Introduction to Rogers PCB Materials
Rogers Corporation is a leading manufacturer of high-performance printed circuit board (PCB) materials. Their products are widely used in various industries, including telecommunications, aerospace, defense, and automotive. Rogers PCB materials are known for their exceptional electrical properties, thermal stability, and mechanical strength, making them ideal for demanding applications.
What Makes Rogers PCB Materials Special?
Rogers PCB materials are engineered to provide superior performance compared to conventional PCB materials. Some of the key features that set Rogers PCB materials apart include:
- Low dielectric constant and loss tangent
- High thermal conductivity
- Excellent dimensional stability
- Resistance to moisture absorption
- Wide range of available thicknesses and copper cladding options
These properties enable Rogers PCB materials to deliver optimal signal integrity, power handling capability, and reliability in high-frequency and high-speed applications.
Types of Rogers PCB Materials
Rogers offers a variety of PCB materials to suit different application requirements. Some of the most popular Rogers PCB materials include:
1. RO4000 Series
The RO4000 series is a family of high-performance hydrocarbon ceramic laminates designed for demanding RF and microwave applications. These materials offer a low dielectric constant and loss tangent, making them suitable for applications up to 40 GHz.
Material | Dielectric Constant | Dissipation Factor | Thermal Conductivity (W/m·K) |
---|---|---|---|
RO4003C | 3.38 | 0.0027 | 0.71 |
RO4350B | 3.48 | 0.0037 | 0.69 |
RO4360G2 | 6.15 | 0.0038 | 0.66 |
2. RT/duroid Series
RT/duroid materials are PTFE-based composites reinforced with glass microfibers. These materials offer excellent electrical properties, low moisture absorption, and a wide range of dielectric constants, making them suitable for RF and microwave applications.
Material | Dielectric Constant | Dissipation Factor | Thermal Conductivity (W/m·K) |
---|---|---|---|
RT/duroid 5870 | 2.33 | 0.0012 | 0.26 |
RT/duroid 5880 | 2.20 | 0.0009 | 0.26 |
RT/duroid 6010 | 10.2 | 0.0023 | 0.60 |
3. TMM Series
The TMM series is a family of ceramic thermoset polymer composite materials designed for high-frequency applications. These materials offer a low dielectric constant, low loss tangent, and excellent thermal stability.
Material | Dielectric Constant | Dissipation Factor | Thermal Conductivity (W/m·K) |
---|---|---|---|
TMM3 | 3.27 | 0.0020 | 0.70 |
TMM4 | 4.50 | 0.0020 | 0.70 |
TMM10i | 9.80 | 0.0020 | 0.70 |
Choosing the Right Rogers PCB Material
When selecting a Rogers PCB material for your application, consider the following factors:
- Frequency range
- Dielectric constant and loss tangent requirements
- Thermal management needs
- Mechanical strength and dimensional stability
- Cost and availability
By carefully evaluating your application’s requirements and matching them with the appropriate Rogers PCB material, you can ensure optimal performance, reliability, and cost-effectiveness.
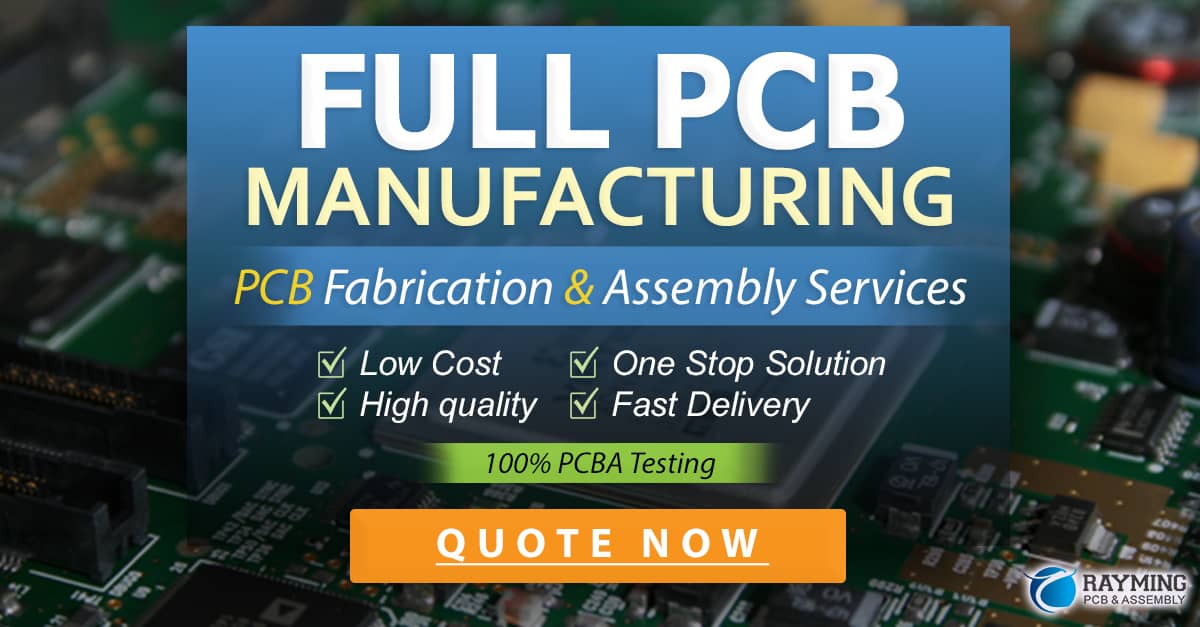
Applications of Rogers PCB Materials
Rogers PCB materials find applications in various industries and products, such as:
- Wireless communication devices (smartphones, tablets, laptops)
- 5G infrastructure (base stations, small cells)
- Radar systems (automotive, aerospace, defense)
- Satellite communication systems
- Medical equipment (MRI, ultrasound)
- High-speed digital circuits (data centers, servers)
- Automotive electronics (ADAS, infotainment systems)
The unique properties of Rogers PCB materials make them essential for these applications, where high performance, reliability, and signal integrity are critical.
Manufacturing Considerations
When working with Rogers PCB materials, it is essential to follow the manufacturer’s guidelines for processing and handling. Some key considerations include:
- Proper storage and conditioning of materials before use
