Introduction
Circuit boards, also known as printed circuit boards (PCBs), are essential components in nearly every electronic device. They provide the foundation on which microchips, resistors, capacitors and other components are mounted and connected together with conductive pathways called traces. Assembling circuit boards is a delicate process that requires great precision and attention to detail. This guide will walk through the key steps involved in properly assembling a circuit board by hand.
Gather Materials and Tools
Before beginning assembly, you need to gather all the necessary materials and tools:
- Circuit board – The bare PCB forms the base of the assembly. Ensure it is the right size and layout for your purposes.
- Components – Resistors, capacitors, ICs, transistors, etc. that will be soldered to the board.
- Solder and soldering iron – Used to fuse components to board. Lead-free solder is recommended.
- Magnifying glass – Helps visualize small components and solder joints.
- Needle nose pliers – For bending and cutting component leads.
- Flux and flux pen – Flux improves solder flow and connections.
- Isopropyl alcohol – For cleaning board after soldering.
- Multimeter – Tests conductivity of traces and detects short circuits.
Prepare the Board
Before placing any components, the board itself must be prepared:
- Clean – Remove any debris, dust or residue from the board with isopropyl alcohol.
- Inspect – Look for any scratches, breaks in traces or damage to board.
- Apply solder mask – Optional layer to prevent solder bridges.
- Tin pads – Apply a small amount of solder to any pads that will have components soldered to them. This improves adhesion.
Place and Solder Components
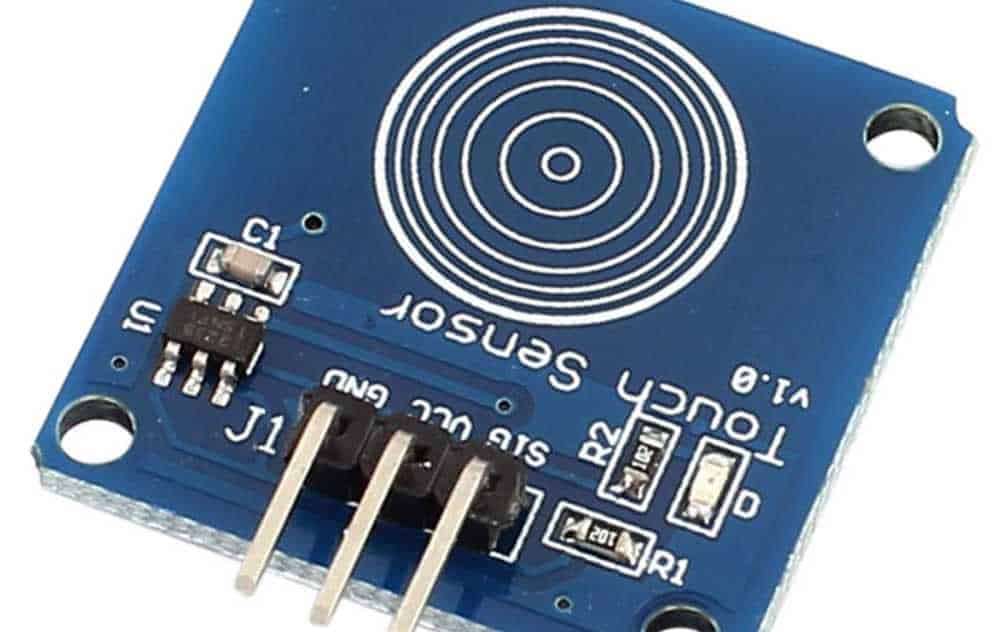
Now the board is ready for components to be added:
- Insert components – Carefully insert each component into its designated place on the board, ensuring the correct orientation and alignment. Verify values/ratings match circuit design.
- Bend leads – Bend the component leads slightly to hold components in place before soldering.
- Apply flux – Use flux pen to coat any solder points, such as component leads and pads. This aids solder flow.
- Solder components – Heat pads and leads with soldering iron tip, apply solder until joint is formed. Work systematically from smallest to largest components.
- Trim leads – After solder joints cool, use needle nose pliers to trim any excess component leads close to the solder joint.
- Inspect solder joints – Visually inspect each joint under magnifying glass. Fix any bad connections or cold joints.
- Clean board – Use isopropyl alcohol and swabs to thoroughly clean flux residue from the board.
Test Circuit Board
Once assembly is complete, the board must be tested:
- Visual inspection – Look for poor joints, bridges or wrongly placed components.
