Introduction to PCB Fabrication
PCB fabrication is the process of designing and manufacturing printed circuit boards (PCBs). PCBs are essential components in almost all electronic devices, from smartphones and laptops to industrial control systems and medical equipment. While PCBs are typically mass-produced in factories, it is possible to make them at home with the right tools and techniques. In this article, we will explore an easy approach to PCB fabrication that you can do in the comfort of your own home.
What is a PCB?
A PCB is a flat board made of insulating material, such as fiberglass or plastic, with conductive tracks printed on one or both sides. These tracks, also known as traces, connect various electronic components, such as resistors, capacitors, and integrated circuits (ICs), to form a complete circuit. PCBs provide a compact and reliable way to assemble electronic circuits, as opposed to using individual wires or breadboards.
Why Make PCBs at Home?
There are several reasons why you might want to make PCBs at home:
-
Cost savings: Making your own PCBs can be cheaper than ordering them from a manufacturer, especially for small quantities or prototype designs.
-
Customization: When you make your own PCBs, you have complete control over the design and can easily modify it as needed.
-
Learning experience: PCB fabrication is a valuable skill to have for anyone interested in electronics. Making PCBs at home is a great way to learn about circuit design and manufacturing processes.
-
Rapid prototyping: With a home PCB fabrication setup, you can quickly create prototypes and test your designs without waiting for a manufacturer to deliver the boards.
Tools and Materials Required for PCB Fabrication
To make PCBs at home, you will need the following tools and materials:
Hardware
Tool | Description |
---|---|
Laser printer | Used to print the PCB design onto transfer paper |
Clothes iron | Used to transfer the printed design onto the copper-clad board |
UV exposure unit | Used to expose the photoresist-coated board to UV light |
Etching tank | Used to etch away the unwanted copper from the board |
Drill or drill press | Used to drill holes for component leads and mounting |
Consumables
Material | Description |
---|---|
Copper-clad board | The base material for the PCB, typically FR-4 or similar |
Transfer paper | Special paper used to transfer the printed design onto the copper-clad board |
Photoresist film | Light-sensitive film used to create the etching mask on the copper-clad board |
Developer solution | Chemical solution used to develop the exposed photoresist film |
Etching solution | Chemical solution used to remove the unwanted copper from the board |
Drill bits | Small drill bits used to create holes in the PCB |
Step-by-Step Guide to Making PCBs at Home
Step 1: Design the PCB
The first step in PCB fabrication is to design the circuit and create the PCB layout. You can use various software tools for this purpose, such as KiCad, Eagle, or Altium Designer. These tools allow you to create schematic diagrams, assign footprints to components, and route the traces on the board.
When designing your PCB, keep the following considerations in mind:
- Choose an appropriate board size and shape based on your project requirements.
- Ensure that the component footprints match the actual components you will be using.
- Follow good PCB design practices, such as maintaining appropriate trace widths and clearances, avoiding sharp angles, and providing proper grounding.
- If your PCB will be double-sided, make sure to properly align the layers and add vias for inter-layer connections.
Step 2: Print the PCB Design
Once your PCB design is complete, you need to print it onto transfer paper using a laser printer. It is important to use a laser printer rather than an inkjet printer, as the toner from a laser printer is more suitable for the heat transfer process.
Before printing, make sure to mirror the PCB design so that it will be transferred correctly onto the copper-clad board. Also, adjust the printer settings to ensure the highest possible print quality and toner density.
Step 3: Transfer the Design onto the Copper-Clad Board
To transfer the printed design onto the copper-clad board, follow these steps:
- Clean the copper-clad board with steel wool or fine sandpaper to remove any oxidation and improve adhesion.
- Place the printed transfer paper onto the copper side of the board, with the toner side facing down.
- Apply heat and pressure using a clothes iron set to its highest temperature setting without steam. Press the iron firmly onto the transfer paper for several minutes, ensuring even coverage.
- Allow the board to cool, then carefully peel off the transfer paper. The toner should have transferred onto the copper surface.
Step 4: Apply Photoresist Film
To create the etching mask, you need to apply a photoresist film onto the copper-clad board. Photoresist film is a light-sensitive material that hardens when exposed to UV light. There are two types of photoresist film: positive and negative. Positive photoresist becomes soluble when exposed to UV light, while negative photoresist becomes insoluble.
