What is a Flex PCB?
A Flex PCB, also known as a flexible printed circuit board, is a type of PCB that consists of a thin, flexible substrate made of materials such as polyimide or polyester. Unlike traditional rigid PCBs, Flex PCBs can bend, twist, and conform to various shapes and sizes, making them ideal for applications where space is limited or where the device requires movement or flexibility.
Flex PCBs are composed of several layers, including:
- Flexible substrate (e.g., polyimide or polyester)
- Copper traces for electrical connectivity
- Cover layers for protection and insulation
- Adhesive layers for bonding the different layers together
The number of layers in a Flex PCB can vary depending on the complexity of the design and the specific requirements of the application.
Benefits of Flex PCBs
Flex PCBs offer numerous advantages over traditional rigid PCBs, making them an attractive choice for many applications. Some of the key benefits include:
-
Flexibility and Durability: Flex PCBs can withstand repeated bending and flexing without compromising their electrical performance or structural integrity. This makes them ideal for applications where the device is subject to movement, vibration, or shock.
-
Space Savings: By eliminating the need for bulky connectors and wires, Flex PCBs allow for more compact and streamlined designs. This is particularly important in applications where space is at a premium, such as wearable devices, medical implants, and aerospace systems.
-
Weight Reduction: Flex PCBs are significantly lighter than their rigid counterparts, which is crucial in weight-sensitive applications such as aerospace and automotive industries.
-
Improved Signal Integrity: The shorter interconnections and reduced parasitic capacitance and inductance in Flex PCBs result in improved signal integrity and reduced electromagnetic interference (EMI).
-
Enhanced Reliability: Flex PCBs eliminate the need for connectors and solder joints, which are common points of failure in electronic assemblies. This leads to increased reliability and longer product lifetimes.
-
Design Freedom: The flexibility and conformability of Flex PCBs allow for greater design freedom, enabling engineers to create innovative and complex shapes that would be challenging or impossible with rigid PCBs.
Applications of Flex PCBs
Flex PCBs find applications in a wide range of industries and products. Some of the most common applications include:
-
Consumer Electronics: Flex PCBs are extensively used in smartphones, tablets, laptops, and wearable devices, where their flexibility and space-saving properties are highly valued.
-
Medical Devices: Flex PCBs are employed in various medical devices, such as hearing aids, pacemakers, and imaging equipment, where their reliability and ability to conform to the human body are essential.
-
Automotive Electronics: In the automotive industry, Flex PCBs are used in applications such as dashboard displays, infotainment systems, and advanced driver assistance systems (ADAS).
-
Aerospace and Defense: Flex PCBs are utilized in aerospace and defense applications, including avionics, satellites, and military communication systems, where their lightweight and high-reliability properties are critical.
-
Industrial Equipment: Flex PCBs are found in various industrial applications, such as robotics, automation systems, and process control equipment, where their flexibility and durability are advantageous.
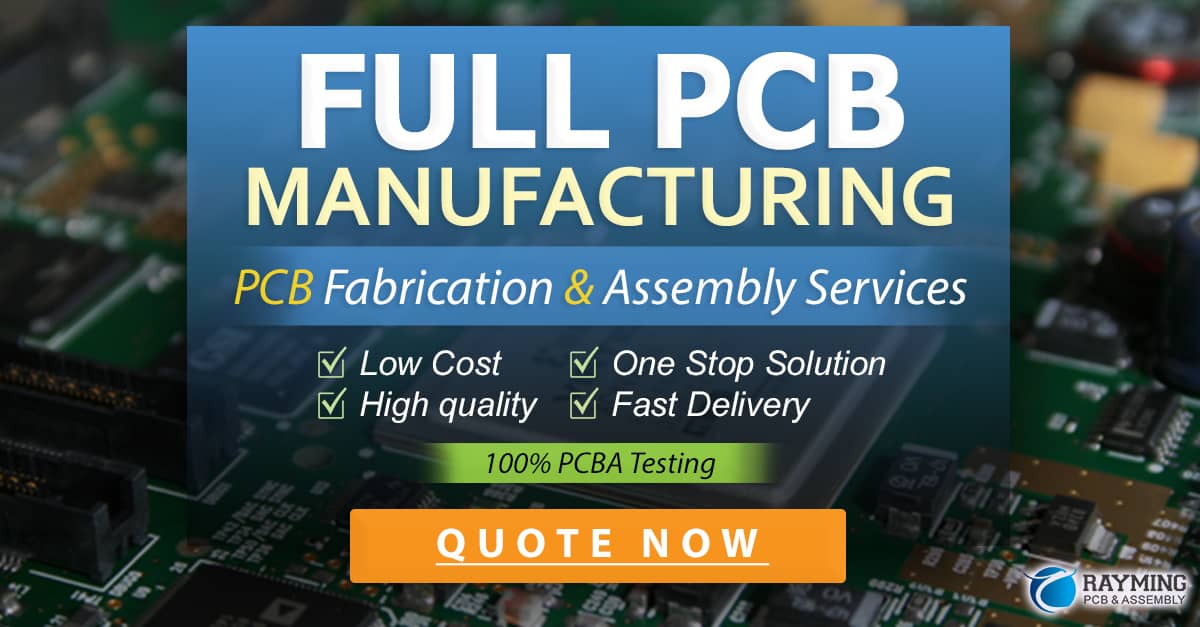
Flex PCB Manufacturing Process
The manufacturing process for Flex PCBs is similar to that of rigid PCBs, with a few key differences to accommodate the flexible nature of the substrate. The main steps in the Flex PCB manufacturing process are as follows:
-
Design and Artwork Creation: The first step is to create the PCB design using specialized CAD software. The artwork, which includes the copper traces, solder mask, and silkscreen layers, is generated based on the design.
