What is PCBA?
PCBA stands for Printed Circuit Board Assembly. It is a process of attaching electronic components to a printed circuit board (PCB) to create a functional Electronic Assembly. The PCBA process involves several steps, including PCB fabrication, component placement, soldering, and testing.
PCB Fabrication
The first step in the PCBA process is PCB fabrication. A PCB is a flat board made of insulating material, such as fiberglass or plastic, with conductive copper traces printed on its surface. The copper traces form the electrical connections between the components that will be attached to the board.
PCBs are fabricated using a process called photolithography. The process involves the following steps:
- Design: The PCB design is created using computer-aided design (CAD) software.
- Film Generation: The CAD design is used to create a photographic film of the PCB layout.
- Exposure: The film is used to expose a photoresist layer on a copper-clad board.
- Development: The exposed photoresist is developed, leaving a pattern of the PCB layout on the copper.
- Etching: The unwanted copper is etched away, leaving only the desired copper traces.
- Drilling: Holes are drilled in the board for component leads and mounting.
- Plating: The holes are plated with copper to provide electrical continuity.
- Solder Mask: A solder mask is applied to the board to protect the copper traces and prevent short circuits.
- Silkscreen: A silkscreen layer is applied to the board to add component labels and other markings.
Component Placement
Once the PCB is fabricated, the next step is to place the electronic components on the board. This is done using a machine called a pick-and-place machine. The machine uses a vacuum nozzle to pick up the components from a tape or tray and place them on the board in the correct location.
The components are held in place by a solder paste that is applied to the board before the components are placed. The solder paste is a mixture of tiny solder balls and flux that helps the solder adhere to the board and the component leads.
Soldering
After the components are placed on the board, the next step is to solder them in place. This is done using a process called reflow soldering. The board is placed in a reflow oven, which heats the board and melts the solder paste. The solder then flows around the component leads and forms a permanent electrical and mechanical connection.
Reflow soldering is a highly controlled process that requires precise temperature and time control to ensure that the solder melts and flows properly without damaging the components or the board.
Testing
The final step in the PCBA process is testing. The assembled board is tested to ensure that it functions properly and meets the required specifications. Testing can be done using automated test equipment (ATE) or manually using test probes and other equipment.
Common tests include:
- Continuity Test: Checks that all the electrical connections are intact and there are no open circuits.
- Resistance Test: Measures the resistance of the circuit to ensure that it is within the specified range.
- Functionality Test: Verifies that the board performs its intended function.
- In-Circuit Test (ICT): Tests the board at the component level to ensure that each component is functioning properly.
Types of PCBAs
There are several types of PCBAs, each with its own unique characteristics and applications. The most common types are:
Single-Sided PCBA
A single-sided PCBA has components and copper traces on only one side of the board. This type of PCBA is the simplest and least expensive to manufacture, but it has limitations in terms of circuit density and complexity.
Single-sided PCBAs are commonly used in simple electronic devices such as calculators, toys, and low-cost consumer electronics.
Double-Sided PCBA
A double-sided PCBA has components and copper traces on both sides of the board. This allows for higher circuit density and more complex designs than single-sided PCBAs.
Double-sided PCBAs are used in a wide range of electronic devices, including smartphones, laptops, and industrial control systems.
Multi-Layer PCBA
A multi-layer PCBA has multiple layers of copper traces separated by insulating layers. This allows for even higher circuit density and complexity than double-sided PCBAs.
Multi-layer PCBAs are used in high-performance electronic devices such as servers, network switches, and aerospace systems.
Flexible PCBA
A flexible PCBA is made using a flexible substrate material instead of a rigid board. This allows the PCBA to bend and flex without breaking.
Flexible PCBAs are used in applications where space is limited or where the device needs to conform to a specific shape, such as in wearable electronics and medical devices.
High Density Interconnect (HDI) PCBA
An HDI PCBA is a type of multi-layer PCBA that uses microvias (tiny holes) to connect the layers. This allows for even higher circuit density and smaller component sizes than traditional multi-layer PCBAs.
HDI PCBAs are used in high-performance electronic devices such as smartphones, tablets, and medical devices.
