What is the Definition of a PCB?
The PCB Definition can be stated as follows:
A Printed Circuit Board is a flat, insulating board with conductive pathways printed or etched onto its surface to connect electronic components and form a functional electronic circuit.
The History of PCBs
The development of PCBs can be traced back to the early 20th century. In 1903, Albert Hanson, a German inventor, filed a patent for a method of creating conductive pathways on an insulating board. However, it wasn’t until the 1940s that PCBs began to gain widespread use in electronic devices.
During World War II, the demand for compact, reliable electronic equipment for military applications led to significant advancements in PCB technology. In 1943, Paul Eisler, an Austrian engineer, developed a method for etching conductive pathways onto a non-conductive substrate, which became the foundation for modern PCB manufacturing.
Timeline of PCB Development
Year | Event |
---|---|
1903 | Albert Hanson files a patent for creating conductive pathways on an insulating board |
1943 | Paul Eisler develops the etching method for creating conductive pathways on a non-conductive substrate |
1950s | PCBs become widely adopted in consumer electronics |
1960s | Multi-layer PCBs are introduced, enabling more complex circuit designs |
1980s | Surface-mount technology (SMT) gains popularity, allowing for smaller and more densely populated PCBs |
2000s | High-density interconnect (HDI) PCBs emerge, facilitating the development of compact, high-performance electronic devices |
Types of PCBs
There are several types of PCBs, each designed to meet specific requirements and applications. The most common types include:
1. Single-Layer PCBs
Single-layer PCBs have conductive traces on only one side of the insulating board. They are the simplest and most cost-effective type of PCB, suitable for basic electronic circuits and low-density designs.
2. Double-Layer PCBs
Double-layer PCBs have conductive traces on both sides of the insulating board, connected through holes drilled in the board called vias. These PCBs offer higher component density and more complex circuit designs compared to single-layer boards.
3. Multi-Layer PCBs
Multi-layer PCBs consist of three or more layers of conductive traces separated by insulating layers. These boards enable even higher component density and more intricate circuit designs, making them ideal for advanced electronic applications, such as smartphones, computers, and aerospace systems.
4. Flexible PCBs
Flexible PCBs are made from flexible insulating materials, such as polyimide, allowing the board to bend and conform to various shapes. These PCBs are commonly used in wearable electronics, medical devices, and applications where space is limited, or the device needs to adapt to a specific form factor.
5. Rigid-Flex PCBs
Rigid-flex PCBs combine the benefits of both rigid and flexible PCBs. They consist of rigid sections connected by flexible sections, enabling the board to be folded or bent to fit into a specific space or to connect multiple rigid boards together.
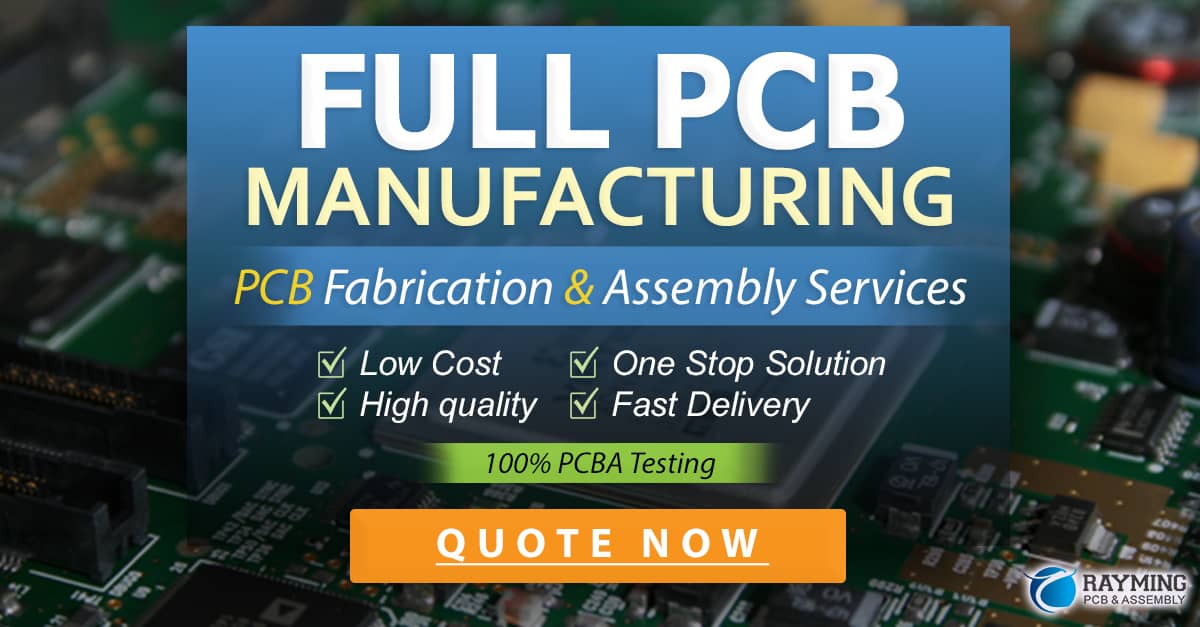
PCB Manufacturing Process
The PCB manufacturing process involves several steps to create a functional printed circuit board. The main stages include:
