Introduction to PCB prototyping
PCB (Printed Circuit Board) prototyping is a crucial step in the development of new electronic products. It allows designers and engineers to test and validate their designs before committing to full-scale production. In this comprehensive guide, we will explore the various aspects of PCB prototyping, including its benefits, the process involved, and best practices to ensure a successful prototype.
What is PCB Prototyping?
PCB prototyping is the process of creating a functional prototype of a printed circuit board design. This prototype is used to test and validate the design, ensuring that it meets the required specifications and functions as intended. PCB Prototypes are typically created using specialized software and manufacturing techniques, such as PCB Assembly services.
Benefits of PCB Prototyping
-
Design Validation: PCB prototyping allows designers to test and validate their designs before committing to full-scale production. This helps identify any potential issues or flaws in the design, saving time and money in the long run.
-
Cost-Effective: Creating a PCB prototype is much more cost-effective than going straight into full-scale production. It allows designers to make necessary changes and improvements without incurring significant costs.
-
Time-Saving: PCB prototyping streamlines the product development process by identifying and addressing issues early on. This saves time that would otherwise be spent on debugging and troubleshooting during full-scale production.
-
Improved Functionality: By testing and validating the design through PCB prototyping, designers can ensure that the final product functions as intended and meets the required specifications.
The PCB Prototyping Process
Step 1: Design Creation
The first step in PCB prototyping is creating the design using specialized software, such as Eagle, KiCad, or Altium Designer. The design should include all the necessary components, traces, and connections required for the PCB to function as intended.
Step 2: Design Review
Once the design is created, it should be thoroughly reviewed to ensure that it meets all the required specifications. This includes checking for any design rule violations, component placement issues, or potential manufacturing challenges.
Step 3: Prototype Fabrication
After the design has been reviewed and finalized, the PCB prototype can be fabricated using PCB assembly services. This typically involves the following steps:
-
PCB Fabrication: The PCB is manufactured using specialized equipment and techniques, such as etching, drilling, and plating.
-
Component Sourcing: The necessary components for the PCB are sourced from reliable suppliers.
-
PCB Assembly: The components are placed and soldered onto the PCB using automated assembly equipment or manual soldering techniques.
Step 4: Testing and Validation
Once the PCB prototype has been assembled, it must undergo rigorous testing and validation to ensure that it functions as intended. This may include:
-
Functional Testing: Verifying that the PCB performs all the required functions and meets the specified performance criteria.
-
Environmental Testing: Subjecting the PCB to various environmental conditions, such as temperature, humidity, and vibration, to ensure its durability and reliability.
-
Compliance Testing: Ensuring that the PCB complies with relevant industry standards and regulations.
Step 5: Design Iteration
Based on the results of the testing and validation phase, the PCB design may need to be iterated and refined. This may involve making changes to the component placement, trace routing, or other aspects of the design.
Best Practices for PCB Prototyping
To ensure a successful PCB prototyping process, consider the following best practices:
-
Use Reliable PCB Assembly Services: Choose a reputable PCB assembly service provider with experience in prototyping and a proven track record of delivering high-quality results.
-
Communicate Clearly with Your PCB Assembly Partner: Provide clear and detailed design files, specifications, and requirements to your PCB assembly partner to avoid misunderstandings and delays.
-
Plan for Testing and Validation: Allocate sufficient time and resources for the testing and validation phase to ensure that the PCB prototype meets all the required specifications and functions as intended.
-
Be Prepared for Design Iterations: Anticipate the need for design iterations based on the results of the testing and validation phase. Be flexible and open to making necessary changes to improve the design.
-
Consider Design for Manufacturability (DFM): Design your PCB with manufacturability in mind, taking into account factors such as component placement, trace routing, and manufacturing tolerances.