PCBA Manufacturing Process
The PCBA manufacturing process involves several steps, each of which must be carefully controlled to ensure the quality and reliability of the final product. The steps are:
Design
The first step in the PCBA manufacturing process is to design the circuit board. This is done using computer-aided design (CAD) software, which allows engineers to create a digital model of the board and its components.
The design process involves several steps, including:
- Schematic Design: Creating a schematic diagram of the circuit, showing the connections between the components.
- Component Selection: Choosing the appropriate components for the design, based on factors such as cost, availability, and performance.
- Layout Design: Arranging the components on the board and routing the copper traces to connect them.
- Design Rule Check (DRC): Verifying that the design meets the manufacturing constraints and design rules.
Prototyping
Once the design is complete, the next step is to create a prototype of the board. This allows engineers to test the design and make any necessary changes before mass production begins.
Prototyping can be done using several methods, including:
- 3D Printing: Creating a physical model of the board using a 3D printer.
- CNC Milling: Cutting the board shape and drilling holes using a computer-controlled milling machine.
- Rapid Prototyping: Using a specialized machine to quickly create a prototype board from the CAD design.
Fabrication
After the prototype has been tested and any necessary changes have been made, the next step is to fabricate the PCB. This involves several steps, as described in the PCB Fabrication section above.
Assembly
Once the PCB has been fabricated, the next step is to assemble the components onto the board. This is done using a pick-and-place machine and reflow soldering, as described in the Component Placement and Soldering sections above.
Testing
The final step in the PCBA manufacturing process is testing. This involves several types of tests, as described in the Testing section above.
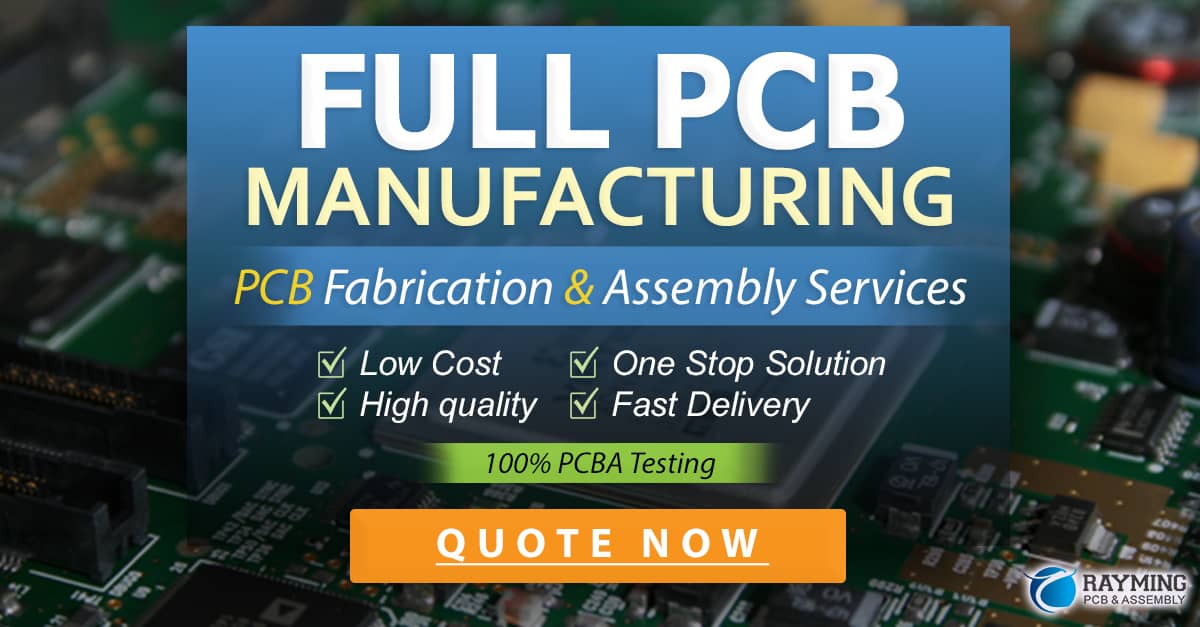
PCBA Quality Control
Quality control is critical in the PCBA manufacturing process to ensure that the final product meets the required specifications and performs reliably in the field. There are several quality control measures that are commonly used in PCBA manufacturing, including:
Incoming Inspection
Incoming inspection involves testing the components and materials that are used in the PCBA manufacturing process to ensure that they meet the required specifications. This can include visual inspection, electrical testing, and chemical analysis.
