Introduction to PCB Fabrication
Printed Circuit Board (PCB) fabrication is a crucial process in the electronics industry, enabling the creation of complex electronic circuits on a compact and durable substrate. PCB fabrication involves a series of steps, including design, layout, etching, drilling, and component assembly. In this article, we will delve into the intricacies of prototype PCB fabrication, exploring the various techniques, materials, and best practices involved in creating high-quality PCBs for prototyping purposes.
The Importance of Prototype PCB Fabrication
Prototype PCB fabrication plays a vital role in the product development lifecycle. It allows engineers and designers to test and validate their designs before committing to large-scale production. By creating prototypes, potential issues can be identified and rectified early, saving time and resources in the long run. Prototype PCBs also provide an opportunity to optimize the design for manufacturability, ensuring a smooth transition to mass production.
PCB Design and Layout
Schematic Design
The first step in prototype PCB fabrication is creating a schematic design. This involves defining the electrical connections and components required for the circuit. Engineers use electronic design automation (EDA) software to create a virtual representation of the circuit, specifying the components, their values, and the interconnections between them. The schematic design serves as a blueprint for the subsequent PCB layout process.
PCB Layout
Once the schematic design is finalized, the next step is to create the PCB layout. This involves arranging the components and routing the traces on the PCB substrate. The layout designer must consider various factors, such as component placement, signal integrity, power distribution, and manufacturing constraints. EDA software is used to create the PCB layout, which generates the necessary files for fabrication, including Gerber files and drill files.
Design for Manufacturability (DFM)
During the PCB layout process, it is essential to adhere to design for manufacturability (DFM) guidelines. DFM ensures that the PCB design can be efficiently and reliably manufactured. Some key DFM considerations include:
- Minimum trace width and spacing
- Minimum drill hole size
- Copper pour and ground plane design
- Solder mask and silkscreen requirements
- Component placement and orientation
By following DFM guidelines, designers can minimize manufacturing issues and improve the overall quality of the prototype PCBs.
PCB Fabrication Techniques
Traditional Subtractive Method
The traditional subtractive method is the most commonly used technique for prototype PCB fabrication. It involves starting with a copper-clad substrate and selectively removing unwanted copper to create the desired circuit pattern. The process typically involves the following steps:
-
Copper Cladding: A substrate material, such as FR-4, is coated with a thin layer of copper on one or both sides.
-
Applying Photoresist: A photosensitive material, known as photoresist, is applied to the copper surface.
-
Exposure: The PCB layout artwork is used to create a photomask, which is placed on top of the photoresist-coated substrate. The photomask is then exposed to UV light, hardening the exposed areas of the photoresist.
-
Developing: The unexposed areas of the photoresist are removed using a chemical developer, leaving the desired circuit pattern protected by the hardened photoresist.
-
Etching: The exposed copper areas are chemically etched away, leaving only the desired circuit pattern on the substrate.
-
Stripping: The remaining photoresist is removed, revealing the final copper circuit pattern.
-
Drilling: Holes are drilled through the substrate to accommodate through-hole components and provide interconnections between layers.
-
Surface Finish: A surface finish, such as soldermask and silkscreen, is applied to the PCB to protect the copper traces and provide component markings.
The traditional subtractive method is well-suited for prototype PCB fabrication due to its versatility and relatively low cost. However, it has limitations in terms of minimum feature sizes and trace/space widths, which can impact high-density designs.
Additive Manufacturing
Additive manufacturing, also known as 3D printing, is an emerging technology in PCB fabrication. Instead of selectively removing material, additive manufacturing builds up the circuit pattern layer by layer. There are various additive manufacturing techniques used for PCB fabrication, including:
-
Inkjet Printing: Conductive ink is selectively deposited onto the substrate using inkjet printheads. Multiple layers can be printed to create the desired circuit pattern.
-
Aerosol Jet Printing: A fine aerosol mist of conductive material is precisely deposited onto the substrate using a focused jet of gas. This technique enables the creation of high-resolution features.
-
Stereolithography (SLA): A photopolymer resin is selectively cured using a laser or UV light source to build up the PCB structure layer by layer. Conductive traces can be added using conductive inks or plating processes.
Additive manufacturing offers several advantages for prototype PCB fabrication, including rapid prototyping, improved design flexibility, and the ability to create complex 3D structures. However, the technology is still maturing, and the materials and processes used may have limitations in terms of conductivity, durability, and compatibility with standard components.
