avionics, guidance systems, communications. SMT enables compact, ruggedized, high reliability electronics.
Medical – Implants, imaging systems, diagnostic equipment. SMT allows greater device miniaturization.
Industrial – Programmable automation controllers, motor drives, sensors. SMT supports integration and performance.
Continuing improvements in SMT technology, materials and processes will expand applications across more industries and products.
The Future of SMT Assembly
Key trends shaping the future of SMT assembly include:
- Continued miniaturization of components and higher density PCBs enabled by smaller SMT components and finer interconnects.
- Growth in advanced packaging like 2.5D/3D, flip chip, and wafer-level packaging to enable heterogenous integration of components.
- Improved solder alloys like SAC305 offering superior thermal and mechanical reliability. Alternatives like silver solder may gain traction.
- More multi-functional assembly with integration of components, substrates, and addition of thermal compounds/EMI shielding in a single production platform.
- Increased automation and intelligence through advances like AI-enabled pick-and-place, solder paste inspection, and other smart factory technologies.
- Flexible and additive manufacturing using 3D printing of conformal electronics or solder paste could transform prototyping and small batch production.
Frequently Asked Questions
Q: What types of components are used in SMT assembly?
Common SMT component packages include:
- Resistors/capacitors: 0402, 0603, 0805, 1210 etc. dimensions
- ICs: SOIC, QFP, BGA, CSP, DFN etc.
- Connectors: SMT card edge, mezzanine, board-to-board etc.
Components trending towards smaller 01005 and 0201 packages.
Q: How many components can be assembled using SMT?
High speed pick-and-place machines can accurately place over 35,000 components per hour. Dense PCB designs can incorporate thousands of SMT components on a single board.
Q: How are very small SMT components handled?
Miniaturized components like 01005 are packaged in tape-and-reel to enable automated feeding. Vacuum pickup nozzles handle the tiny components. Microscope systems are used for inspection.
Q: Does solder paste have a shelf life?
Yes, solder paste is only usable for a certain duration when stored correctly between 5-10°C. The flux has a limited active life. Checking paste printing quality indicates when paste should be replaced.
Q: Why is conformal coating used?
Conformal coatings protect PCBs from moisture, dust, chemicals and mechanical damage. Coatings like acrylic, silicone, urethane or epoxy can shield components and solder joints from environmental threats.
Conclusion
SMT assembly enables creation of feature-rich, compact and robust electronic devices through automated population of PCBs with surface mount components. Selecting an expert SMT assembly services partner provides access to advanced technical capabilities and optimized quality processes for cost-effective prototyping through volume production.
0 Comments