Introduction to Rigid-Flex PCBs
Rigid-Flex PCBs are a unique combination of rigid and flexible printed circuit boards that offer numerous advantages over traditional PCB designs. By integrating both rigid and flexible sections into a single board, designers can create more compact, lightweight, and reliable electronic devices. This article will explore the benefits of Rigid-Flex PCBs, design considerations, manufacturing processes, and best practices for improving reliability.
Benefits of Rigid-Flex PCBs
Space Savings and Miniaturization
One of the primary advantages of rigid-flex PCBs is their ability to save space and enable miniaturization. By combining rigid and flexible sections, designers can create 3D configurations that minimize the overall footprint of the device. This is particularly beneficial for applications where space is limited, such as wearable electronics, medical devices, and aerospace systems.
Reduced Weight
Rigid-flex PCBs can significantly reduce the weight of electronic devices compared to traditional PCB assemblies. By eliminating the need for connectors and cables between rigid boards, Rigid-Flex Designs minimize the number of components required. This weight reduction is crucial for applications where every gram counts, such as satellites, drones, and portable devices.
Improved Reliability
Rigid-flex PCBs offer improved reliability compared to traditional PCB assemblies. By eliminating connectors and cables, rigid-flex designs reduce the number of potential failure points. Additionally, the flexible sections can absorb stress and vibration, reducing the risk of mechanical failures. This enhanced reliability is essential for applications that require long-term durability, such as automotive electronics and industrial control systems.
Design Considerations for Rigid-Flex PCBs
Layer Stackup
Designing the layer stackup for a rigid-flex PCB requires careful consideration. The rigid sections typically consist of multiple layers of copper and dielectric material, while the flexible sections use thinner, more flexible materials. Designers must ensure that the layer stackup provides adequate signal integrity, power distribution, and mechanical stability.
Layer | Material | Thickness |
---|---|---|
Top Cover | Polyimide | 0.025mm |
Top Copper | Copper | 0.018mm |
Dielectric | Polyimide | 0.050mm |
Bottom Copper | Copper | 0.018mm |
Bottom Cover | Polyimide | 0.025mm |
Example of a simple rigid-flex layer stackup
Bend Radius
The bend radius is a critical design parameter for rigid-flex PCBs. It determines the minimum radius that the flexible sections can be bent without causing damage or degrading performance. Designers must consider the bend radius when defining the mechanical outline of the device and ensure that the flexible sections can accommodate the required bending.
Flex Material | Minimum Bend Radius |
---|---|
Polyimide | 6x material thickness |
Polyester | 8x material thickness |
PTFE | 10x material thickness |
Minimum bend radii for common flexible materials
Controlled Impedance
Maintaining controlled impedance is essential for high-speed signals in rigid-flex PCBs. Designers must carefully select the dielectric materials and copper thickness to achieve the desired characteristic impedance. The flexible sections may require different dielectric materials or copper weights compared to the rigid sections to maintain consistent impedance throughout the board.
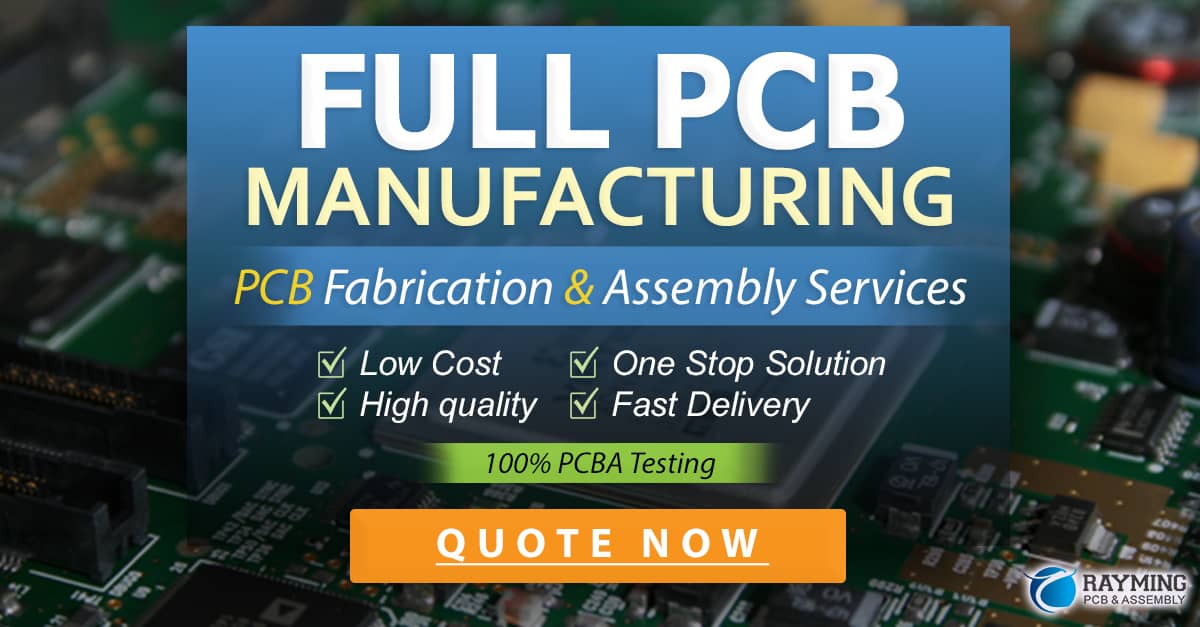
Manufacturing Processes for Rigid-Flex PCBs
Material Selection
Selecting the appropriate materials for rigid-flex PCBs is crucial for ensuring reliability and performance. The rigid sections typically use standard FR-4 or high-performance materials like Rogers or Isola. The flexible sections use thin, flexible substrates such as polyimide or polyester. Adhesives and cover layers must also be carefully chosen to provide adequate bonding and protection.
