Introduction to Flex PCBs
Flexible printed circuit boards (Flex PCBs) have revolutionized the electronics industry by providing a versatile, lightweight, and space-saving solution for various applications. Unlike traditional rigid PCBs, Flex PCBs can bend, twist, and conform to unique shapes, making them ideal for devices that require flexibility and durability. As the demand for smaller, more compact electronic devices grows, the importance of selecting the right Flex PCB manufacturer becomes increasingly crucial.
What are Flex PCBs?
Flex PCBs are printed circuit boards made from flexible substrate materials, such as polyimide or polyester. These materials allow the PCB to bend and flex without damaging the copper traces or components. Flex PCBs can be single-sided, double-sided, or multi-layered, depending on the complexity of the design and the application requirements.
Advantages of Flex PCBs
- Flexibility: Flex PCBs can bend and twist, enabling them to fit into tight spaces and conform to unique shapes.
- Lightweight: Flex PCBs are thinner and lighter than rigid PCBs, making them ideal for portable and wearable devices.
- Durability: Flex PCBs can withstand repeated bending and flexing without breaking or losing functionality.
- Space-saving: Flex PCBs can replace multiple rigid PCBs and connectors, reducing the overall size and weight of the device.
- Improved signal integrity: Flex PCBs can reduce signal interference and improve signal integrity by eliminating connectors and reducing the distance between components.
Factors to Consider When Choosing a Flex PCB Manufacturer
1. Experience and Expertise
When selecting a Flex PCB manufacturer, it is essential to consider their experience and expertise in the field. Look for a manufacturer with a proven track record of producing high-quality Flex PCBs for various industries and applications. An experienced manufacturer will have the knowledge and skills necessary to guide you through the design and manufacturing process, offering valuable insights and recommendations along the way.
Questions to Ask:
- How long has the manufacturer been producing Flex PCBs?
- What industries and applications have they served?
- Do they have experience with projects similar to yours?
2. Manufacturing Capabilities
Flex PCB manufacturing requires specialized equipment and processes that differ from those used for rigid PCBs. Ensure that the manufacturer you choose has the necessary capabilities to produce your Flex PCB design efficiently and effectively.
Key Capabilities to Look For:
- Material selection: Can the manufacturer work with a wide range of flexible substrate materials?
- Layer count: Can they produce single-sided, double-sided, and multi-layered Flex PCBs?
- Minimum trace width and spacing: Can they achieve the fine trace widths and spacing required for your design?
- Impedance control: Do they have the capability to control impedance for high-speed applications?
- Assembly: Can they provide Flex PCB Assembly services, such as component placement and soldering?
3. Quality Control and Testing
The reliability and performance of your Flex PCB depend on the quality control measures and testing procedures implemented by the manufacturer. A reputable Flex PCB manufacturer should have a robust quality management system in place to ensure that every PCB meets or exceeds the specified requirements.
Quality Control Measures to Inquire About:
- Visual inspection: Do they perform automated optical inspection (AOI) and manual visual inspection?
- Electrical testing: Do they conduct continuity, insulation resistance, and high-voltage testing?
- Mechanical testing: Do they perform bend testing and adhesion testing?
- Environmental testing: Can they conduct thermal cycling, humidity, and vibration testing?
- Certification: Are they ISO 9001 and/or IATF 16949 certified?
4. Lead Time and Pricing
Lead time and pricing are critical factors to consider when selecting a Flex PCB manufacturer, especially if you have a tight deadline or budget. Look for a manufacturer that can provide competitive pricing without compromising quality and can deliver your Flex PCBs within your required timeframe.
Factors Affecting Lead Time and Pricing:
- Design complexity: More complex designs with higher layer counts and finer features may require longer lead times and higher costs.
- Order quantity: Larger order quantities may be eligible for volume discounts and faster lead times.
- Material availability: Some specialized materials may have longer lead times or higher costs.
- Manufacturing location: Offshore manufacturers may offer lower prices but longer lead times compared to domestic manufacturers.
5. Customer Support and Communication
Effective communication and responsive customer support are essential for a smooth and successful Flex PCB manufacturing experience. Choose a manufacturer that is easy to communicate with and provides prompt and helpful support throughout the entire process.
