What is an HDI PCB?
An HDI PCB is a printed circuit board that incorporates high-density interconnect technology. This technology allows for the creation of smaller vias (holes that connect different layers of the PCB), finer trace widths, and reduced spacing between components. As a result, HDI PCBs can accommodate a higher number of components in a smaller area, making them ideal for compact and complex electronic devices.
The main characteristics of an HDI PCB include:
– Smaller via sizes (typically less than 0.15mm)
– Finer trace widths (typically less than 0.15mm)
– Higher component density
– Increased number of layers (up to 20 or more)
– Reduced overall board size and weight
Advantages of HDI PCBs
HDI PCBs offer several advantages over traditional PCBs, making them an attractive choice for many applications. Some of the key benefits include:
1. Miniaturization
The smaller via sizes and finer trace widths of HDI PCBs allow for the creation of more compact designs. This is particularly important for portable electronic devices, such as smartphones, tablets, and wearables, where space is at a premium.
2. Improved Signal Integrity
HDI PCBs offer better signal integrity due to the reduced distance between components and the use of finer traces. This results in lower signal loss, reduced crosstalk, and improved overall performance, which is crucial for high-speed applications.
3. Increased Functionality
With the ability to accommodate more components in a smaller area, HDI PCBs enable the creation of more complex and feature-rich designs. This allows for the integration of multiple functions into a single device, such as combining a smartphone, camera, and GPS in one compact package.
4. Cost Reduction
Although the initial manufacturing costs of HDI PCBs may be higher than traditional PCBs, they can lead to overall cost savings in the long run. The smaller size and lighter weight of HDI PCBs can reduce material costs, shipping expenses, and the need for additional components or connectors.
HDI PCB Manufacturing Process
The manufacturing process for HDI PCBs is more complex than that of traditional PCBs due to the smaller features and higher precision required. The main steps involved in HDI PCB manufacturing include:
-
Design and Layout: The HDI PCB design is created using specialized software, taking into account the smaller via sizes, finer trace widths, and component placement.
-
Material Selection: High-quality materials, such as advanced laminates and copper foils, are chosen to ensure the reliability and performance of the HDI PCB.
-
Drilling and Plating: Micro-vias are drilled using laser or mechanical drilling techniques, followed by copper plating to create conductive paths between layers.
-
Patterning and Etching: The desired circuit pattern is transferred onto the PCB using photolithography, and unwanted copper is etched away.
-
Lamination: The individual layers of the HDI PCB are laminated together under high pressure and temperature to form a single, compact board.
-
Surface Finishing: A protective surface finish, such as ENIG (Electroless Nickel Immersion Gold) or HASL (Hot Air Solder Leveling), is applied to the HDI PCB to prevent oxidation and improve solderability.
-
Electrical Testing: The completed HDI PCB undergoes rigorous electrical testing to ensure proper functionality and adherence to specifications.
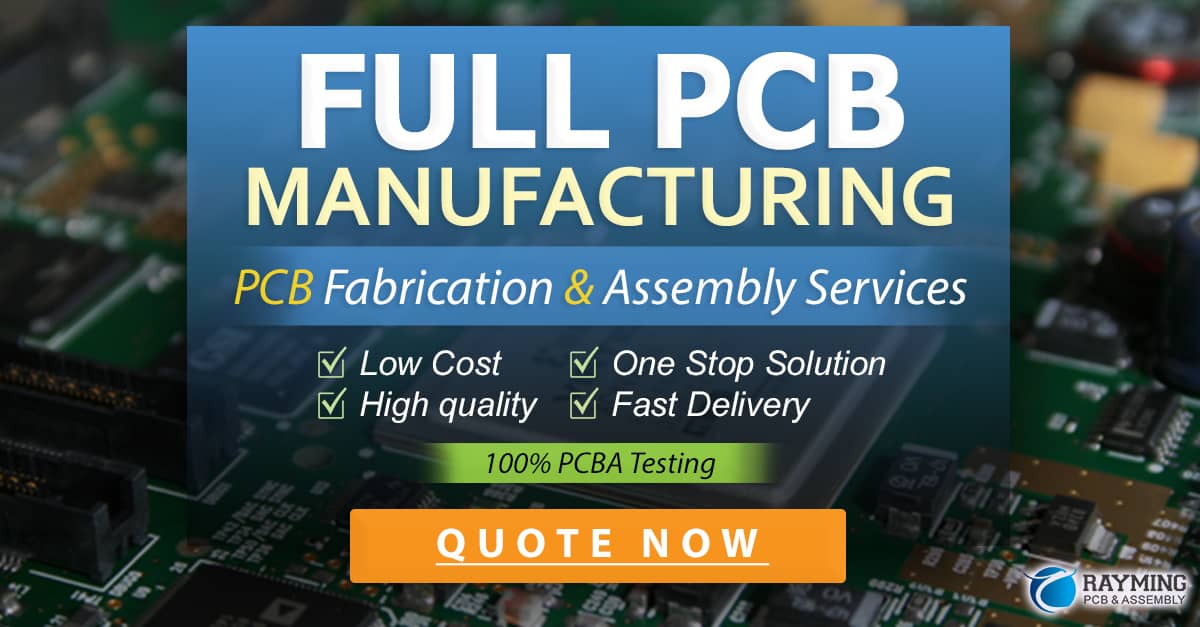
Applications of HDI PCBs
HDI PCBs find applications in a wide range of industries and products, particularly those that require high performance, compact size, and advanced functionality. Some common applications include:
1. Consumer Electronics
- Smartphones
- Tablets
- Smartwatches
- Digital cameras
- Gaming consoles
2. Automotive Electronics
- Advanced driver assistance systems (ADAS)
- In-vehicle infotainment systems
- Engine control units (ECUs)
- Autonomous driving systems
