Introduction to Automotive PCBs
Automotive Printed Circuit Boards (PCBs) are essential components in modern vehicles, powering various electronic systems such as engine control units, infotainment systems, and advanced driver assistance systems (ADAS). As the automotive industry continues to evolve and incorporate more advanced technologies, the demand for high-quality, reliable automotive PCBs has never been greater. Choosing the right automotive PCB manufacturer is crucial to ensure the safety, performance, and longevity of your vehicle’s electronic systems.
Key Factors to Consider When Selecting an Automotive PCB Manufacturer
When selecting an automotive PCB manufacturer, there are several key factors to consider to ensure you partner with a reliable and experienced provider. These factors include:
1. Industry Certifications and Standards Compliance
Ensure that the automotive PCB manufacturer holds relevant industry certifications and complies with international standards. Some important certifications and standards to look for include:
- IATF 16949: Quality management system standard for the automotive industry
- ISO 9001: Quality management system standard
- IPC-A-610: Acceptability of electronic assemblies
- IPC-6012: Qualification and performance specification for rigid printed boards
- UL 94: Standard for flammability of plastic materials
2. Experience and Expertise in Automotive PCB Manufacturing
Choose a manufacturer with extensive experience and expertise in producing automotive PCBs. They should have a proven track record of delivering high-quality products to automotive clients and be familiar with the unique challenges and requirements of the industry.
3. State-of-the-Art Facilities and Equipment
A reliable automotive PCB manufacturer should invest in state-of-the-art facilities and equipment to ensure consistent product quality and efficiency. Look for manufacturers that utilize advanced manufacturing technologies, such as:
- Automated optical inspection (AOI)
- 3D solder paste inspection (SPI)
- Flying probe testing
- X-ray inspection
4. Robust Quality Control and Testing Procedures
Quality control and testing are critical aspects of automotive PCB manufacturing. Ensure that the manufacturer has a comprehensive quality management system in place and conducts rigorous testing at various stages of the production process. Some essential testing procedures include:
- Electrical testing
- Environmental stress screening (ESS)
- Thermal cycling
- Vibration testing
- Accelerated life testing (ALT)
5. Supply Chain Management and On-Time Delivery
A reliable automotive PCB manufacturer should have a well-managed supply chain and be able to deliver products on time consistently. They should have strong relationships with raw material suppliers and implement efficient inventory management practices to minimize lead times and ensure a stable supply of components.
6. Customer Support and Communication
Choose a manufacturer that offers excellent customer support and maintains open communication throughout the project. They should be responsive to your inquiries, provide regular updates on project progress, and be willing to collaborate closely with your team to address any issues or concerns.
Automotive PCB Manufacturing Process Overview
Understanding the automotive PCB manufacturing process can help you better evaluate potential manufacturers and ensure they have the capabilities to meet your specific requirements. The typical automotive PCB manufacturing process involves the following steps:
-
Design and Engineering: The PCB design is created using specialized software, taking into account the specific requirements of the automotive application.
-
Material Selection: High-quality, automotive-grade materials are selected for the PCB substrate, copper foil, and other components.
-
PCB Fabrication: The PCB is fabricated using a multi-step process that includes:
- Printing and etching the circuit pattern onto the copper-clad substrate
- Drilling holes for component placement
- Applying solder mask and silkscreen
-
Surface finishing (e.g., ENIG, HASL, or OSP)
-
Component Placement: Electronic components are placed onto the PCB using automated pick-and-place machines.
-
Soldering: The components are soldered onto the PCB using reflow or wave soldering techniques.
-
Inspection and Testing: The assembled PCB undergoes various inspections and tests to ensure quality and functionality, including AOI, X-ray inspection, and electrical testing.
-
Conformal Coating: A protective coating is applied to the PCB to shield it from environmental factors such as moisture, dust, and chemicals.
-
Final Inspection and Packaging: The finished automotive PCB undergoes a final inspection before being packaged and shipped to the customer.
