Introduction to PCB Assembly
Printed Circuit Board (PCB) assembly is a crucial process in the electronics manufacturing industry. It involves the placement and soldering of electronic components onto a PCB to create a functional electronic device. PCB assembly companies play a vital role in bringing electronic products to life, from small prototypes to large-scale production runs.
In this article, we will focus on prototype PCB assembly companies and their importance in the product development process. We will explore the various aspects of prototype PCB assembly, including the benefits, process, and key considerations when choosing a prototype PCB assembly company.
The Importance of Prototype PCB Assembly
Prototype PCB assembly is an essential step in the product development lifecycle. It allows designers and engineers to test and validate their designs before committing to full-scale production. By creating a physical prototype, companies can identify and address any issues or design flaws early on, saving time and money in the long run.
Here are some key benefits of prototype PCB assembly:
-
Design Validation: Prototype PCB assembly enables designers to test their designs in real-world scenarios. This helps identify any potential issues, such as signal integrity problems, power distribution challenges, or component compatibility issues.
-
Functionality Testing: With a functional prototype, engineers can perform thorough testing to ensure that the device meets the desired specifications and performance requirements. This includes testing for functionality, reliability, and durability.
-
Cost Reduction: Identifying and addressing design issues early in the development process can significantly reduce costs. By catching problems during the prototype stage, companies can avoid expensive redesigns and rework during mass production.
-
Time-to-Market: Prototype PCB assembly allows companies to quickly iterate on their designs and make necessary improvements. This accelerated development process helps companies bring their products to market faster, gaining a competitive edge.
-
Investor and Customer Confidence: Having a functional prototype can be a powerful tool when seeking investment or presenting to potential customers. It demonstrates the feasibility and potential of the product, building confidence and credibility.
The Prototype PCB Assembly Process
The prototype PCB assembly process typically involves several key steps. Understanding these steps can help you better prepare your design files and communicate effectively with your chosen assembly company.
-
Design Review: The first step is to review the PCB design files to ensure they are complete, accurate, and ready for manufacturing. This includes checking for design rule violations, component placement, and manufacturability.
-
Bill of Materials (BOM) Preparation: The BOM is a comprehensive list of all the components required for the assembly. It should include part numbers, quantities, and any special instructions or requirements.
-
PCB Fabrication: Once the design files are finalized, the bare PCBs are fabricated according to the specified material, thickness, and copper weight. The PCBs undergo a series of processes, including etching, drilling, and surface finishing.
-
Component Sourcing: The assembly company procures the necessary components based on the BOM. This may involve purchasing from distributors, manufacturers, or using customer-supplied components.
-
Assembly: The actual assembly process begins with the placement of components onto the PCB. This can be done manually for small quantities or using automated pick-and-place machines for larger volumes. The components are then soldered onto the board using various techniques, such as reflow soldering or wave soldering.
-
Inspection and Testing: After assembly, the boards undergo thorough inspection and testing to ensure proper functionality and quality. This may include visual inspection, automated optical inspection (AOI), X-ray inspection, and functional testing.
-
Rework and Debugging: If any issues are identified during inspection or testing, the boards may require rework or debugging. This involves resolving soldering defects, replacing faulty components, or making design modifications.
-
Final Inspection and Packaging: Once the boards have passed all inspections and tests, they undergo a final quality check before being packaged and shipped to the customer.