-
Substrate Preparation: The flexible substrate, typically polyimide or polyester, is cleaned and treated to ensure proper adhesion of the copper layer.
-
Copper Lamination: A thin layer of copper is laminated onto the flexible substrate using heat and pressure. The copper layer can be applied to one or both sides of the substrate, depending on the design requirements.
-
Photoresist Application: A photoresist layer is applied to the copper surface and exposed to UV light through a photomask containing the PCB Artwork. This process selectively hardens the photoresist in the desired pattern.
-
Etching: The exposed copper is etched away using a chemical solution, leaving behind the desired copper traces.
-
Photoresist Removal: The remaining photoresist is stripped away, revealing the copper traces.
-
Coverlay Lamination: A protective coverlay is laminated onto the PCB to insulate and protect the copper traces.
-
Drilling and Cutting: Holes are drilled through the PCB for component mounting and interconnections. The PCB is then cut to its final shape using a laser or mechanical cutter.
-
Surface Finishing: A surface finish, such as HASL (Hot Air Solder Leveling), ENIG (Electroless Nickel Immersion Gold), or OSP (Organic Solderability Preservative), is applied to the exposed copper to improve solderability and protect against oxidation.
-
Quality Control: The finished Flex PCBs undergo rigorous quality control inspections, including visual inspections, electrical testing, and functional testing, to ensure they meet the required specifications.
Flex PCB Design Considerations
Designing a Flex PCB requires careful consideration of several factors to ensure optimal performance and reliability. Some key design considerations include:
-
Bend Radius: The minimum bend radius of a Flex PCB is determined by the thickness and material properties of the substrate and copper layers. It is essential to design the PCB to withstand the expected bending and flexing without causing damage or deterioration of the electrical performance.
-
Copper Thickness: The thickness of the copper traces on a Flex PCB must be carefully selected to balance electrical performance, mechanical stability, and flexibility. Thinner copper layers are more flexible but may have higher resistance, while thicker layers provide better electrical performance but reduced flexibility.
-
Adhesive Selection: The choice of adhesive for bonding the layers of a Flex PCB is critical for ensuring reliable performance under the expected environmental conditions, such as temperature, humidity, and chemical exposure.
-
Strain Relief: Proper strain relief design is essential to prevent damage to the Flex PCB at the transition points between flexible and rigid sections. This can be achieved through the use of stiffeners, anchors, or other reinforcement techniques.
-
Shielding: In applications where EMI is a concern, shielding layers may be incorporated into the Flex PCB design to minimize interference and ensure signal integrity.
-
Manufacturing Considerations: The design of a Flex PCB must take into account the capabilities and limitations of the manufacturing process to ensure that the PCB can be reliably and cost-effectively produced.
Flex PCB Testing and Reliability
To ensure the reliability and performance of Flex PCBs, various testing methods are employed throughout the manufacturing process and during the product’s lifecycle. Some common testing methods include:
-
Continuity Testing: This test verifies that all the electrical connections on the PCB are intact and that there are no open or short circuits.
-
Insulation Resistance Testing: This test measures the resistance between adjacent conductors to ensure adequate insulation and prevent signal leakage.
-
Flexibility Testing: Flex PCBs are subjected to repeated bending and flexing to ensure they can withstand the expected mechanical stresses without degradation of electrical performance or structural integrity.
-
Environmental Testing: Flex PCBs are exposed to various environmental conditions, such as temperature cycling, humidity, and vibration, to evaluate their performance and reliability under real-world conditions.
-
Accelerated Life Testing: This testing method involves subjecting the Flex PCB to elevated stress levels to simulate long-term use and identify potential failure modes and mechanisms.
By conducting thorough testing and reliability assessments, manufacturers can ensure that their Flex PCBs meet the required quality and performance standards and can withstand the rigors of their intended applications.
Choosing a Flex PCB Manufacturer
Selecting the right Flex PCB manufacturer is crucial for ensuring the success of your project. When evaluating potential manufacturers, consider the following factors:
-
Experience and Expertise: Look for a manufacturer with extensive experience in producing Flex PCBs and a proven track record of success in your specific industry or application.
-
Manufacturing Capabilities: Ensure that the manufacturer has the necessary equipment, processes, and expertise to produce Flex PCBs that meet your design requirements and quality standards.
-
Quality Management: Choose a manufacturer with a robust quality management system in place, preferably one that is certified to industry standards such as ISO 9001 or AS9100.
