Introduction to PCBs
Printed Circuit Boards (PCBs) are the backbone of modern electronics. They are used in almost every electronic device, from smartphones and laptops to medical equipment and aerospace systems. PCBs provide a reliable and efficient way to connect electronic components and create complex circuits.
What is a PCB?
A PCB is a flat board made of insulating material, such as fiberglass or plastic, with conductive copper traces printed on its surface. These traces connect various electronic components, such as resistors, capacitors, and integrated circuits (ICs), to form a functional circuit. PCBs can be single-sided (with components on one side), double-sided (with components on both sides), or multi-layered (with traces and components on multiple layers).
Advantages of Using PCBs
PCBs offer several advantages over traditional point-to-point wiring:
-
Compact size: PCBs allow for a much more compact design compared to point-to-point wiring, enabling the creation of smaller and more portable electronic devices.
-
Reliability: The copper traces on a PCB are more reliable than wire connections, reducing the risk of short circuits and loose connections.
-
Efficiency: PCBs streamline the manufacturing process, making it easier to mass-produce electronic devices with consistent quality.
-
Cost-effective: Once the initial design is complete, PCBs can be manufactured in large quantities at a relatively low cost per unit.
PCB Design Process
The PCB design process involves several steps, from concept to final production. Here’s a brief overview of the main stages:
Schematic Design
The first step in creating a PCB is to design the schematic. This is a graphical representation of the electronic circuit, showing all the components and their interconnections. The schematic is created using Electronic Design Automation (EDA) software, such as Altium Designer, Eagle, or KiCad.
PCB Layout
Once the schematic is complete, the next step is to create the PCB layout. This involves arranging the components on the board and routing the copper traces to connect them according to the schematic. The layout must take into account various factors, such as component placement, trace width, and spacing, to ensure proper functionality and manufacturability.
Design Rule Check (DRC)
After the layout is complete, it’s essential to run a Design Rule Check (DRC). This automated process verifies that the PCB design meets the manufacturer’s specifications and industry standards, such as minimum trace width, spacing, and hole size. The DRC helps identify and correct any potential issues before the board is sent for fabrication.
Gerber File Generation
The final step in the PCB design process is to generate Gerber files. These are the industry-standard file format used by PCB Manufacturers to produce the physical board. Gerber files contain all the necessary information, such as the copper layer patterns, drill holes, and silkscreen markings, to accurately fabricate the PCB.
PCB Fabrication Process
Once the Gerber files are generated, they are sent to a PCB manufacturer for fabrication. The fabrication process involves several steps:
-
Copper Lamination: The raw PCB substrate is laminated with a thin layer of copper on one or both sides, depending on the design requirements.
-
Photoresist Application: A light-sensitive photoresist is applied to the copper layer(s).
-
Exposure and Development: The photoresist is exposed to UV light through a photomask, which contains the PCB layout pattern. The exposed areas of the photoresist are then removed using a developer solution, leaving the desired copper pattern exposed.
-
Etching: The exposed copper is etched away using a chemical solution, leaving only the desired copper traces on the board.
-
Drill Holes: Holes are drilled into the board to accommodate through-hole components and vias (connections between layers in multi-layer PCBs).
-
Solder Mask and Silkscreen: A protective solder mask is applied to the board, covering the copper traces but leaving the component pads exposed. A silkscreen layer is then added to provide text and symbols for component placement and identification.
-
Surface Finish: A surface finish, such as Hot Air Solder Leveling (HASL), Immersion Silver, or Gold Plating, is applied to the exposed copper pads to protect them from oxidation and enhance solderability.
