Benefits of Custom PCBs
Tailored to Your Exact Requirements
The biggest advantage of custom PCBs is that they can be designed and manufactured to your precise specifications and needs. Some of the ways you can customize a PCB include:
- Board shape and size
- Number of layers
- Copper weight/thickness
- Solder mask color
- Silkscreen
- Surface finish (e.g. HASL, ENIG, OSP)
- Unique cutouts/holes
By tailoring the PCB to your exact requirements, you can optimize the size, cost, and performance for your specific application. Generic PCBs force you to design around their fixed specifications.
Optimized Layout for Your Circuit
With a custom PCB, you have full control over the component placement and routing of traces between components. This allows you to optimize the PCB layout for your particular circuit design.
Benefits of an optimized PCB layout include:
- Minimized trace lengths and loop areas
- Reduced crosstalk and EMI
- Better signal integrity
- Efficient use of board space
- Easier assembly and manufacturing
Thoughtful PCB layout is essential for circuits sensitive to noise or with high-speed signals. It’s difficult to achieve an ideal layout with the constraints of a generic PCB.
Cost Savings in Volume
For small quantities, custom PCBs are usually more expensive than generic boards on a per-unit basis, due to the initial setup and tooling charges. However, those fixed costs get amortized over larger production runs.
Quantity | Generic PCB Cost | Custom PCB Cost |
---|---|---|
1 | $5 | $100 |
10 | $50 | $150 |
100 | $500 | $300 |
1000 | $5000 | $1000 |
As the table illustrates, custom boards become the more economical choice at higher volumes. The per-unit cost of custom PCBs drops significantly with scale.
Additionally, a custom PCB tailored to your requirements may reduce the total number of boards and components needed, providing further cost savings.
Intellectual Property Protection
An underappreciated benefit of custom PCBs is the ability to better protect your intellectual property. With a generic PCB, your proprietary circuitry is out in the open for anyone to see and potentially copy.
A custom PCB allows you to implement the following obfuscation techniques:
- Burying sensitive traces on inner layers
- Using blind/buried vias
- Specifying a black solder mask to hide traces
- Omitting or obscuring silkscreen labels
While determined attackers may still be able to reverse engineer a custom PCB, the above methods help protect your IP and increase the difficulty of copying your designs.
Limitations of Custom PCBs
Higher Upfront Costs
As mentioned previously, custom PCBs have higher initial costs compared to generic boards, especially for low quantities. Design and tooling charges can range from hundreds to thousands of dollars.
For smaller businesses and hobbyists, these upfront expenses may be prohibitively high. Generic PCBs are often the only economical option for one-off projects and prototypes.
Longer Lead Times
Fabricating custom PCBs takes longer than buying standard, in-stock boards. There are several reasons for this:
- Time to finalize and double-check the PCB design
- Back-and-forth communication with the manufacturer on specifications and files
- Production steps like making the photomask, drilling, plating, etching, etc.
- Inspection, testing, and shipping
Typical lead times for custom PCBs range from 1-3 weeks, although expedited options are sometimes available for a premium. In contrast, generic boards can often be obtained off-the-shelf or with lead times of a few days.
Minimum Order Quantities
Most custom PCB fabricators have minimum order quantity (MOQ) requirements, often around 5-10 pieces. Low-volume prototyping services are available that will produce smaller quantities, but they command substantially higher per-unit pricing.
Hobbyists and makers who only need one or two boards are usually better served by a generic PCB. However, those designing boards for commercial products need to factor MOQs into their production planning.
Potential for Design Errors
Laying out a custom PCB provides great flexibility, but the downside is that the design burden rests entirely on you. A single mistake in the PCB design can render the entire batch of boards useless.
Common PCB design errors include:
- Incorrect footprints
- Broken/missing connections
- Failing to follow manufacturer DRC guidelines
- Inadequate hole/via sizes
- Mismatched layer stackup
While some design errors can be corrected with manual rework, more serious mistakes may require a complete re-spin of the PCB – an expensive and time-consuming ordeal.
FAQ
What is the typical cost of a custom PCB?
The cost of custom PCBs depends on many factors like quantity, board size, layer count, specifications, and additional services. Setup and tooling fees can range from $100 to over $1000. Per-unit prices may vary from a few dollars to hundreds of dollars based on complexity. It’s best to get quotes from multiple PCB manufacturers.
