What is PCB Copper Balance and Why is it Important?
PCB copper balance refers to achieving an equal distribution of copper across both sides of a printed circuit board (PCB) during the manufacturing process. It is a critical aspect of PCB design and fabrication that impacts the overall quality, reliability, and functionality of the final product.
Maintaining proper copper balance is essential for several reasons:
-
Mechanical stability: Uneven copper distribution can cause warping or twisting of the PCB due to unequal thermal expansion and contraction forces during the fabrication process and during operation.
-
Electrical performance: Copper imbalance can lead to signal integrity issues, such as impedance mismatches, crosstalk, and electromagnetic interference (EMI), which can negatively affect the performance of the circuit.
-
Manufacturing process: Balanced copper distribution ensures better yields during the etching process, as it allows for more consistent etch rates across the board.
-
Cost-effectiveness: PCBs with poor copper balance may require additional processing steps or may have a higher rejection rate, increasing production costs.
Factors Affecting PCB Copper Balance
Several factors can influence the copper balance in a PCB during the design and fabrication stages:
PCB Design Factors
-
Trace width and spacing: The width of the copper traces and the spacing between them can impact the copper distribution on the board. Wider traces and larger spacing can lead to copper imbalance.
-
Copper pour: The use of copper pour (filling unused areas with copper) can help improve copper balance by distributing copper more evenly across the board.
-
Component placement: The location and orientation of components on the PCB can affect copper balance. Placing large components or copper-heavy areas on one side of the board can lead to imbalance.
-
Layer stack-up: The arrangement of copper layers in the PCB stack-up can impact copper balance. Asymmetrical stack-ups or uneven copper distribution across layers can cause imbalance.
PCB Fabrication Factors
-
Etching process: The etching process, which removes unwanted copper from the PCB, can affect copper balance if not properly controlled. Uneven etching rates or over-etching can lead to copper imbalance.
-
Plating process: The copper plating process, used to increase the thickness of copper traces and vias, can cause imbalance if not applied consistently across the board.
-
Material selection: The choice of PCB substrate material and copper foil thickness can impact copper balance. Thinner copper foils or materials with different thermal expansion properties can contribute to imbalance.
Techniques for Achieving PCB Copper Balance
To achieve optimal copper balance in PCB design and fabrication, several techniques can be employed:
Design Techniques
-
Symmetric layout: Designing a symmetrical PCB layout, with an even distribution of components and copper features on both sides of the board, can help maintain copper balance.
-
Copper thieving: Adding copper thieving patterns (small, non-functional copper areas) in regions with low copper density can help balance the overall copper distribution.
-
Trace width control: Ensuring consistent trace widths and spacing throughout the design can contribute to better copper balance.
-
Via balancing: Distributing vias evenly across the board and avoiding large concentrations of vias in specific areas can improve copper balance.
Fabrication Techniques
-
Copper foil selection: Using copper foils with consistent thickness and quality can help maintain copper balance during the fabrication process.
-
Etching process optimization: Properly calibrating and monitoring the etching process to ensure consistent etch rates across the board can minimize copper imbalance.
-
Plating process control: Implementing strict process controls during the copper plating stage to achieve uniform plating thickness can contribute to better copper balance.
-
Inspection and measurement: Regularly inspecting and measuring the copper distribution on the PCBs during fabrication can help identify and correct any imbalances early in the process.
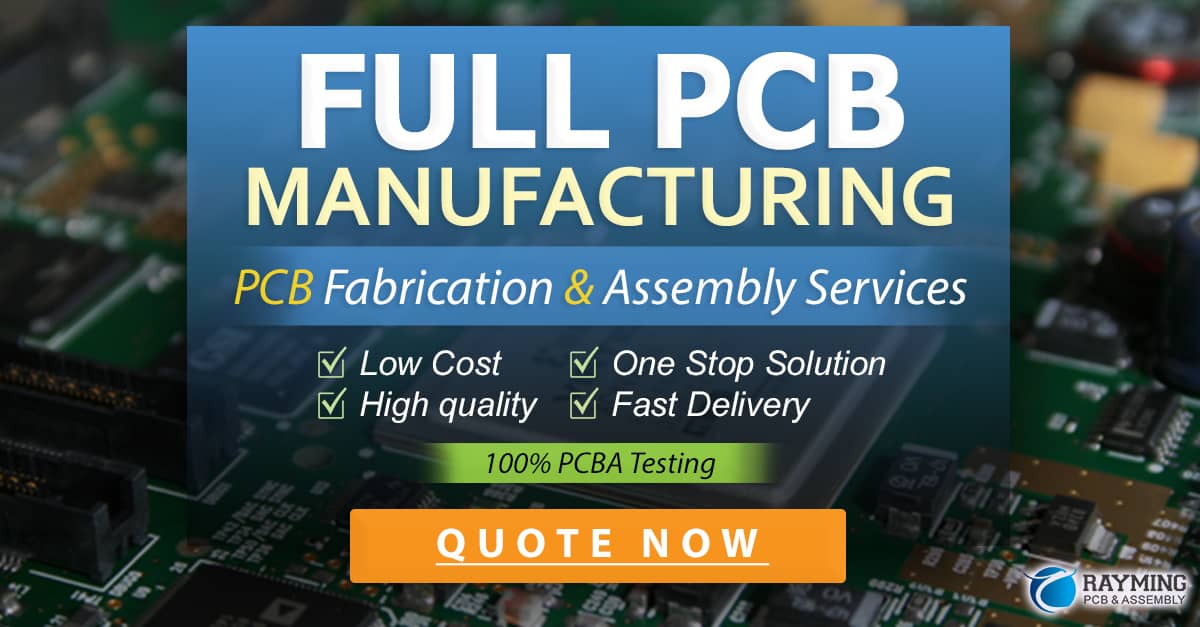
Measuring and Evaluating PCB Copper Balance
To ensure that PCBs meet the required copper balance specifications, various measurement and evaluation methods can be used:
-
Visual inspection: A simple visual inspection of the PCB can reveal obvious copper imbalances, such as large areas of exposed substrate or excessive copper on one side of the board.