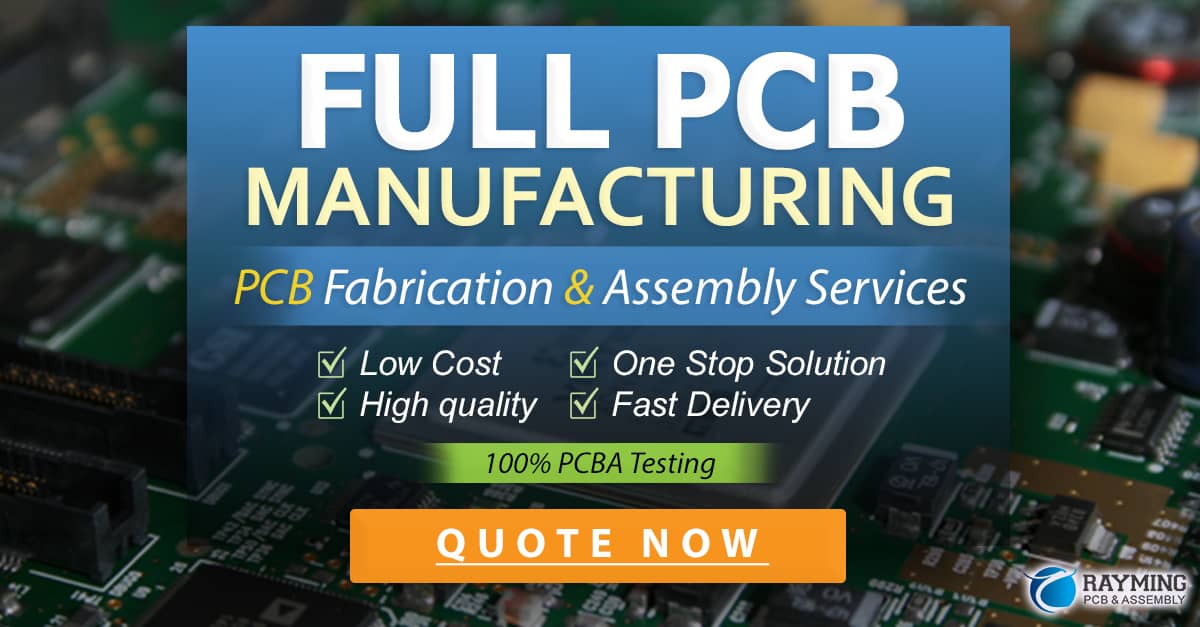
PCB Assembly
After the PCB is fabricated, the next step is to assemble the components onto the board. This can be done manually or using automated assembly processes, depending on the complexity of the design and the production volume.
Through-Hole Assembly
Through-hole components have long leads that are inserted into holes drilled in the PCB and soldered onto the opposite side. This assembly method is suitable for larger components and low-volume production, as it can be done manually using a soldering iron.
Surface Mount Assembly
Surface Mount Technology (SMT) involves placing components directly onto the surface of the PCB and soldering them in place. SMT components are smaller and have shorter leads or no leads at all, making them ideal for high-density designs and automated assembly processes.
SMT Assembly Process
The SMT assembly process typically involves the following steps:
-
Solder Paste Application: A solder paste, consisting of tiny solder particles suspended in a flux medium, is applied to the component pads on the PCB using a stencil or screen printing process.
-
Component Placement: SMT components are placed onto the solder paste using an automated pick-and-place machine or manually using tweezers for low-volume production.
-
Reflow Soldering: The PCB with the placed components is passed through a reflow oven, which heats the board to a specific temperature profile, melting the solder paste and forming a permanent electrical and mechanical connection between the components and the PCB.
-
Inspection and Testing: After the soldering process, the assembled PCB is inspected for any defects, such as bridging (unintended connections between pads), tombstoning (components standing on end), or insufficient solder. Automated Optical Inspection (AOI) systems are often used for this purpose. The board is then tested to ensure proper functionality.
PCB Testing and Validation
Once the PCB is assembled, it must undergo various tests and validation processes to ensure it functions as intended and meets the required specifications. Some common testing methods include:
-
In-Circuit Testing (ICT): This test involves using a bed-of-nails fixture to make electrical contact with specific points on the PCB and verify the presence and value of individual components, as well as the connectivity between them.
