Introduction to Rigid PCB
A Printed Circuit Board (PCB) is the backbone of modern electronic devices, providing a platform for interconnecting electronic components. Among the various types of PCBs, Rigid PCBs are the most commonly used due to their durability, reliability, and cost-effectiveness. In this comprehensive guide, we will dive into the world of Rigid PCBs, covering everything from their basic structure and manufacturing process to their applications and design considerations.
What is a Rigid PCB?
A Rigid PCB is a type of printed circuit board that is made from a solid, non-flexible substrate material, typically FR-4 (a glass-reinforced epoxy laminate). The board consists of multiple layers of copper circuits that are laminated together with the substrate material, creating a sturdy and robust base for mounting electronic components.
Advantages of Rigid PCBs
Rigid PCBs offer several advantages over other types of PCBs, such as:
- Durability: The solid substrate material makes Rigid PCBs highly durable and resistant to physical stress and environmental factors.
- Reliability: The stable structure of Rigid PCBs ensures consistent performance and minimizes the risk of circuit failures.
- Cost-effectiveness: Rigid PCBs are generally less expensive to manufacture compared to flexible or rigid-flex PCBs, making them a cost-effective choice for most applications.
- Ease of assembly: The rigid nature of the board allows for easy component placement and soldering, streamlining the assembly process.
Rigid PCB Structure and Layers
PCB Layers
A Rigid PCB consists of multiple layers of copper circuits separated by insulating layers. The number of layers can vary depending on the complexity of the circuit design and the specific requirements of the application. The most common layer configurations are:
Layers | Description |
---|---|
Single | One layer of copper on one side of the substrate |
Double | Two layers of copper, one on each side of the substrate |
Multi | Three or more layers of copper, alternating with insulators |
Copper Thickness
The thickness of the copper layers in a Rigid PCB is typically measured in ounces per square foot (oz/ft²). Common copper thicknesses include:
Thickness | Description |
---|---|
0.5 oz | Thin copper layer, suitable for low-power circuits |
1 oz | Standard copper thickness for most applications |
2 oz | Thicker copper layer for high-current applications |
Substrate Material
FR-4 is the most widely used substrate material for Rigid PCBs. It is a glass-reinforced epoxy laminate that offers excellent mechanical and electrical properties, such as:
- High dielectric strength
- Good thermal stability
- Low moisture absorption
- Flame retardance
Other substrate materials, such as ceramic or metal-core PCBs, may be used for specific applications that require higher thermal dissipation or improved mechanical properties.
Rigid PCB Manufacturing Process
The manufacturing process of Rigid PCBs involves several steps, each critical to ensuring the quality and reliability of the final product.
Step 1: PCB Design
The first step in the manufacturing process is designing the PCB using specialized software, such as Altium Designer or Eagle. The design includes the circuit layout, component placement, and routing of the copper traces.
Step 2: PCB Fabrication
Once the design is finalized, the PCB fabrication process begins. This involves the following sub-steps:
- Substrate preparation: The FR-4 substrate is cut to the required size and thickness.
- Copper lamination: Thin sheets of copper are laminated onto the substrate using heat and pressure.
- Drilling: Holes are drilled through the board to accommodate components and vias (interconnects between layers).
- Plating: The drilled holes are plated with copper to create electrical connections between layers.
- Etching: The unwanted copper is removed using a chemical etching process, leaving behind the desired circuit pattern.
- Solder mask application: A protective solder mask layer is applied to the board, covering the copper traces while leaving the pads exposed for component soldering.
- Silkscreen printing: Text and symbols are printed onto the board for component identification and assembly guidance.
Step 3: PCB Assembly
After the PCB fabrication is complete, the components are assembled onto the board. This can be done manually for low-volume production or using automated pick-and-place machines for high-volume manufacturing. The components are then soldered to the board using wave soldering, reflow soldering, or hand soldering techniques.
Step 4: Testing and Inspection
The assembled PCBs undergo rigorous testing and inspection to ensure they meet the required quality standards. This includes:
- Visual inspection: Checking for any visible defects, such as poor soldering or damaged components.
- Electrical testing: Verifying the electrical continuity and functionality of the circuit using automated test equipment (ATE) or Flying probe testers.
- Functional testing: Testing the PCB in its intended application to ensure it performs as expected.
