1. Design for Manufacturability (DFM)
Designing a PCB with manufacturability in mind is essential for successful assembly. Here are some key points to consider:
1.1. Component Placement
- Place components in a logical and organized manner
- Ensure adequate spacing between components for easy soldering and inspection
- Consider the orientation of components for optimal assembly
1.2. Trace Width and Spacing
- Follow the recommended trace width and spacing guidelines based on the PCB’s electrical requirements
- Ensure proper clearance between traces to avoid short circuits
1.3. Via and Pad Size
- Use appropriate via and pad sizes based on the component’s pin size and current carrying capacity
- Maintain consistent via and pad sizes throughout the PCB design
Parameter | Recommended Value |
---|---|
Minimum Trace Width | 0.1 mm (4 mil) |
Minimum Trace Spacing | 0.1 mm (4 mil) |
Minimum Via Diameter | 0.3 mm (12 mil) |
Minimum Pad Size | 0.4 mm (16 mil) |
2. Component Selection
Selecting the right components is crucial for PCB Assembly success. Consider the following factors:
2.1. Quality and Reliability
- Choose components from reputable manufacturers with proven track records
- Ensure components meet the required specifications and standards
2.2. Availability and Lead Time
- Select components that are readily available and have short lead times
- Consider alternative components in case of supply chain disruptions
2.3. Cost-Effectiveness
- Balance component cost with performance and reliability requirements
- Conduct a cost analysis to optimize the overall PCB assembly budget
3. Solder Paste Selection
Choosing the appropriate solder paste is essential for achieving reliable solder joints. Consider the following factors:
3.1. Alloy Composition
- Select the solder paste alloy based on the PCB’s thermal and electrical requirements
- Common alloys include Sn63/Pb37, Sn96.5/Ag3.0/Cu0.5 (SAC305), and Sn99.3/Cu0.7
3.2. Particle Size
- Choose the solder paste particle size based on the component pitch and stencil thickness
- Commonly used particle sizes are Type 3 (25-45 µm) and Type 4 (20-38 µm)
3.3. Flux Type
- Select the flux type based on the PCB’s surface finish and cleaning requirements
- Common flux types include no-clean, water-soluble, and rosin-based
Alloy | Melting Point | Composition |
---|---|---|
Sn63/Pb37 | 183°C | 63% Tin, 37% Lead |
SAC305 | 217-220°C | 96.5% Tin, 3% Silver, 0.5% Copper |
Sn99.3/Cu0.7 | 227°C | 99.3% Tin, 0.7% Copper |
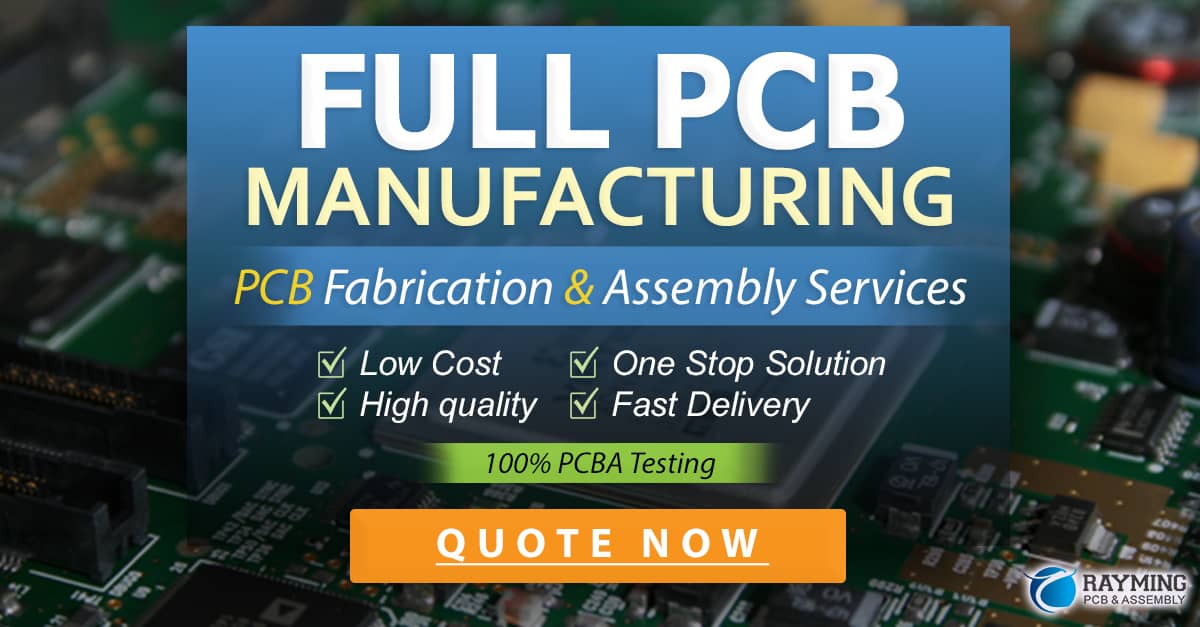
4. Stencil Design
A well-designed stencil is essential for precise solder paste deposition. Consider the following factors:
4.1. Aperture Size and Shape
- Optimize aperture size and shape based on the component’s pad size and pitch
- Use rounded corners to improve solder paste release
4.2. Stencil Thickness
- Select the stencil thickness based on the solder paste’s particle size and volume requirements
- Commonly used stencil thicknesses range from 0.1 mm (4 mil) to 0.15 mm (6 mil)
4.3. Stencil Material
- Choose a stencil material that is durable and resistant to wear
- Common materials include stainless steel, nickel-plated stainless steel, and laser-cut plastic
5. Reflow Soldering Profile
Developing an optimized reflow soldering profile is critical for achieving reliable solder joints. Consider the following factors:
5.1. Preheat Zone
- Gradually raise the PCB’s temperature to activate the flux and evaporate solvents