-
Flying Probe Testing: This is an alternative to ICT that uses movable probes to make electrical contact with the PCB, allowing for more flexible testing without the need for a custom fixture.
-
Functional Testing: This test involves applying input signals to the PCB and measuring the output to verify that the board performs its intended function according to the design specifications.
-
Boundary Scan Testing: This test, also known as JTAG testing, uses a built-in self-test capability in the integrated circuits to test the interconnections and functionality of the components on the PCB.
-
Environmental Testing: This test exposes the PCB to various environmental conditions, such as temperature extremes, humidity, and vibration, to ensure it can withstand the intended operating conditions.
PCB Prototyping
Before committing to a full production run, it’s often necessary to create a prototype PCB to validate the design and functionality. Prototyping allows for iterative design improvements and helps identify any issues early in the development process.
Prototyping Methods
There are several methods for creating PCB Prototypes, each with its own advantages and limitations:
-
Breadboarding: This is the simplest and quickest way to prototype a circuit. Components are plugged into a breadboard, which has a matrix of interconnected sockets, allowing for easy rearrangement and modification of the circuit. However, breadboards are not suitable for high-frequency or sensitive analog circuits due to the inherent capacitance and resistance of the interconnections.
-
Stripboard: Also known as Veroboard, this is a pre-made PCB with a grid of copper strips on one side and holes drilled at regular intervals. Components are soldered directly onto the stripboard, and the copper strips are cut as needed to create the desired connections. Stripboards are more robust than breadboards but still have limitations in terms of circuit density and signal integrity.
-
Perfboard: This is a blank PCB with a grid of holes drilled at regular intervals but no pre-made copper connections. Components are soldered onto the perfboard, and individual connections are made using wire jumpers. Perfboards offer more flexibility than stripboards but require more effort to create the interconnections.
-
Custom PCB Fabrication: For more complex designs or when a higher level of performance is required, custom PCB fabrication is the best option. This involves creating a PCB design using EDA software and sending the Gerber files to a PCB manufacturer for fabrication. Custom PCBs offer the highest level of design flexibility and signal integrity but are more expensive and time-consuming to produce than the other prototyping methods.
Rapid PCB Prototyping Services
For custom PCB prototyping, several online services offer rapid turnaround times and low-volume production. These services typically provide an online platform for uploading PCB design files, selecting the desired specifications (such as board size, layer count, and surface finish), and receiving a quote. Some popular rapid PCB prototyping services include:
- PCBWay
- JLCPCB
- OSH Park
- Seeed Studio
- PCBGOGO
These services often have a turnaround time of a few days to a week, depending on the complexity of the design and the selected options.
PCB Design Considerations
When designing a PCB, there are several key factors to consider to ensure optimal performance and manufacturability:
-
Component Selection and Placement: Choose components that meet the functional and environmental requirements of the design, and place them on the PCB in a way that minimizes signal interference and facilitates efficient routing.
-
Signal Integrity: Ensure that the PCB layout minimizes signal reflections, crosstalk, and electromagnetic interference (EMI) by using appropriate trace widths, spacings, and grounding techniques.
-
Power Management: Provide a stable and clean power supply to the components on the PCB by using appropriate power planes, decoupling capacitors, and voltage regulators.
-
Thermal Management: Ensure that the PCB can dissipate heat effectively to prevent component overheating and premature failure.
-
Manufacturing Considerations: Design the PCB with manufacturability in mind, adhering to the manufacturer’s design rules and guidelines for minimum trace widths, spacings, and drill sizes.
-
Cost Optimization: Consider the cost implications of the PCB design, such as the choice of materials, layer count, and surface finish, to ensure that the design is cost-effective for the intended production volume.
Frequently Asked Questions (FAQ)
1. What is the difference between a single-sided and a double-sided PCB?
A single-sided PCB has components and copper traces on only one side of the board, while a double-sided PCB has components and traces on both sides. Double-sided PCBs offer higher component density and more efficient routing but are more expensive to manufacture than single-sided PCBs.
