Introduction to PCB Development
Printed Circuit Boards (PCBs) have revolutionized the electronics industry since their inception in the early 20th century. PCBs are the backbone of modern electronic devices, providing a platform for interconnecting electronic components and enabling the creation of complex circuits. This article will delve into the development history of PCBs, exploring key milestones, technological advancements, and current trends shaping the future of PCB design and manufacturing.
Early History of PCB Development
The Advent of PCBs
The concept of PCBs can be traced back to the early 1900s when German inventor Albert Hanson filed a patent for a “printed wire” in 1903. However, it wasn’t until the 1930s that the first practical PCBs emerged. In 1936, Austrian engineer Paul Eisler developed a method for printing conductive traces on an insulating substrate, laying the foundation for modern PCBs.
World War II and PCB Adoption
The outbreak of World War II accelerated the development and adoption of PCBs. The demand for compact and reliable electronic systems in military applications, such as radar and communication equipment, drove the need for efficient circuit manufacturing techniques. PCBs offered a solution by providing a standardized and reproducible method for assembling electronic components.
Post-War Developments
After the war, PCB technology continued to evolve. In the 1950s, the introduction of through-hole technology allowed for the mounting of components on both sides of the board, increasing circuit density and functionality. The 1960s saw the development of multilayer PCBs, enabling the stacking of multiple conductive layers separated by insulating materials, further enhancing circuit complexity and miniaturization.
Advancements in PCB Manufacturing
Photo-Imaging and Etching Processes
The introduction of photo-imaging and etching processes in the 1960s revolutionized PCB manufacturing. This technique involved using photographic masks and light-sensitive resists to selectively expose and etch the conductive patterns on the PCB substrate. Photo-imaging enabled higher precision, finer feature sizes, and improved throughput compared to earlier manual methods.
Surface Mount Technology (SMT)
The 1980s marked a significant shift in PCB Assembly with the widespread adoption of Surface Mount Technology (SMT). SMT components were smaller and had leads that could be directly soldered onto the surface of the PCB, eliminating the need for through-hole mounting. SMT allowed for higher component density, improved reliability, and automated assembly processes, leading to more compact and cost-effective electronic devices.
Advancements in Materials and Substrates
Over the years, advancements in materials and substrates have played a crucial role in PCB development. The introduction of high-performance materials, such as polyimide and Teflon, enabled the fabrication of PCBs with enhanced thermal stability, chemical resistance, and electrical properties. These materials have been instrumental in meeting the demands of harsh operating environments and high-frequency applications.
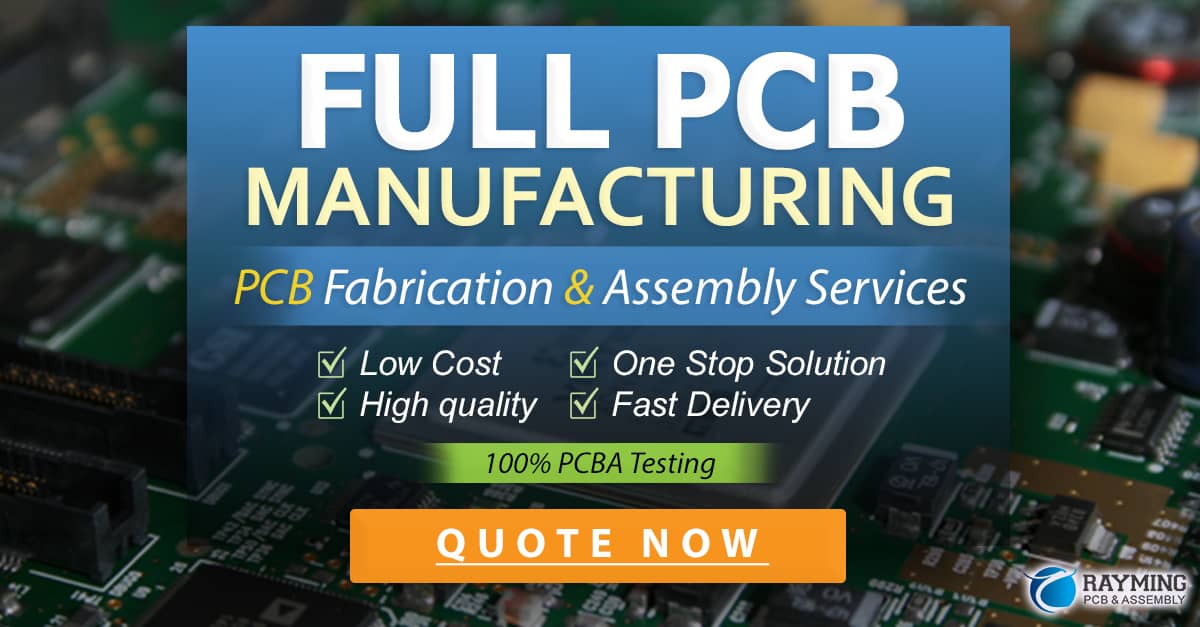
PCB Design and Simulation Tools
Computer-Aided Design (CAD) Software
The advent of Computer-Aided Design (CAD) software in the 1980s revolutionized PCB design processes. CAD tools, such as Altium Designer, OrCAD, and Eagle, provided engineers with powerful capabilities for schematic capture, layout design, and component placement. These tools streamlined the design process, reduced errors, and enabled the creation of complex multilayer PCBs with ease.
