Introduction to PCB Prototyping
Printed Circuit Board (PCB) prototyping is an essential step in the electronics design process. It allows engineers and hobbyists to test and validate their circuit designs before committing to large-scale production. PCB Prototypes help identify potential issues, optimize performance, and ensure the overall functionality of the circuit.
In this article, we will explore the world of low-cost 1 to 4 layer PCB prototypes, discussing various aspects such as PCB design considerations, fabrication techniques, and cost-saving strategies. Whether you’re a seasoned electronic engineer or a beginner in the field, understanding PCB prototyping is crucial for bringing your ideas to life.
Understanding PCB Layers
PCBs consist of one or more conductive layers that interconnect electronic components. The number of layers in a PCB depends on the complexity of the circuit and the desired functionality. Let’s take a closer look at the different layer configurations:
Single Layer PCBs
Single layer PCBs, also known as 1-layer PCBs, have conductive traces on only one side of the board. They are the simplest and most cost-effective option for basic circuits with a low component count. Single layer PCBs are commonly used in:
- Simple Arduino projects
- LED circuits
- Basic sensor applications
Double Layer PCBs
Double layer PCBs, or 2-layer PCBs, have conductive traces on both sides of the board. They offer more design flexibility and allow for higher component density compared to single layer PCBs. Double layer PCBs are suitable for:
- Microcontroller-based projects
- Moderate complexity circuits
- Low-power applications
Multi-Layer PCBs
Multi-layer PCBs have three or more conductive layers, with insulating material separating each layer. The most common configurations are 4-layer and 6-layer PCBs. Multi-layer PCBs offer several advantages:
- Increased routing density
- Better signal integrity
- Improved electromagnetic compatibility (EMC)
- Enhanced thermal management
Multi-layer PCBs are commonly used in:
- High-speed digital circuits
- RF and wireless applications
- Complex analog circuits
Layer Count | Typical Applications |
---|---|
1 | Simple circuits, LED projects |
2 | Microcontroller projects, moderate complexity |
4 | High-speed digital, RF, complex analog |
6 or more | High-density designs, advanced applications |
PCB Design Considerations
When designing a PCB prototype, several factors need to be considered to ensure optimal performance and manufacturability. Let’s discuss some key design considerations:
Component Selection and Placement
Choosing the right components and placing them strategically on the PCB is crucial for a successful design. Consider the following:
- Select components with appropriate ratings and packages
- Place components to minimize trace lengths and signal interference
- Consider thermal dissipation and provide adequate spacing
- Follow manufacturer’s recommendations for component placement
Trace Routing and Spacing
Proper trace routing and spacing are essential for maintaining signal integrity and avoiding issues like crosstalk and electromagnetic interference (EMI). Keep these guidelines in mind:
- Use appropriate trace widths based on current requirements
- Maintain adequate spacing between traces to prevent short circuits
- Avoid sharp angles and use smooth curves for trace routing
- Use ground planes and power planes for better signal integrity
Design for Manufacturing (DFM)
Designing your PCB prototype with manufacturing in mind can save you time and money in the long run. Consider the following DFM practices:
- Adhere to the manufacturer’s design rules and guidelines
- Use standard hole sizes and pad dimensions
- Provide adequate clearance for tooling and assembly
- Include fiducial markers for automated assembly processes
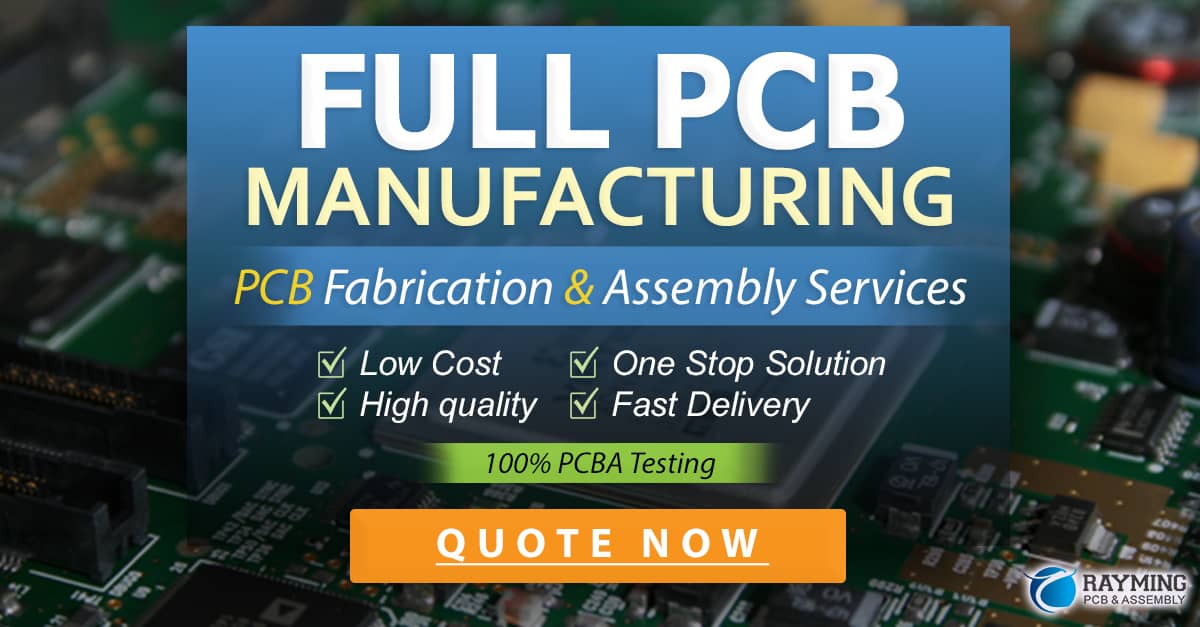
PCB Fabrication Techniques
There are several fabrication techniques used for creating PCB prototypes. Understanding these techniques can help you choose the most suitable method for your project.
