Introduction to PCB Heaters
A PCB (Printed Circuit Board) heater is a compact, efficient, and reliable heating solution that is widely used in various applications, from consumer electronics to industrial equipment. These heaters are designed to provide localized heating to specific components or areas on a PCB, ensuring optimal performance and preventing condensation or frost formation.
How PCB Heaters Work
PCB heaters work by converting electrical energy into heat through a resistive heating element embedded in the PCB. The heating element is typically made of a thin layer of conductive material, such as copper or nickel, which is etched onto the PCB substrate. When an electric current passes through the heating element, it encounters resistance, causing the element to heat up and dissipate thermal energy to the surrounding area.
Advantages of PCB Heaters
PCB heaters offer several advantages over traditional heating methods:
- Compact size: PCB heaters are thin and can be easily integrated into the design of a PCB, saving space and allowing for more compact devices.
- Efficient heating: The resistive heating element provides direct and targeted heating, minimizing energy loss and ensuring efficient heat transfer to the desired area.
- Precise temperature control: PCB heaters can be designed with integrated temperature sensors, allowing for precise temperature monitoring and control.
- Reliability: With no moving parts and a simple design, PCB heaters are highly reliable and have a long lifespan.
- Cost-effective: PCB heaters are relatively inexpensive to manufacture and can be easily customized to suit specific applications.
Types of PCB Heaters
There are several types of PCB heaters, each with its own unique characteristics and applications.
Polyimide PCB Heaters
Polyimide PCB heaters are made using a thin, flexible polyimide substrate with a copper or nickel heating element. These heaters are lightweight, resistant to chemicals and high temperatures, and can be easily shaped to fit various applications. Polyimide PCB heaters are commonly used in battery warming, medical devices, and aerospace applications.
Aluminum PCB Heaters
Aluminum PCB heaters feature an aluminum substrate with a copper or nickel heating element. The aluminum substrate provides excellent thermal conductivity, allowing for efficient heat dissipation and distribution. These heaters are more rigid than polyimide heaters and are often used in applications requiring a more sturdy heating solution, such as automotive electronics and industrial control panels.
Ceramic PCB Heaters
Ceramic PCB heaters use a ceramic substrate, such as aluminum nitride or alumina, with a printed resistive heating element. Ceramic substrates offer high thermal conductivity, electrical insulation, and resistance to high temperatures. These heaters are ideal for applications requiring high-temperature operation, such as semiconductor processing and scientific instrumentation.
Flexible PCB Heaters
Flexible PCB heaters are designed using a thin, flexible substrate, such as polyimide or polyester, with a printed heating element. These heaters can be easily bent or shaped to conform to various surfaces and are often used in applications requiring a flexible heating solution, such as wearable electronics, medical devices, and aerospace components.
Applications of PCB Heaters
PCB heaters find applications in a wide range of industries and products. Some common applications include:
- Consumer electronics: PCB heaters are used in devices like smartphones, tablets, and laptops to prevent condensation and maintain optimal operating temperatures.
- Medical devices: In medical equipment, PCB heaters are used to maintain the temperature of sensitive components, such as sensors or fluid reservoirs, and to prevent condensation in devices like respirators and dialysis machines.
- Automotive electronics: PCB heaters are employed in various automotive applications, such as battery warming, sensor heating, and condensation prevention in headlights and cameras.
- Industrial equipment: In industrial settings, PCB heaters are used to maintain the temperature of critical components, prevent condensation, and ensure reliable operation in harsh environments.
- Aerospace and defense: PCB heaters are utilized in aerospace and defense applications to maintain the temperature of sensitive electronics, prevent icing on sensors, and ensure reliable operation in extreme conditions.
