Introduction to PCB Development
Printed Circuit Boards (PCBs) have revolutionized the electronics industry since their inception in the early 20th century. PCBs are the backbone of modern electronic devices, providing a platform for the interconnection and integration of electronic components. The development of PCBs has been a continuous process, driven by advancements in technology, materials, and manufacturing processes. In this article, we will explore the history, key milestones, and current trends in PCB development.
History of PCB Development
The concept of PCBs dates back to the early 1900s when inventors began experimenting with methods to connect electronic components using conductive traces. However, it wasn’t until the 1940s that the first practical PCBs were developed. During World War II, the demand for compact and reliable electronic equipment for military applications drove the development of PCBs.
In 1936, Austrian engineer Paul Eisler invented the first printed circuit board as part of a radio set. Eisler’s PCB consisted of a thin sheet of insulating material with conductive copper traces printed on its surface. This early PCB design laid the foundation for future developments in the field.
Evolution of PCB Manufacturing Techniques
Over the years, PCB manufacturing techniques have evolved significantly to meet the increasing complexity and miniaturization demands of electronic devices. Let’s take a look at some of the key milestones in PCB manufacturing:
1. Through-Hole Technology (THT)
In the early days of PCB manufacturing, through-hole technology (THT) was the dominant method. THT involves drilling holes into the PCB substrate and inserting electronic components with long leads through the holes. The leads are then soldered to the copper traces on the other side of the board. THT PCBs are sturdy and reliable but have limitations in terms of component density and miniaturization.
2. Surface Mount Technology (SMT)
Surface mount technology (SMT) emerged in the 1960s and revolutionized PCB manufacturing. SMT allows electronic components to be mounted directly onto the surface of the PCB without the need for through-holes. SMT components are smaller and have shorter leads, enabling higher component density and miniaturization. SMT also enables automation in the assembly process, reducing manufacturing costs and improving productivity.
3. Multi-Layer PCBs
As electronic devices became more complex, the need for higher component density and improved signal integrity led to the development of multi-layer PCBs. Multi-layer PCBs consist of multiple layers of conductive copper traces separated by insulating layers. The layers are interconnected using through-holes or vias. Multi-layer PCBs allow for more complex routing and improved signal integrity compared to single-layer boards.
4. High-Density Interconnect (HDI) PCBs
High-density interconnect (HDI) PCBs are an advanced form of multi-layer PCBs that offer even higher component density and improved signal integrity. HDI PCBs use micro-vias, which are small holes drilled using laser technology, to interconnect the layers. HDI PCBs enable the miniaturization of electronic devices and are commonly used in smartphones, tablets, and wearable devices.
Advancements in PCB Materials
The choice of materials used in PCB manufacturing plays a crucial role in the performance and reliability of the final product. Over the years, there have been significant advancements in PCB materials to meet the evolving requirements of electronic devices.
1. FR-4
FR-4 is the most commonly used PCB substrate material. It is a composite material made of woven fiberglass cloth with an epoxy resin binder. FR-4 offers good mechanical strength, electrical insulation, and thermal stability. It is suitable for a wide range of applications and is cost-effective.
2. High-Frequency Laminates
With the increasing demand for high-speed and high-frequency applications, such as 5G communication and automotive radar systems, the need for specialized PCB materials has grown. High-frequency laminates, such as Rogers and Isola materials, offer superior dielectric properties and low loss at high frequencies. These materials enable the design of high-performance PCBs for demanding applications.
3. Flexible PCBs
Flexible PCBs, also known as flex circuits, are made using flexible substrate materials such as polyimide or polyester. Flexible PCBs can bend and conform to various shapes, making them ideal for applications where space is limited or where the PCB needs to fit into a specific form factor. Flexible PCBs are commonly used in wearable devices, medical equipment, and aerospace applications.
4. Metal Core PCBs
Metal core PCBs (MCPCBs) are designed for applications that require efficient heat dissipation. MCPCBs have a metal base, typically aluminum, which acts as a heat sink. The metal core is covered with a thin layer of dielectric material, followed by the copper traces. MCPCBs are commonly used in high-power LED lighting, automotive electronics, and power electronics.
