Introduction to PCBs
A printed circuit board (PCB) is the foundation of all modern electronics. It is a board made of fiberglass or other composite materials that provides mechanical support and electrical connections between electronic components using conductive copper tracks. PCBs allow complex circuit designs to be laid out in a compact area and mass produced.
Some key advantages of using PCBs:
- Durability – PCBs are very durable and can withstand shaking, vibrations, heat and other environmental stresses. The fiberglass material is designed for longevity.
- Compact design – PCBs allow for much denser circuit designs by allowing traces to pass both above and below the board surface. This is not possible with hand soldering.
- Ease of assembly – Components can be easily inserted and soldered to a PCB in an automated assembly process. This also improves reliability over hand-wiring.
- Cost effectiveness – PCBs enable mass production of electronic devices at a low cost per unit. The PCB fabrication process itself benefits from economies of scale.
- Testability – It is easier to test and identify faults in a PCB assembly compared to individual wired connections.
PCB Manufacturing Process
The PCB fabrication process can be complex, involving many steps to transform the original circuit design into a physical board. Here is an overview of the typical PCB manufacturing workflow:
1. Design
The electronics design process starts with concept diagrams and schematics to plan out the circuit and components required. PCB design software is then used to precisely layout the traces, pads, vias and other features based on the schematic. Some key outputs of PCB design are:
- Gerber files – Standard format files containing circuit board layers, drill location data, etc.
- Bill of Materials (BOM) – List of all components required for the board.
- Assembly drawings – Files to assist PCB assembly such as component layout diagrams.
2. Fabrication
The PCB fabrication stage involves taking the design files and physically manufacturing the board. Some key steps are:
- CAM – Computer Aided Manufacturing data is generated from the Gerber files. This ensures the design meets manufacturing requirements.
- Panelization – To optimize fabrication, PCB designs are arranged onto large panels that hold multiple boards.
- Copper patterning – The conductive copper layer on the PCB is etched away to leave only the required circuit traces.
- Hole drilling – Holes are precisely drilled for mounting components. Plated through-holes make connections between layers.
- Solder mask – A lacquer layer is applied to protect copper traces and prevent solder bridges.
- Silkscreen – Component labels, board outlines and markings are screen printed.
- Testing – The fabricated boards are electrically tested for opens, shorts and function.
3. Assembly
In the assembly stage, electronic components are mounted and soldered onto the fabricated PCB. Some key steps are:
- Population – Components are inserted onto the board by automatic pick-and-place machines or human assemblers.
- Soldering – The board goes through a reflow oven to melt solder and permanently attach components.
- Cleaning – Excess flux is washed off to prevent corrosion and improve appearance.
- Testing – Assembled boards are powered up and tested for correct function. Failed boards are reworked or discarded.
4. Final Testing and Shipment
Before delivery to the customer, finished boards go through final quality checks:
- Visual inspection – Boards are examined for flaws in assembly like missing components or poor solder joints.
- Functional testing – Detailed verification of board function based on its specifications and performance requirements.
- Burn-in testing – Running assembled boards at elevated voltages and temperatures to check for early failures.
- Packaging – Boards are packaged with electro-static prevention to avoid chip damage during shipment.
Factors to Consider When Choosing a PCB Manufacturer
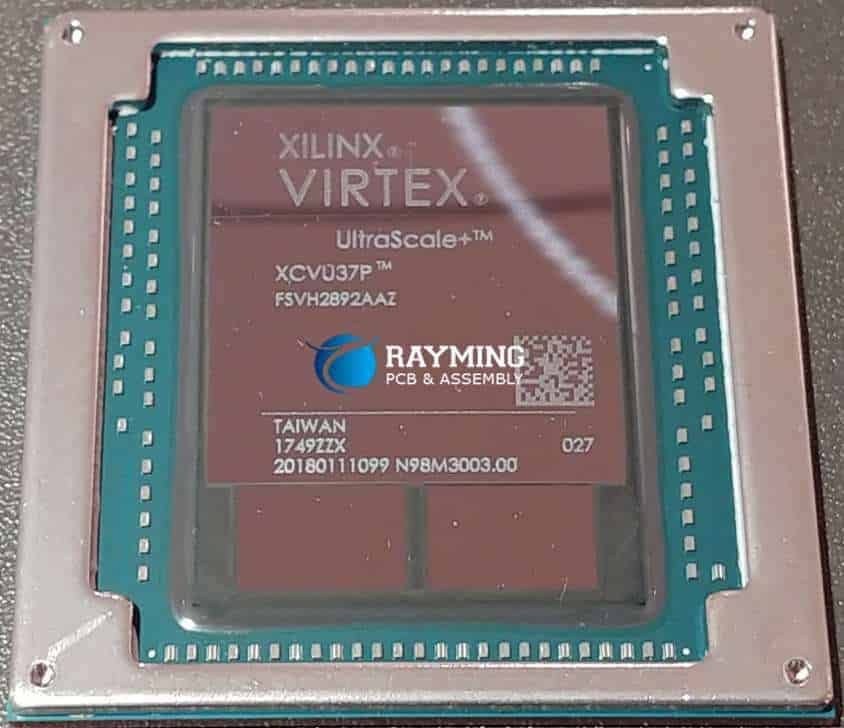
Choosing the right PCB production partner is crucial. Here are some key factors to evaluate:
Capabilities
- Can they fabricate the board layers and complexity your design requires? More layers accommodates more complex circuity.