To apply the photoresist film:
- Cut a piece of photoresist film slightly larger than your PCB.
- Remove the protective backing from the film and carefully place it onto the copper side of the board, ensuring that there are no air bubbles or wrinkles.
- Use a squeegee or roller to firmly press the film onto the board and remove any remaining air bubbles.
Step 5: Expose the Photoresist
With the photoresist film applied, you need to expose it to UV light to harden the areas that will form the traces on your PCB. To do this, place your PCB in a UV exposure unit for the recommended exposure time (usually a few minutes, depending on the photoresist and UV intensity).
If you don’t have a UV exposure unit, you can use the sun as a UV source. Place your PCB in direct sunlight for about 15-20 minutes, depending on the intensity of the sunlight.
Step 6: Develop the Photoresist
After exposing the photoresist, you need to develop it to remove the unhardened areas. This is done by immersing the PCB in a developer solution for a few minutes, following the manufacturer’s instructions.
The developer solution will dissolve the unhardened photoresist, leaving behind the hardened areas that form your PCB traces. Gently agitate the board in the solution to ensure even development.
Step 7: Etch the PCB
With the photoresist mask in place, you can now etch away the unwanted copper from the board. There are two common methods for etching PCBs at home: ferric chloride and copper chloride.
Ferric Chloride Etching
Ferric chloride is a popular choice for PCB Etching due to its effectiveness and availability. To etch your PCB using ferric chloride:
- Prepare a ferric chloride solution according to the manufacturer’s instructions.
- Place your PCB in the etching tank and pour the ferric chloride solution over it, ensuring that the board is completely submerged.
- Agitate the solution gently to promote even etching. The etching process typically takes 10-30 minutes, depending on the strength of the solution and the thickness of the copper.
- Periodically check the progress of the etching. When all the unwanted copper has been removed, remove the board from the solution and rinse it thoroughly with water.
Copper Chloride Etching
Copper chloride is another option for PCB etching that is less hazardous than ferric chloride. To prepare a copper chloride etching solution:
- Dissolve 150 grams of hydrochloric acid (30% concentration) in 1 liter of water.
- Add 50 grams of hydrogen peroxide (3% concentration) to the solution.
- Gradually stir in 65 grams of copper(II) chloride dihydrate. The solution will turn green as the copper chloride dissolves.
To etch your PCB using copper chloride, follow the same steps as for ferric chloride etching.
Step 8: Remove the Photoresist Mask
After etching, you need to remove the hardened photoresist mask from the PCB. This can be done using a photoresist stripper solution or by gently scrubbing the board with steel wool or fine sandpaper.
Be sure to clean the board thoroughly to remove any remaining photoresist or etchant residue.
Step 9: Drill Holes and Apply Solder Mask (Optional)
If your PCB requires through-hole components or mounting holes, you’ll need to drill them using a drill or drill press and appropriately sized drill bits. Be careful to align the holes accurately with the pads on your PCB design.
Optionally, you can apply a solder mask to your PCB to protect the copper traces from oxidation and prevent accidental short circuits during soldering. Solder mask is available in liquid or film form and can be applied using a similar process to the photoresist film.
Step 10: Cut and Finish the PCB
Finally, cut your PCB to its final size and shape using a saw or router. If desired, you can also apply a silkscreen layer to add component labels and other markings to your board.
Your homemade PCB is now ready for component assembly and soldering!