Current Trends in PCB Development
PCB development continues to evolve to meet the demands of emerging technologies and applications. Some of the current trends in PCB development include:
1. Internet of Things (IoT)
The proliferation of IoT devices has driven the demand for small, low-power, and wireless-enabled PCBs. IoT PCBs often integrate sensors, microcontrollers, and wireless communication modules to enable seamless connectivity and data exchange. The development of IoT PCBs focuses on miniaturization, energy efficiency, and cost optimization.
2. Automotive Electronics
The automotive industry is undergoing a significant transformation with the increasing adoption of electric vehicles and advanced driver assistance systems (ADAS). PCBs play a critical role in automotive electronics, enabling functions such as infotainment, navigation, and safety features. Automotive PCBs must meet stringent reliability and environmental requirements, including temperature extremes, vibration, and electromagnetic compatibility (EMC).
3. 5G Communication
The deployment of 5G networks has created new challenges and opportunities for PCB development. 5G PCBs require high-frequency materials, advanced packaging techniques, and precise impedance control to enable high-speed data transmission. The development of 5G PCBs focuses on minimizing signal loss, reducing crosstalk, and ensuring signal integrity.
4. Artificial Intelligence (AI) and Machine Learning (ML)
AI and ML are transforming various industries, from healthcare to finance. PCBs designed for AI and ML applications often incorporate high-performance computing platforms, such as graphics processing units (GPUs) and field-programmable gate arrays (FPGAs). These PCBs require high-speed interfaces, efficient power delivery, and effective thermal management to support the demanding computational requirements of AI and ML algorithms.
Frequently Asked Questions (FAQ)
1. What is a PCB, and how does it work?
A: A PCB, or printed circuit board, is a flat board made of insulating material with conductive copper traces printed on its surface. PCBs provide a platform for the interconnection and integration of electronic components. The copper traces act as pathways for electrical signals to flow between the components, enabling the functioning of the electronic device.
2. What are the different types of PCBs?
A: There are several types of PCBs, including:
– Single-layer PCBs: These have conductive traces on only one side of the board.
– Double-layer PCBs: These have conductive traces on both sides of the board.
– Multi-layer PCBs: These have multiple layers of conductive traces separated by insulating layers.
– Flexible PCBs: These are made using flexible substrate materials and can bend and conform to various shapes.
– Rigid-flex PCBs: These combine rigid and flexible sections to provide both stability and flexibility.
3. What are the advantages of using SMT over THT in PCB manufacturing?
A: Surface mount technology (SMT) offers several advantages over through-hole technology (THT) in PCB manufacturing:
– Higher component density: SMT components are smaller and have shorter leads, allowing for more components to be placed on the PCB.
– Miniaturization: SMT enables the design of smaller and more compact electronic devices.
– Automated assembly: SMT is well-suited for automated assembly processes, reducing manufacturing costs and improving productivity.
– Improved signal integrity: SMT reduces the length of component leads, minimizing signal distortion and improving signal integrity.
4. What factors should be considered when choosing PCB materials?
A: When selecting PCB materials, several factors should be considered:
– Dielectric properties: The dielectric constant and loss tangent of the material affect signal propagation and signal integrity.
– Thermal properties: The thermal conductivity and coefficient of thermal expansion (CTE) of the material influence heat dissipation and thermal stability.
– Mechanical properties: The strength, flexibility, and dimensional stability of the material are important for the physical integrity of the PCB.
– Cost: The cost of the material should be balanced with the performance requirements and production volume.
5. What are the challenges in designing PCBs for high-frequency applications?
A: Designing PCBs for high-frequency applications poses several challenges:
– Signal integrity: High-frequency signals are more susceptible to signal distortion, crosstalk, and electromagnetic interference (EMI).
– Material selection: High-frequency PCBs require specialized materials with low dielectric loss and controlled impedance.
– Impedance matching: Precise impedance control is necessary to minimize signal reflections and ensure proper signal transmission.