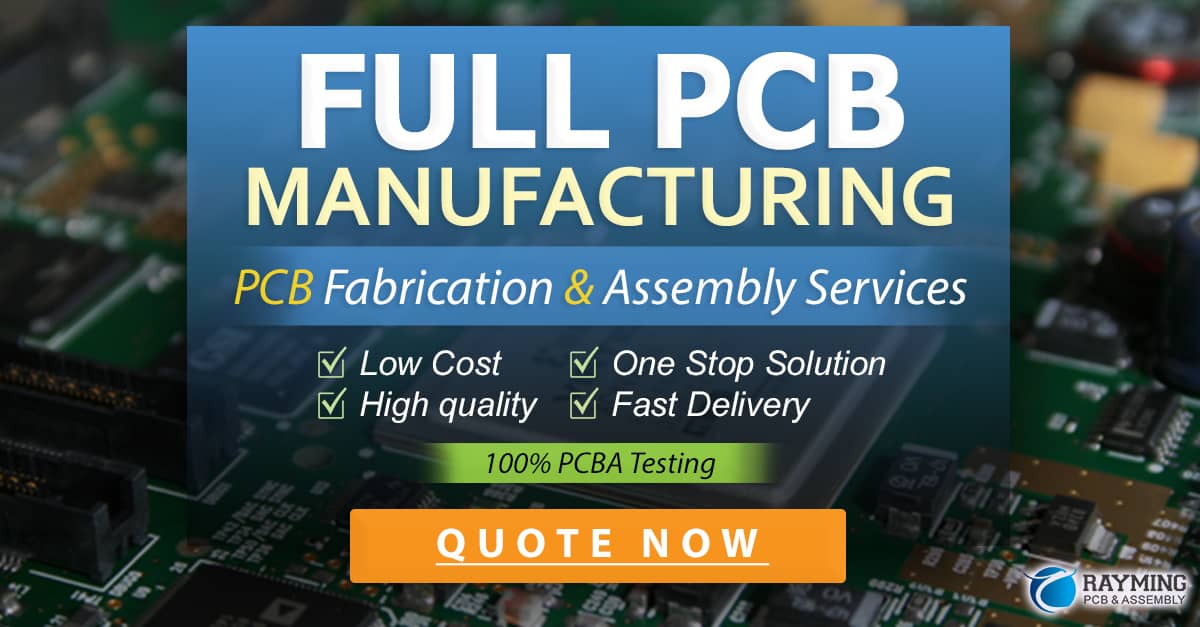
PCB Materials
Substrate Materials
The choice of substrate material is crucial in prototype PCB fabrication. The substrate provides the foundation for the circuit and influences the PCB’s electrical, thermal, and mechanical properties. Common substrate materials include:
-
FR-4: A glass-reinforced epoxy laminate, FR-4 is the most widely used substrate material for PCBs. It offers good electrical insulation, mechanical strength, and thermal stability.
-
High-Frequency Materials: For high-speed and high-frequency applications, specialized substrate materials such as Rogers, Teflon, and ceramics are used. These materials offer superior dielectric properties and controlled impedance characteristics.
-
Flexible Substrates: Flexible PCBs use thin, flexible substrate materials such as polyimide or polyester. They are used in applications that require conformability or where space constraints are a concern.
Copper Thickness
The thickness of the copper layer on the PCB substrate is an important consideration in prototype PCB fabrication. Copper thickness is typically measured in ounces per square foot (oz/ft²). Common copper thicknesses include:
- 0.5 oz/ft² (17.5 μm)
- 1 oz/ft² (35 μm)
- 2 oz/ft² (70 μm)
- 3 oz/ft² (105 μm)
Thicker copper layers offer better current-carrying capacity and improved thermal dissipation but may increase the cost and complexity of the fabrication process.
PCB Assembly
Through-Hole Assembly
Through-hole assembly involves inserting component leads through drilled holes in the PCB and soldering them to pads on the opposite side. This assembly method is well-suited for prototype PCBs due to its simplicity and compatibility with a wide range of components. Through-hole components are generally larger and more robust compared to surface-mount components.