- Typical preheat ramp rate is 1-3°C/second
5.2. Soak Zone
- Maintain a stable temperature to allow the flux to remove oxides and prepare the surfaces for soldering
- Typical soak temperature is 150-180°C for 60-120 seconds
5.3. Reflow Zone
- Raise the temperature above the solder paste’s melting point to form solder joints
- Peak temperature should be 20-40°C above the solder paste’s melting point
- Typical reflow time is 30-90 seconds
5.4. Cooling Zone
- Gradually cool the PCB to solidify the solder joints and prevent thermal shock
- Typical cooling ramp rate is 2-6°C/second
Reflow Profile Zone | Temperature Range | Duration |
---|---|---|
Preheat | 25-150°C | 30-90 seconds |
Soak | 150-180°C | 60-120 seconds |
Reflow | 220-250°C | 30-90 seconds |
Cooling | 250-25°C | 30-90 seconds |
6. Automated Optical Inspection (AOI)
Implementing AOI is essential for detecting assembly defects and ensuring PCB quality. Consider the following factors:
6.1. AOI System Selection
- Choose an AOI system that is compatible with the PCB’s size, component types, and inspection requirements
- Consider the system’s resolution, speed, and defect detection capabilities
6.2. Inspection Coverage
- Ensure the AOI system covers all critical areas of the PCB, including components, solder joints, and traces
- Define inspection criteria based on the PCB’s quality requirements
6.3. False Call Reduction
- Optimize the AOI system’s parameters to minimize false calls and improve inspection accuracy
- Regularly review and update the inspection library to accommodate new components and assembly variations
7. X-Ray Inspection
X-ray inspection is crucial for detecting hidden assembly defects, such as voids and bridging. Consider the following factors:
7.1. X-Ray System Selection
- Choose an X-ray system that is suitable for the PCB’s size, component types, and inspection requirements
- Consider the system’s resolution, magnification, and defect detection capabilities
7.2. Inspection Coverage
- Focus on critical areas of the PCB, such as ball grid arrays (BGAs), quad flat no-leads (QFNs), and other high-density components
- Define inspection criteria based on the component’s specifications and quality requirements
7.3. Void Analysis
- Use the X-ray system’s void analysis tools to measure void size, location, and distribution
- Establish acceptable void limits based on industry standards and customer requirements
8. Cleaning and Conformal Coating
Proper cleaning and conformal coating are essential for PCB reliability and protection. Consider the following factors:
8.1. Cleaning Method
- Select a cleaning method that is compatible with the PCB’s components, solder paste, and flux residues
- Common methods include aqueous cleaning, solvent cleaning, and no-clean processes
8.2. Cleanliness Testing
- Conduct cleanliness testing to ensure the PCB meets the required cleanliness levels
- Use methods such as ionic contamination testing and surface insulation resistance (SIR) testing
8.3. Conformal Coating Selection
- Choose a conformal coating that provides the required level of protection against moisture, dust, and other environmental factors
- Common coatings include acrylic, silicone, urethane, and parylene
9. Traceability and Documentation
Maintaining proper traceability and documentation is essential for quality control and continuous improvement. Consider the following factors:
9.1. Component Traceability