3. Medical Devices
- Implantable devices
- Wearable health monitors
- Diagnostic equipment
- Surgical instruments
4. Aerospace and Defense
- Avionics systems
- Satellite communications
- Military communications equipment
- Radar and surveillance systems
5. Industrial Automation
- Robotics
- Machine vision systems
- Process control equipment
- Sensors and actuators
HDI PCB Design Considerations
When designing an HDI PCB, several factors must be taken into account to ensure optimal performance and manufacturability. Some key considerations include:
1. Via Types and Sizes
HDI PCBs typically employ micro-vias, which can be categorized into three main types:
Via Type | Description | Typical Size Range |
---|---|---|
Through Hole | Extends through all layers of the PCB | 0.15mm – 0.20mm |
Blind | Connects an outer layer to an inner layer | 0.10mm – 0.15mm |
Buried | Connects inner layers without extending to the outer layers | 0.10mm – 0.15mm |
Choosing the appropriate via type and size is crucial for maintaining signal integrity and ensuring reliable connections between layers.
2. Trace Width and Spacing
HDI PCBs feature finer trace widths and reduced spacing between traces compared to traditional PCBs. The following table provides a general guideline for trace width and spacing based on the copper weight:
Copper Weight (oz) | Minimum Trace Width | Minimum Spacing |
---|---|---|
0.5 | 0.075mm | 0.075mm |
1.0 | 0.100mm | 0.100mm |
2.0 | 0.150mm | 0.150mm |
It is essential to adhere to these guidelines to prevent signal integrity issues and ensure proper manufacturability.
3. Layer Stackup
The layer stackup of an HDI PCB plays a crucial role in its performance and manufacturability. A well-designed stackup should consider factors such as:
- Signal integrity
- Impedance control
- Power distribution
- Thermal management
- Manufacturing constraints
Working closely with the PCB manufacturer to optimize the layer stackup can help minimize potential issues and ensure the best possible performance.
FAQ
1. What is the difference between an HDI PCB and a traditional PCB?
HDI PCBs feature smaller via sizes, finer trace widths, and higher component density compared to traditional PCBs. This allows for more compact and complex designs, improved signal integrity, and increased functionality.
2. What are the main advantages of using HDI PCBs?
The main advantages of using HDI PCBs include miniaturization, improved signal integrity, increased functionality, and potential cost reduction through reduced material usage and shipping expenses.
3. What industries commonly use HDI PCBs?
HDI PCBs are commonly used in industries that require high-performance, compact, and feature-rich electronic devices, such as consumer electronics, automotive electronics, medical devices, aerospace and defense, and industrial automation.
4. What are the different types of vias used in HDI PCBs?
The three main types of vias used in HDI PCBs are through hole vias (extending through all layers), blind vias (connecting an outer layer to an inner layer), and buried vias (connecting inner layers without extending to the outer layers).
5. What factors should be considered when designing an HDI PCB?
When designing an HDI PCB, key factors to consider include via types and sizes, trace width and spacing, layer stackup, signal integrity, impedance control, power distribution, thermal management, and manufacturing constraints.
In conclusion, HDI PCBs represent a significant advancement in printed circuit board technology, offering numerous benefits for a wide range of applications. By understanding the features, advantages, manufacturing processes, and design considerations associated with HDI PCBs, engineers and product designers can create more compact, high-performance, and feature-rich electronic devices that meet the demands of today’s increasingly connected world.
0 Comments