Introduction to Rogers PCB
Rogers PCB, also known as Rogers Printed Circuit Board, is a specialized type of PCB that utilizes high-performance materials manufactured by Rogers Corporation. These materials are renowned for their exceptional electrical, thermal, and mechanical properties, making them ideal for applications that require high reliability, high frequency, and low loss.
What is Rogers Corporation?
Rogers Corporation is a global leader in engineered materials that enable clean energy, internet connectivity, safety and protection applications. The company was founded in 1832 and has since been at the forefront of innovation in the materials industry. Rogers Corporation offers a wide range of advanced materials, including high-frequency laminates, ceramic substrates, and elastomeric materials.
Advantages of Rogers PCB
Rogers PCB offers several advantages over traditional FR-4 PCBs, including:
-
Low Dielectric Loss: Rogers materials have a low dielectric constant and low dissipation factor, which minimizes signal loss and allows for higher frequency operation.
-
High Thermal Conductivity: Many Rogers materials have excellent thermal conductivity, which helps to dissipate heat more effectively and improve the overall reliability of the PCB.
-
Dimensional Stability: Rogers materials maintain their dimensional stability over a wide temperature range, which is crucial for applications that require consistent performance in varying environmental conditions.
-
Moisture Resistance: Rogers PCBs are highly resistant to moisture absorption, which prevents delamination and other moisture-related issues.
-
High-Frequency Performance: The unique properties of Rogers materials make them well-suited for high-frequency applications, such as RF and microwave circuits.
Types of Rogers PCB Materials
Rogers Corporation offers a wide range of PCB materials, each with its own unique set of properties and applications. Some of the most popular Rogers PCB materials include:
1. RO4000 Series
The RO4000 series is a family of high-performance, glass-reinforced hydrocarbon/ceramic laminates designed for demanding RF and microwave applications. These materials offer excellent electrical properties, including low dielectric constant and low loss tangent, as well as good thermal and mechanical stability.
Key Features:
- Dielectric Constant (Dk): 3.38 – 3.48
- Dissipation Factor (Df): 0.0027 – 0.0037
- Thermal Conductivity: 0.64 – 0.81 W/m/K
- Temperature Range: -55°C to +280°C
2. RT/duroid 5870-5880 Series
The RT/duroid 5870-5880 series is a family of glass microfiber reinforced PTFE composites that offer excellent electrical and mechanical properties. These materials are well-suited for high-frequency applications that require low dielectric loss and a low dielectric constant.
Key Features:
- Dielectric Constant (Dk): 2.33 – 2.45
- Dissipation Factor (Df): 0.0012 – 0.0020
- Thermal Conductivity: 0.22 – 0.25 W/m/K
- Temperature Range: -55°C to +260°C
3. RO3000 Series
The RO3000 series is a family of ceramic-filled PTFE composites that offer a combination of low dielectric loss, low moisture absorption, and good thermal stability. These materials are ideal for high-frequency applications that require a balance of electrical and mechanical properties.
Key Features:
- Dielectric Constant (Dk): 3.00 – 3.50
- Dissipation Factor (Df): 0.0010 – 0.0025
- Thermal Conductivity: 0.50 – 0.70 W/m/K
- Temperature Range: -55°C to +260°C
Rogers PCB Manufacturing Process
The manufacturing process for Rogers PCB is similar to that of traditional FR-4 PCBs, but with some additional considerations due to the unique properties of Rogers materials. The key steps in the Rogers PCB manufacturing process include:
-
Material Selection: The appropriate Rogers material is selected based on the specific requirements of the application, such as frequency, dielectric constant, and thermal conductivity.
-
Lamination: The Rogers material is laminated to a substrate, typically using a high-temperature and high-pressure process to ensure good bonding and minimal voids.
-
Drilling: Holes are drilled into the laminated board to accommodate components and vias. Special care must be taken to avoid delamination and damage to the Rogers material during drilling.
-
Plating: The drilled holes are plated with copper to create electrical connections between layers. The plating process must be carefully controlled to ensure good adhesion and minimal stress on the Rogers material.
-
Etching: The unwanted copper is etched away using a photolithographic process, leaving only the desired circuit pattern. The etching process must be optimized for the specific Rogers material to ensure accurate feature sizes and minimal undercutting.
-
Solder Mask and Silkscreen: A solder mask is applied to the board to protect the copper traces from oxidation and prevent solder bridging. A silkscreen layer is also applied to label components and provide visual references.
