Introduction to PCB assemblies
Printed Circuit Board (PCB) assemblies are essential components in modern electronic devices. They consist of a board made of insulating materials, such as fiberglass or plastic, with conductive tracks, pads, and other features etched onto the surface. PCB assemblies are used to mechanically support and electrically connect electronic components using conductive pathways, tracks, or signal traces etched from copper sheets laminated onto a non-conductive substrate.
Types of PCB Assemblies
There are several types of PCB assemblies, each with its own unique characteristics and applications:
-
Single-sided PCBs: These have conductive tracks on one side of the board only. They are the simplest and most cost-effective type of PCB assembly.
-
Double-sided PCBs: These have conductive tracks on both sides of the board, allowing for more complex circuits and higher component density.
-
Multi-layer PCBs: These consist of multiple layers of conductive tracks separated by insulating layers. They are used for complex, high-density applications.
-
Flexible PCBs: These are made from flexible materials, allowing them to bend and fit into tight spaces.
-
Rigid-Flex PCBs: These combine rigid and flexible sections, providing the benefits of both types of PCBs.
Type of PCB Assembly | Characteristics | Applications |
---|---|---|
Single-sided PCBs | – One conductive layer – Simple, cost-effective |
– Simple electronic devices – Low-cost applications |
Double-sided PCBs | – Two conductive layers – More complex circuits |
– Moderately complex devices – Higher component density |
Multi-layer PCBs | – Multiple conductive layers – High-density |
– Complex, high-performance devices – Aerospace, medical, etc. |
Flexible PCBs | – Flexible materials – Can bend and fit in tight spaces |
– Wearable electronics – Compact devices |
Rigid-Flex PCBs | – Combination of rigid and flexible sections – Versatile |
– Devices requiring both rigidity and flexibility – Space-constrained applications |
ROHS Compliance in PCB Assemblies
The Restriction of Hazardous Substances (RoHS) Directive is a set of regulations that restrict the use of certain hazardous materials in the manufacture of electronic and electrical equipment. The directive aims to reduce the environmental impact of electronic waste and protect human health by limiting the use of lead, mercury, cadmium, hexavalent chromium, polybrominated biphenyls (PBB), and polybrominated diphenyl ethers (PBDE) in electronic products.
Importance of ROHS Compliance
ROHS compliance is crucial for several reasons:
-
Environmental protection: By restricting the use of hazardous substances, ROHS helps reduce the environmental impact of electronic waste.
-
Human health: Limiting exposure to hazardous materials in electronic products helps protect the health of workers in the electronics industry and consumers.
-
Legal requirement: In many countries, ROHS compliance is a legal requirement for electronic products. Non-compliant products may face import bans or penalties.
-
Market access: Many consumers and businesses prefer or require ROHS-compliant products, making compliance essential for accessing these markets.
Achieving ROHS Compliance in PCB Assemblies
To ensure ROHS compliance in PCB assemblies, manufacturers must:
- Use materials and components that meet ROHS requirements
- Implement strict quality control and testing procedures to verify compliance
- Maintain accurate documentation and labeling of ROHS-compliant products
- Stay up-to-date with changes to ROHS regulations and adapt their processes accordingly
PCB Assembly Prototypes
Prototyping is an essential step in the development of PCB assemblies. It allows designers and engineers to test and refine their designs before committing to full-scale production.
Benefits of PCB Assembly Prototyping
-
Design validation: Prototyping allows designers to test their PCB layouts and identify any issues or areas for improvement.
-
Functionality testing: Prototypes can be used to verify the functionality of the PCB assembly and ensure it meets the desired specifications.
-
Cost savings: By identifying and addressing issues during the prototyping stage, manufacturers can avoid costly mistakes and rework in full-scale production.
-
Time-to-market: Prototyping helps streamline the development process, allowing manufacturers to bring their products to market faster.
ROHS-Compliant PCB Assembly Prototyping
When creating PCB assembly prototypes, it is essential to use ROHS-compliant materials and processes. This ensures that the final product will meet ROHS requirements and avoids the need for costly redesigns or rework later in the development process.
