Introduction to EMS PCBs
Printed circuit boards (PCBs) are essential components of most modern electronic devices. PCBs provide the physical structure and electrical connections between the various components that make up an electronic system. As products become more complex, PCB design and manufacturing have become highly specialized skills. This has led many companies to outsource PCB production to external suppliers known as electronics manufacturing services (EMS).
EMS providers offer end-to-end PCB design, fabrication, assembly, and testing services catered to the unique requirements of each customer. Working with an EMS can help companies accelerate time-to-market for new products while reducing costs and manufacturing risks. This guide provides an in-depth look at EMS PCB solutions and how they benefit electronic product development.
Overview of the EMS PCB Process
The EMS PCB production process involves several key steps:
PCB Design
The PCB design process defines the layout of copper traces, component footprints, vias, and other features that will be fabricated on the board. EMS providers offer PCB design services covering:
- Schematic capture
- Board layout
- Signal integrity analysis
- DFM analysis to optimize manufacturability
Customers can provide initial design requirements and work closely with the EMS designer or submit a completed design for fabrication.
Prototype Production
Once the PCB design is finalized, the EMS will build prototypes for design verification and testing. Prototyping often involves producing small batches of boards with various layer counts and fabrication tolerances.
Volume PCB Fabrication
This involves producing production quantities of the PCB, from tens to thousands of boards. The EMS has fabrication facilities with advanced manufacturing capabilities tailored to high-volume PCB production.
PCB Assembly
The EMS will then assemble the components and devices onto the fabricated PCBs. This includes automated SMT assembly and manual insertion of through-hole parts.
Testing and Quality Control
PCBs from the EMS undergo electrical testing, optical inspection, and quality audits throughout the assembly process. This helps ensure each completed board meets the product’s quality and reliability requirements.
Logistics and Fulfillment
As a final step, the EMS can provide global order fulfillment solutions to deliver customized PCB assemblies wherever and whenever the customer needs them.
Key Benefits of Using an EMS for PCBs
EMS providers offer many advantages over relying on in-house PCB production:
Reduced Time-to-Market
EMS suppliers have the engineering resources and manufacturing capacity to accelerate PCB fabrication and assembly. This allows customers to launch products faster.
Flexible Production Scalability
Customers can start with low-volume prototyping and seamlessly scale up to high-volume production as needed. The EMS manages production capacity behind the scenes.
Cost Savings
Economies of scale allow an EMS to produce PCBs at a lower unit cost compared to a smaller in-house operation. Outsourcing also converts fixed PCB production costs into a variable cost model.
Improved Quality
Experience producing millions of PCBs results in robust quality control and process optimization that is difficult to match in-house. Customers benefit from extremely low defect rates.
Risk Reduction
Relying on an expert EMS reduces technical risks across PCB design, fabrication, and assembly processes. The EMS also handles supply chain complexities related to sourcing components.
Focus on Core Competencies
Outsourcing PCB production to an EMS allows customers to focus their internal engineering and manufacturing resources on core product development strengths.
Factors to Consider When Selecting an EMS Provider
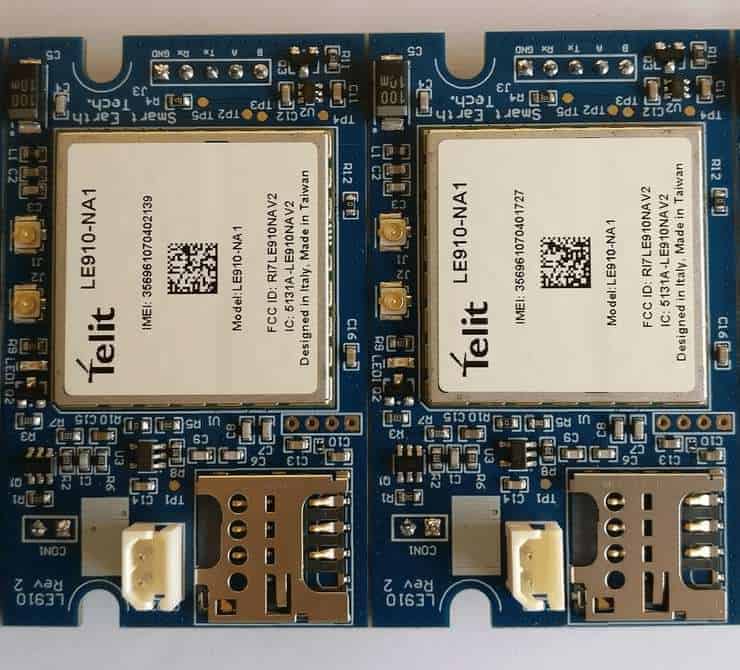
Choosing the right EMS involves evaluating several aspects of their capabilities and approach:
Geographic Location
- Proximity to the customer’s facilities for shorter product development cycles and supply chain response times. Global geographic coverage also supports international customers and regional production needs.