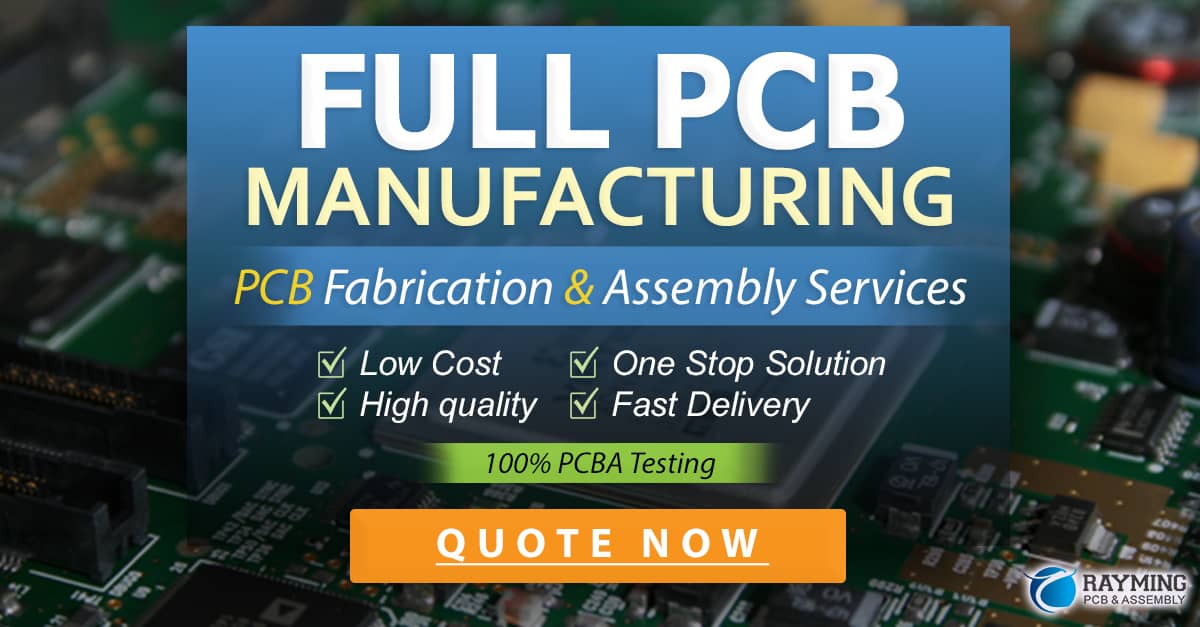
PCB Prototyping Technologies
There are several technologies used in PCB prototyping, each with its own advantages and limitations. Here are some of the most common PCB prototyping technologies:
Technology | Description | Advantages | Limitations |
---|---|---|---|
Traditional Etching | Uses chemical etching to remove unwanted copper from the PCB substrate | Cost-effective for low-volume production | Limited resolution and accuracy |
CNC Milling | Uses computer-controlled milling machines to remove unwanted copper from the PCB substrate | High precision and accuracy | Higher cost compared to traditional etching |
3D Printing | Uses additive manufacturing techniques to create PCB Prototypes | Rapid prototyping and customization | Limited material options and lower durability |
Laser Etching | Uses laser technology to remove unwanted copper from the PCB substrate | High precision and accuracy | Higher cost compared to traditional etching |
PCB Assembly Services
PCB assembly services play a crucial role in the PCB prototyping process. These services typically offer a range of capabilities, including:
-
PCB Fabrication: Manufacturing the PCB substrate using various techniques, such as etching, drilling, and plating.
-
Component Sourcing: Procuring the necessary components for the PCB from reliable suppliers.
-
PCB Assembly: Placing and soldering the components onto the PCB using automated assembly equipment or manual soldering techniques.
-
Testing and Inspection: Performing various tests and inspections to ensure the quality and functionality of the assembled PCB.
When choosing a PCB assembly service for your prototyping needs, consider factors such as:
- Experience and expertise in PCB prototyping
- Range of services offered
- Quality control processes
- Turnaround time and pricing
- Customer support and communication
Frequently Asked Questions (FAQ)
-
Q: How long does PCB prototyping typically take?
A: The time required for PCB prototyping varies depending on the complexity of the design and the chosen PCB assembly service. Generally, it can take anywhere from a few days to several weeks to complete the prototyping process. -
Q: How much does PCB prototyping cost?
A: The cost of PCB prototyping depends on factors such as the complexity of the design, the chosen PCB assembly service, and the number of prototypes required. Prices can range from a few hundred to several thousand dollars. -
Q: What are the minimum order quantities for PCB prototyping?
A: Minimum order quantities for PCB prototyping vary among PCB assembly services. Some services offer low minimum order quantities, even as low as one or two prototypes, while others may require higher quantities. -
Q: Can I use any PCB design software for PCB prototyping?
A: Most PCB assembly services accept design files from popular PCB design software, such as Eagle, KiCad, and Altium Designer. However, it’s always best to check with your chosen service provider for their specific requirements and supported file formats. -
Q: What should I do if my PCB prototype doesn’t function as intended?
A: If your PCB prototype doesn’t function as intended, the first step is to identify the root cause of the issue. This may involve further testing, debugging, and design analysis. Based on the findings, you may need to iterate the design and create a new prototype to address the identified issues.
Conclusion
PCB prototyping is an essential step in the development of new electronic products, allowing designers and engineers to test and validate their designs before committing to full-scale production. By following best practices and leveraging the expertise of reliable PCB assembly services, you can streamline the prototyping process and ensure a successful outcome.
Remember to carefully plan your prototyping process, communicate clearly with your PCB assembly partner, and be prepared for design iterations based on testing and validation results. By doing so, you can build a new product quickly and efficiently with the help of PCB assembly prototyping.
0 Comments