- Implement a system to track components from incoming inspection to final assembly
- Record component lot numbers, date codes, and supplier information
9.2. Process Documentation
- Document all critical assembly processes, including solder paste printing, component placement, and reflow soldering
- Maintain records of process parameters, inspection results, and any deviations or corrective actions
9.3. Quality Metrics
- Establish key quality metrics, such as first pass yield, defect rate, and customer returns
- Regularly review and analyze quality metrics to identify improvement opportunities
10. Continuous Improvement
Embracing a culture of continuous improvement is essential for long-term PCB assembly success. Consider the following factors:
10.1. Root Cause Analysis
- Conduct thorough root cause analysis for assembly defects and quality issues
- Identify and address the underlying causes to prevent recurrence
10.2. Process Optimization
- Continuously monitor and optimize assembly processes to improve efficiency, quality, and cost-effectiveness
- Implement statistical process control (SPC) to detect and correct process variations
10.3. Training and Development
- Invest in regular training and development programs for assembly operators and quality personnel
- Encourage cross-functional collaboration and knowledge sharing
Frequently Asked Questions (FAQ)
- What is the difference between lead-based and lead-free solder paste?
-
Lead-based solder paste contains a combination of tin and lead, typically Sn63/Pb37, while lead-free solder paste uses alternative alloys, such as SAC305 (Sn96.5/Ag3.0/Cu0.5). Lead-free solder paste has a higher melting point and requires different reflow profiles compared to lead-based solder paste.
-
How can I prevent tombstoning during PCB assembly?
-
Tombstoning occurs when a component lifts off the PCB due to uneven solder joint formation. To prevent tombstoning, ensure proper component placement, use a balanced solder paste deposition, and optimize the reflow profile to achieve uniform heating and cooling.
-
What are the most common PCB assembly defects?
-
Common PCB assembly defects include solder bridges, open joints, insufficient solder, component misalignment, and lifted leads. These defects can be caused by various factors, such as improper solder paste deposition, incorrect component placement, and suboptimal reflow profiles.
-
How often should I perform cleanliness testing on assembled PCBs?
-
The frequency of cleanliness testing depends on the PCB’s application, environmental conditions, and customer requirements. It is generally recommended to perform cleanliness testing on a regular basis, such as once per shift or daily, to ensure consistent quality and reliability.
-
What are the benefits of using an automated optical inspection (AOI) system?
- AOI systems offer several benefits, including fast and accurate defect detection, reduced human error, and improved traceability. AOI can identify a wide range of assembly defects, such as missing components, solder bridges, and incorrect component orientation, enabling early detection and correction of issues.
By following these top 10 tips for PCB assembly success, manufacturers can improve product quality, reliability, and customer satisfaction. Implementing best practices in design, component selection, soldering techniques, inspection, and continuous improvement will help ensure consistent and successful PCB assembly outcomes.
0 Comments