- Appropriate drilling and routing parameters
- Controlled impedance design and stackup planning
- Specialized bonding and lamination processes
- Careful handling to avoid contamination and damage
By adhering to these guidelines and working with experienced PCB manufacturers, you can ensure the successful fabrication of high-quality Rogers PCB-based products.
Future Trends in Rogers PCB Materials
As technology continues to advance, Rogers Corporation is continually developing new and improved PCB materials to meet the evolving needs of various industries. Some of the future trends in Rogers PCB materials include:
- Materials with even lower dielectric constants and loss tangents
- Improved thermal management solutions
- Environmentally friendly and halogen-free materials
- Materials optimized for additive manufacturing processes
- Integration of embedded components and 3D structures
By staying at the forefront of PCB material technology, Rogers Corporation aims to support the development of next-generation electronic devices and systems.
Frequently Asked Questions (FAQ)
1. What is the main difference between Rogers PCB materials and conventional PCB materials?
Rogers PCB materials are engineered to provide superior electrical, thermal, and mechanical properties compared to conventional PCB materials. They offer lower dielectric constants, lower loss tangents, higher thermal conductivity, and better dimensional stability, making them ideal for high-frequency and high-speed applications.
2. Can I use Rogers PCB materials for low-frequency applications?
While Rogers PCB materials are primarily designed for high-frequency applications, they can also be used for low-frequency applications where high performance, reliability, and signal integrity are required. However, for cost-sensitive low-frequency applications, conventional PCB materials may be more suitable.
3. Are Rogers PCB materials compatible with standard PCB manufacturing processes?
Yes, Rogers PCB materials are compatible with most standard PCB manufacturing processes. However, some materials may require specialized processing techniques, such as controlled impedance design, specialized bonding, and lamination processes. It is essential to work with experienced PCB manufacturers who are familiar with handling Rogers materials.
4. How do I select the right Rogers PCB material for my application?
To select the right Rogers PCB material, consider factors such as the frequency range, dielectric constant and loss tangent requirements, thermal management needs, mechanical strength, dimensional stability, cost, and availability. Evaluate your application’s requirements and match them with the properties of the available Rogers PCB materials.
5. Are Rogers PCB materials environmentally friendly?
Rogers Corporation is committed to developing environmentally friendly PCB materials. Some of their products, such as the RO4000 series, are halogen-free and comply with various environmental regulations, including RoHS and REACH. As technology advances, Rogers continues to work on developing more eco-friendly materials without compromising performance.
Conclusion
Rogers PCB materials are essential for high-performance electronic applications, offering superior electrical, thermal, and mechanical properties compared to conventional PCB materials. By understanding the different types of Rogers PCB materials, their properties, and applications, engineers and designers can make informed decisions when selecting the right material for their projects.
As technology continues to evolve, Rogers Corporation remains committed to developing innovative PCB materials that meet the demanding requirements of various industries. By staying at the forefront of PCB material technology, Rogers aims to support the development of next-generation electronic devices and systems that push the boundaries of performance, reliability, and sustainability.
0 Comments