Traditional Etching
Traditional etching involves applying a photoresist layer to the copper-clad board, exposing it to UV light through a photomask, and then etching away the unwanted copper using a chemical solution. This method is suitable for low-volume prototypes and can be done in-house with the right equipment.
CNC Milling
CNC milling uses a computer-controlled machine to route away the unwanted copper from the board, leaving behind the desired traces. This method is faster than traditional etching and allows for more precise control over the trace dimensions. CNC milling is ideal for rapid prototyping and low-volume production.
PCB Printing
PCB printing is an emerging technology that uses conductive ink to print the traces directly onto the substrate. This method is fast, cost-effective, and environmentally friendly. However, the availability of PCB printing services is currently limited, and the technology is still evolving.
Fabrication Technique | Advantages | Disadvantages |
---|---|---|
Traditional Etching | Low cost, suitable for low-volume prototypes | Time-consuming, requires chemicals |
CNC Milling | Fast, precise, ideal for rapid prototyping | Higher setup costs |
PCB Printing | Fast, cost-effective, eco-friendly | Limited availability, evolving technology |
Cost-Saving Strategies
When prototyping PCBs, it’s important to keep costs under control. Here are some strategies to help you save money without compromising on quality:
Batch Production
Ordering multiple PCBs in a single batch can significantly reduce the per-unit cost. Many PCB manufacturers offer discounts for higher quantities, so consider consolidating your designs or collaborating with others to take advantage of bulk pricing.
Panelization
Panelization involves combining multiple PCB designs onto a single panel for fabrication. This technique optimizes the use of materials and reduces the overall manufacturing cost. When panelizing your designs, consider the following:
- Ensure adequate spacing between individual PCBs
- Include tooling holes and breakaway tabs for easy separation
- Follow the manufacturer’s panelization guidelines
Open Source Design Tools
Using open-source PCB design software can save you money on expensive licenses. Some popular open-source options include:
- KiCad
- Eagle (limited free version)
- JUMP’z PCB Layout Calculator
- FreeCAD
These tools offer a wide range of features and are suitable for both beginners and experienced designers.
FAQ
Q1: What is the minimum feature size for low-cost PCB prototypes?
A1: The minimum feature size depends on the fabrication technique and the manufacturer’s capabilities. Typically, low-cost PCB prototypes can achieve a minimum trace width and spacing of around 6-8 mils (0.15-0.20 mm). However, it’s always best to consult with your chosen manufacturer for their specific design rules.
Q2: How long does it take to fabricate a PCB prototype?
A2: The fabrication time varies depending on the complexity of the design, the chosen fabrication technique, and the manufacturer’s workload. On average, low-cost PCB prototypes can be fabricated within 1-2 weeks. Some manufacturers offer expedited services for faster turnaround times, but this may incur additional costs.
Q3: Can I assemble my PCB prototype myself?
A3: Yes, you can assemble your PCB prototype yourself if you have the necessary skills, tools, and components. Hand soldering is a common method for assembling low-volume prototypes. However, if your design includes surface-mount components or requires precise placement, it may be more cost-effective and time-efficient to outsource the assembly to a professional service.
Q4: How can I test my PCB prototype?
A4: Testing your PCB prototype is crucial to ensure its functionality and identify any potential issues. Some common testing methods include:
- Visual inspection for manufacturing defects
- Continuity testing to verify proper connections
- Power-on testing to check for shorts and overcurrent conditions
- Functional testing to validate the circuit’s performance
It’s important to have a comprehensive test plan and the necessary equipment, such as multimeters, oscilloscopes, and logic analyzers, to thoroughly test your prototype.
Q5: What should I do if my PCB prototype doesn’t work as expected?
A5: If your PCB prototype fails to function as intended, don’t panic. Troubleshooting is an essential part of the prototyping process. Start by visually inspecting the board for any obvious defects or soldering issues. Then, systematically test the various sections of the circuit to isolate the problem. Use schematic diagrams and datasheets to verify component values and connections. If necessary, consult with experienced engineers or online communities for guidance and support.
Conclusion
Low-cost 1 to 4 layer PCB prototypes play a vital role in the electronics design process, allowing engineers and hobbyists to test and validate their ideas before committing to large-scale production. By understanding PCB layers, design considerations, fabrication techniques, and cost-saving strategies, you can create high-quality prototypes while keeping costs under control.
Remember to choose the appropriate layer configuration for your project, follow best practices for component placement and trace routing, and consider design for manufacturing principles. Explore different fabrication techniques and take advantage of cost-saving strategies like batch production and panelization.
With the right knowledge and tools, you can bring your electronic ideas to life and create innovative solutions that make a difference in the world. Happy prototyping!
0 Comments