What is an LED PCB?
An LED PCB, or light-emitting diode printed circuit board, is a specialized type of PCB designed to power and control LEDs. LEDs are highly efficient, long-lasting light sources used in a wide variety of applications from industrial and automotive lighting to consumer electronics and displays.
LEDs require a constant current to operate optimally and have specific voltage requirements. An LED PCB incorporates the necessary circuitry to drive the LEDs properly. This typically includes current-limiting resistors and may also have additional components like capacitors, diodes, and ICs for more advanced functionality.
Advantages of LED PCBs
LED PCBs offer several key benefits:
- Compact integration of LEDs and control circuitry
- Efficient heat dissipation for increased LED lifespan
- Enables high power LED applications
- Allows complex LED display patterns and effects
- Durable and vibration resistant
LED PCB Design Considerations
Designing an optimized LED PCB requires careful planning and attention to key factors that impact LED performance, efficiency, and reliability. The main design considerations include:
LED Selection
The type, size, color, and power of the LEDs must be chosen based on the application requirements. High power LEDs generate more heat and may require aluminium core PCBs for sufficient heat dissipation.
Circuit Design
The driver circuit should deliver the appropriate current to each LED. Current-limiting resistors are the simplest way to control current. More complex designs may use constant current drivers or PWM circuits for precise control and dimming.
Power Supply
LEDs are current-driven devices and require a clean, stable power supply. The power supply should provide sufficient voltage and current for all LEDs in the circuit. Capacitors are often used to smooth voltage ripple.
Thermal Management
LEDs generate a significant amount of heat, especially high power versions. Proper thermal management is critical to prevent overheating which degrades LED lifespan and efficiency. Using wider copper traces, thermal vias, and heatsinks helps dissipate heat. Aluminum core PCBs are ideal for high power applications.
Layout
A thoughtful PCB layout optimizes electrical and thermal performance. Guidelines include:
- Placing current-limiting resistors close to LEDs
- Using wide, short traces to minimize voltage drop
- Providing adequate space between components for heat dissipation
- Separating high and low current traces
- Using ground planes for efficient current return
LED PCB Materials
The PCB material impacts the electrical, thermal, and mechanical performance of the LED PCB. The most common types are:
Material | Composition | Thermal Conductivity (W/mK) | Dielectric Constant @1MHz | Applications |
---|---|---|---|---|
FR-4 | Glass fiber/epoxy | 0.3 | 4.5 | General purpose |
Metal core (MCPCB) | Dielectric layer/metal core | 1-8 | 4.5 | High power LEDs |
Flexible | Polyimide/PET | 0.2 | 3.2-3.5 | Wearables, displays |
Ceramic | Alumina, AlN | 20-180 | 9.8 | UV LEDs, high power |
FR-4 is the most common material for low power LED PCBs. Metal core PCBs, specifically aluminum, provide excellent heat transfer for high power applications. Flexible PCBs are used where the LED PCB needs to conform to a curved surface or flex during use. Ceramic PCBs offer the highest thermal conductivity for the most demanding high power LEDs.
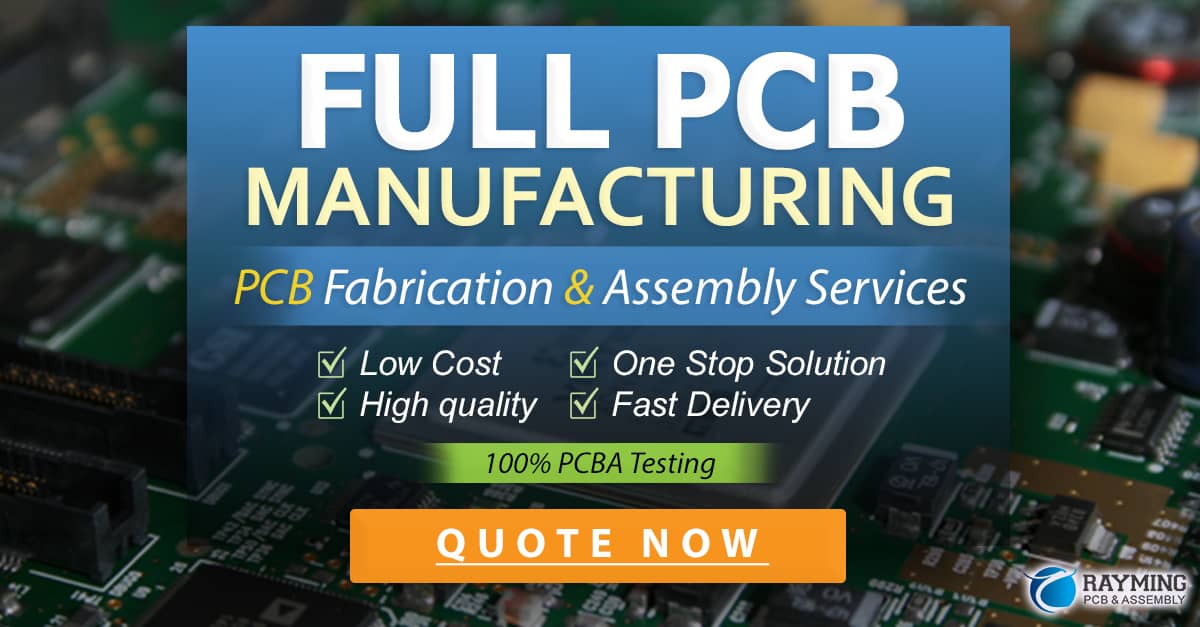
LED PCB Manufacturing Process
LED PCBs are fabricated using standard PCB manufacturing processes with some specialized steps:
-
Material Selection – The appropriate PCB material is chosen based on the application.