-
Design: The PCB design is created using specialized software, such as Eagle or Altium Designer. The design includes the schematic diagram, component layout, and routing of the conductive traces.
-
Printing: The PCB design is printed onto a transparent film or photomask, which will be used to transfer the design onto the copper-clad insulating board.
-
Etching: The copper-clad board is coated with a light-sensitive resist and exposed to UV light through the photomask. The exposed areas of the resist are then removed, leaving the desired conductive pattern. The board is then immersed in an etching solution, which removes the unwanted copper, leaving only the conductive traces.
-
Drilling: Holes are drilled into the board to accommodate through-hole components and to create vias for multi-layer boards.
-
Plating: The holes are plated with a conductive material, usually copper, to ensure electrical connectivity between layers in multi-layer boards.
-
Solder Mask Application: A protective solder mask is applied to the board, covering the conductive traces while leaving the pads exposed for component soldering.
-
Silkscreen: A silkscreen layer is added to the board, providing text, logos, and component outlines for easier assembly and identification.
-
Surface Finish: A surface finish, such as HASL (Hot Air Solder Leveling), ENIG (Electroless Nickel Immersion Gold), or OSP (Organic Solderability Preservative), is applied to the exposed pads to prevent oxidation and enhance solderability.
-
Assembly: The electronic components are soldered onto the PCB using either through-hole or surface-mount technology (SMT).
-
Testing: The assembled PCB undergoes various tests, such as visual inspection, automated optical inspection (AOI), and electrical testing, to ensure proper functionality and quality.
Advantages of Using PCBs
PCBs offer numerous advantages over other methods of creating electronic circuits, such as point-to-point wiring or wire-wrapping. Some of the main benefits include:
-
Compact Size: PCBs allow for the miniaturization of electronic devices by enabling high component density and efficient use of space.
-
Reliability: The fixed layout and robust construction of PCBs reduce the risk of short circuits, loose connections, and other issues that can affect the reliability of electronic circuits.
-
Consistency: PCBs ensure consistent performance across multiple units of the same design, as the manufacturing process is highly standardized and automated.
-
Cost-Effective: Mass production of PCBs is cost-effective, as the manufacturing process can be automated, and the use of standardized components reduces overall costs.
-
Improved Signal Integrity: The precise layout and controlled impedance of PCB traces help maintain signal integrity, minimizing issues such as crosstalk, noise, and signal reflections.
-
Heat Dissipation: PCBs can be designed with thermal management features, such as heat sinks and thermal vias, to effectively dissipate heat generated by electronic components.
-
Ease of Maintenance: PCBs facilitate easier troubleshooting and repair, as components can be easily identified and replaced if necessary.