-
Surface Finish: A surface finish, such as HASL, ENIG, or OSP, is applied to the exposed copper to protect it from oxidation and improve solderability.
-
Inspection and Testing: The finished Rogers PCB is inspected for defects and tested for electrical performance to ensure that it meets the required specifications.
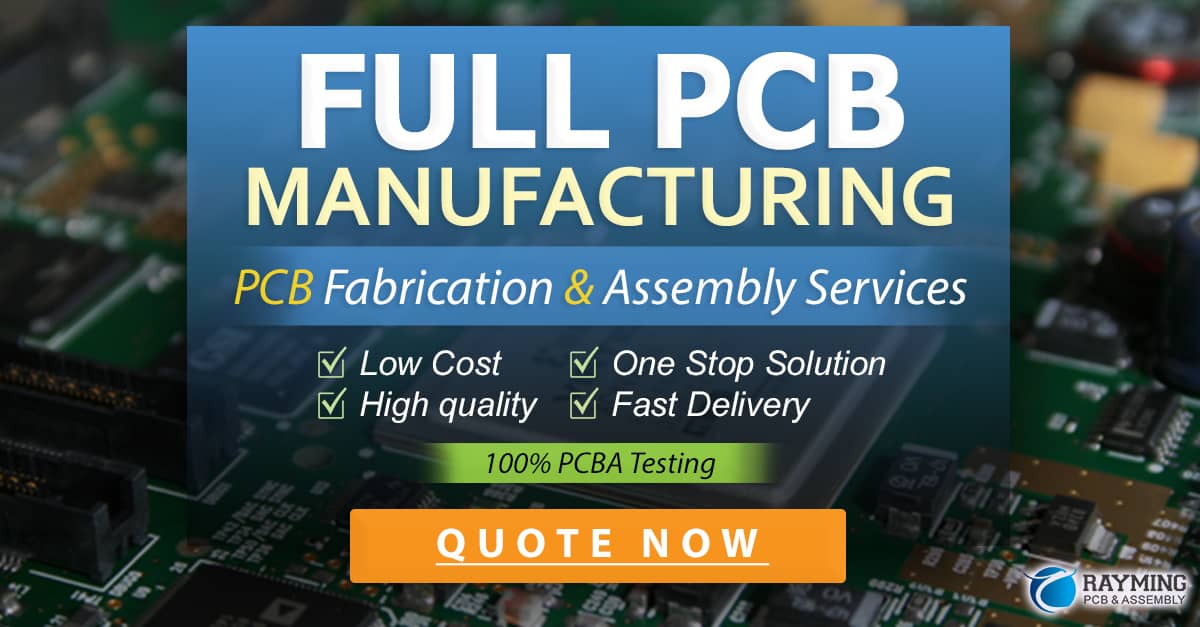
Choosing a Rogers PCB Manufacturer
Choosing the right Rogers PCB manufacturer is critical to ensuring the quality, reliability, and performance of your final product. When selecting a Rogers PCB manufacturer, consider the following factors:
-
Experience with Rogers Materials: Look for a manufacturer that has extensive experience working with Rogers materials and can provide examples of past projects.
-
Manufacturing Capabilities: Ensure that the manufacturer has the necessary equipment and expertise to handle the specific requirements of your Rogers PCB, such as high-frequency testing and controlled impedance routing.
-
Quality Control: Choose a manufacturer with a robust quality control system in place, including ISO 9001 certification and IPC standards compliance.
-
Technical Support: Look for a manufacturer that offers strong technical support and can provide guidance on material selection, design optimization, and troubleshooting.
-
Lead Time and Cost: Consider the manufacturer’s lead time and cost structure to ensure that they align with your project timeline and budget.