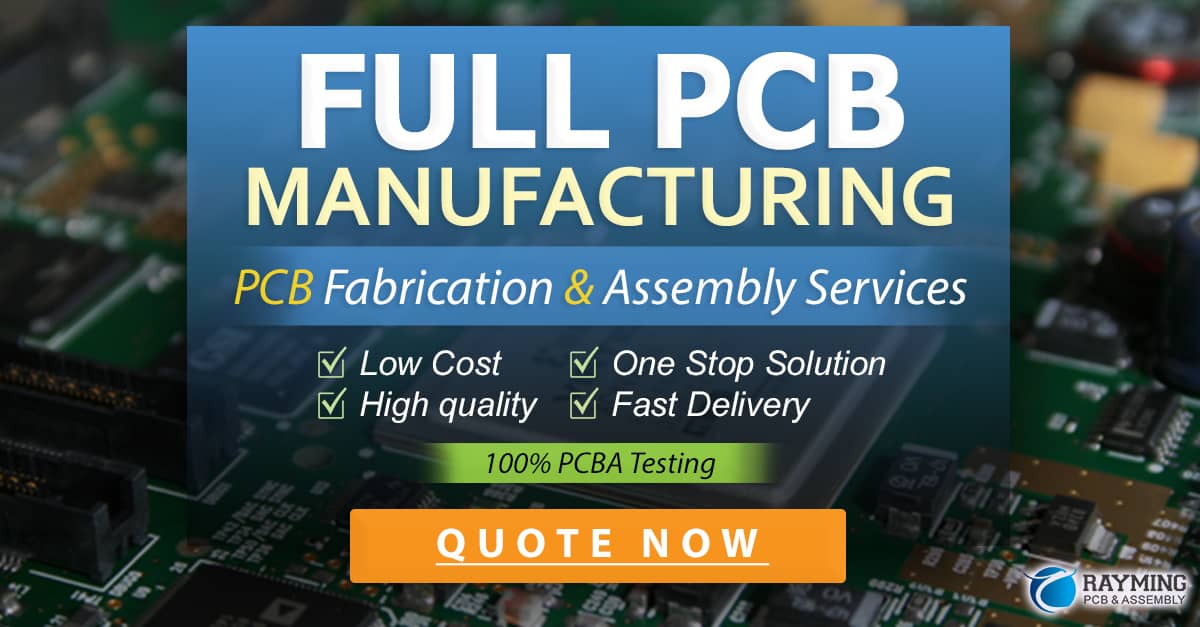
Choosing a Prototype PCB Assembly Company
Selecting the right prototype PCB assembly company is crucial for the success of your project. Here are some key factors to consider when evaluating potential partners:
-
Experience and Expertise: Look for a company with a proven track record in prototype PCB assembly. They should have experience working with a wide range of PCB technologies, components, and assembly techniques.
-
Quality Standards: Ensure that the company adheres to strict quality standards and has a robust quality management system in place. This may include certifications such as ISO 9001, IPC-A-610, or J-STD-001.
-
Turnaround Time: Prototype projects often have tight deadlines. Choose a company that offers fast turnaround times without compromising on quality. Some companies specialize in quick-turn prototype assembly, offering lead times as short as 24-48 hours.
-
Design Support: A good prototype PCB assembly company should offer design support services to help optimize your design for manufacturability. This may include design rule checks (DRC), bill of materials (BOM) review, and component selection assistance.
-
Communication and Collaboration: Clear communication and collaboration are essential for a successful prototype project. Look for a company that is responsive, proactive, and willing to work closely with your team to address any challenges or requirements.
-
Pricing and Value: While cost is an important consideration, it should not be the sole determining factor. Consider the overall value provided by the assembly company, including quality, service, and support. A slightly higher price may be justified if it results in a superior prototype and a smoother development process.
-
Scalability: If you plan to transition from prototyping to low-volume or high-volume production, consider a company that can support your long-term manufacturing needs. This can help ensure a seamless transition and maintain consistency in quality and processes.
PCB Assembly Techniques
Prototype PCB assembly companies employ various techniques to assemble components onto the PCB. The choice of technique depends on factors such as component package types, board complexity, and production volume. Here are some common PCB assembly techniques:
-
Through-Hole Assembly: Through-hole components have leads that are inserted into holes drilled in the PCB and soldered onto the opposite side. This technique is suitable for larger components and provides strong mechanical connections. However, it is more labor-intensive and requires more board space compared to surface mount assembly.
-
Surface Mount Assembly: Surface mount components are placed directly onto the surface of the PCB and soldered using reflow or wave soldering processes. Surface mount technology (SMT) allows for smaller component sizes, higher component density, and automated assembly. It is the most common assembly technique for modern PCBs.