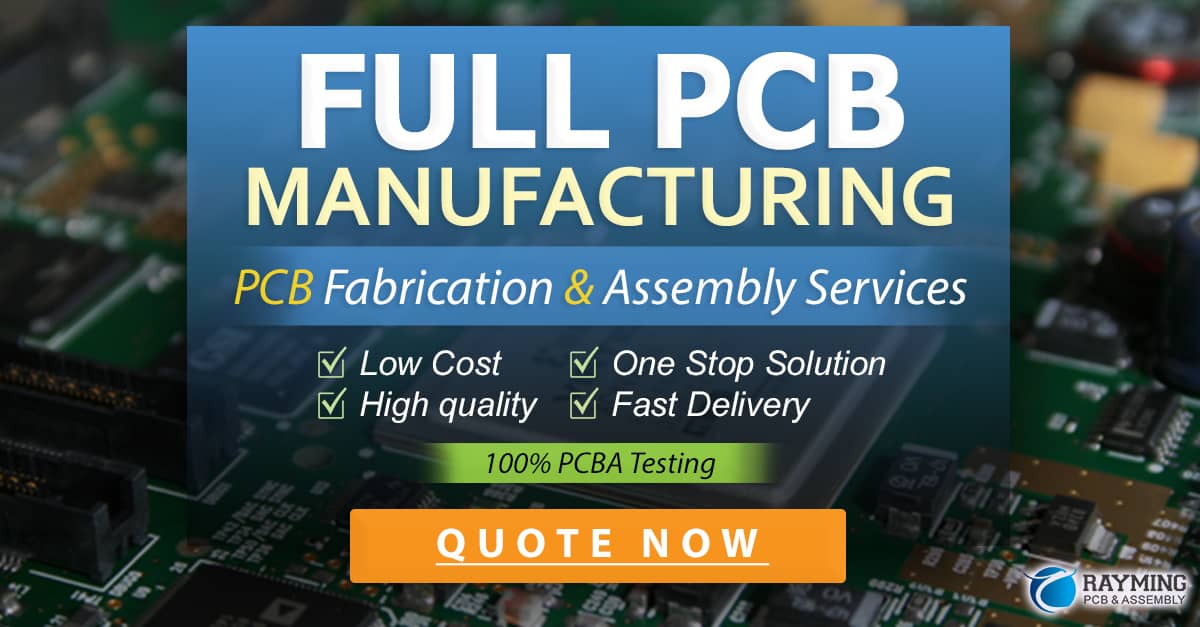
Frequently Asked Questions (FAQ)
1. Can I make multi-layer PCBs at home?
Making multi-layer PCBs at home is more challenging than single or double-sided boards due to the additional alignment and lamination steps required. While it is possible with specialized equipment and materials, it is not typically recommended for beginners. If your project requires a multi-layer PCB, it may be more practical to order it from a professional manufacturer.
2. What safety precautions should I take when making PCBs at home?
PCB fabrication involves the use of chemicals that can be harmful if mishandled. Always work in a well-ventilated area, wear protective gloves and eyewear, and avoid breathing in fumes from the etching or developer solutions. Properly dispose of used solutions and waste materials in accordance with local regulations. If you’re unsure about the safety of any process or material, consult the manufacturer’s instructions or seek advice from an experienced professional.
3. Can I reuse the etching solution?
Etching solutions can be reused multiple times, but their effectiveness will gradually diminish as the dissolved copper content increases. When the etching process becomes noticeably slower or less effective, it’s time to replace the solution. Be sure to dispose of used etching solutions properly, as they can be harmful to the environment.
4. How can I improve the quality of my homemade PCBs?
To improve the quality of your homemade PCBs, consider the following tips:
- Use high-quality materials, such as clean copper-clad boards and fresh chemicals.
- Ensure that your PCB design follows good practices, such as appropriate trace widths and clearances.
- Maintain a clean and dust-free work environment to minimize contamination of your boards.
- Practice proper alignment and exposure techniques when transferring your design and applying the photoresist.
- Regularly maintain and calibrate your equipment, such as the UV exposure unit and etching tank.
5. Are there any alternatives to the photoresist method for making PCBs at home?
Yes, there are several alternative methods for making PCBs at home, including:
- Toner transfer method: This involves printing your PCB design onto glossy paper using a laser printer, then transferring the toner onto the copper-clad board using heat and pressure.
- Sharpie or resist pen method: This method uses a permanent marker or special resist pen to draw the PCB traces directly onto the copper-clad board, then etching away the unmarked areas.
- CNC milling: If you have access to a CNC machine, you can use it to mill away the unwanted copper from your board, leaving behind the desired traces.
Each method has its own advantages and limitations, so choose the one that best suits your skills, resources, and project requirements.
Conclusion
Making PCBs at home is a rewarding and educational experience that can save you time and money in your electronics projects. By following the steps outlined in this article and taking the necessary safety precautions, you can create professional-quality PCBs in the comfort of your own home.
Remember to start with simple designs and gradually work your way up to more complex boards as you gain experience and confidence in your PCB fabrication skills. With practice and patience, you’ll soon be producing Custom PCBs for all your electronics needs.
0 Comments