What is PCBA?
PCBA stands for Printed Circuit Board Assembly. It refers to the process of attaching electronic components to a printed circuit board (PCB) to create a functional Electronic Assembly. The PCBA process involves several steps, including placing components on the PCB, soldering them in place, and testing the completed assembly to ensure it functions as intended.
PCBAs are used in a wide range of electronic devices, from smartphones and laptops to medical equipment and aerospace systems. They provide a compact, reliable, and cost-effective way to interconnect electronic components and create complex circuits.
Types of PCBA
There are several types of PCBA, each with its own unique characteristics and applications. Here are the main types of PCBA:
Through-hole PCBA
Through-hole PCBA is the traditional method of assembling PCBs. In this process, components with long leads are inserted into holes drilled in the PCB and soldered to pads on the opposite side of the board. Through-hole PCBA is known for its strength and reliability, making it well-suited for applications that require high durability, such as military and aerospace systems.
Surface Mount PCBA
Surface mount PCBA is a more modern method of assembling PCBs. In this process, components are placed directly on the surface of the PCB and soldered in place using a reflow oven. Surface mount components are smaller and have shorter leads than through-hole components, allowing for higher component density and smaller PCBs. Surface mount PCBA is widely used in consumer electronics, such as smartphones and laptops.
Mixed Technology PCBA
Mixed technology PCBA combines both through-hole and surface mount components on the same PCB. This approach allows for the use of specialized components that are only available in through-hole packages, while still taking advantage of the space-saving benefits of surface mount technology. Mixed technology PCBA is often used in complex industrial and medical devices.
Flexible PCBA
Flexible PCBA uses a flexible substrate, such as polyimide or polyester, instead of a rigid PCB. This allows the PCBA to bend and flex without breaking, making it ideal for applications that require a high degree of flexibility, such as wearable electronics and automotive systems.
Rigid-Flex PCBA
Rigid-Flex PCBA combines rigid PCBs with flexible interconnects to create a single, integrated assembly. This approach allows for the creation of complex, three-dimensional assemblies that can be folded or shaped to fit into tight spaces. Rigid-flex PCBA is often used in aerospace, military, and medical applications.
Applications of PCBA
PCBAs are used in a wide range of industries and applications. Here are some of the most common applications of PCBA:
Consumer Electronics
PCBAs are used in virtually all consumer electronics, from smartphones and laptops to televisions and gaming consoles. They provide the interconnects and circuitry needed to power and control these devices, while also enabling advanced features such as wireless connectivity and high-resolution displays.
Automotive Electronics
PCBAs are increasingly used in automotive electronics, from engine control modules and infotainment systems to advanced driver assistance systems (ADAS) and autonomous vehicles. They provide the reliable, high-performance interconnects needed to support these complex systems in the harsh automotive environment.
Medical Devices
PCBAs are used in a wide range of medical devices, from patient monitoring systems and diagnostic equipment to implantable devices such as pacemakers and insulin pumps. They provide the precise, reliable interconnects needed to ensure the safety and efficacy of these life-critical devices.
Industrial Automation
PCBAs are used in industrial automation systems, such as programmable logic controllers (PLCs), human-machine interfaces (HMIs), and sensor networks. They provide the rugged, reliable interconnects needed to withstand the harsh conditions of industrial environments, while also enabling advanced features such as remote monitoring and predictive maintenance.
Aerospace and Defense
PCBAs are used in a wide range of aerospace and defense applications, from satellites and aircraft to military communications and radar systems. They provide the high-reliability, high-performance interconnects needed to support these mission-critical systems in the extreme environments of space and the battlefield.
