Understanding Through-hole PCB Technology
What is a Through-hole PCB?
A through-hole PCB is a printed circuit board that features components with long leads that are inserted into holes drilled through the board. The leads are then soldered to pads on the opposite side of the board to create a secure electrical connection. This type of PCB is also known as a plated-through-hole (PTH) board, as the holes are typically plated with a conductive material to enhance the connection between the component leads and the copper traces on the board.
Advantages of Through-hole PCB Assembly
Through-hole PCB assembly offers several advantages over other methods, such as surface-mount technology:
-
Mechanical Strength: Through-hole components are held in place by their leads, which are soldered to the board. This provides a strong mechanical connection that can withstand vibration and physical stress better than surface-mounted components.
-
Ease of Repair: Through-hole components can be easily replaced or repaired using manual soldering techniques, making it a preferred choice for applications that require frequent maintenance or modifications.
-
Lower Setup Costs: Through-hole PCB assembly requires less sophisticated equipment and tooling compared to SMT, which can result in lower setup costs for low-volume production runs.
-
Compatibility with High-power Components: Through-hole technology is well-suited for high-power components, such as transformers and large capacitors, which generate significant heat and require a more robust connection to the board.
Disadvantages of Through-hole PCB Assembly
While through-hole PCB assembly has its advantages, it also has some drawbacks compared to surface-mount technology:
-
Lower Component Density: Through-hole components occupy more space on the board due to their larger size and the need for drilled holes, which limits the achievable component density compared to SMT.
-
Increased Manufacturing Time: Through-hole PCB assembly is generally slower than SMT, as components must be inserted manually or with the help of specialized equipment, and the soldering process is more time-consuming.
-
Higher Assembly Costs: For high-volume production, through-hole PCB assembly can be more expensive than SMT due to the increased labor and time required.
-
Limited Design Flexibility: Through-hole components have fixed lead spacings and sizes, which can limit the design flexibility and the ability to minimize the overall PCB size.
Through-hole PCB Assembly Process
The through-hole PCB assembly process typically involves the following steps:
-
PCB Fabrication: The PCB is designed and fabricated with the necessary holes for through-hole components, as well as any required copper traces and pads.
-
Component Insertion: Through-hole components are inserted into the corresponding holes on the PCB, either manually or using automated insertion machines.
-
Soldering: The component leads are soldered to the pads on the opposite side of the board, creating a secure electrical and mechanical connection. This can be done using manual soldering techniques, such as hand soldering or wave soldering, or with the help of automated soldering machines.
-
Inspection and Testing: The assembled PCB undergoes visual inspection and electrical testing to ensure proper functionality and adherence to quality standards.
-
Cleaning and Finishing: The PCB is cleaned to remove any flux residue or contaminants, and any necessary surface finishes, such as conformal coating or potting, are applied.
Manual vs. Automated Through-hole PCB Assembly
Through-hole PCB assembly can be performed manually or with the help of automated equipment, depending on the production volume, component types, and available resources.
-
Manual Through-hole PCB Assembly: This method involves hand-placing components into the PCB and soldering them using a soldering iron. Manual assembly is suitable for low-volume production, prototyping, or when dealing with unusual component shapes or sizes that cannot be easily handled by automated equipment.
-
Automated Through-hole PCB Assembly: Automated assembly utilizes specialized machines to insert components and perform soldering. Two common automated techniques are:
a. Axial and Radial Lead Component Insertion: Machines designed for inserting axial and radial lead components automatically cut, bend, and insert the leads into the appropriate holes on the PCB.
b. Wave Soldering: In this process, the PCB with inserted components is passed over a molten solder wave, which creates a solid connection between the component leads and the pads on the board.
Automated through-hole PCB assembly is more suitable for high-volume production, as it offers increased speed, consistency, and efficiency compared to manual methods.