-
Mixed Assembly: Some PCBs require a combination of through-hole and surface mount components. Mixed assembly involves placing and soldering both types of components onto the same board. This technique is used when certain components are only available in through-hole packages or when specific mechanical or electrical requirements dictate the use of through-hole components.
-
Automated Assembly: Automated assembly uses pick-and-place machines to place components onto the PCB with high speed and precision. These machines can handle a wide range of component sizes and types, from small chip resistors to large BGA packages. Automated assembly is essential for high-volume production and ensures consistent placement accuracy.
-
Manual Assembly: For low-volume prototypes or complex boards with unusual components, manual assembly may be necessary. Skilled technicians hand-place and solder components onto the PCB using soldering irons or hot-air stations. Manual assembly offers flexibility and can accommodate last-minute design changes or component substitutions.
PCB Assembly Materials and Components
The choice of materials and components plays a significant role in the performance, reliability, and cost of the assembled PCB. Here are some key considerations:
-
PCB Substrate: The PCB substrate is the base material on which the copper traces and components are mounted. Common substrate materials include FR-4, Rogers, and polyimide. The choice of substrate depends on factors such as dielectric constant, thermal stability, and cost.
-
Copper Weight: The copper weight refers to the thickness of the copper traces on the PCB. Higher copper weights offer better current carrying capacity and improved signal integrity but may increase the cost and manufacturing complexity.
-
Surface Finish: The surface finish is applied to the exposed copper traces to prevent oxidation and improve solderability. Common surface finishes include Hot Air Solder Leveling (HASL), Immersion Silver, Immersion Tin, and Electroless Nickel Immersion Gold (ENIG).
-
Solder Mask: The solder mask is a protective layer applied over the copper traces, leaving only the component pads exposed. It prevents accidental short circuits and provides insulation between adjacent traces. Solder mask color options include green, red, blue, and black.
-
Silkscreen: The silkscreen is a printed layer on the PCB that provides component identifiers, logos, and assembly instructions. It helps in the assembly process and improves the readability of the board.
-
Component Selection: Choosing the right components is critical for the functionality and reliability of the assembled PCB. Factors to consider include component package type, tolerance, temperature rating, and availability. It is important to work closely with your assembly company to ensure component compatibility and sourcing.
Prototype PCB Assembly Challenges and Solutions
Prototype PCB assembly comes with its own set of challenges. Here are some common challenges and solutions:
-
Design for Manufacturing (DFM): Ensuring that the PCB design is optimized for manufacturing can be challenging. Designers should follow DFM guidelines, such as maintaining appropriate trace widths, clearances, and component spacing. Prototype PCB assembly companies often offer DFM review services to identify and address any potential manufacturability issues.
-
Component Availability: Sourcing components for prototype builds can be difficult, especially for small quantities or obsolete parts. Prototype PCB assembly companies may offer component sourcing services or recommend alternative components to mitigate availability issues.
-
Design Changes: Prototype projects often involve frequent design changes and iterations. Assembly companies should be flexible and accommodate these changes without significant delays or cost increases. Clear communication and version control are essential to manage design changes effectively.
-
Turnaround Time: Meeting tight deadlines is a common challenge in prototype PCB assembly. Choosing a company with fast turnaround capabilities and prioritizing critical tasks can help mitigate this challenge. Additionally, providing complete and accurate design files and specifications can streamline the assembly process.
-
Cost Management: Prototype PCB assembly can be expensive, especially for small quantities. To manage costs, consider optimizing the PCB design for manufacturability, reducing the number of unique components, and leveraging the assembly company’s expertise for cost-saving recommendations.
The Future of Prototype PCB Assembly
As technology continues to advance, prototype PCB assembly companies must adapt to new challenges and opportunities. Here are some trends shaping the future of prototype PCB assembly:
-
Miniaturization: The demand for smaller and more compact electronic devices is driving the need for miniaturized PCBs and components. Prototype PCB assembly companies must invest in advanced equipment and processes to handle tiny components and high-density designs.
