What is an Aluminum PCB?
An Aluminum PCB, also known as a Metal Core PCB (MCPCB), is a type of printed circuit board that uses an aluminum substrate instead of the traditional FR-4 material. The aluminum substrate provides excellent thermal conductivity, allowing for better heat dissipation compared to standard PCBs. This makes Aluminum PCBs ideal for applications that generate a significant amount of heat, such as high-power LEDs, power electronics, and automotive systems.
Structure of an Aluminum PCB
An Aluminum PCB typically consists of three layers:
- Dielectric layer: This layer is a thin, thermally conductive material that electrically isolates the copper circuit layer from the aluminum substrate.
- Copper circuit layer: This layer contains the actual circuit traces and components, just like a standard PCB.
- Aluminum substrate: The base layer of the PCB, which provides mechanical support and acts as a heat sink.
Here’s a visual representation of the layers in an Aluminum PCB:
Layer | Material | Thickness |
---|---|---|
Copper Circuit | Copper | 1-4 oz |
Dielectric | Thermally Conductive Material | 0.003″ – 0.006″ |
Aluminum Substrate | Aluminum Alloy | 0.04″ – 0.25″ |
Advantages of Aluminum PCBs
1. Enhanced Thermal Management
The primary advantage of using an Aluminum PCB is its superior thermal management properties. The aluminum substrate has a much higher thermal conductivity than FR-4, allowing it to quickly and efficiently transfer heat away from the components. This helps to prevent overheating and ensures stable performance, even in high-temperature environments.
2. Improved Reliability
By effectively dissipating heat, Aluminum PCBs can significantly improve the reliability and lifespan of electronic components. This is particularly important for applications that operate in harsh conditions or require continuous operation, such as industrial control systems, automotive electronics, and outdoor lighting.
3. Reduced Size and Weight
Aluminum PCBs can be made thinner and lighter than traditional PCBs, as the aluminum substrate provides both mechanical support and heat dissipation. This allows for more compact designs and reduces the overall weight of the electronic device, which is crucial for applications such as aerospace, drones, and portable devices.
4. Cost-Effective Solution
While Aluminum PCBs may have a higher initial cost compared to standard PCBs, they can be a cost-effective solution in the long run. The improved thermal management and reliability can reduce the need for additional heat sinks, cooling systems, and maintenance, ultimately saving on overall system costs.
Applications of Aluminum PCBs
1. LED Lighting
Aluminum PCBs are widely used in LED lighting applications, particularly for high-power LEDs. The excellent thermal conductivity of the aluminum substrate helps to dissipate the heat generated by the LEDs, ensuring optimal performance and longevity. This is crucial for applications such as street lighting, stadium lighting, and automotive lighting.
2. Power Electronics
Power electronic devices, such as motor drives, inverters, and power supplies, generate significant amounts of heat due to the high currents and voltages involved. Aluminum PCBs can effectively manage this heat, allowing for more compact designs and reliable operation in demanding environments.
3. Automotive Electronics
The automotive industry has increasingly adopted Aluminum PCBs for various electronic systems, such as engine control units, power steering control modules, and LED headlights. The enhanced thermal management and reliability provided by Aluminum PCBs are essential for the harsh operating conditions encountered in vehicles, including high temperatures, vibrations, and moisture.
4. Aerospace and Defense
Aluminum PCBs are well-suited for aerospace and defense applications, where weight reduction and reliable performance are critical. The compact design and excellent thermal management properties of Aluminum PCBs make them ideal for use in avionics, radar systems, and satellite communications equipment.