- Continuity test – Use a multimeter to check for electrical connectivity and shorts between different test points.
- Power-up test – Connect board to power source and measure outputs to verify expected circuit operation.
- Function test – Connect external components/devices and validate entire system works as intended.
- Debug – If any issues, rework solder joints, replace damaged parts, or check design and assembly steps.
Thorough testing helps catch errors and fixes them before putting the assembled circuit board into service.
Safety Considerations
Proper precautions should be taken:
- Wear eye protection – Solder can splash molten metal.
- Ventilate work area – Avoid inhaling solder fumes.
- Handle boards carefully – Prevent electrostatic discharge damage.
- Use lead-free solder – Reduces health risks.
- Keep work area clean – Prevent slips or falls on clutter.
Following basic safety measures makes circuit board assembly safer.
Common Problems and Solutions
Here are some common issues and ways to troubleshoot them:
Cold Solder Joints
- Cause: Not enough heat applied, dirty/oxidized surfaces
- Fix: Reheat joint fully until smooth and shiny
Solder Bridges
- Cause: Excess solder creates short circuit between points
- Fix: Use solder wick to remove excess solder
Dry Joints
- Cause: No solder or flux applied
- Fix: Apply flux and re-solder the joint
Wrong Components
- Cause: Incorrect parts populated on board
- Fix: Replace with proper components
Damaged PCB Traces
- Cause: Cracks or breaks in copper traces
- Fix: Carefully repair traces with wire or conductive ink
Power or Signal Shorts
- Cause: Unintended connection creating short
- Fix: Insulate between points or reroute wiring
Tips for Successful Assembly
Follow these tips when assembling your own circuit boards:
- Work slowly and methodically. Rushing leads to mistakes.
- Use the correct soldering temperature. Too hot risks damage.
- Keep components flush to the board when soldering.
- Apply just enough solder to create a “fillet” on the joint.
- Double check component values and orientations before soldering.
- Use good quality flux suited for electronics. Acid-based plumbing flux will corrode traces.
- Watch out for solder splashes which can create shorts.
- Keep boards very clean and free of debris during assembly.
- Have proper soldering tools and keep tips freshly tinned.
Conclusion
Assembling circuit boards requires great care, patience and fine workmanship to be done successfully. Following the steps outlined in this guide, taking safety precautions and applying best practices will help you produce professional, functioning circuit boards for your electronics projects and products. With practice, you can become skilled at hand soldering complex boards and enjoy the satisfaction of creating your own electronics from the ground up.
Frequently Asked Questions
What are some good ways to learn PCB assembly as a beginner?
Some recommendations to learn basic PCB assembly:
- Watch videos of experienced assemblers soldering components. Study their techniques closely.
- Start with a simple practice kit or board specifically designed for beginners.
- Read guides and tutorials about the assembly process from start to finish.
- Enroll in a class at a local makerspace or workshop focused on circuit board fabrication and assembly.
- Find an experienced hobbyist or engineer mentor who can observe your progress and provide tips.
- Invest in basic tools and supplies and practice soldering spare wires, joints, and components.
How small of components can reasonably be hand soldered?

With practice, experienced assemblers can solder very small surface-mount components down to sizes of 0402 or 0201 by hand using fine tipped soldering irons, quality flux, precision tweezers, and magnifying aids. However for beginners, 0805 or larger components are recommended. Anything smaller is extremely challenging without specialized tools and scopes.
What is the best way to remove or desolder a component from a board?
To remove a component already soldered to a board, apply flux to all pins and joints, then use a solder sucker tool to vacuum up the molten solder. Be careful not to overheat and lift pads. Once all pins are desoldered, the component can be gently lifted off. Alternately, solder wick can be used to absorb excess solder. Take care not to rip up traces.
Is it possible to repair damaged PCBs or lift pads?
Yes, it is possible to repair damaged PCBs, restore lifted pads, and replace broken traces through skilled rework. Methods include bridging with small gauge magnet wire, filling damaged areas with conductive epoxy, or scraping away conformal coating and laying thin copper tape over damaged areas. Rework requires great care and precision. Seriously damaged boards may need professional re-manufacturing.
How does one safely dispose of electronic waste like used circuit boards?
Proper e-waste disposal is important. Used circuit boards contain hazardous materials like lead that should not go to landfills. Many municipalities have special electronic waste recycling programs that accept old electronics and boards. You can also mail boards back to reputable electronics recyclers. Never burn or throw used circuit boards in the trash. Handling e-waste properly avoids pollution.
0 Comments