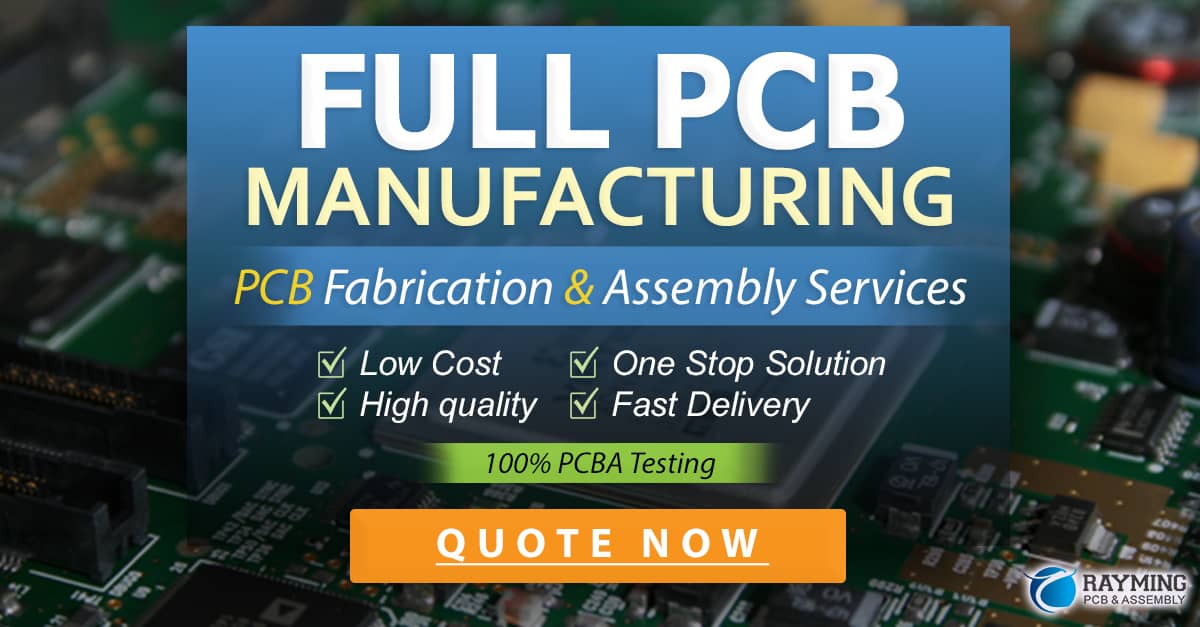
Designing PCB Heaters
When designing a PCB heater, several factors must be considered to ensure optimal performance and reliability.
Heating Element Material and Geometry
The choice of heating element material and geometry plays a crucial role in the performance of a PCB heater. Common materials include copper and nickel, with copper being the most widely used due to its high electrical and thermal conductivity. The geometry of the heating element, such as its shape, thickness, and spacing, determines the heat distribution and power density of the heater.
Substrate Material and Thickness
The substrate material and thickness influence the thermal performance and mechanical properties of the PCB heater. Common substrate materials include FR-4, polyimide, aluminum, and ceramics. The substrate thickness affects the heater’s thermal mass, flexibility, and mechanical strength. Thinner substrates provide faster heating and cooling times but may be more fragile, while thicker substrates offer better mechanical stability but slower thermal response.
Power Density and Temperature Range
The power density of a PCB heater determines the amount of heat generated per unit area and is expressed in watts per square inch (W/in²) or watts per square centimeter (W/cm²). Higher power densities allow for faster heating and higher maximum temperatures but may also lead to increased thermal stress and reduced heater lifespan. The temperature range of the heater should be carefully selected based on the application requirements and the limitations of the substrate and heating element materials.
Temperature Sensing and Control
Incorporating temperature sensing and control mechanisms is essential for maintaining the desired temperature and preventing overheating. Common temperature sensors include thermistors, RTDs (Resistance Temperature Detectors), and thermocouples. These sensors can be integrated into the PCB design or placed in close proximity to the heater. Temperature control can be achieved using simple on/off control, proportional control, or more advanced PID (Proportional-Integral-Derivative) control algorithms.
Thermal Insulation and Heat Spreading
Proper thermal insulation and heat spreading are crucial for efficient and safe operation of PCB heaters. Thermal insulation materials, such as silicone foam or aerogel, can be used to minimize heat loss and improve energy efficiency. Heat spreading techniques, such as using thermal vias or incorporating a Metal Core PCB, help distribute the heat evenly across the surface and prevent localized hot spots.
Manufacturing PCB Heaters
The manufacturing process for PCB heaters involves several key steps:
- PCB design and layout: The heater design is created using PCB design software, incorporating the heating element, temperature sensors, and control circuitry.
- Substrate preparation: The chosen substrate material is cut to size and cleaned to ensure proper adhesion of the copper layer.
- Copper deposition: A thin layer of copper is deposited onto the substrate using techniques like electroplating or lamination.
- Etching: The copper layer is selectively etched to create the desired heating element pattern and conductive traces.
- Lamination: For multi-layer PCB heaters, the etched layers are laminated together using heat and pressure.
- Drilling and cutting: Holes are drilled for through-hole components, and the PCB is cut to its final shape.
- Component assembly: Temperature sensors, control circuitry, and other components are soldered onto the PCB.
- Testing and quality control: The assembled PCB heater is tested for proper functionality, temperature accuracy, and safety.
Safety Considerations for PCB Heaters
When using PCB heaters, it is essential to consider safety to prevent accidents and ensure reliable operation.