Surface-Mount Assembly
Surface-mount assembly involves placing components directly onto pads on the PCB surface and soldering them in place. Surface-mount technology (SMT) offers several advantages, including smaller component sizes, higher component density, and improved high-frequency performance. However, SMT assembly requires precise component placement and specialized soldering techniques, which can be more challenging for prototype PCBs.
Mixed Assembly
Mixed assembly combines both through-hole and surface-mount components on the same PCB. This approach offers flexibility in component selection and can be suitable for prototype PCBs that require a mix of component types. However, mixed assembly may increase the complexity of the assembly process and require careful planning to ensure compatibility between the different component types.
Best Practices for Prototype PCB Fabrication
To ensure successful prototype PCB fabrication, consider the following best practices:
-
Design for Manufacturability: Follow DFM guidelines to minimize manufacturing issues and improve the reliability of the prototype PCBs.
-
Component Selection: Choose components that are readily available and compatible with the selected fabrication and assembly techniques.
-
Documentation: Provide clear and comprehensive documentation, including schematic diagrams, bill of materials (BOM), and assembly instructions, to facilitate accurate prototype fabrication and assembly.
-
Communication: Maintain open communication with the PCB fabrication and assembly partners to ensure that design intent is properly understood and any issues are promptly addressed.
-
Testing and Validation: Perform thorough testing and validation of the prototype PCBs to identify any design or manufacturing issues early in the development process.
Frequently Asked Questions (FAQ)
-
What is the typical turnaround time for prototype PCB fabrication?
The turnaround time for prototype PCB fabrication varies depending on the complexity of the design, the selected fabrication technique, and the workload of the fabrication facility. Typical turnaround times range from a few days to a few weeks. Rush services may be available for faster turnaround times, but they often come at a higher cost. -
How much does prototype PCB fabrication cost?
The cost of prototype PCB fabrication depends on several factors, including the PCB size, layer count, material selection, and quantity. Prototype quantities typically range from a few pieces to a few dozen, and the cost per unit is generally higher compared to large-scale production. It’s best to request quotes from multiple PCB fabrication providers to compare prices and services. -
What files are needed for prototype PCB fabrication?
To fabricate prototype PCBs, the following files are typically required: - Gerber files: These files contain the layer-by-layer information for the PCB, including copper layers, solder mask, and silkscreen.
- Drill files: These files specify the location, size, and type of holes to be drilled in the PCB.
- Pick and place files: These files provide information for automated component placement during assembly.
-
Bill of Materials (BOM): The BOM lists all the components required for the PCB assembly, including their quantities, part numbers, and specifications.
-
Can I fabricate prototype PCBs in-house?
In-house prototype PCB fabrication is possible, but it requires specialized equipment, materials, and expertise. For simple, single-layer designs, manual fabrication techniques such as toner transfer or photo-etching can be used. However, for more complex, multi-layer designs, it is generally more cost-effective and time-efficient to outsource the fabrication to a professional PCB fabrication facility. -
How can I ensure the quality of my prototype PCBs?
To ensure the quality of prototype PCBs, consider the following: - Choose a reputable PCB fabrication partner with a proven track record of quality and reliability.
- Provide clear and accurate design files and specifications to minimize the risk of manufacturing errors.
- Specify appropriate quality control measures, such as electrical testing, visual inspection, and cross-sectioning, to verify the PCB’s integrity.
- Conduct thorough testing and validation of the assembled prototype PCBs to identify any issues related to design, fabrication, or assembly.
Conclusion
Prototype PCB fabrication is a critical step in the electronics product development process. It enables designers and engineers to validate their designs, identify potential issues, and optimize the PCB for manufacturability. By understanding the various fabrication techniques, materials, and best practices involved in prototype PCB fabrication, designers can make informed decisions and ensure the successful realization of their electronic circuits.
As technology advances, new techniques and materials continue to emerge, offering improved capabilities and possibilities for prototype PCB fabrication. Additive manufacturing, for example, holds promise for rapid prototyping and the creation of complex, three-dimensional PCB structures. However, traditional subtractive methods remain the mainstay of prototype PCB fabrication due to their reliability, affordability, and compatibility with a wide range of materials and components.
Ultimately, the choice of fabrication technique, materials, and assembly methods depends on the specific requirements of the project, including the design complexity, performance demands, timeline, and budget. By collaborating closely with PCB fabrication and assembly partners, designers can navigate the challenges of prototype PCB fabrication and bring their innovative electronic products to life.
0 Comments