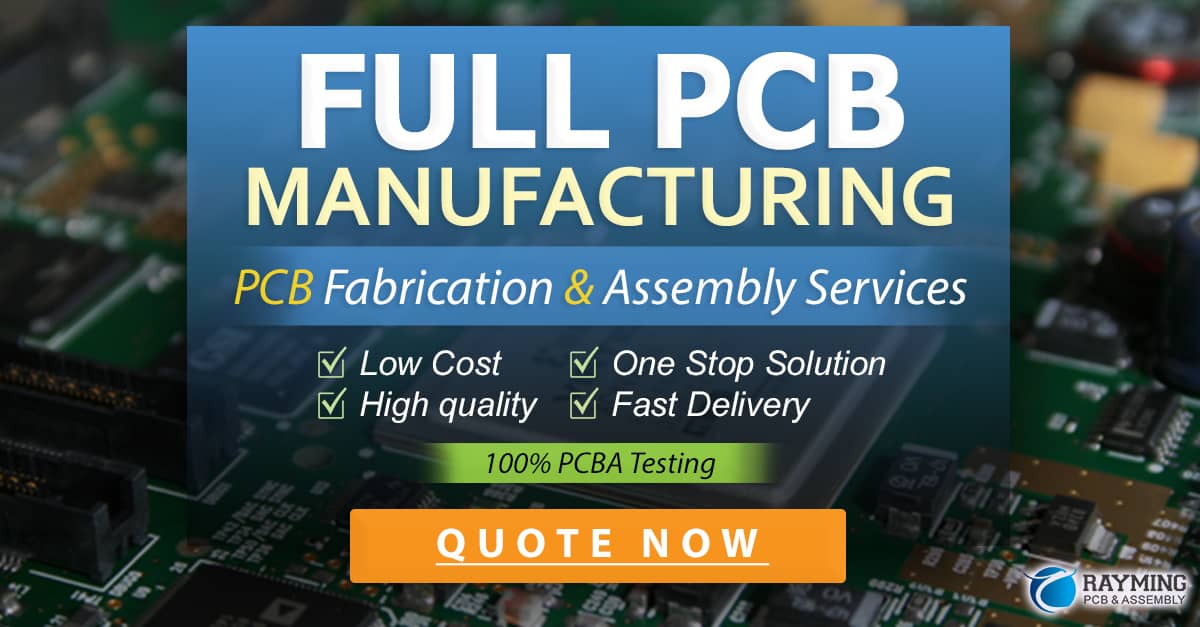
Automotive PCB Material Selection
Selecting the right materials for automotive PCBs is crucial to ensure their reliability and performance in harsh operating conditions. Some common materials used in automotive PCB manufacturing include:
Material | Description | Benefits |
---|---|---|
FR-4 | A glass-reinforced epoxy laminate | – Cost-effective – Good mechanical and electrical properties – Suitable for most automotive applications |
High Tg FR-4 | FR-4 with a higher glass transition temperature | – Improved thermal stability – Better resistance to thermal cycling – Ideal for high-temperature automotive environments |
Polyimide | A high-performance polymer material | – Excellent thermal stability – High mechanical strength – Resistance to chemicals and solvents |
Copper | The conductive material used for PCB traces | – High electrical conductivity – Good thermal conductivity – Available in various thicknesses to suit different applications |
Automotive PCB Design Considerations
Designing automotive PCBs requires careful consideration of various factors to ensure optimal performance and reliability. Some key design considerations include:
1. Environmental Factors
Automotive PCBs are exposed to harsh environmental conditions, such as extreme temperatures, vibrations, and moisture. Designers must take these factors into account and incorporate appropriate protection measures, such as:
- Using high-temperature materials
- Implementing vibration-damping techniques
- Applying conformal coatings to protect against moisture and contaminants
2. Electromagnetic Compatibility (EMC)
Automotive PCBs must be designed to minimize electromagnetic interference (EMI) and ensure electromagnetic compatibility (EMC) with other electronic systems in the vehicle. Some EMC design techniques include:
- Proper grounding and shielding
- Minimizing loop areas and trace lengths
- Using filters and ferrites to suppress high-frequency noise
3. Power Management
Efficient power management is essential for automotive PCBs to ensure optimal performance and minimize power consumption. Designers should consider:
- Selecting appropriate voltage regulators and power converters
- Implementing power sequencing and monitoring
- Using low-power components and design techniques
4. Signal Integrity
Maintaining signal integrity is crucial for automotive PCBs to ensure reliable data transmission and prevent errors. Some signal integrity design considerations include:
- Impedance matching and termination
- Minimizing crosstalk and reflections
- Using differential signaling for high-speed data transmission
5. Thermal Management
Proper thermal management is essential to prevent overheating and ensure the long-term reliability of automotive PCBs. Designers should consider:
- Using thermal vias and heat sinks to dissipate heat
- Selecting components with appropriate power ratings and thermal characteristics
- Implementing temperature monitoring and protection circuitry
Automotive PCB Testing and Validation
Thorough testing and validation are essential to ensure the reliability and performance of automotive PCBs. Some common testing and validation methods include:
1. Environmental Stress Screening (ESS)
ESS involves subjecting the PCB to various environmental stresses, such as temperature cycling, vibration, and humidity, to identify potential weaknesses and failures.
2. Accelerated Life Testing (ALT)
ALT is used to predict the long-term reliability of automotive PCBs by subjecting them to elevated stress levels for a shorter duration. This helps identify potential failure modes and estimate the product’s lifespan.
3. Functional Testing
Functional testing verifies that the automotive PCB performs as intended under various operating conditions. This includes testing the PCB’s response to different input signals, communication protocols, and power supply variations.
4. Electrical Testing
Electrical testing verifies that the automotive PCB meets the specified electrical characteristics, such as voltage, current, resistance, and capacitance.
5. Electromagnetic Compatibility (EMC) Testing
EMC testing ensures that the automotive PCB does not generate excessive electromagnetic interference (EMI) and is not susceptible to external EMI sources. This involves conducting radiated and conducted emissions tests, as well as immunity tests.