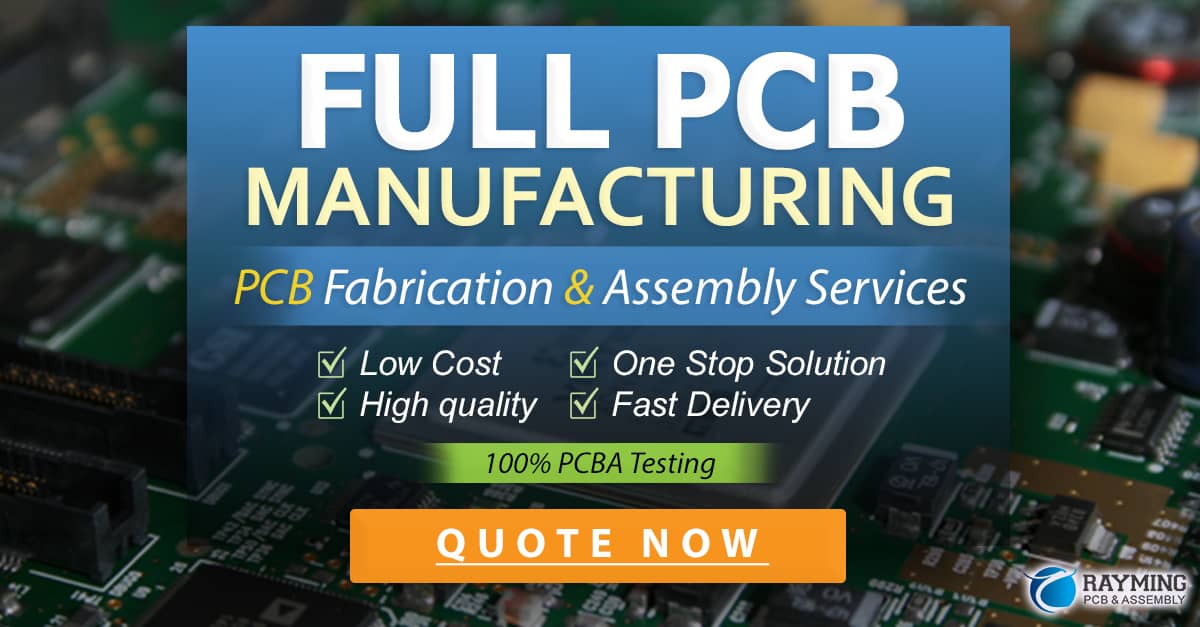
The PCBA Process
The PCBA process involves several steps, from design and fabrication to assembly and testing. Here is an overview of the typical PCBA process:
Step 1: Design
The first step in the PCBA process is to design the PCB and select the components that will be used in the assembly. This involves creating a schematic diagram that shows the electrical connections between components, as well as a layout that shows the physical placement of components on the PCB. The design must also take into account factors such as signal integrity, power distribution, and thermal management.
Step 2: Fabrication
Once the design is complete, the next step is to fabricate the PCB. This involves creating a photomask of the PCB layout, which is used to transfer the circuit pattern onto a copper-clad substrate. The substrate is then etched to remove the unwanted copper, leaving only the desired circuit pattern. Holes are drilled in the PCB to accommodate through-hole components, and solder mask and silkscreen are applied to protect the circuit and provide labeling.
Step 3: Component Placement
After the PCB is fabricated, the next step is to place the components on the board. For through-hole components, this involves inserting the leads into the holes in the PCB and bending them over to secure the component in place. For surface mount components, a pick-and-place machine is used to accurately place the components on the pads on the surface of the PCB.
Step 4: Soldering
Once the components are placed, they must be soldered to the PCB to create electrical connections. For through-hole components, this involves applying solder to the leads and pads on the opposite side of the board, typically using a wave soldering machine. For surface mount components, a reflow oven is used to melt the solder paste and create a bond between the component and the pad.
Step 5: Inspection and Testing
After soldering, the PCBA undergoes a series of inspections and tests to ensure that it functions as intended. This may include visual inspection to check for defects such as bridging or tombstoning, as well as electrical testing to verify that the assembly meets the required specifications for resistance, capacitance, and other parameters. Functional testing may also be performed to ensure that the PCBA performs as expected in its intended application.
Step 6: Coating and Potting
In some cases, the PCBA may require additional protection from environmental factors such as moisture, dust, or vibration. This can be achieved through the application of conformal coating, which is a thin layer of polymer that conforms to the surface of the PCBA and provides a barrier against contaminants. Potting, which involves encapsulating the PCBA in a solid compound such as epoxy or silicone, may also be used for added protection in harsh environments.
Step 7: Final Assembly
Once the PCBA is complete, it may be assembled into a larger system or product. This may involve mounting the PCBA in an enclosure, connecting it to other subsystems or components, and performing final testing and calibration to ensure that the entire system functions as intended.
PCBA Quality Control
Ensuring the quality of PCBAs is critical to the reliability and performance of the end product. Here are some of the key quality control measures used in PCBA Manufacturing:
Incoming Inspection
Before components are used in the PCBA process, they must undergo incoming inspection to ensure that they meet the required specifications for quality and performance. This may involve visual inspection, electrical testing, and other verification methods to detect defects or variations that could affect the final assembly.
In-Process Inspection
During the PCBA process, various inspections are performed to ensure that each step is completed correctly and that the assembly meets the required quality standards. This may include visual inspection of solder joints, automated optical inspection (AOI) to detect defects such as missing or misaligned components, and X-ray inspection to detect hidden defects such as voids or cracks in solder joints.
Functional Testing
After the PCBA is complete, functional testing is performed to ensure that it performs as expected in its intended application. This may involve simulating the operating conditions of the end product and measuring key performance parameters such as power consumption, signal integrity, and electromagnetic compatibility (EMC).
Environmental Testing
Depending on the intended application, PCBAs may also undergo environmental testing to ensure that they can withstand the expected operating conditions. This may include temperature cycling, humidity testing, vibration testing, and other methods to simulate the stresses and strains of the end-use environment.