-
Customer Support: Select a manufacturer that offers responsive and knowledgeable customer support, from the initial design phase through production and post-sales support.
-
Cost and Lead Time: Consider the manufacturer’s pricing and lead times to ensure they align with your budget and project timeline. However, be cautious of sacrificing quality for lower costs or faster turnaround times.
-
Intellectual Property Protection: If your Flex PCB design contains proprietary or sensitive information, choose a manufacturer with strong intellectual property protection measures in place.
By carefully evaluating potential Flex PCB Manufacturers and selecting one that meets your specific needs and requirements, you can ensure a successful partnership and a high-quality end product.
Future Trends in Flex PCB Technology
As technology continues to advance and new applications emerge, the Flex PCB industry is poised for significant growth and innovation. Some of the key trends shaping the future of Flex PCB technology include:
-
Miniaturization: The demand for smaller, lighter, and more compact electronic devices will drive the development of even thinner and more flexible PCBs, enabling the creation of increasingly miniaturized and wearable devices.
-
High-Speed Applications: As data rates continue to increase, Flex PCBs will play a critical role in enabling high-speed data transmission in applications such as 5G networks, high-performance computing, and advanced automotive systems.
-
Advanced Materials: The development of new substrate materials, such as liquid crystal polymers (LCPs) and thermoplastic polyurethanes (TPUs), will offer enhanced properties, including higher temperature resistance, improved dimensional stability, and better chemical resistance.
-
Embedded Components: The integration of passive and active components directly into the Flex PCB substrate will enable further miniaturization and improved signal integrity, leading to more compact and efficient electronic assemblies.
-
Additive Manufacturing: The adoption of additive manufacturing techniques, such as 3D printing, for Flex PCB Fabrication will enable faster prototyping, greater design freedom, and the ability to create complex, three-dimensional PCB structures.
-
Sustainable Manufacturing: As environmental concerns continue to grow, the Flex PCB industry will focus on developing more sustainable manufacturing processes, including the use of eco-friendly materials, reduced waste generation, and improved energy efficiency.
By staying at the forefront of these trends and continuously innovating, Flex PCB manufacturers will be well-positioned to meet the evolving needs of their customers and drive the future of the electronics industry.
Frequently Asked Questions (FAQ)
-
What is the difference between a Flex PCB and a rigid PCB?
A Flex PCB is made from a thin, flexible substrate material that allows it to bend and conform to various shapes, while a rigid PCB is made from a solid, non-flexible substrate. Flex PCBs offer advantages such as improved durability, space savings, and design freedom compared to rigid PCBs. -
Can Flex PCBs be used in high-temperature applications?
Yes, Flex PCBs can be designed to withstand high temperatures by using appropriate substrate materials, such as polyimide, which can maintain its properties at temperatures up to 260°C. However, the specific temperature range will depend on the materials and construction of the Flex PCB. -
How do I choose the right Flex PCB manufacturer for my project?
When selecting a Flex PCB manufacturer, consider factors such as their experience and expertise in your specific industry or application, manufacturing capabilities, quality management systems, customer support, cost and lead time, and intellectual property protection measures. It is essential to choose a manufacturer that can meet your specific needs and requirements. -
What are the common applications for Flex PCBs?
Flex PCBs are used in a wide range of applications, including consumer electronics (smartphones, wearables), medical devices (hearing aids, pacemakers), automotive electronics (dashboard displays, ADAS), aerospace and defense (avionics, satellites), and industrial equipment (robotics, automation systems). -
How can I ensure the reliability of my Flex PCB design?
To ensure the reliability of your Flex PCB design, consider factors such as the minimum bend radius, copper thickness, adhesive selection, strain relief, shielding, and manufacturing considerations. Conduct thorough testing and reliability assessments, including continuity testing, insulation resistance testing, flexibility testing, environmental testing, and accelerated life testing to validate the performance and durability of your Flex PCB.
Characteristic | Flex PCB | Rigid PCB |
---|---|---|
Substrate Material | Thin, flexible materials (e.g., polyimide, polyester) | Solid, non-flexible materials (e.g., FR-4, aluminum) |
Flexibility | Can bend and conform to various shapes | Cannot bend or flex |
Durability | High, can withstand repeated bending and flexing | Limited, prone to cracking or breaking under stress |
Space Savings | Significant, enables more compact designs | Limited, requires connectors and wiring |
Weight | Low, ideal for weight-sensitive applications | Higher than Flex PCBs |
Design Freedom | High, allows for complex and innovative shapes | Limited by the rigidity of the substrate |
Common Applications | Consumer electronics, medical devices, automotive, aerospace | High-power, high-reliability, and cost-sensitive applications |
In conclusion, Flex PCBs have emerged as a critical technology in the electronics industry, offering numerous benefits, including flexibility, durability, space savings, and design freedom. As technology continues to advance and new applications emerge, the demand for Flex PCBs is expected to grow significantly. By understanding the manufacturing process, design considerations, testing methods, and future trends, engineers and manufacturers can harness the full potential of Flex PCBs to create innovative, reliable, and high-performance electronic devices that meet the evolving needs of their customers.
0 Comments