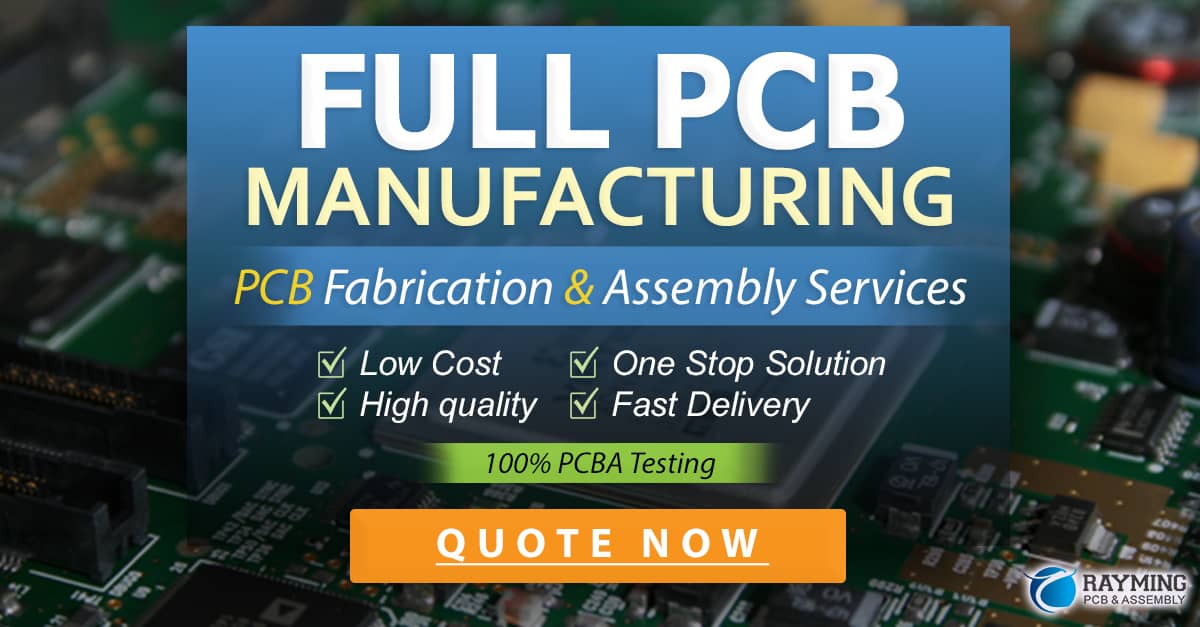
Rigid PCB Design Considerations
When designing a Rigid PCB, several factors must be considered to ensure optimal performance, reliability, and manufacturability.
Component Placement
Proper component placement is crucial for several reasons:
- Signal integrity: Components should be placed to minimize the length of critical signal paths and avoid crosstalk between adjacent traces.
- Thermal management: Heat-generating components should be distributed evenly across the board and placed away from temperature-sensitive components.
- Manufacturing: Components should be placed with sufficient spacing to allow for automated assembly and soldering processes.
Trace Routing
Trace routing refers to the placement and design of the copper traces that connect the components on the PCB. Key considerations include:
- Trace width: The width of the traces should be sufficient to carry the required current without excessive heating or voltage drop.
- Trace spacing: Adjacent traces should be spaced far enough apart to minimize crosstalk and ensure manufacturing tolerances are met.
- Vias: The number and placement of vias should be optimized to minimize signal degradation and improve manufacturability.
Power and Ground Planes
Incorporating power and ground planes in a multi-layer PCB can significantly improve the performance and reliability of the circuit. These planes provide a low-impedance path for power distribution and help to reduce noise and electromagnetic interference (EMI).
Design for Manufacturing (DFM)
DFM principles should be applied throughout the PCB design process to ensure the board can be manufactured efficiently and cost-effectively. This includes:
- Adhering to the manufacturer’s design rules and guidelines
- Using standard component sizes and footprints
- Avoiding unnecessarily small features or tight tolerances
- Incorporating adequate test points and fiducials for automated assembly and testing
Applications of Rigid PCBs
Rigid PCBs find applications in a wide range of industries and products, including:
- Consumer electronics: Smartphones, laptops, televisions, and home appliances
- Automotive: Engine control units, infotainment systems, and sensors
- Industrial: Process control systems, automation equipment, and power electronics
- Medical: Diagnostic devices, monitoring equipment, and implantable devices
- Aerospace and defense: Avionics, communication systems, and military equipment
Frequently Asked Questions (FAQ)
1. What is the difference between a Rigid PCB and a Flexible PCB?
A Rigid PCB is made from a solid, non-flexible substrate material, while a Flexible PCB is made from a thin, flexible polymer film. Rigid PCBs are more durable and cost-effective but cannot be bent or folded, while Flexible PCBs offer greater design freedom and can be used in applications that require flexibility or space constraints.
2. Can Rigid PCBs be used in high-frequency applications?
Yes, Rigid PCBs can be used in high-frequency applications, such as RF and microwave circuits. However, special design considerations, such as controlled impedance routing and the use of low-loss substrate materials, may be necessary to ensure optimal performance.
3. What is the typical turnaround time for Rigid PCB manufacturing?
The turnaround time for Rigid PCB manufacturing varies depending on the complexity of the design, the number of layers, and the manufacturing capabilities of the PCB fabricator. Simple, double-sided boards can typically be manufactured in 1-2 weeks, while complex, multi-layer boards may take 3-4 weeks or longer.
4. How can I ensure my Rigid PCB design is manufacturable?
To ensure your Rigid PCB design is manufacturable, follow these guidelines:
- Adhere to the manufacturer’s design rules and guidelines
- Use standard component sizes and footprints
- Avoid unnecessarily small features or tight tolerances
- Incorporate adequate test points and fiducials for automated assembly and testing
- Communicate with your PCB fabricator early in the design process to discuss any potential manufacturability issues
5. What is the maximum number of layers that can be achieved in a Rigid PCB?
The maximum number of layers in a Rigid PCB is not strictly limited but is typically constrained by practical and economic considerations. Most commercial PCB Fabricators can manufacture boards with up to 40 layers, while some specialized facilities can produce boards with 60 or more layers. However, as the number of layers increases, so does the complexity and cost of the manufacturing process.
Conclusion
Rigid PCBs are the foundation of modern electronic devices, offering a reliable and cost-effective solution for interconnecting electronic components. By understanding the structure, manufacturing process, and design considerations of Rigid PCBs, beginners can create robust and efficient circuits for a wide range of applications.
As technology continues to advance, the demand for more complex and high-performance Rigid PCBs will only increase. By staying up-to-date with the latest design techniques and manufacturing capabilities, designers and engineers can unlock the full potential of Rigid PCBs and create innovative electronic products that shape our future.
0 Comments