In-Process Inspection
In-process inspection involves testing the PCBA at various stages of the manufacturing process to ensure that it is being assembled correctly and meets the required specifications. This can include visual inspection, electrical testing, and x-ray inspection.
Final Inspection
Final inspection involves testing the completed PCBA to ensure that it meets the required specifications and functions properly. This can include functional testing, burn-in testing, and environmental testing.
Traceability
Traceability involves tracking the components and materials used in the PCBA manufacturing process from the point of origin to the final product. This allows manufacturers to quickly identify and resolve any quality issues that may arise.
PCBA Applications
PCBAs are used in a wide range of electronic devices and systems, including:
Consumer Electronics
PCBAs are used in a variety of consumer electronic devices, including:
- Smartphones
- Tablets
- Laptops
- Televisions
- Gaming Consoles
Industrial Electronics
PCBAs are used in industrial electronic systems, such as:
- Industrial Control Systems
- Robotics
- Automation Systems
- Test and Measurement Equipment
Medical Electronics
PCBAs are used in medical electronic devices, such as:
- Medical Imaging Systems
- Patient Monitoring Systems
- Diagnostic Equipment
- Implantable Devices
Automotive Electronics
PCBAs are used in automotive electronic systems, such as:
- Engine Control Units
- Infotainment Systems
- Advanced Driver Assistance Systems (ADAS)
- Electric Vehicle Charging Systems
Aerospace Electronics
PCBAs are used in aerospace electronic systems, such as:
- Avionics Systems
- Satellite Communication Systems
- Radar Systems
- Navigation Systems
PCBA Design Considerations
When designing a PCBA, there are several factors that must be considered to ensure that the final product meets the required specifications and performs reliably in the field. These factors include:
Component Selection
Choosing the appropriate components for the design is critical to ensure that the PCBA performs as intended. Factors to consider when selecting components include:
- Cost
- Availability
- Performance
- Size
- Power Requirements
Signal Integrity
Signal integrity refers to the quality of the electrical signals transmitted through the PCBA. Poor signal integrity can lead to errors, noise, and other problems that can affect the performance of the device.
Factors that can affect signal integrity include:
- Trace Length and Width
- Impedance Matching
- Crosstalk
- Electromagnetic Interference (EMI)
Thermal Management
Thermal management refers to the ability of the PCBA to dissipate heat generated by the components. Poor thermal management can lead to component failure and reduced reliability.
Factors that can affect thermal management include:
- Component Placement
- Airflow
- Heat Sinks
- Thermal Interface Materials
Manufacturing Constraints
The design of the PCBA must take into account the constraints of the manufacturing process, such as:
- Minimum Trace Width and Spacing
- Minimum Hole Size
- Maximum Board Size
- Number of Layers
Failure to consider these constraints can lead to manufacturing problems and increased costs.
PCBA Testing Methods
There are several methods used to test PCBAs to ensure that they meet the required specifications and perform reliably in the field. These methods include:
In-Circuit Testing (ICT)
ICT involves testing the PCBA at the component level using a Bed-of-Nails Test fixture. The test fixture makes electrical contact with each component on the board and tests it individually to ensure that it is functioning properly.
Flying Probe Testing
Flying probe testing involves using a set of movable test probes to make electrical contact with the PCBA and test the components and connections. This method is slower than ICT but more flexible, as it does not require a custom test fixture.
Boundary Scan Testing
Boundary scan testing involves using a set of test points built into the components on the PCBA to test the connections between them. This method is useful for testing complex PCBAs with many layers and small components.
Functional Testing
Functional testing involves testing the PCBA as a complete system to ensure that it performs its intended function. This can include testing the device under various environmental conditions, such as temperature and humidity, to ensure that it performs reliably in the field.