Engineering and Design Experience
- Expertise with various PCB technologies, component packages, high-speed signaling, DFM, testability, etc. The ability to support innovative and challenging customer design requirements.
Manufacturing Capabilities
- Range of available PCB fabrication processes such as layer count, line width/spacing, materials, and special treatments. Support for high-mix and quick-turn requirements.
Assembly Options
- SMT, thru-hole, advanced packaging, automation, and other assembly technologies. Ability to work with various component types and packages.
Quality Systems
- Quality control procedures, testing capabilities, process controls and optimization, management standards. Consistent process capability and extremely low defect rates.
Customer Service
- Responsiveness to requests, design support, supply chain transparency, documentation, ease of doing business. Strong customer focus.
Cost Structure
- Competitive pricing, minimum order quantities, low prototyping costs, and inventory management programs. Flexibility to meet unique customer cost requirements.
Comparison of Small vs. Large EMS Providers
There is a wide range of EMS companies to choose from. Here is an overview comparing large global EMS companies versus smaller regional providers:
EMS Company Size | Small | Large |
---|---|---|
Geographic Presence | Local/Regional | Global |
Revenue and Capacity | <$100M revenue<br>1-2 facilities | >$1B revenue<br>10+ facilities worldwide |
Manufacturing Technology | Mainstream | Advanced |
Engineering Capabilities | Basic design support | Hundreds of engineers, extensive expertise |
Cost Structure | Potentially higher piece cost | Lower piece cost at high volumes |
Quality Systems | Good | Robust, optimized over decades |
Customer Type | Startups, small/medium companies | Large enterprises |
Responsiveness | Very fast | Medium, some bureaucracy |
Trends Shaping the EMS Market
Several factors are influencing the continued growth and evolution of EMS solutions for PCB production:
- Miniaturization – Devices become smaller and use advanced packaging. EMS must support ultra-fine line width PCBs.
- Industry 4.0 – Data-driven smart manufacturing. EMS implements automation, IoT sensors, analytics, and digital twin technology.
- Supply Chain Management – Geopolitical factors make supply chains more complex. EMS leverages global sourcing networks.
- Sustainability – Organizations demand greener production. EMS aims for carbon neutrality and environmental responsibility.
- Customization – Customers need low-volume, high-mix production. EMS can economically address small to mid-size production runs.
These trends will drive ongoing innovation as EMS providers deliver next-generation PCB solutions tailored to emerging customer needs.
Conclusion
EMS partners provide invaluable PCB design, fabrication, assembly, and testing capabilities that enable companies to successfully develop and manufacture advanced electronic products. Selecting an EMS involves weighing factors such as technical expertise, manufacturing capacity, quality, cost, and customer service. Both large and small EMS providers have unique advantages depending on a customer’s specific requirements and constraints. Continued evolution of the EMS industry will open up new possibilities to accelerate innovation as electronics become ever more essential across countless industries.
Frequently Asked Questions
What are the key differences when comparing PCB manufacturers vs EMS providers?
PCB manufacturers focus exclusively on fabrication of bare printed circuit boards. They provide engineering support for PCB layout/design and optimize their factories for high-volume PCB production. EMS providers offer end-to-end services spanning initial design through testing completed PCB assemblies. This includes sourcing components, SMT assembly, post-assembly testing, and global order fulfillment.
How can EMS improve PCB quality and reliability?
EMS providers accumulate vast experience across thousands of PCB fabrication and assembly projects. They implement rigorous quality systems and leverage Six Sigma, 5S, and other process optimization methods. Stringent testing and inspection regimes improve reliability. These best practices are challenging to match with limited in-house production.
Does outsourcing PCB production result in IP risks?
Reputable EMS providers implement strong IP protection standards within their design, production, and order fulfillment operations. Customers own their PCB data. Manufacturing agreements can include non-disclosure clauses and other IP protections.
Can EMS scale to very high production volumes?
The largest EMS companies have dozens of factories worldwide and can produce millions of PCB assemblies per month. They also have established supply chain networks to procure components at massive scale. EMS provides the production capacity and logistics infrastructure to scale to extremely high PCB volumes.
How does EMS pricing compare to in-house PCB production?
EMS leverages economies of scale and optimized processes to achieve very competitive PCB fabrication and assembly costs, especially at mid to high volumes. Lower capital costs, less waste, and shared overhead vs. in-house production also provide cost advantages. The EMS “pay-as-you-go” model converts high fixed costs into a variable cost structure.
0 Comments