What are Rigid-Flex PCBs?
Rigid-flex PCBs are a type of printed circuit board that combines both rigid and flexible substrates. The rigid portions of the board provide structural support and stability, while the flexible portions allow for bending and folding, enabling more compact and space-efficient designs. This combination of rigidity and flexibility makes rigid-flex PCBs ideal for applications that require high reliability, durability, and flexibility.
Advantages of Rigid-Flex PCBs
Rigid-flex PCBs offer several advantages over traditional rigid or flexible PCBs, including:
- Space savings: By combining rigid and flexible substrates, rigid-flex PCBs can be designed to fit into smaller spaces, reducing the overall size and weight of the device.
- Increased reliability: The flexible portions of the board eliminate the need for connectors and cables, reducing the number of potential failure points and increasing overall reliability.
- Improved signal integrity: The elimination of connectors and cables also reduces signal loss and interference, resulting in better signal integrity and performance.
- Enhanced durability: Rigid-flex PCBs are more resistant to vibration, shock, and thermal stress, making them suitable for harsh environments and demanding applications.
- Cost-effective: Although the initial cost of rigid-flex PCBs may be higher than traditional PCBs, the reduced assembly time, fewer components, and improved reliability can lead to long-term cost savings.
Types of Rigid-Flex PCBs Offered by RAYPCB Technology
RAYPCB Technology offers several types of rigid-flex PCBs to meet the diverse needs of their customers:
1. Single-Layer Rigid-Flex PCBs
Single-layer rigid-flex PCBs consist of a single layer of flexible substrate laminated between two rigid substrates. This type of board is suitable for simple applications that require minimal flexibility and low cost.
Feature | Description |
---|---|
Layers | 1 flexible layer |
Thickness | 0.2 mm – 0.3 mm |
Material | Polyimide (PI) |
Applications | Simple devices, low-cost products |
2. Double-Layer Rigid-Flex PCBs
Double-layer rigid-flex PCBs have two layers of flexible substrate laminated between rigid substrates. This configuration allows for more complex routing and increased flexibility compared to single-layer boards.
Feature | Description |
---|---|
Layers | 2 flexible layers |
Thickness | 0.3 mm – 0.5 mm |
Material | Polyimide (PI) |
Applications | Moderate complexity devices, consumer electronics |
3. Multi-Layer Rigid-Flex PCBs
Multi-layer rigid-flex PCBs consist of three or more layers of flexible substrate laminated between rigid substrates. These boards offer the highest level of complexity and flexibility, making them suitable for the most demanding applications.
Feature | Description |
---|---|
Layers | 3 or more flexible layers |
Thickness | 0.5 mm – 2.0 mm |
Material | Polyimide (PI) |
Applications | High-complexity devices, aerospace, medical equipment |
4. Rigid-Flex PCBs with Stiffeners
Rigid-flex PCBs with stiffeners incorporate additional rigid layers in specific areas of the flexible substrate to provide extra support and stability. This design is useful for applications that require a balance between flexibility and mechanical strength.
Feature | Description |
---|---|
Layers | Flexible layers with rigid stiffeners |
Thickness | Varies based on design |
Material | Polyimide (PI) and FR-4 |
Applications | Devices requiring targeted mechanical support |
5. High-Density Interconnect (HDI) Rigid-Flex PCBs
HDI rigid-flex PCBs combine the benefits of rigid-flex technology with the high-density routing capabilities of HDI PCBs. These boards feature fine pitch components, micro vias, and blind and buried vias, allowing for even greater space savings and performance.
Feature | Description |
---|---|
Layers | Multiple flexible and rigid layers |
Thickness | Varies based on design |
Material | Polyimide (PI) and high-performance laminates |
Applications | High-density devices, miniaturized products |
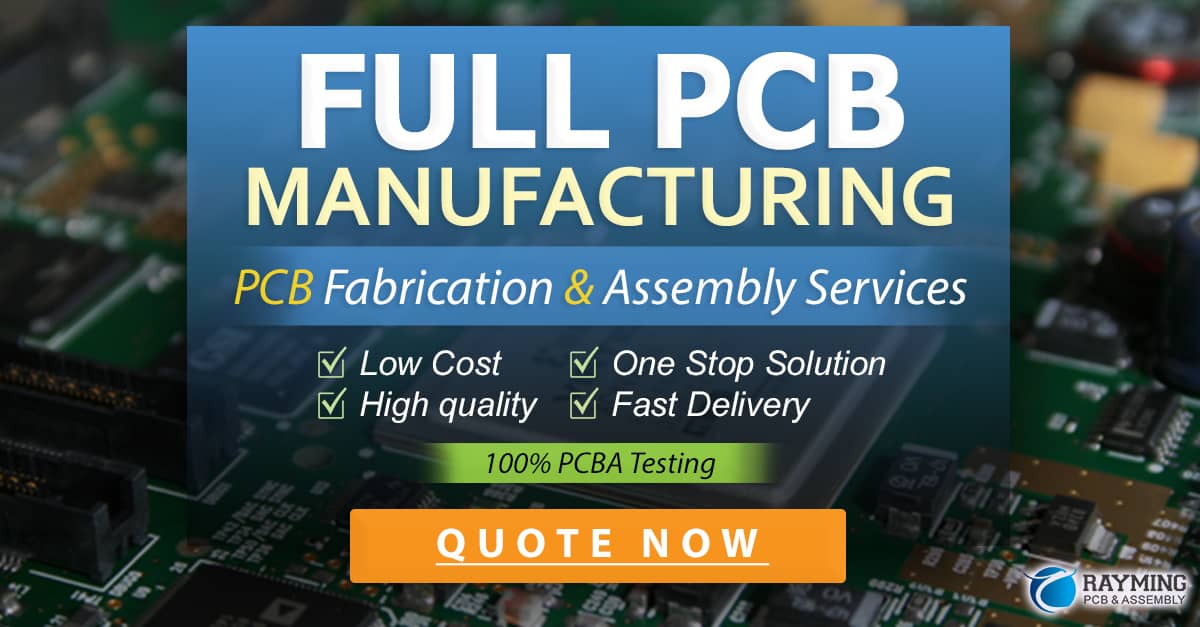
Applications of Rigid-Flex PCBs
Rigid-flex PCBs are used in a wide range of industries and applications, including:
- Aerospace and defense: Avionics, satellite systems, and military equipment
- Medical devices: Implantable devices, diagnostic equipment, and wearable technology
- Automotive: In-vehicle entertainment systems, navigation systems, and sensors
- Consumer electronics: Smartphones, tablets, and wearables
- Industrial automation: Robotics, machine vision systems, and process control equipment
RAYPCB Technology’s Rigid-Flex PCB Manufacturing Capabilities