Simulation and Analysis Tools
As PCB designs became more intricate and high-speed, the need for simulation and analysis tools grew. Electronic Design Automation (EDA) software, such as Ansys and Cadence, offered advanced capabilities for signal integrity analysis, thermal modeling, and electromagnetic compatibility (EMC) simulation. These tools helped engineers optimize PCB designs, minimize signal integrity issues, and ensure reliable performance in real-world conditions.
Current Trends in PCB Development
High-Density Interconnect (HDI) PCBs
High-Density Interconnect (HDI) PCBs have emerged as a key trend in recent years. HDI PCBs feature finer trace widths, smaller via sizes, and higher layer counts compared to traditional PCBs. These advancements enable the integration of more components and functionality into smaller form factors, meeting the demands of miniaturization in consumer electronics, wearables, and IoT devices.
Flexible and Rigid-Flex PCBs
Flexible and Rigid-Flex PCBs have gained popularity due to their ability to conform to unique shapes and withstand mechanical stress. Flexible PCBs, made from thin, pliable materials, can be bent and folded to fit into compact spaces. Rigid-Flex PCBs combine the benefits of both rigid and flexible substrates, allowing for three-dimensional packaging and improved reliability in applications such as aerospace, medical devices, and automotive electronics.
Embedded Components and 3D PCBs
Embedded components and 3D PCBs represent a significant advancement in PCB technology. Embedded components, such as resistors, capacitors, and ICs, are directly integrated into the PCB substrate, reducing the need for surface-mounted components and saving valuable board space. 3D PCBs take this concept further by stacking and interconnecting multiple PCB Layers, creating three-dimensional structures that enable higher component density and shorter signal paths.
Sustainable and Eco-Friendly PCB Manufacturing
Environmental sustainability has become a pressing concern in the electronics industry. PCB Manufacturers are increasingly adopting eco-friendly practices and materials to minimize their environmental impact. Lead-free soldering, halogen-free substrates, and the use of biodegradable materials are some of the initiatives being implemented to promote sustainability in PCB manufacturing.
Future Outlook and Challenges
Miniaturization and High-Frequency Applications
The trend towards miniaturization and high-frequency applications will continue to drive PCB development in the future. As electronic devices become smaller and more powerful, PCBs will need to accommodate higher component densities, faster signal speeds, and improved thermal management. Advancements in materials, manufacturing processes, and design tools will be crucial in meeting these challenges.
Integration of Embedded Systems and IoT
The proliferation of embedded systems and the Internet of Things (IoT) will have a significant impact on PCB development. PCBs will need to integrate more functionality, including sensors, wireless connectivity, and power management, to enable seamless communication and data exchange in IoT networks. The development of low-power, high-performance PCBs will be essential for battery-operated IoT devices.