- Do they support the fabrication specs needed – line width/space, hole size, corner radius, etc.?
- What assembly services do they offer? e.g. only SMT, thru-hole, or full assembly.
Quality
- How rigorous is their quality control and testing at various stages?
- Do they have quality certifications like ISO 9001, IATF 16949, or ITAR?
- What tolerances, yields and defect rates do they guarantee?
Lead Time
- How fast can they fabricate and assemble the boards? Standard lead times range from 2 days to 4 weeks.
- For prototype runs, some offer expedited fabrication in 24-48 hours.
- For production runs, lead time depends on order size and current demand.
Cost
- Do they offer competitive pricing models for both prototypes and production runs?
- Are there discounts or reduced costs for higher order quantities?
- How are costs structured – one-time fees, recurring fees, etc.?
Customer Service
- How responsive are they to inquiries and requests? This gives a sense of their level of customer service.
- Do they have dedicated engineering support for design assistance?
- Is there transparency about order status and progress updates?
Popular Techniques to Optimize PCB Design
Well optimized PCB design practices can have significant benefits for the reliability, performance, cost and manufacturability of the final board. Here are some popular techniques:
Symmetry
Laying out components symmetrically on the board helps ensure even distribution of heat and prevents warping. This is especially important for larger boards.
Grids
Using alignment grids (for traces, pads, etc.) makes layout more organized and routing traces easier. Grid sizes are typically 0.1inch or 2.54mm.
Autorouting
Autorouters quickly generate trace connections based on defined rules. This automates much of the complex routing work.
Planes
Using large copper regions or planes on inner layers provides stable voltage references. This helps reduce noise and EMI effects.
Heat Dissipation
Strategically place heat generating components so their heat can dissipate efficiently out to the edges. Avoid placing them in concentrated hotspots.
Test Points
Include test point pads connected to important nets to make debugging and testing easier after assembly.
Component Orientation
Orient polarized components like diodes, ICs consistently to avoid assembly mixups. Follow manufacturer recommended orientations.
Trace Width
Use wider traces for high current paths to reduce resistance and avoid overheating. Narrow traces work for low current signal routing.
Mixed Signal
Keep analog and digital sections separated with isolation gaps on the PCB to prevent noise coupling.
Edges and Corners
Keep high speed traces away from the PCB edges and corners. These are prone to EMI radiation.
Examples of Innovative PCB Designs
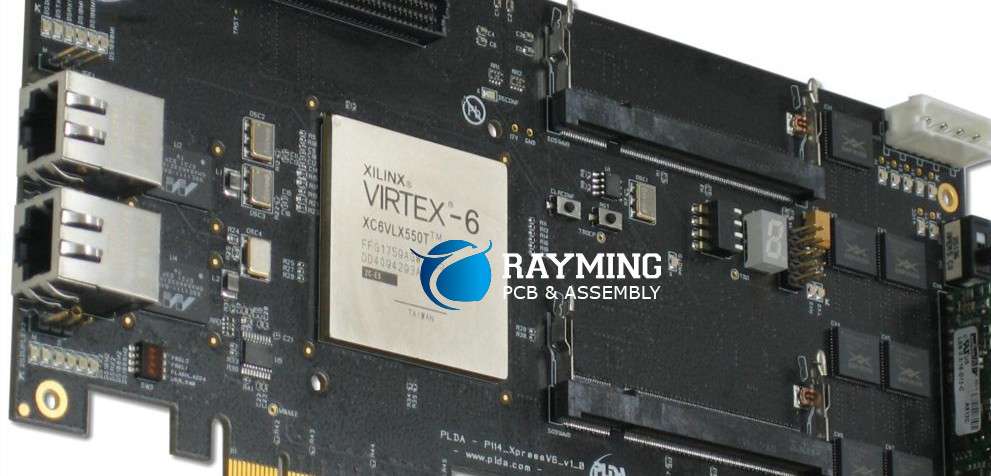
Here are some examples of novel and complex PCB implementations that stretch the boundaries of conventional board design:
Rigid-Flex
These have both rigid sections and flexible circuits allowing the PCB to flex and bend. Often used when the board must fit a curved surface like a wearable device.