2. What are vias, and why are they used in PCBs?
Vias are small holes drilled through a PCB that allow electrical connections between different layers of a multi-layer board. They are used to route signals between layers and to create ground and power connections. There are several types of vias, including through-hole, blind, and buried vias, each serving specific purposes in the PCB design.
3. What is the purpose of a solder mask on a PCB?
A solder mask is a protective layer applied to the copper traces on a PCB, leaving only the component pads exposed. The solder mask serves several purposes:
- It prevents solder bridges from forming between closely spaced pads during the soldering process.
- It protects the copper traces from oxidation and other environmental factors that can degrade the board’s performance over time.
- It provides electrical insulation between adjacent traces, reducing the risk of short circuits.
- It improves the aesthetic appearance of the PCB by providing a uniform color and texture to the board surface.
4. What is the difference between HASL and lead-free surface finishes?
Hot Air Solder Leveling (HASL) and lead-free surface finishes are two common types of surface treatments applied to the exposed copper pads on a PCB. HASL involves dipping the PCB in a molten solder bath and then using hot air to remove excess solder, creating a uniform solder coating on the pads. Lead-free surface finishes, such as Immersion Silver, Immersion Tin, and ENIG (Electroless Nickel Immersion Gold), are applied using chemical processes and do not contain lead, which is a hazardous substance.
Lead-free surface finishes are becoming increasingly popular due to environmental regulations and health concerns associated with lead. They offer several advantages over HASL, such as better planarity (flatness) of the pads, finer pitch capability, and improved shelf life. However, lead-free surface finishes are generally more expensive than HASL.
5. What is the role of a Bill of Materials (BOM) in PCB assembly?
A Bill of Materials (BOM) is a comprehensive list of all the components, parts, and materials required to assemble a PCB. The BOM typically includes the following information for each item:
- Reference designator (e.g., R1, C2, U3)
- Manufacturer part number
- Description
- Quantity
- Supplier information
- Unit cost
The BOM serves as a critical document in the PCB assembly process, enabling the procurement of the necessary components and ensuring that the correct parts are used during the assembly. It also helps in cost estimation, inventory management, and traceability of the assembled PCBs.
Conclusion
PCBs are an essential component of modern electronics, providing a reliable and efficient means of connecting and integrating various electronic components. The PCB design and fabrication process involves multiple stages, from schematic design and layout to prototyping and testing. Choosing the appropriate materials, components, and manufacturing processes is crucial for ensuring the optimal performance, reliability, and cost-effectiveness of the final product.
As electronic devices continue to become more complex and compact, advancements in PCB technology will play a key role in enabling the development of innovative and high-performance products across a wide range of industries.
Table: Common PCB Materials and Their Properties
Material | Dielectric Constant | Dissipation Factor | Thermal Conductivity (W/mK) | Tg (°C) | Applications |
---|---|---|---|---|---|
FR-4 | 4.3-4.8 | 0.02 | 0.3 | 130-140 | General-purpose, low-cost |
High Tg FR-4 | 4.3-4.8 | 0.02 | 0.3 | 170-180 | High-temperature, automotive, aerospace |
Polyimide | 3.4-3.5 | 0.002-0.003 | 0.35 | 250-260 | Flexible, high-temperature, aerospace |
PTFE (Teflon) | 2.1-2.3 | 0.0004-0.0009 | 0.25 | 327 | High-frequency, low-loss, microwave |
Rogers RO4003C | 3.38 | 0.0027 | 0.71 | >280 | High-frequency, aerospace, defense |
Isola IS410 | 3.8-3.9 | 0.014 | 0.43 | 200 | High-speed digital, automotive, telecom |
This table provides an overview of some common PCB substrate materials and their key properties, such as dielectric constant, dissipation factor, thermal conductivity, and glass transition temperature (Tg). These properties influence the electrical, thermal, and mechanical performance of the PCB. The choice of substrate material depends on the specific application requirements, such as frequency range, thermal management, and environmental conditions.
0 Comments