To create ROHS-compliant PCB assembly prototypes, manufacturers should:
- Use ROHS-compliant PCB materials, such as lead-free solder and copper foils
- Select ROHS-compliant components from reliable suppliers
- Implement ROHS-compliant manufacturing processes, such as lead-free soldering and avoiding the use of prohibited substances
- Maintain accurate documentation and labeling of ROHS-compliant prototypes
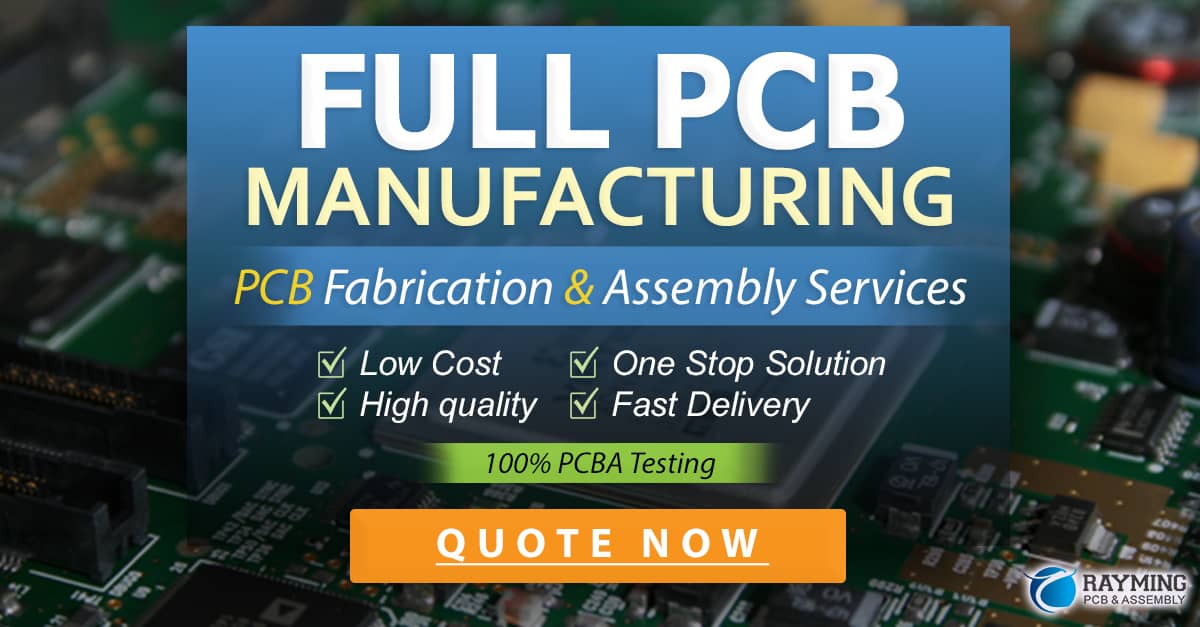
Choosing a PCB Assembly Provider
When selecting a PCB assembly provider, it is essential to choose a company that offers ROHS-compliant services and has experience in creating high-quality PCB assembly prototypes.
Factors to Consider
-
ROHS compliance: Ensure the provider offers ROHS-compliant PCB assembly services and has a track record of meeting ROHS requirements.
-
Prototyping capabilities: Look for a provider with experience in creating high-quality PCB assembly prototypes and the ability to handle your specific requirements.
-
Quality control: Choose a provider with strict quality control processes in place to ensure the consistency and reliability of their PCB assemblies.
-
Technical expertise: Select a provider with a knowledgeable and experienced team that can provide guidance and support throughout the PCB assembly process.
-
Cost and lead times: Consider the provider’s pricing and lead times to ensure they align with your budget and project timeline.
Questions to Ask a Potential PCB Assembly Provider
- What experience do you have in creating ROHS-compliant PCB assemblies and prototypes?
- What quality control processes do you have in place to ensure the consistency and reliability of your PCB assemblies?
- Can you provide examples of similar projects you have completed successfully?
- What are your typical lead times for PCB assembly prototypes and full-scale production?
- How do you handle issues or changes that may arise during the PCB assembly process?
Conclusion
ROHS-compliant PCB assemblies and prototypes are essential for creating high-quality, environmentally-friendly electronic products. By choosing a PCB assembly provider with experience in ROHS compliance and prototyping, manufacturers can ensure their products meet regulatory requirements and perform as intended.
When selecting a PCB assembly provider, it is crucial to consider factors such as ROHS compliance, prototyping capabilities, quality control, technical expertise, and cost and lead times. By asking the right questions and carefully evaluating potential providers, manufacturers can find a partner that will help them bring their PCB assembly projects to success.
Frequently Asked Questions
-
What is ROHS compliance?
ROHS (Restriction of Hazardous Substances) compliance refers to the adherence to a set of regulations that restrict the use of certain hazardous materials in the manufacture of electronic and electrical equipment. These regulations aim to reduce the environmental impact of electronic waste and protect human health. -
Why is ROHS compliance important for PCB assemblies?
ROHS compliance is important for PCB assemblies because it ensures that the products meet regulatory requirements, reduces the environmental impact of electronic waste, and protects the health of workers and consumers. Additionally, many consumers and businesses prefer or require ROHS-compliant products, making compliance essential for accessing these markets. -
What are the benefits of PCB assembly prototyping?
PCB assembly prototyping offers several benefits, including design validation, functionality testing, cost savings, and faster time-to-market. By creating prototypes, designers and engineers can test and refine their designs before committing to full-scale production, avoiding costly mistakes and streamlining the development process. -
How can I ensure my PCB assembly prototypes are ROHS-compliant?
To ensure your PCB assembly prototypes are ROHS-compliant, use ROHS-compliant PCB materials and components, implement ROHS-compliant manufacturing processes, and maintain accurate documentation and labeling. Choose a PCB assembly provider with experience in creating ROHS-compliant prototypes and a track record of meeting ROHS requirements. -
What should I look for when choosing a PCB assembly provider?
When choosing a PCB assembly provider, look for a company that offers ROHS-compliant services, has experience in creating high-quality PCB assembly prototypes, implements strict quality control processes, and has a knowledgeable and experienced team. Consider their pricing and lead times to ensure they align with your budget and project timeline, and ask for examples of similar projects they have completed successfully.
0 Comments