-
High-Speed and High-Frequency: With the increasing prevalence of high-speed digital interfaces and wireless technologies, PCBs must be designed and assembled to handle high-frequency signals. This requires specialized materials, layout techniques, and assembly processes to ensure signal integrity and minimize interference.
-
Flexible and Stretchable PCBs: Flexible and stretchable PCBs are gaining traction in wearable electronics, medical devices, and IoT applications. Prototype PCB assembly companies must develop expertise in handling and assembling these unconventional substrates.
-
Additive Manufacturing: 3D printing technologies are emerging as a viable option for rapid prototyping of PCBs. Additive manufacturing allows for the creation of complex geometries, embedded components, and multi-layer PCBs. Prototype PCB assembly companies may integrate 3D printing capabilities to offer faster and more flexible prototyping solutions.
-
Automation and Industry 4.0: The adoption of automation, robotics, and data-driven manufacturing is transforming the PCB assembly industry. Prototype PCB assembly companies must embrace these technologies to improve efficiency, quality, and traceability. This includes implementing automated inspection systems, real-time process monitoring, and data analytics to optimize assembly processes.
FAQ
-
What is the typical turnaround time for prototype PCB assembly?
The turnaround time for prototype PCB assembly varies depending on the complexity of the design, component availability, and the assembly company’s capabilities. Some companies offer quick-turn services with lead times as short as 24-48 hours, while others may take several days or weeks. It is important to discuss your specific requirements and timeline with the assembly company to ensure they can meet your needs. -
How much does prototype PCB Assembly Cost?
The cost of prototype PCB assembly depends on several factors, including the PCB size, layer count, component count, and assembly complexity. Additionally, the quantity of prototypes required and the turnaround time can impact the cost. Prototype assembly is generally more expensive per unit compared to high-volume production due to the setup costs and manual labor involved. It is best to request quotes from multiple assembly companies and compare the cost and value they offer. -
What design files are required for prototype PCB assembly?
To facilitate smooth prototype PCB assembly, you should provide a complete set of design files, including: - Gerber files: These files contain the PCB layout information, such as copper layers, solder mask, and silkscreen.
- Drill files: These files specify the location and size of the holes to be drilled in the PCB.
- Bill of Materials (BOM): The BOM lists all the components required for the assembly, including part numbers, quantities, and reference designators.
- Assembly drawings: These drawings provide visual instructions for component placement and orientation on the PCB.
-
Schematic diagrams: The schematic diagrams show the electrical connections and component values.
-
Can prototype PCB assembly companies handle complex designs?
Yes, most prototype PCB assembly companies have the expertise and capabilities to handle complex designs. They work with a wide range of PCB technologies, including high-density interconnect (HDI), flexible PCBs, and rigid-flex combinations. However, it is important to discuss your specific design requirements with the assembly company to ensure they have the necessary equipment and experience to handle your project. -
What quality standards should I look for in a prototype PCB assembly company?
When selecting a prototype PCB assembly company, look for those that adhere to industry-recognized quality standards. Some key certifications and standards include: - ISO 9001: This standard ensures that the company has a robust quality management system in place.
- IPC-A-610: This standard defines the acceptability criteria for electronic assemblies, including soldering, component placement, and workmanship.
- J-STD-001: This standard specifies the requirements for soldered electrical and electronic assemblies.
- UL certification: This certification ensures that the assembled PCBs meet safety and performance standards.
A company that maintains these certifications demonstrates a commitment to quality and reliability.
Conclusion
Prototype PCB assembly is a critical step in the product development process, enabling designers and engineers to test and validate their designs before moving to full-scale production. Choosing the right prototype PCB assembly company is essential for the success of your project. Consider factors such as experience, quality standards, turnaround time, design support, and communication when evaluating potential partners.
As technology advances, prototype PCB assembly companies must adapt to new challenges and opportunities, such as miniaturization, high-speed designs, flexible substrates, and additive manufacturing. By staying at the forefront of these trends and investing in advanced equipment and processes, prototype PCB assembly companies can continue to support innovation and product development in the electronics industry.
0 Comments