-
Microscopic examination: Using a microscope to examine the copper distribution at a higher magnification can provide more detailed information about the copper balance.
-
Cross-sectional analysis: Creating cross-sectional samples of the PCB and analyzing them under a microscope can reveal the copper distribution across the layers and help identify any imbalances.
-
Electrical testing: Performing electrical tests, such as impedance and resistance measurements, can indirectly indicate copper balance issues that may affect the electrical performance of the PCB.
-
Automated optical inspection (AOI): AOI systems can quickly scan the PCB surface and compare the copper distribution to predefined templates, identifying any areas of imbalance.
Method | Advantages | Disadvantages |
---|---|---|
Visual Inspection | Quick and inexpensive | Limited to obvious imbalances |
Microscopic Examination | Detailed information | Time-consuming and requires specialized equipment |
Cross-Sectional Analysis | Reveals copper distribution across layers | Destructive and time-consuming |
Electrical Testing | Relates copper balance to electrical performance | Indirect measurement and may not detect all imbalances |
Automated Optical Inspection (AOI) | Fast and automated | Requires specialized equipment and setup |
Case Studies and Examples
Case Study 1: Smartphone PCB Copper Balance Optimization
A smartphone manufacturer was experiencing yield issues and performance problems with their PCBs due to copper imbalance. By analyzing the PCB design and fabrication process, they identified several areas for improvement:
- Redesigning the PCB layout to achieve a more symmetrical distribution of components and copper features.
- Implementing copper thieving techniques in regions with low copper density.
- Optimizing the etching and plating processes to ensure consistent copper removal and deposition.
After implementing these changes, the manufacturer observed a significant improvement in PCB yield and device performance, with fewer instances of signal integrity issues and mechanical failures.
Case Study 2: High-Speed PCB Copper Balance for Automotive Applications
An automotive electronics supplier was developing a high-speed PCB for a critical safety system. Maintaining proper copper balance was crucial to ensure reliable performance under harsh environmental conditions. The supplier took the following steps to achieve optimal copper balance:
- Carefully selecting PCB materials with matched thermal expansion properties to minimize warping.
- Designing a symmetrical layer stack-up with even copper distribution across layers.
- Utilizing advanced simulation tools to analyze and optimize the copper distribution during the design phase.
- Implementing strict process controls and regular inspections during PCB fabrication to maintain copper balance.
As a result, the high-speed PCB met all performance and reliability requirements, enabling the successful deployment of the automotive safety system.
Frequently Asked Questions (FAQ)
-
What is the ideal copper balance for a PCB?
The ideal copper balance for a PCB depends on the specific application and design requirements. Generally, a copper balance within 10-20% between the top and bottom layers is considered acceptable for most applications. However, more stringent requirements may apply for high-performance or safety-critical applications. -
Can copper imbalance cause PCB warping?
Yes, copper imbalance can cause PCB warping due to uneven thermal expansion and contraction forces. When one side of the PCB has significantly more copper than the other, the board may warp or twist during the fabrication process or during operation, leading to mechanical stress and potential reliability issues. -
How does copper imbalance affect signal integrity?
Copper imbalance can affect signal integrity by causing impedance mismatches, crosstalk, and electromagnetic interference (EMI). Uneven copper distribution can create variations in the characteristic impedance of traces, leading to signal reflections and distortions. Additionally, imbalanced copper can act as an antenna, radiating or picking up unwanted EMI. -
What is copper thieving, and how does it help with copper balance?
Copper thieving is a technique used in PCB design to improve copper balance by adding small, non-functional copper areas in regions with low copper density. These copper thieving patterns help distribute the copper more evenly across the board, reducing the overall copper imbalance. Copper thieving is typically added during the PCB layout stage. -
How can I measure copper balance in a PCB?
There are several methods to measure copper balance in a PCB, including visual inspection, microscopic examination, cross-sectional analysis, electrical testing, and automated optical inspection (AOI). Each method has its advantages and disadvantages in terms of speed, accuracy, and destructiveness. A combination of these methods may be used depending on the specific requirements and available resources.
Conclusion
Achieving proper copper balance is a critical aspect of PCB design and fabrication, as it directly impacts the mechanical stability, electrical performance, manufacturability, and cost-effectiveness of the final product. By understanding the factors that influence copper balance and employing appropriate design and fabrication techniques, PCB manufacturers can ensure optimal copper distribution and minimize the risk of PCB failures.
Regular monitoring, measurement, and evaluation of copper balance throughout the PCB fabrication process are essential for maintaining high-quality standards and identifying potential issues early on. By following best practices and continuously improving copper balancing techniques, PCB manufacturers can deliver reliable, high-performance products that meet the ever-increasing demands of modern electronic applications.
0 Comments