– Layout and routing: The PCB layout and routing must be carefully designed to minimize signal path lengths, avoid discontinuities, and maintain proper grounding and shielding.
Conclusion
The development of electronic PCBs has been a transformative journey, enabling the creation of increasingly complex and miniaturized electronic devices. From the early days of through-hole technology to the advent of surface mount technology and multi-layer PCBs, each advancement has pushed the boundaries of what is possible in electronic design and manufacturing.
As we look towards the future, PCB development will continue to evolve to meet the demands of emerging technologies and applications. The Internet of Things, automotive electronics, 5G communication, and artificial intelligence are just a few examples of areas where PCB development will play a critical role.
To stay at the forefront of PCB development, designers and manufacturers must embrace new materials, manufacturing techniques, and design methodologies. Collaboration between industry, academia, and government will be essential to drive innovation and address the challenges posed by the ever-increasing complexity of electronic devices.
As we continue to push the limits of PCB technology, it is important to consider the environmental impact of PCB manufacturing and disposal. Sustainable practices, such as the use of eco-friendly materials and recycling programs, will be crucial in ensuring the long-term viability of the PCB industry.
In conclusion, the development of electronic PCBs has been a remarkable journey of innovation and progress. As we look towards the future, the possibilities for PCB technology are endless, limited only by our imagination and the boundaries of science. By embracing new technologies, collaborating across disciplines, and prioritizing sustainability, we can continue to shape the future of electronic design and manufacturing, one PCB at a time.
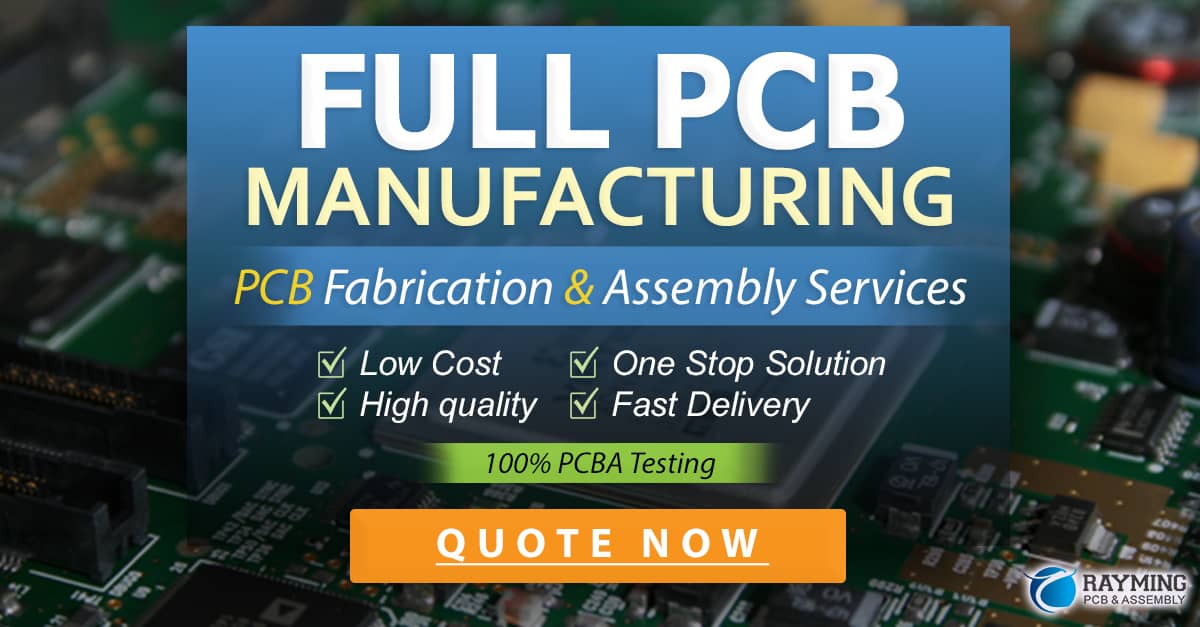
0 Comments