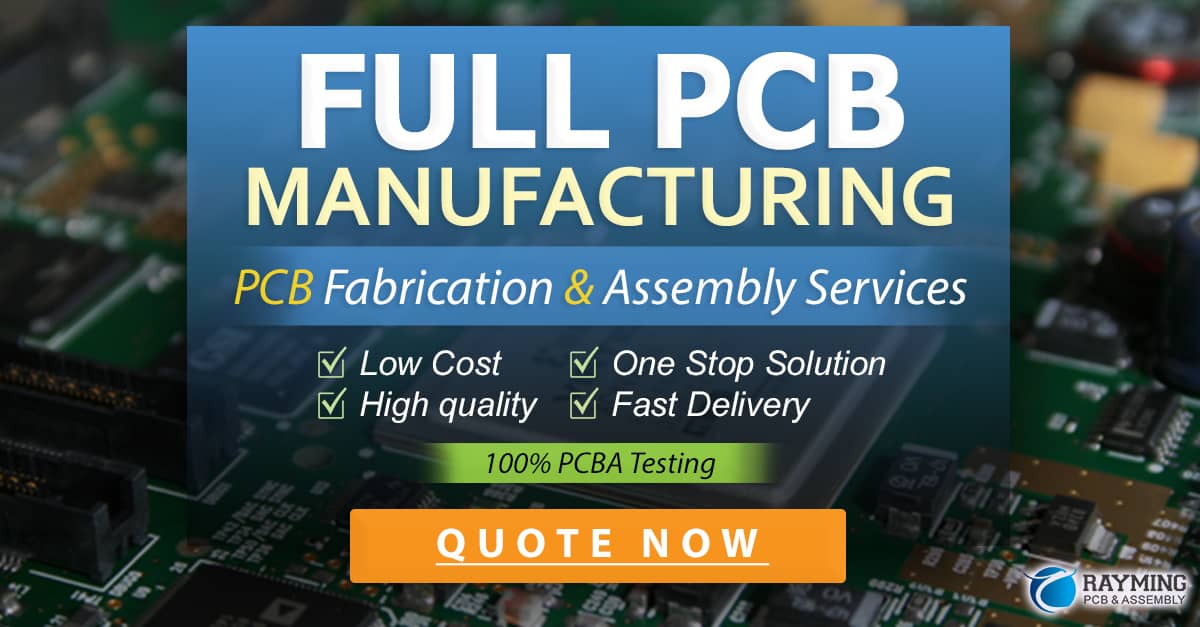
Designing with Aluminum PCBs
When designing circuits using Aluminum PCBs, there are several key considerations to keep in mind:
1. Thermal Management
While the aluminum substrate provides excellent thermal conductivity, it is still essential to carefully consider the thermal design of your circuit. This includes properly sizing the aluminum substrate, selecting appropriate dielectric materials, and strategically placing components to optimize heat dissipation.
2. Electrical Isolation
The dielectric layer in an Aluminum PCB is crucial for maintaining electrical isolation between the copper circuit layer and the aluminum substrate. It is important to choose a dielectric material with the appropriate thickness and dielectric strength to ensure proper isolation and prevent short circuits.
3. Component Selection
When selecting components for use on an Aluminum PCB, it is important to consider their thermal characteristics and power dissipation requirements. Components with high power densities or temperature-sensitive specifications may require additional thermal management techniques, such as thermal vias or heat sinks.
4. Manufacturing Considerations
Manufacturing Aluminum PCBs requires specialized equipment and processes compared to standard PCBs. It is important to work with a PCB manufacturer that has experience and expertise in fabricating Aluminum PCBs to ensure the highest quality and reliability.
FAQs
-
Q: Can Aluminum PCBs be used for all types of electronic circuits?
A: While Aluminum PCBs offer superior thermal management and reliability, they may not be suitable for all applications. They are best suited for circuits that generate significant amounts of heat or require operation in harsh environments. Standard FR-4 PCBs may be more appropriate for low-power, cost-sensitive applications. -
Q: Are Aluminum PCBs more expensive than traditional PCBs?
A: Aluminum PCBs typically have a higher initial cost compared to standard FR-4 PCBs due to the specialized materials and manufacturing processes involved. However, they can be a cost-effective solution in the long run, as they can reduce the need for additional heat sinks, cooling systems, and maintenance. -
Q: Can Aluminum PCBs be used for high-frequency applications?
A: Aluminum PCBs can be used for high-frequency applications, but special considerations must be made during the design process. The dielectric layer and the surface finish of the copper layer can impact the high-frequency performance of the circuit. It is important to work with a PCB manufacturer that has experience in designing and fabricating high-frequency Aluminum PCBs. -
Q: How do I select the appropriate thickness for the aluminum substrate?
A: The thickness of the aluminum substrate depends on several factors, including the power dissipation requirements of the circuit, the size and weight constraints of the application, and the manufacturing capabilities of the PCB fabricator. Generally, thicker aluminum substrates provide better thermal conductivity and mechanical stability, but may increase the overall thickness and weight of the PCB. It is best to consult with your PCB manufacturer to determine the optimal aluminum substrate thickness for your specific application. -
Q: Can Aluminum PCBs be soldered using standard soldering techniques?
A: Yes, Aluminum PCBs can be soldered using standard soldering techniques, such as reflow soldering or wave soldering. However, it is important to consider the thermal mass of the aluminum substrate when developing the soldering profile, as it may require adjustments to the temperature and duration of the soldering process. Additionally, ensuring proper surface finish and cleanliness of the PCB is crucial for achieving reliable solder joints.
Conclusion
Aluminum PCBs offer a range of benefits over traditional FR-4 PCBs, including enhanced thermal management, improved reliability, reduced size and weight, and cost-effectiveness in certain applications. By understanding the structure, advantages, and key design considerations of Aluminum PCBs, engineers and designers can leverage this technology to create high-performance, reliable electronic systems for a wide range of industries, including LED lighting, power electronics, automotive, aerospace, and defense.
As the demand for more efficient and robust electronic systems continues to grow, Aluminum PCBs are poised to play an increasingly important role in enabling the next generation of innovative products and technologies.
0 Comments