-
Circuit Design – The schematic circuit is designed including LEDs and driver components.
-
PCB Layout – The physical PCB layout is created from the schematic.
-
PCB Fabrication – The bare PCB is manufactured using etching, drilling, and plating processes. Solder mask and silkscreen are applied.
-
Component Placement – The LEDs and other SMD components are placed onto the PCB using automated pick-and-place machines.
-
Reflow Soldering – The populated PCB is run through a reflow oven which melts the solder paste, soldering the components.
-
Inspection and Test – The assembled LED PCB is visually inspected and electrically tested to ensure proper functionality.
-
Potting/Coating – For harsh environments, the LED PCB may be potted in epoxy or conformal coated for protection.
Applications of LED PCBs
LED PCBs are used in countless applications across industries. Some common uses include:
Lighting
- Residential and commercial light fixtures
- Industrial and warehouse lighting
- Automotive headlights and tail lights
- Street and traffic lights
- Stage and entertainment lighting
Displays
- LCD backlights for TVs, monitors, phones
- LED video walls and digital signage
- Wearable displays
- Virtual reality and gaming headsets
- Instrument panels and gauges
Indicators and Signals
- Fire/smoke alarms and detectors
- Control panel status lights and buttons
- Aviation and marine navigation lights
- Railroad signal lights
LED PCB Troubleshooting
When an LED PCB is not functioning as intended, methodical troubleshooting can identify the issue.
Visual Inspection
Check for any obvious physical damage, cold solder joints, or burnt components. Ensure LEDs are in the correct orientation.
Power Supply Check
Verify the power supply is providing the specified voltage and current. Check for any voltage drop across long PCB traces or wires.
LED Continuity
With power off, use a multimeter to check continuity across each LED. An open LED will not illuminate.
Component Temperatures
Use an infrared thermometer to check component temperatures. Overheating can indicate short circuits, overcurrent, or inadequate heat sinking.
Current Measurements
Measure current flow through each string of LEDs. Current should be consistent and not exceed the maximum rating. High current can overheat and damage LEDs.
FAQ
Q: How do I select the right LED for my PCB design?
A: Consider the following factors when choosing an LED:
– Color (wavelength)
– Brightness (lumens or candela)
– Forward voltage and current
– Viewing angle
– Size and package type
Select an LED that meets your optical output and efficiency requirements while staying within the electrical and thermal limits of your PCB design.
Q: Why are Aluminum PCBs used for LEDs?
A: Aluminum PCBs, also known as metal core PCBs (MCPCBs), are used for high power LED applications because of their excellent thermal conductivity. The aluminum substrate quickly spreads and dissipates the heat generated by the LEDs, preventing thermal damage and extending their lifespan. This is critical for high brightness and high power LEDs which generate significant heat.
Q: What is the purpose of the current-limiting resistor in an LED circuit?
A: LEDs are current-driven devices and require a specific forward current to operate optimally. Exceeding this current can cause the LED to burn out prematurely. The current-limiting resistor serves to limit the current flowing through the LED to its specified value, protecting it from overcurrent damage. The resistor value is chosen based on the LED’s forward voltage and the supply voltage using Ohm’s law.
Q: Can I use standard FR-4 PCBs for LED applications?
A: FR-4 PCBs are suitable for most low power LED applications. However, for high power LEDs or dense LED arrays, FR-4 may not provide adequate heat dissipation, leading to reduced LED lifespan and efficiency. In these cases, aluminum PCBs or other high thermal conductivity substrates are recommended to manage the heat load and maintain LED performance.
Q: How do I control the brightness of LEDs on a PCB?
A: There are two main methods to control LED brightness on a PCB:
-
Analog dimming – Varying the DC current through the LED using a variable resistor or a dedicated LED driver IC. Higher current equals brighter light.
-
Pulse Width Modulation (PWM) dimming – Rapidly switching the LED on and off with a fixed current but varying the on/off time ratio. Longer “on” time equals brighter perceived light. PWM is the preferred method as it maintains consistent LED color and efficiency.
In summary, LED PCBs are specialized printed circuit boards designed to optimally drive and control LEDs. Proper PCB material selection, circuit design, layout, and thermal management are critical for LED performance and longevity. LED PCBs enable the efficient use of LEDs in a wide array of applications from general lighting to high resolution displays. As LED technology continues to advance, so will the capabilities and complexities of LED PCBs.
0 Comments