Fabrication Techniques
Manufacturing rigid-flex PCBs requires specialized fabrication techniques. The process typically involves the following steps:
- Fabricating the rigid and flexible sections separately
- Laminating the flexible sections to the rigid sections using adhesives
- Drilling and plating through-holes to interconnect the layers
- Patterning and etching the copper layers
- Applying solder mask and silkscreen
- Cutting and profiling the final board shape
Testing and Inspection
Thorough testing and inspection are essential for ensuring the quality and reliability of rigid-flex PCBs. Common testing methods include:
- Continuity testing to verify electrical connections
- Insulation resistance testing to detect shorts and leakage
- Impedance testing to ensure controlled impedance
- Microsectioning to verify layer stackup and adhesion
- Flex testing to validate the mechanical integrity of the flexible sections
Best Practices for Improving Rigid-Flex Reliability
Design for Manufacturability (DFM)
Designing rigid-flex PCBs with manufacturability in mind can significantly improve reliability. Designers should follow DFM guidelines, such as:
- Providing adequate clearances and tolerances
- Avoiding acute angles and sharp corners
- Using teardrop pads to reinforce trace-to-pad connections
- Minimizing the number of layers in the flexible sections
- Specifying appropriate hole sizes and pad diameters
Strain Relief
Incorporating strain relief features can help prevent mechanical failures in rigid-flex PCBs. Techniques for strain relief include:
- Using gradual bends instead of sharp folds
- Adding stiffeners or reinforcements in high-stress areas
- Providing adequate slack in the flexible sections
- Using stress-relieving curves or serpentine patterns
Thermal Management
Proper thermal management is crucial for maintaining the reliability of rigid-flex PCBs. Designers should consider the following:
- Using thermally conductive materials in the layer stackup
- Providing adequate copper coverage for heat dissipation
- Incorporating thermal vias to transfer heat between layers
- Using heatsinks or other cooling solutions when necessary
FAQ
Q: What are the advantages of using rigid-flex PCBs over traditional PCB assemblies?
A: Rigid-flex PCBs offer several advantages, including space savings, weight reduction, improved reliability, and the ability to create 3D configurations. By combining rigid and flexible sections into a single board, designers can minimize the overall footprint and eliminate the need for connectors and cables.
Q: How do I determine the appropriate bend radius for a rigid-flex PCB?
A: The appropriate bend radius depends on the thickness and material of the flexible sections. As a general rule, the minimum bend radius should be at least 6 times the material thickness for polyimide, 8 times for polyester, and 10 times for PTFE. Designers should consult the manufacturer’s guidelines and perform mechanical testing to validate the bend radius.
Q: What materials are commonly used for the flexible sections of rigid-flex PCBs?
A: The most common materials for the flexible sections of rigid-flex PCBs are polyimide and polyester. Polyimide offers excellent thermal and mechanical properties, while polyester is more cost-effective for less demanding applications. Other materials, such as PTFE, may be used for specialized requirements.
Q: How can I ensure controlled impedance in rigid-flex PCBs?
A: To ensure controlled impedance in rigid-flex PCBs, designers must carefully select the dielectric materials and copper thickness. The flexible sections may require different materials or copper weights compared to the rigid sections to maintain consistent impedance. Designers should perform impedance calculations and simulations to verify the design and work closely with the manufacturer to ensure proper fabrication.
Q: What testing methods are used to ensure the reliability of rigid-flex PCBs?
A: Common testing methods for rigid-flex PCBs include continuity testing, insulation resistance testing, impedance testing, microsectioning, and flex testing. Continuity testing verifies electrical connections, while insulation resistance testing detects shorts and leakage. Impedance testing ensures controlled impedance, and microsectioning verifies layer stackup and adhesion. Flex testing validates the mechanical integrity of the flexible sections.
Conclusion
Rigid-flex PCBs offer numerous benefits over traditional PCB assemblies, including space savings, weight reduction, and improved reliability. By carefully considering design factors such as layer stackup, bend radius, and controlled impedance, designers can create robust and reliable rigid-flex designs. Specialized manufacturing processes and thorough testing are essential for ensuring the quality and performance of rigid-flex PCBs. By following best practices for design, strain relief, and thermal management, designers can further enhance the reliability of their rigid-flex designs. As electronic devices continue to become smaller, lighter, and more complex, rigid-flex PCBs will play an increasingly important role in enabling the next generation of innovative products.
0 Comments