Some of the top Rogers PCB manufacturers and fabricators include:
- Candor Industries
- Advanced Circuits
- PCB Universe
- Sierra Circuits
- APCT
Rogers PCB Design Considerations
Designing a Rogers PCB requires careful consideration of the unique properties of Rogers materials and the specific requirements of the application. Some key design considerations for Rogers PCB include:
1. Material Selection
Choosing the right Rogers material is critical to achieving the desired electrical and mechanical performance. Factors to consider when selecting a Rogers material include:
- Dielectric Constant (Dk)
- Dissipation Factor (Df)
- Thermal Conductivity
- Thickness
- Copper Cladding
2. Controlled Impedance
Many high-frequency applications require controlled impedance routing to ensure signal integrity and minimize reflections. When designing a Rogers PCB with controlled impedance, consider the following:
- Trace width and spacing
- Dielectric thickness
- Copper thickness
- Ground plane configuration
3. Thermal Management
Rogers materials have excellent thermal conductivity, but proper thermal management is still essential to ensure reliable operation and prevent overheating. When designing a Rogers PCB, consider the following thermal management techniques:
- Adequate copper thickness
- Thermal vias
- Heat sinks
- Thermal interface materials
4. High-Frequency Layout
Designing a high-frequency Rogers PCB requires careful attention to layout and routing to minimize signal loss, crosstalk, and electromagnetic interference (EMI). Some key high-frequency layout considerations include:
- Minimizing trace lengths
- Avoiding sharp corners and bends
- Providing adequate ground planes
- Using guard traces and shielding
- Minimizing stub lengths
5. Manufacturing Tolerances
Rogers materials have tighter manufacturing tolerances compared to traditional FR-4, which must be accounted for in the design process. When designing a Rogers PCB, consider the following manufacturing tolerances:
- Trace width and spacing
- Hole size and placement
- Copper thickness
- Dielectric thickness
Rogers PCB Applications
Rogers PCB is used in a wide range of high-frequency and high-reliability applications, including:
-
Wireless Communication: Rogers materials are widely used in wireless communication applications, such as cellular base stations, antennas, and satellite communication systems.
-
Aerospace and Defense: Rogers PCBs are used in radar systems, avionics, and other aerospace and defense applications that require high reliability and performance.
-
Automotive: Rogers materials are used in automotive radar systems, GPS navigation, and other applications that require high-frequency performance and reliability.
-
Medical: Rogers PCBs are used in medical imaging systems, such as MRI and CT scanners, as well as in other medical devices that require high-frequency performance and reliability.
-
Industrial: Rogers materials are used in industrial control systems, power electronics, and other applications that require high-frequency performance and reliability in harsh environments.
Frequently Asked Questions (FAQ)
1. What is the difference between Rogers PCB and traditional FR-4 PCB?
Rogers PCB utilizes high-performance materials manufactured by Rogers Corporation, which offer superior electrical, thermal, and mechanical properties compared to traditional FR-4. These properties make Rogers PCB ideal for high-frequency and high-reliability applications.
2. Can Rogers PCB be manufactured using the same processes as traditional FR-4?
While the manufacturing process for Rogers PCB is similar to that of traditional FR-4, some additional considerations must be taken into account due to the unique properties of Rogers materials. These include optimized drilling, plating, and etching processes to ensure the best possible performance and reliability.
3. How do I select the right Rogers material for my application?
Selecting the right Rogers material depends on the specific requirements of your application, such as frequency, dielectric constant, loss tangent, and thermal conductivity. Consult with your Rogers PCB manufacturer or refer to Rogers Corporation’s product data sheets to determine the best material for your needs.
4. What are the lead times and costs associated with Rogers PCB?
Lead times and costs for Rogers PCB can vary depending on the specific material, complexity of the design, and manufacturing requirements. In general, Rogers PCB may have slightly longer lead times and higher costs compared to traditional FR-4 due to the specialized materials and processes involved. However, the superior performance and reliability of Rogers PCB often justify the additional time and expense.
5. Can Rogers PCB be used for non-high-frequency applications?
While Rogers PCB is primarily designed for high-frequency applications, it can also be used in non-high-frequency applications that require exceptional thermal conductivity, dimensional stability, or moisture resistance. However, the higher cost of Rogers materials compared to traditional FR-4 may not be justified for applications that do not require these specific properties.
Conclusion
Rogers PCB is a specialized type of printed circuit board that utilizes high-performance materials manufactured by Rogers Corporation. These materials offer superior electrical, thermal, and mechanical properties, making Rogers PCB ideal for high-frequency and high-reliability applications in wireless communication, aerospace and defense, automotive, medical, and industrial sectors.
When designing and manufacturing Rogers PCB, careful consideration must be given to material selection, controlled impedance, thermal management, high-frequency layout, and manufacturing tolerances. Choosing the right Rogers PCB manufacturer is also critical to ensuring the quality, reliability, and performance of the final product.
As technology continues to advance and the demand for high-frequency and high-reliability electronics grows, Rogers PCB will play an increasingly important role in enabling the next generation of innovative products and solutions.
0 Comments