Aspects of Customer Support to Consider:
- Responsiveness: How quickly do they respond to inquiries and requests?
- Technical support: Can they provide guidance and assistance with design and manufacturing issues?
- Project updates: Do they provide regular updates on the status of your project?
- Language barriers: Can they communicate effectively in your preferred language?
Flex PCB Manufacturing Process Overview
Understanding the Flex PCB manufacturing process can help you better communicate your requirements to the manufacturer and ensure that your design is optimized for manufacturability. The following is a high-level overview of the key steps involved in Flex PCB manufacturing.
1. Design and Artwork Creation
The Flex PCB manufacturing process begins with creating the PCB design and artwork using electronic design automation (EDA) software. The designer must consider the specific requirements of Flex PCBs, such as bend radii, stiffener placement, and coverlay openings.
2. Material Selection
The manufacturer selects the appropriate flexible substrate material based on the design requirements, such as the number of layers, bend radius, and environmental conditions. Common substrate materials include polyimide and polyester.
3. Imaging and Etching
The artwork is used to create a photomask, which is then used to transfer the circuit pattern onto the copper-clad substrate. The exposed copper is etched away, leaving the desired circuit pattern.
4. Lamination and Drilling
For multi-layer Flex PCBs, the individual layers are aligned and laminated together under high temperature and pressure. Holes are drilled through the laminated board for vias and component mounting.
5. Plating and Surface Finishing
The drilled holes are plated with copper to create electrical connections between layers. The exposed copper surfaces are then finished with a protective coating, such as ENIG or HASL, to prevent oxidation and improve solderability.
6. Coverlay Application and Cutting
A coverlay film is applied to the Flex PCB to protect the circuits and provide electrical insulation. The coverlay is then cut and opened in areas where components will be mounted or where electrical contacts are required.
7. Stiffener Attachment
If required, stiffeners are attached to specific areas of the Flex PCB to provide additional support and rigidity. Stiffeners can be made from materials such as FR-4, aluminum, or polyimide.
8. Electrical Testing and Inspection
The completed Flex PCB undergoes electrical testing and visual inspection to ensure that it meets the specified requirements and is free from defects.
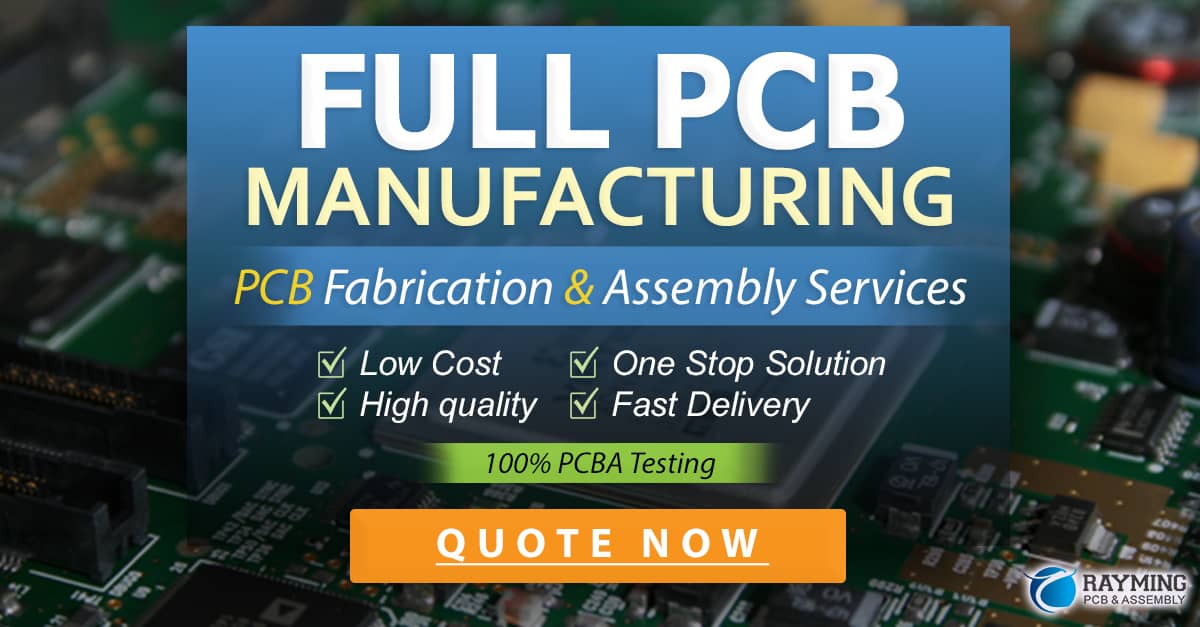
Flex PCB Design Considerations
Designing a Flex PCB requires a different approach than designing a rigid PCB. The following are some key design considerations to keep in mind when creating your Flex PCB design.