Automotive PCB Manufacturing Challenges and Solutions
Automotive PCB manufacturing presents unique challenges due to the stringent quality and reliability requirements of the industry. Some common challenges and their solutions include:
1. Miniaturization and High-Density Interconnect (HDI)
As automotive electronics become more complex and compact, there is a growing demand for miniaturized PCBs with high-density interconnects. To address this challenge, manufacturers can:
- Utilize advanced PCB fabrication techniques, such as micro-vias and embedded components
- Implement 3D PCB design and stacked-via technology
- Use high-resolution printing and etching processes
2. Harsh Environmental Conditions
Automotive PCBs must withstand extreme temperatures, vibrations, and exposure to moisture and chemicals. To overcome these challenges, manufacturers can:
- Select high-performance materials with excellent thermal and mechanical properties
- Implement robust protection measures, such as conformal coatings and potting compounds
- Conduct thorough environmental stress screening and accelerated life testing
3. Supply Chain Management and Cost Pressure
Managing the supply chain and controlling costs are ongoing challenges in automotive PCB manufacturing. To address these issues, manufacturers can:
- Establish long-term partnerships with reliable raw material suppliers
- Implement lean manufacturing practices and continuous improvement initiatives
- Utilize advanced inventory management systems and just-in-time (JIT) delivery
4. Rapid Technological Advancements
The automotive industry is constantly evolving, with new technologies and requirements emerging regularly. To stay competitive, automotive PCB Manufacturers must:
- Invest in research and development to stay at the forefront of technological advancements
- Collaborate closely with customers and industry partners to understand and address emerging needs
- Continuously upgrade their facilities and equipment to support new manufacturing processes and materials
Future Trends in Automotive PCB Manufacturing
As the automotive industry continues to evolve, several trends are shaping the future of automotive PCB manufacturing:
1. Increased Adoption of Advanced Driver Assistance Systems (ADAS) and Autonomous Vehicles
The growing demand for ADAS and autonomous vehicles is driving the need for more complex and reliable automotive PCBs. Manufacturers must develop PCBs that can support high-speed data processing, sensor integration, and failsafe mechanisms.
2. Shift Towards Electrification and Hybrid Vehicles
The global push towards electrification and hybrid vehicles is creating new opportunities and challenges for automotive PCB manufacturers. PCBs for electric and hybrid vehicles must support high-power electronics, battery management systems, and efficient power distribution.
3. 5G and Vehicle-to-Everything (V2X) Communication
The advent of 5G networks and V2X communication is enabling new possibilities for connected and intelligent vehicles. Automotive PCB manufacturers must develop PCBs that can support high-speed, low-latency communication and ensure the security and reliability of data transmission.
4. Sustainability and Eco-Friendly Manufacturing
As environmental concerns continue to grow, there is an increasing focus on sustainable and eco-friendly manufacturing practices in the automotive PCB industry. Manufacturers are exploring the use of biodegradable materials, implementing energy-efficient processes, and developing recycling and waste reduction initiatives.
Conclusion
Choosing a reliable automotive PCB manufacturer is essential to ensure the safety, performance, and longevity of your vehicle’s electronic systems. By considering factors such as industry certifications, experience, manufacturing capabilities, quality control, and customer support, you can select a manufacturer that meets your specific needs and requirements.
As the automotive industry continues to evolve, PCB manufacturers must adapt to new technologies, materials, and manufacturing processes to stay competitive. By staying at the forefront of these trends and continuously improving their capabilities, automotive PCB manufacturers can play a crucial role in shaping the future of the industry.
Frequently Asked Questions (FAQ)
1. What is the difference between automotive PCBs and regular PCBs?
Automotive PCBs are designed to withstand harsh environmental conditions, such as extreme temperatures, vibrations, and exposure to moisture and chemicals. They also have to meet stringent quality and reliability standards, as well as industry-specific certifications and requirements. Regular PCBs, on the other hand, may not be designed to withstand such conditions or meet the same standards.
2. How do I know if an automotive PCB manufacturer is reliable?
A reliable automotive PCB manufacturer should hold relevant industry certifications (e.g., IATF 16949, ISO 9001), have extensive experience in automotive PCB manufacturing, invest in state-of-the-art facilities and equipment, implement robust quality control and testing procedures, and offer excellent customer support and communication.
3. What are some common materials used in automotive PCB manufacturing?
Common materials used in automotive PCB manufacturing include FR-4, High Tg FR-4, polyimide, and copper. The choice of material depends on the specific requirements of the application, such as temperature range, mechanical stress, and electrical performance.
4. How can I ensure the electromagnetic compatibility (EMC) of my automotive PCB?
To ensure the EMC of your automotive PCB, consider implementing proper grounding and shielding techniques, minimizing loop areas and trace lengths, and using filters and ferrites to suppress high-frequency noise. It’s also essential to conduct thorough EMC testing to verify that the PCB meets the required standards.
5. What are some future trends in automotive PCB manufacturing?
Some future trends in automotive PCB manufacturing include the increased adoption of advanced driver assistance systems (ADAS) and autonomous vehicles, the shift towards electrification and hybrid vehicles, the integration of 5G and vehicle-to-everything (V2X) communication, and the focus on sustainability and eco-friendly manufacturing practices.
0 Comments