RAYPCB Technology has state-of-the-art manufacturing facilities and a team of experienced engineers to design and produce high-quality rigid-flex PCBs. Their capabilities include:
- Advanced materials: RAYPCB Technology works with a variety of flexible and rigid substrate materials, including polyimide (PI), FR-4, and high-performance laminates.
- High-density routing: The company can produce HDI rigid-flex PCBs with fine pitch components, micro vias, and blind and buried vias.
- Controlled impedance: RAYPCB Technology can design and manufacture rigid-flex PCBs with controlled impedance to ensure optimal signal integrity and performance.
- Comprehensive testing: All rigid-flex PCBs undergo rigorous testing, including electrical, mechanical, and environmental testing, to ensure the highest quality and reliability.
Designing Rigid-Flex PCBs
Designing rigid-flex PCBs requires careful consideration of several factors, including:
- Material selection: Choose the appropriate flexible and rigid substrate materials based on the application’s requirements, such as temperature range, flexibility, and durability.
- Bend radius: Ensure that the minimum bend radius of the flexible portions is within the material’s specifications to avoid damage and ensure long-term reliability.
- Stackup design: Develop an optimal stackup that balances the number of layers, thickness, and material properties to meet the application’s requirements.
- Routing and placement: Consider the placement of components and routing of traces to minimize stress on the flexible portions and ensure proper functionality.
- Mechanical support: Incorporate stiffeners or other mechanical support structures as needed to provide additional stability and protection for the flexible portions.
Advantages of Working with RAYPCB Technology
Partnering with RAYPCB Technology for rigid-flex PCB design and manufacturing offers several advantages, including:
- Expertise: RAYPCB Technology has a team of experienced engineers who can provide guidance and support throughout the design and manufacturing process.
- Advanced facilities: The company has state-of-the-art manufacturing facilities equipped with the latest technology to produce high-quality rigid-flex PCBs.
- Quality assurance: RAYPCB Technology follows strict quality control procedures and conducts comprehensive testing to ensure that all rigid-flex PCBs meet the highest standards of quality and reliability.
- Customization: The company can work closely with customers to develop custom rigid-flex PCB solutions tailored to their specific application requirements.
- Cost-effectiveness: RAYPCB Technology offers competitive pricing and can help customers optimize their designs for cost-effectiveness without compromising quality or performance.
Frequently Asked Questions (FAQ)
- What is the minimum bend radius for rigid-flex PCBs?
-
The minimum bend radius depends on the thickness and material properties of the flexible substrate. Generally, the minimum bend radius is 6-10 times the thickness of the flexible layer. RAYPCB Technology can provide guidance on the appropriate bend radius for specific designs.
-
Can rigid-flex PCBs be used in high-temperature applications?
-
Yes, rigid-flex PCBs can be designed for high-temperature applications by selecting appropriate materials, such as polyimide (PI), which can withstand temperatures up to 260°C. RAYPCB Technology can help customers choose the best materials for their specific application requirements.
-
How do I determine the number of layers needed for my rigid-flex PCB?
-
The number of layers needed depends on the complexity of the circuit, the required functionality, and the space constraints of the application. RAYPCB Technology’s experienced engineers can help customers determine the optimal number of layers for their specific design.
-
What is the typical lead time for rigid-flex PCBs?
-
Lead times for rigid-flex PCBs can vary depending on the complexity of the design, the materials required, and the quantity ordered. RAYPCB Technology strives to provide competitive lead times and can work with customers to meet their specific timeline requirements.
-
How do I get started with designing a rigid-flex PCB for my application?
- To get started, customers can contact RAYPCB Technology with their application requirements and any initial design concepts. The company’s engineers will work closely with the customer to refine the design, select the appropriate materials, and optimize the layout for manufacturing. RAYPCB Technology can also provide prototyping services to help customers validate their designs before moving to full-scale production.
0 Comments