Challenges in PCB Design and Manufacturing
Despite the advancements in PCB technology, several challenges remain. Signal integrity, power integrity, and electromagnetic compatibility become increasingly complex as PCBs operate at higher frequencies and lower voltages. Ensuring reliable performance in harsh environments, such as extreme temperatures, vibrations, and moisture, requires robust design and manufacturing practices. Additionally, the demand for faster time-to-market and cost optimization puts pressure on PCB designers and manufacturers to innovate and streamline their processes.
Frequently Asked Questions (FAQ)
- What are the different types of PCBs?
- Single-sided PCBs: Conductive traces are present on only one side of the substrate.
- Double-sided PCBs: Conductive traces are present on both sides of the substrate, with through-hole connections.
- Multilayer PCBs: Multiple conductive layers are stacked and interconnected using vias.
- Flexible PCBs: Made from flexible materials, allowing for bending and folding.
-
Rigid-Flex PCBs: Combines rigid and flexible sections for 3D packaging and improved reliability.
-
What are the common materials used in PCB fabrication?
- FR-4: A glass-reinforced epoxy laminate, widely used for its good mechanical and electrical properties.
- Polyimide: A high-performance material known for its excellent thermal stability and chemical resistance.
- Teflon: Used in high-frequency applications due to its low dielectric constant and low loss tangent.
-
Copper: The primary conductive material used for PCB traces and pads.
-
What is the difference between through-hole and surface mount technology?
- Through-hole technology involves mounting components with leads that pass through holes in the PCB and are soldered on the opposite side.
- Surface Mount Technology (SMT) involves mounting components directly on the surface of the PCB, with leads soldered to pads on the same side.
-
SMT allows for smaller component sizes, higher density, and automated assembly compared to through-hole technology.
-
What are the key considerations in PCB design?
- Schematic design: Capturing the electrical connectivity and component selection.
- Layout design: Placing components and routing traces on the PCB while considering signal integrity, power integrity, and electromagnetic compatibility.
- Manufacturing constraints: Ensuring the PCB design is compatible with the chosen manufacturing process and meets the required tolerances.
-
Testing and verification: Performing simulations and physical tests to validate the PCB design and ensure reliable performance.
-
What are the benefits of using CAD and simulation tools in PCB design?
- CAD tools streamline the design process, reduce errors, and enable the creation of complex multilayer PCBs.
- Simulation tools, such as signal integrity and thermal analysis software, help optimize PCB designs and identify potential issues before fabrication.
- CAD and simulation tools improve design efficiency, reduce development time, and minimize the risk of costly design iterations.
Conclusion
The development history of PCBs is a testament to the continuous evolution and innovation in the electronics industry. From the early days of manual assembly to the advanced manufacturing techniques and design tools of today, PCBs have been at the forefront of enabling technological progress. As electronic devices become more sophisticated and demanding, PCB technology will continue to adapt and evolve to meet the challenges of miniaturization, high-frequency operation, and environmental sustainability.
By understanding the key milestones, advancements, and trends in PCB development, engineers and designers can make informed decisions and push the boundaries of what is possible in electronic design. The future of PCBs is exciting, with the potential for further miniaturization, integration of embedded systems, and the adoption of eco-friendly practices. As we embark on this journey, collaboration between PCB designers, manufacturers, and material suppliers will be crucial in driving innovation and shaping the future of the electronics industry.
Era | Key Developments |
---|---|
1900s | Concept of “printed wire” patented by Albert Hanson |
1930s | First practical PCBs developed by Paul Eisler |
1940s | Adoption of PCBs in military applications during WWII |
1950s | Introduction of through-hole technology |
1960s | Development of multilayer PCBs and photo-imaging processes |
1980s | Widespread adoption of Surface Mount Technology (SMT) |
1990s | Advancements in materials and substrates |
2000s | Emergence of High-Density Interconnect (HDI) PCBs |
2010s | Flexible, Rigid-Flex, and 3D PCBs gain popularity |
Present | Focus on miniaturization, high-frequency applications, and sustainability |
Table 1: Timeline of key developments in PCB history
0 Comments