Introduction to SMT stencils and PCB prototyping
Surface Mount Technology (SMT) has revolutionized the world of electronics manufacturing, enabling the production of smaller, more compact, and highly efficient printed circuit boards (PCBs). One of the key components in the SMT process is the use of SMT stencils, which play a crucial role in simplifying the PCB prototyping process. In this article, we will explore how and why SMT stencils are essential for efficient and accurate PCB prototyping.
What are SMT Stencils?
SMT stencils are thin, flat sheets of metal or other materials that are precisely cut with apertures corresponding to the pads on a PCB. These apertures allow for the controlled application of solder paste onto the PCB pads, ensuring the correct amount of paste is deposited in the right locations. SMT stencils are typically made from stainless steel, brass, or nickel, and can be custom-made to suit specific PCB designs.
The Role of SMT Stencils in PCB Prototyping
PCB prototyping is the process of creating a functional prototype of a PCB design before mass production. This process is essential for testing and validating the design, identifying any issues, and making necessary improvements. SMT stencils play a vital role in PCB prototyping by:
- Ensuring precise solder paste application
- Improving the speed and efficiency of the prototyping process
- Reducing the risk of human error
- Enabling the creation of complex PCB designs
Benefits of Using SMT Stencils in PCB Prototyping
1. Precise Solder Paste Application
One of the primary benefits of using SMT stencils in PCB prototyping is the precise application of solder paste. The stencil’s apertures are designed to match the exact dimensions and locations of the PCB pads, ensuring that the correct amount of solder paste is deposited on each pad. This precision is essential for creating reliable and functional PCB Prototypes, as it minimizes the risk of short circuits, bridging, and other solder-related defects.
Advantages of Precise Solder Paste Application
- Improved PCB functionality and reliability
- Reduced risk of short circuits and bridging
- Better component alignment and placement
- Enhanced overall PCB quality
2. Increased Speed and Efficiency
SMT stencils significantly increase the speed and efficiency of the PCB prototyping process. By using a stencil, the solder paste application process is automated, eliminating the need for manual paste dispensing. This automation not only saves time but also ensures consistent paste application across the entire PCB. As a result, PCB prototyping can be completed more quickly, allowing for faster design iterations and shorter time-to-market.
Comparison of Manual vs. Stencil-Based Solder Paste Application
Factor | Manual Application | Stencil-Based Application |
---|---|---|
Speed | Slow | Fast |
Consistency | Variable | Consistent |
Accuracy | Low | High |
Labor Intensity | High | Low |
3. Reduction of Human Error
Human error is a significant concern in PCB prototyping, as even small mistakes can lead to costly delays and rework. By using SMT stencils, the risk of human error is greatly reduced. The stencil’s precise apertures ensure that solder paste is applied consistently and accurately, minimizing the potential for mistakes. This reduction in human error leads to higher quality PCB Prototypes and fewer design iterations, ultimately saving time and resources.
4. Enabling Complex PCB Designs
SMT stencils enable the creation of complex PCB designs with fine-pitch components and high-density layouts. As electronic devices become smaller and more sophisticated, PCBs must accommodate an increasing number of components in limited space. SMT stencils allow for the precise application of solder paste on these compact and intricate PCB designs, ensuring reliable connections and proper component placement.
Examples of Complex PCB Designs Enabled by SMT Stencils
- High-density PCBs for smartphones and wearables
- Multi-layer PCBs for advanced electronic systems
- PCBs with fine-pitch BGA and QFN components
- Flex and rigid-flex PCBs for compact and flexible electronics
Choosing the Right SMT Stencil for PCB Prototyping
Stencil Material Selection
Selecting the appropriate stencil material is crucial for successful PCB prototyping. The most common materials used for SMT stencils are stainless steel, brass, and nickel. Each material has its own advantages and disadvantages, and the choice depends on factors such as durability, cost, and the specific requirements of the PCB design.
Comparison of SMT Stencil Materials
Material | Durability | Cost | Suitable Applications |
---|---|---|---|
Stainless Steel | High | Moderate | High-volume production, fine-pitch designs |
Brass | Moderate | Low | Low-volume production, less demanding designs |
Nickel | High | High | High-volume production, ultra-fine pitch designs |
Stencil Thickness Considerations
The thickness of an SMT stencil plays a vital role in determining the amount of solder paste deposited on the PCB pads. Thicker stencils deposit more paste, while thinner stencils deposit less. The optimal stencil thickness depends on factors such as the size and pitch of the components, the PCB’s pad geometry, and the desired solder joint profile.
Common SMT Stencil Thicknesses and Their Applications
Thickness (mm) | Typical Applications |
---|---|
0.100 | Standard SMD components, 0.5mm pitch and above |
0.125 | Fine-pitch components, 0.4mm to 0.5mm pitch |
0.150 | Ultra-fine pitch components, 0.3mm pitch and below |
0.200 | Power components, connectors, and other large components |
Aperture Design and Customization
The aperture design of an SMT stencil is critical for ensuring the correct amount of solder paste is deposited on each PCB pad. Apertures can be customized to suit specific PCB designs, taking into account factors such as pad size, shape, and pitch. Proper aperture design helps to minimize solder defects and improve the overall quality of the PCB prototype.