PCBA Troubleshooting
When a PCBA fails to perform as intended, it is important to be able to troubleshoot the problem quickly and efficiently. There are several steps that can be taken to troubleshoot a PCBA, including:
Visual Inspection
The first step in troubleshooting a PCBA is to visually inspect the board for any obvious defects, such as:
- Broken or Missing Components
- Solder Bridges or Opens
- Damaged Traces or Pads
Electrical Testing
If the visual inspection does not reveal any obvious defects, the next step is to perform electrical testing on the board. This can include:
- Continuity Testing
- Resistance Testing
- Voltage Testing
- Current Testing
Component Testing
If the electrical testing does not reveal any problems, the next step is to test the individual components on the board. This can be done using a variety of methods, including:
- In-Circuit Testing
- Boundary Scan Testing
- Functional Testing
Root Cause Analysis
Once the problem has been identified, the next step is to perform a root cause analysis to determine the underlying cause of the failure. This can involve analyzing the design of the PCBA, the manufacturing process, or the components used.
PCBA Design Software
There are several software tools available for designing PCBAs, including:
Altium Designer
Altium Designer is a comprehensive PCB design software package that includes schematic capture, PCB layout, and 3D visualization tools. It is widely used in the electronics industry for designing complex PCBAs.
Eagle
Eagle is a popular PCB design software package that is known for its ease of use and affordability. It includes schematic capture and PCB layout tools, as well as a large library of components.
KiCad
KiCad is an open-source PCB design software package that includes schematic capture, PCB layout, and 3D visualization tools. It is popular among hobbyists and small businesses due to its low cost and flexibility.
OrCAD
OrCAD is a comprehensive PCB design software package that includes schematic capture, PCB layout, and simulation tools. It is widely used in the electronics industry for designing complex PCBAs.
PCBA Manufacturing Services
There are many companies that offer PCBA manufacturing services, ranging from small prototyping shops to large-scale contract manufacturers. When choosing a PCBA manufacturing service, there are several factors to consider, including:
Quality
The quality of the PCBA is critical to the performance and reliability of the final product. Look for a manufacturer with a proven track record of producing high-quality PCBAs and a robust quality control process.
Cost
The cost of PCBA manufacturing can vary widely depending on factors such as the complexity of the design, the quantity ordered, and the turnaround time required. Look for a manufacturer that offers competitive pricing without sacrificing quality.
Capabilities
Different PCBA manufacturers have different capabilities in terms of the types of PCBAs they can produce, the manufacturing processes they use, and the testing and inspection methods they employ. Look for a manufacturer that has the capabilities required for your specific project.
Turnaround Time
The turnaround time for PCBA manufacturing can vary widely depending on the complexity of the design and the quantity ordered. Look for a manufacturer that can meet your project timeline without sacrificing quality.
Communication
Good communication is essential for a successful PCBA manufacturing project. Look for a manufacturer that is responsive to your questions and concerns and provides regular updates on the status of your project.
Frequently Asked Questions
What is the difference between a PCB and a PCBA?
A PCB (printed circuit board) is the bare board with copper traces and pads, but without any components attached. A PCBA (printed circuit board assembly) is a PCB with electronic components attached, making it a functional electronic assembly.
What are the different types of PCBAs?
The most common types of PCBAs are single-sided, double-sided, multi-layer, flexible, and high density interconnect (HDI). Each type has its own unique characteristics and applications.
What is the PCBA manufacturing process?
The PCBA manufacturing process involves several steps, including design, prototyping, fabrication, assembly, and testing. Each step must be carefully controlled to ensure the quality and reliability of the final product.
What are some common PCBA testing methods?
Common PCBA testing methods include in-circuit testing (ICT), flying probe testing, boundary scan testing, and functional testing. Each method has its own advantages and disadvantages depending on the specific application.
How do I choose a PCBA manufacturing service?
When choosing a PCBA manufacturing service, consider factors such as quality, cost, capabilities, turnaround time, and communication. Look for a manufacturer with a proven track record of producing high-quality PCBAs and a commitment to customer service.
Conclusion
PCBAs are a critical component of many electronic devices and systems, from consumer electronics to aerospace applications. The design and manufacturing of PCBAs involves a complex process that requires expertise in electrical engineering, materials science, and manufacturing technology.
When designing a PCBA, it is important to consider factors such as component selection, signal integrity, thermal management, and manufacturing constraints. Testing and quality control are also critical to ensure that the final product meets the required specifications and performs reliably in the field.
There are many software tools and manufacturing services available to assist with PCBA design and production. By understanding the basics of PCBA technology and selecting the right tools and partners, engineers and manufacturers can create high-quality, reliable electronic products that meet the needs of their customers.
0 Comments