Overheating Protection
Incorporating overheating protection mechanisms is crucial to prevent damage to the heater and surrounding components. This can be achieved through proper temperature sensing and control, as well as using fuses or thermal cutoffs that disconnect power to the heater if the temperature exceeds a safe limit.
Electrical Isolation
Ensuring proper electrical isolation between the heating element and other conductive parts of the PCB is essential to prevent short circuits and electrical hazards. This can be achieved through the use of insulating materials, such as soldermask or conformal coatings, and by maintaining adequate clearance and creepage distances between conductive traces.
Moisture and Contamination Protection
PCB heaters should be protected from moisture and contamination, which can cause corrosion, short circuits, and degradation of the heater’s performance. Conformal coatings, encapsulation, or hermetic sealing can be used to protect the heater from environmental factors.
Compliance with Safety Standards
PCB heaters must comply with relevant safety standards and regulations, such as UL, CE, or RoHS, depending on the application and region. Adhering to these standards ensures that the heater meets the required safety criteria and is suitable for its intended use.
Maintenance and Troubleshooting
Regular maintenance and troubleshooting can help extend the lifespan of PCB heaters and ensure their reliable operation.
Inspection and Cleaning
Periodically inspecting the PCB heater for signs of damage, corrosion, or contamination can help identify potential issues before they lead to failure. Cleaning the heater with appropriate solvents or compressed air can remove dust, dirt, and other contaminants that may affect its performance.
Temperature Calibration
Over time, temperature sensors may drift and require calibration to maintain accurate temperature control. Regularly checking the temperature accuracy of the heater and performing calibration, if necessary, can help ensure consistent performance.
Troubleshooting Common Issues
Common issues with PCB heaters include uneven heating, insufficient heating, or complete failure. These issues can often be traced back to problems such as damaged heating elements, faulty temperature sensors, or loose connections. Systematically testing the heater’s components and connections can help identify the root cause of the problem and guide the appropriate repair or replacement.
Future Trends in PCB Heaters
As technology advances, PCB heaters continue to evolve to meet the changing needs of various industries.
Integration of Smart Features
The integration of smart features, such as wireless connectivity, real-time monitoring, and remote control, is becoming increasingly common in PCB heaters. These features allow for easier management, data logging, and predictive maintenance, improving the overall efficiency and reliability of the heating system.
Miniaturization and Increased Power Density
With the growing demand for smaller, more compact devices, PCB heaters are being designed with reduced footprints and increased power densities. Advances in materials science and manufacturing techniques enable the development of thinner, more efficient heating elements that can deliver higher temperatures in smaller packages.
Sustainable and Eco-Friendly Materials
There is a growing trend towards the use of sustainable and eco-friendly materials in PCB heaters. This includes the use of recyclable substrates, such as paper or bioplastics, and the development of new heating element materials that are less toxic and more environmentally friendly.
Frequently Asked Questions (FAQ)
-
What is the typical lifespan of a PCB heater?
The lifespan of a PCB heater depends on various factors, such as the heater’s design, materials, and operating conditions. With proper design and maintenance, PCB heaters can last for several years, often exceeding 10,000 hours of continuous operation. -
Can PCB heaters be customized for specific applications?
Yes, PCB heaters can be easily customized to suit specific applications. Factors such as the heater’s size, shape, power density, and temperature range can be tailored to meet the unique requirements of a particular device or system. -
How do I select the appropriate PCB heater for my application?
When selecting a PCB heater, consider factors such as the required temperature range, power density, size constraints, and environmental conditions. Consult with a PCB heater manufacturer or specialist to determine the most suitable heater design for your specific application. -
Are PCB heaters energy-efficient?
PCB heaters are generally energy-efficient compared to other heating methods due to their targeted heating and minimal heat loss. However, the actual energy efficiency depends on factors such as the heater’s design, insulation, and temperature control method. -
How do I ensure the safety of my PCB heater?
To ensure the safety of your PCB heater, incorporate overheating protection, ensure proper electrical isolation, protect against moisture and contamination, and comply with relevant safety standards and regulations. Regularly inspect and maintain the heater to identify and address potential issues before they lead to failures or safety hazards.
Conclusion
PCB heaters are a versatile, efficient, and reliable heating solution for a wide range of applications. By understanding the different types of PCB heaters, their design considerations, and manufacturing processes, engineers and designers can create customized heating solutions that meet the specific requirements of their projects. Ensuring safety, regular maintenance, and staying informed about future trends in PCB heater technology will help optimize the performance and longevity of these essential components in modern electronic devices and systems.
0 Comments