Applications of PCBs
PCBs are used in a wide range of electronic devices and systems, from consumer electronics to industrial equipment and aerospace applications. Some common applications include:
-
Consumer Electronics: Smartphones, tablets, laptops, televisions, and home appliances.
-
Automotive Industry: Engine control units, infotainment systems, and advanced driver assistance systems (ADAS).
-
Medical Devices: Diagnostic equipment, patient monitoring systems, and implantable devices.
-
Industrial Automation: Programmable logic controllers (PLCs), sensors, and control systems.
-
Aerospace and Defense: Avionics, satellite systems, and military communication equipment.
-
IoT Devices: Smart home devices, wearable technology, and sensor networks.
-
Power Electronics: Switchmode power supplies, inverters, and motor drives.
Future Trends in PCB Technology
As electronic devices continue to advance and become more complex, PCB technology must evolve to keep pace. Some of the future trends in PCB technology include:
-
Miniaturization: The demand for smaller, more compact electronic devices will drive the development of even higher-density PCBs and the increased use of advanced packaging techniques, such as system-in-package (SiP) and 3D packaging.
-
High-Speed Design: With the growing need for faster data transmission and processing, PCBs will need to be designed to support higher signal speeds and minimize signal integrity issues.
-
Flexible and Stretchable PCBs: The increasing popularity of wearable electronics and flexible devices will lead to the development of more advanced flexible and stretchable PCB materials and manufacturing techniques.
-
Embedded Components: To further reduce the size and improve the performance of electronic devices, more components will be embedded directly into the PCB substrate, creating a more integrated and compact solution.
-
Sustainable Materials: As environmental concerns grow, there will be a push for the development and use of more sustainable and eco-friendly PCB materials and manufacturing processes.
-
Additive Manufacturing: 3D printing technology may be increasingly used in PCB fabrication, enabling the creation of complex, three-dimensional circuit structures and reducing waste in the manufacturing process.
Frequently Asked Questions (FAQ)
-
What is the difference between a PCB and a PCBA?
A PCB is the bare board without any components attached, while a PCBA (Printed Circuit Board Assembly) is a PCB with all the electronic components soldered onto it, forming a complete functional unit. -
Can PCBs be recycled?
Yes, PCBs can be recycled. The recycling process involves separating the various materials, such as copper, gold, and plastic, which can then be reused in the production of new PCBs or other products. However, the recycling process can be complex and costly due to the presence of hazardous materials in some PCBs. -
What is the typical lifespan of a PCB?
The lifespan of a PCB depends on various factors, such as the quality of the materials used, the manufacturing process, and the operating environment. Generally, a well-designed and manufactured PCB can last for several decades under normal operating conditions. However, factors such as exposure to extreme temperatures, humidity, or vibrations can reduce the lifespan of a PCB. -
How can I choose the right PCB manufacturer for my project?
When choosing a PCB manufacturer, consider factors such as their experience, manufacturing capabilities, quality control processes, and customer support. Look for manufacturers with a proven track record of delivering high-quality PCBs on time and within budget. It’s also essential to ensure that the manufacturer can meet your specific requirements, such as PCB complexity, material selection, and certifications. -
What is the minimum feature size achievable on a PCB?
The minimum feature size on a PCB depends on the manufacturing capabilities of the PCB fabricator. Most standard PCB manufacturers can achieve a minimum trace width and spacing of around 0.1 mm (4 mil). However, advanced PCB fabrication techniques, such as high-density interconnect (HDI) and micro-via technology, can enable even smaller feature sizes, down to 0.05 mm (2 mil) or less.
In conclusion, PCBs have revolutionized the electronics industry, enabling the development of compact, reliable, and cost-effective electronic devices. As technology continues to advance, PCBs will play an increasingly crucial role in shaping the future of electronics, from consumer gadgets to industrial automation and beyond. By understanding the fundamentals of PCBs, including their design, manufacturing, and applications, engineers and enthusiasts can create innovative solutions that push the boundaries of what is possible in the world of electronics.
0 Comments