How long does it take to get custom PCBs made?
Standard lead times for custom PCB orders are usually 1-3 weeks, although this can stretch to over a month for complex, high-reliability boards. Most fabs offer expedited services with 1-5 day turns for a 20-100% upcharge. Design and testing time should also be factored in.
What information is needed to order custom PCBs?
At a minimum, PCB manufacturers need the “Gerber” files that describe the copper artwork for each layer, drill file, and a fabrication drawing with all the board specifications like material, thickness, color, finish, etc. Additional documentation like a bill of materials, centroid file, and 3D STEP model may be required for turnkey assembly.
What are some reliable custom PCB manufacturers?
Some well-regarded custom PCB fabs include Advanced Circuits, Sunstone Circuits, OSH Park, Bay Area Circuits, Sierra Circuits, and Imagineering. For overseas production, popular choices are JLCPCB, PCBWay, Seeed Studio, and Gold Phoenix PCB. However, there are countless other reliable manufacturers.
When should I consider using a custom PCB vs. a generic board?
Custom PCBs are recommended when you have specific size, shape, layer, or performance requirements that can’t be met with off-the-shelf boards. They provide the most benefit in volume production and for optimizing your PCB layout. Generic PCBs are better suited for one-off prototypes, very low quantities, and hobbyist projects.
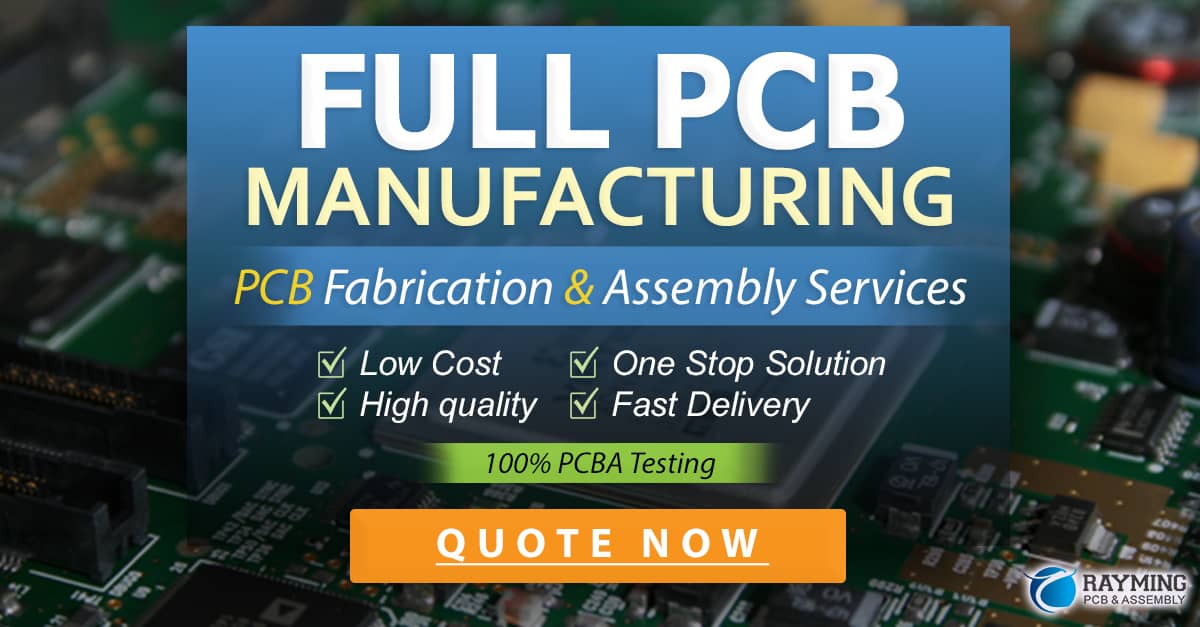
Conclusion
In summary, custom PCBs offer several compelling advantages like tailored specifications, optimized layouts, IP protection, and volume cost savings. However, they also have higher upfront costs, longer lead times, minimum order quantities, and the potential for costly design errors.
Whether a custom or generic PCB is the right choice depends on the specific needs, budget, and production scale of your project. By weighing the benefits and limitations, you can make an informed decision on the best approach for your PCB needs.
0 Comments