Benefits | Challenges |
---|---|
Conforms to different geometries | Complex modeling of flex radius |
Allows movement between rigid areas | Specialized assembly fixtures needed |
Very compact 3D layouts possible | Higher cost than standard PCBs |
Metal Core (MC-PCB)
A thick metal layer like aluminum or copper is used as the core instead of FR4 fiberglass. The metal core acts as a heatspreader keeping components cool.
Benefits | Challenges |
---|---|
Improved thermal performance | Higher material cost |
Ideal for LED lighting | Metal core is electrically live |
Components can run at higher power | Need insulation layers around core |
High Frequency
Boards with working frequencies above 3GHz, often used in radar, communications and satellite systems.
Benefits | Challenges |
---|---|
Support microwave band applications | Much tighter constraints on trace dimensions and spacing |
Direct integration of RF systems | Absorptive materials required to dampen standing waves |
Higher DATA rates possible | Tougher requirements on dielectric consistency |
Stretchable Circuits
Flexible PCBs fabricated on elastic polymers that can stretch and compress like rubber. Used in wearable devices.
Benefits | Challenges |
---|---|
Can accommodate large physical deformations | Stretchable conductors need to handle high strain |
Used in skin-tight wearables | Components also need to flex without damage |
Maintains electrical connectivity when stretched | Specialized conductive and solder-less assembly |
Key Considerations for PCB Component Selection
Choosing suitable electronic components is an integral part of designing a functioning PCB assembly. Here are some key considerations for selection:
Function
- Components must provide the desired functionality – amplification, voltage regulation, data storage, user interfaces etc.
- Consider required specifications – operating frequency range, power ratings, output drive strength, logic voltage levels etc.
Dimensions
- Components must physically fit on the board layout.
- Check footprint dimensions and clearances.
- Height restrictions might apply for tightly stacked boards.
Pricing
- Balance desired component performance with its cost.
- Certain operating conditions may require more expensive components rated for higher temperature, voltage, frequency etc.
Packaging
- Components must be available in PCB-mount packaging – SMT, through-hole, BGA etc. Some are only available in wired packages.
- Ensure the packaging type is compatible with assembly processes to be used – reflow soldering, wave soldering etc.
Reliability
- Component should meet the target product lifetime with an adequately low failure rate.
- Consider replacement and repair costs if component has shorter lifetime.
Availability
- Check that the component is in volume production and not end-of-life.
- Assess expected lead times and purchase volumes.
Frequently Asked Questions
Q1: What is the difference between a single-sided, double-sided and multilayer PCB?
A1: The main differences are:
- Single-sided – Conductive copper tracks are on one side of the board only. Components are mounted on the same side. Cheapest option.
- Double-sided – Has copper tracks on both sides allowing more complex interconnections. Through-plated holes connect the two layers. Components can be mounted on both sides.
- Multilayer – Constructed from alternating copper and insulating dielectric layers bonded together. Allows circuit density with up to 20-30 conductive layers. Best for complex, compact designs.
Q2: How are most PCBs assembled today – through hole or surface mount?
A2: Surface mount technology (SMT) dominates modern PCB assembly. SMT components have solder pads rather than leads and sit directly on the board surface. This allows extreme miniaturization and component density compared to through hole mounting. However, connectors, large transformers and some other components may still use through hole packaging.
Q3: What are some signs of a poor quality PCB?
A3: Some signs of low quality PCBs are:
- Components lifted off or tombstoned after soldering due to poor wetting
- Short circuits or open circuits in the traces visible under magnification
- Cracked laminate or traces, often stemming from drill holes
- Overetched traces with reduced widths compared to design
- Acidic residue remaining after etching causing corrosion over time
- Plating voids in barrels of plated through holes limiting conductivity
- Warped boards that don’t sit flush against components
Q4: How are most PCBs tested?
A4: Common testing methods include:
- Visual inspection – Checking board quality and assembly under magnification. Done throughout fabrication and assembly.
- Flying probe – Electrically probes test pads to verify connectivity between different nets on unassembled boards. Checks for shorts and opens.
- Boundary scan – Special integrated circuits on board let software confirm IC interconnectivity. Done after assembly.
- Functional testing – Running assembled boards with electrical stimuli to confirm operation matches specifications.
- Burn-in testing – Stress testing assembled boards at temperature and voltage extremes to force failures.
- X-ray – X-ray imaging used to inspect internal features like buried vias or layer alignment.
Q5: What file formats are typically used for PCB design and manufacturing?
A5: Common PCB file formats are:
- Gerber – Standard format for individual PCB layers, drill files, etc. Needed for board fabrication.
- ODB++ – Contains complete board design and metadata in a single file. Used to transfer from design to manufacturing.
- IPC-2581 – Open standard that combines PCB fabrication and assembly data. Supports PCB stackup, 3D models, BoM, etc.
- DXF – 2D vector image file. Often used for mechanical profiles, routing tabs, documentation.
- PDF – Widely used vector image format for printable documentation like assembly drawings.
- STEP – Contains 3D models and is used for sharing board outlines with mechanical CAD systems.
0 Comments