Common Aperture Designs and Their Benefits
- Rectangular apertures: Simple and effective for most SMD components
- Circular apertures: Ideal for round pads and BGA components
- D-shaped apertures: Provide better paste release for fine-pitch components
- Home plate apertures: Optimize paste deposition for QFP and SOIC components
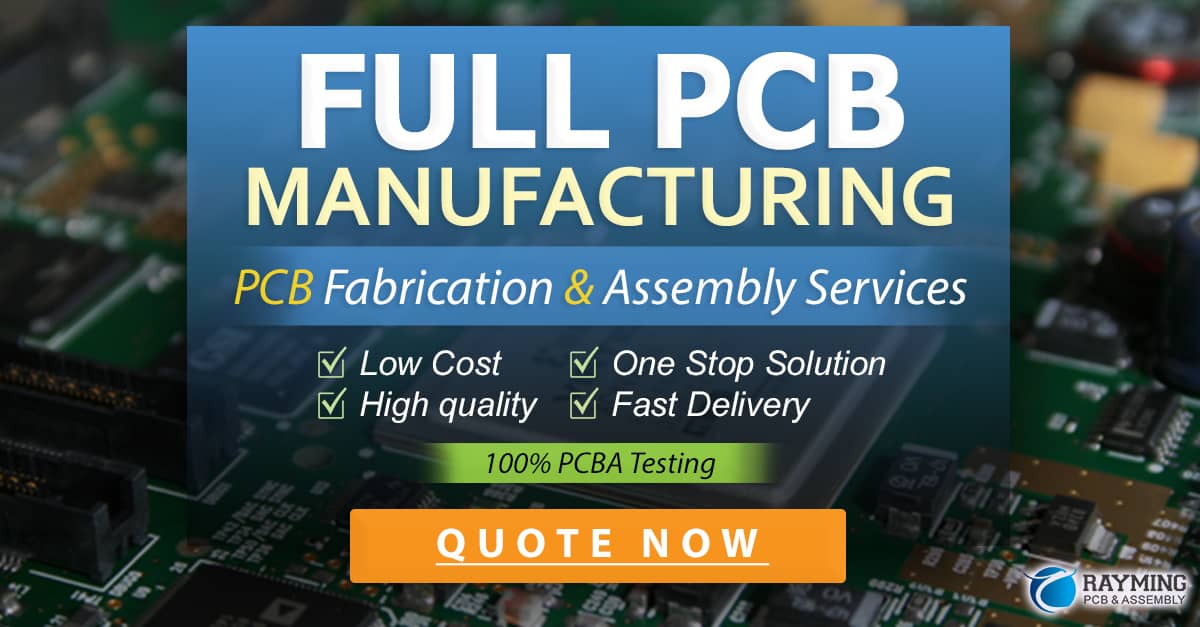
Stencil Cleaning and Maintenance
Proper cleaning and maintenance of SMT stencils are essential for ensuring consistent solder paste application and extending the stencil’s lifespan. Regularly cleaning the stencil prevents the buildup of solder paste residue, which can clog apertures and lead to defects in the PCB prototype.
Stencil Cleaning Methods
- Manual cleaning with solvents and wiping materials
- Automated stencil cleaning systems using ultrasonic or spray technologies
- Stencil underwipe systems for in-process cleaning
Stencil Storage and Handling
Proper storage and handling of SMT stencils are crucial for maintaining their quality and performance. Stencils should be stored in a clean, dry environment and protected from damage during handling. When not in use, stencils should be kept in protective packaging or containers to prevent contamination and damage.
Frequently Asked Questions (FAQ)
-
Q: Can SMT stencils be used for both prototyping and production?
A: Yes, SMT stencils are suitable for both PCB prototyping and high-volume production. The same stencil can often be used for both purposes, ensuring consistency throughout the product development cycle. -
Q: How long do SMT stencils typically last?
A: The lifespan of an SMT stencil depends on factors such as the material, thickness, and frequency of use. With proper cleaning and maintenance, a high-quality stencil can last for thousands of print cycles. -
Q: Can SMT stencils be customized for specific PCB designs?
A: Yes, SMT stencils can be custom-made to suit specific PCB designs. Stencil manufacturers can create stencils with customized apertures, thicknesses, and materials based on the requirements of the PCB. -
Q: How do I choose the right stencil thickness for my PCB prototype?
A: The choice of stencil thickness depends on factors such as the size and pitch of the components, the PCB’s pad geometry, and the desired solder joint profile. Consult with your stencil manufacturer or use industry guidelines to determine the appropriate thickness for your specific PCB design. -
Q: Can SMT stencils be used with different solder paste types?
A: Yes, SMT stencils can be used with various solder paste types, including lead-based and lead-free pastes. However, it is essential to ensure that the stencil’s aperture design and thickness are compatible with the specific solder paste being used.
Conclusion
In conclusion, the utilization of SMT stencils significantly simplifies the process of PCB prototyping by ensuring precise solder paste application, increasing speed and efficiency, reducing human error, and enabling the creation of complex PCB designs. By choosing the right stencil material, thickness, and aperture design, and following proper cleaning and maintenance procedures, PCB designers and manufacturers can leverage the benefits of SMT stencils to create high-quality, reliable PCB prototypes. As the demand for smaller, more advanced electronic devices continues to grow, the use of SMT stencils in PCB prototyping will remain an essential tool for innovation and success in the electronics industry.
0 Comments