1. Bend Radius
The bend radius is the minimum radius that a Flex PCB can be bent without damaging the copper traces or substrate. The bend radius depends on factors such as the substrate material, copper thickness, and the number of layers. Consult with your manufacturer to determine the appropriate bend radius for your design.
2. Stiffener Placement
Stiffeners are used to provide support and rigidity to specific areas of the Flex PCB, such as connector locations or component mounting areas. Proper stiffener placement is crucial to ensure the reliability and durability of the Flex PCB.
3. Coverlay Openings
Coverlay openings are areas where the coverlay film is removed to expose the copper traces for component mounting or electrical contacts. Ensure that the coverlay openings are properly sized and positioned to accommodate the components and connectors.
4. Trace Width and Spacing
Flex PCBs often require finer trace widths and spacing compared to rigid PCBs to maintain flexibility and reduce stress on the copper traces. Work with your manufacturer to determine the minimum trace width and spacing achievable for your design.
5. Impedance Control
For high-speed applications, impedance control is essential to maintain signal integrity and reduce electromagnetic interference (EMI). Flex PCBs can be designed with controlled impedance traces by adjusting the trace width, spacing, and substrate thickness.
Frequently Asked Questions (FAQ)
1. What is the difference between a Flex PCB and a rigid PCB?
A Flex PCB is made from a flexible substrate material that allows it to bend and twist without damaging the copper traces or components. A rigid PCB, on the other hand, is made from a rigid substrate material, such as FR-4, and cannot bend or flex.
2. Can Flex PCBs be used for high-speed applications?
Yes, Flex PCBs can be designed with controlled impedance traces to maintain signal integrity and reduce EMI for high-speed applications. However, designing high-speed Flex PCBs requires careful consideration of factors such as trace geometry, material selection, and shielding.
3. How long does it typically take to manufacture a Flex PCB?
The lead time for Flex PCB manufacturing varies depending on factors such as design complexity, order quantity, and material availability. Typical lead times range from 2-4 weeks for prototype quantities and 4-8 weeks for production quantities. However, expedited options may be available for an additional cost.
4. Can Flex PCBs be assembled using the same processes as rigid PCBs?
Flex PCBs can be assembled using similar processes as rigid PCBs, such as SMT and through-hole assembly. However, special considerations must be taken to account for the flexibility of the substrate, such as using low-stress components and adhesives.
5. How do I choose the right substrate material for my Flex PCB?
The choice of substrate material depends on factors such as the bend radius, environmental conditions, and electrical requirements of your application. Common substrate materials include polyimide and polyester, each with its own advantages and limitations. Consult with your manufacturer to determine the best substrate material for your specific application.
Conclusion
Selecting the best Flex PCB manufacturer for your next project requires careful consideration of factors such as experience, manufacturing capabilities, quality control, lead time, pricing, and customer support. By understanding the Flex PCB manufacturing process and key design considerations, you can effectively communicate your requirements to the manufacturer and ensure a successful outcome.
When evaluating potential Flex PCB manufacturers, ask questions about their experience, capabilities, and quality control measures. Request samples and references to assess the quality of their work and their ability to meet your specific requirements.
Ultimately, choosing the right Flex PCB manufacturer is essential to the success of your project. By partnering with a reputable and experienced manufacturer, you can ensure that your Flex PCBs are of the highest quality, reliability, and performance.
0 Comments