Traceability
To ensure that any quality issues can be quickly identified and addressed, PCBAs must be traceable throughout the manufacturing process. This involves assigning unique identifiers to each PCBA and recording key process parameters such as component lot numbers, solder paste batch numbers, and inspection results. Traceability allows manufacturers to quickly identify the root cause of any quality issues and take corrective action to prevent future occurrences.
PCBA Manufacturing Challenges
While PCBA manufacturing has become increasingly automated and standardized, there are still several challenges that manufacturers must overcome to ensure high quality and reliability. Here are some of the key challenges in PCBA manufacturing:
Miniaturization
As electronic devices become smaller and more complex, PCBAs must also become smaller and more densely packed with components. This poses challenges for component placement, soldering, and inspection, as well as for thermal management and signal integrity.
High-Mix, Low-Volume Production
Many PCBA manufacturers must be able to quickly adapt to changing customer requirements and produce a wide variety of PCBAs in small quantities. This requires flexible manufacturing processes, quick changeover times, and effective supply chain management to ensure that the right components are available when needed.
Counterfeit Components
The proliferation of counterfeit electronic components poses a significant risk to PCBA manufacturers and end users. Counterfeit components may not meet the required specifications for quality and reliability, leading to premature failure or even safety hazards. Manufacturers must have robust processes in place to detect and prevent the use of counterfeit components, including traceability and testing.
Environmental Regulations
PCBAs are subject to a wide range of environmental regulations, including restrictions on hazardous substances such as lead, cadmium, and mercury. Manufacturers must ensure that their processes and materials comply with these regulations, which can require significant investment in new equipment and training.
Supply Chain Disruptions
The global nature of the electronics supply chain means that PCBA manufacturers are vulnerable to disruptions caused by natural disasters, geopolitical events, and other factors beyond their control. Manufacturers must have contingency plans in place to ensure continuity of supply and minimize the impact of disruptions on their customers.
PCBA Manufacturing Trends
The PCBA manufacturing industry is constantly evolving to meet the changing needs of customers and take advantage of new technologies. Here are some of the key trends shaping the future of PCBA manufacturing:
Industry 4.0
Industry 4.0 refers to the integration of advanced technologies such as automation, artificial intelligence, and the Internet of Things (IoT) into manufacturing processes. For PCBA manufacturers, this means using data analytics and machine learning to optimize processes, predict maintenance needs, and improve quality control.
3D Printing
3D printing technology is increasingly being used in PCBA manufacturing to create custom jigs and fixtures, as well as to prototype new designs. In the future, 3D printing may also be used to create functional PCBAs with embedded components and circuitry.
Advanced Materials
New materials such as graphene, carbon nanotubes, and conductive inks are being developed for use in PCBAs. These materials offer improved performance, flexibility, and sustainability compared to traditional materials such as copper and solder.
Sustainable Manufacturing
As concerns about the environmental impact of electronics manufacturing continue to grow, PCBA manufacturers are under increasing pressure to adopt sustainable practices. This includes using renewable energy sources, reducing waste and emissions, and designing products for recyclability and reuse.
Reshoring
The COVID-19 pandemic has highlighted the risks of relying on global supply chains for critical components and products. As a result, some PCBA manufacturers are shifting production back to their home countries or regions to improve supply chain resilience and reduce lead times.
FAQ
What is the difference between PCB and PCBA?
A PCB (printed circuit board) is the bare board with the copper traces and pads, but without any components attached. A PCBA (printed circuit board assembly) is a PCB with the components soldered onto it, making it a functional electronic assembly.
What are the advantages of surface mount technology (SMT) over through-hole technology?
SMT offers several advantages over through-hole technology, including:
- Smaller component size and higher component density
- Faster assembly and soldering
- Lower cost due to automated processes
- Improved reliability due to fewer solder joints
What is the purpose of solder mask on a PCB?
Solder mask is a thin layer of polymer that is applied to the surface of a PCB to protect the copper traces and pads from oxidation and prevent solder bridges from forming between adjacent pads. Solder mask also provides electrical insulation and improves the appearance of the PCB.
What is the difference between reflow soldering and wave soldering?
Reflow soldering is used for surface mount components and involves applying solder paste to the pads on the PCB, placing the components onto the paste, and then heating the entire assembly in a reflow oven to melt the solder and create a bond between the component and the pad.
Wave soldering is used for through-hole components and involves passing the PCB over a wave of molten solder, which flows through the holes in the board and creates a bond between the component leads and the pads on the opposite side of the board.
What is the purpose of a pick-and-place machine in PCBA manufacturing?
A pick-and-place machine is used to automatically place surface mount components onto the pads on a PCB. The machine uses a vacuum nozzle to pick up the component from a feeder and place it accurately onto the solder paste on the pad. Pick-and-place machines can place components at high speeds and with high precision, reducing the time and cost of PCBA manufacturing.
0 Comments