Comparing Through-hole and Surface-mount Technology
While through-hole PCB assembly remains a viable option for many applications, surface-mount technology (SMT) has gained widespread adoption in recent years. Here’s a comparison of the two technologies:
Factor | Through-hole PCB Assembly | Surface-mount Technology (SMT) |
---|---|---|
Component Density | Lower | Higher |
Manufacturing Speed | Slower | Faster |
Assembly Costs | Higher for high-volume | Lower for high-volume |
Mechanical Strength | Stronger | Weaker |
Ease of Repair | Easier | More difficult |
Design Flexibility | Limited | Greater |
Suitable Applications | High-power, low-volume | High-volume, compact designs |
In many cases, a combination of through-hole and surface-mount components can be used on the same PCB to leverage the advantages of both technologies. This is known as a mixed-technology or hybrid PCB assembly.
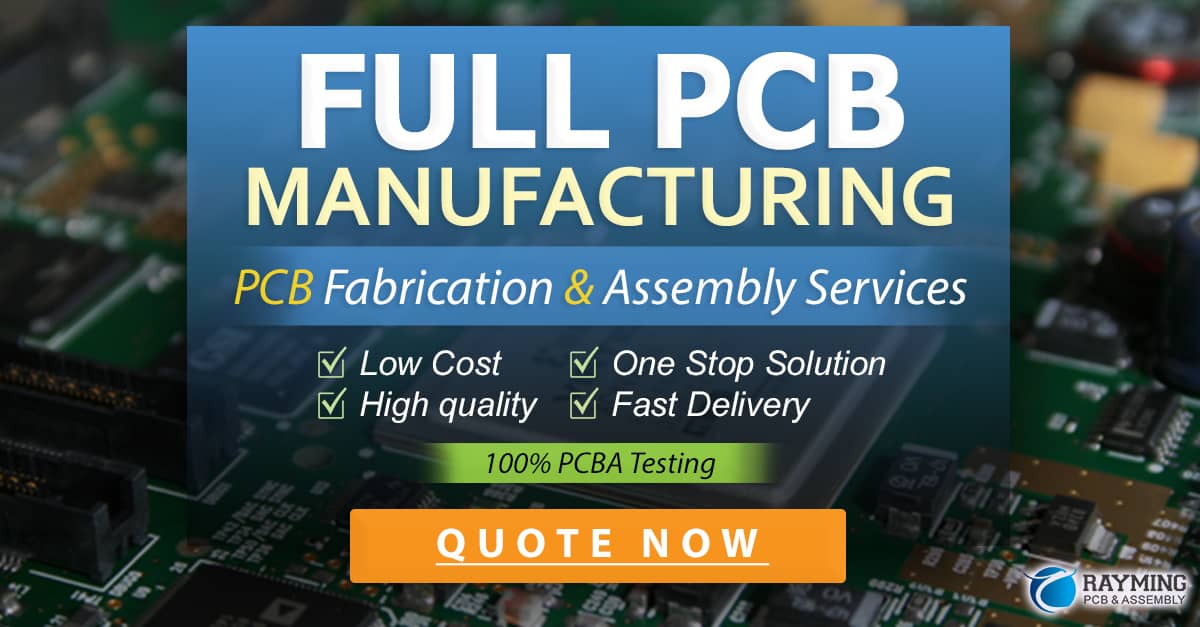
Frequently Asked Questions (FAQ)
-
Q: What is the difference between through-hole and surface-mount PCB assembly?
A: Through-hole PCB assembly involves inserting component leads through holes in the board and soldering them to pads on the opposite side, while surface-mount assembly places components directly onto pads on the surface of the board. -
Q: When should I choose through-hole PCB assembly over surface-mount technology?
A: Through-hole PCB assembly is a good choice when mechanical strength, ease of repair, or compatibility with high-power components are prioritized over component density and manufacturing speed. It is also suitable for low-volume production or prototyping. -
Q: Can through-hole and surface-mount components be used on the same PCB?
A: Yes, it is possible to design a mixed-technology or hybrid PCB that incorporates both through-hole and surface-mount components, allowing designers to take advantage of the benefits of both technologies. -
Q: Is through-hole PCB assembly more expensive than surface-mount assembly?
A: For high-volume production, through-hole PCB assembly can be more expensive due to the increased labor and time required. However, for low-volume production or prototyping, through-hole assembly may have lower setup costs compared to surface-mount technology. -
Q: What are the main steps involved in the through-hole PCB assembly process?
A: The main steps in through-hole PCB assembly include PCB fabrication, component insertion, soldering, inspection and testing, and cleaning and finishing. These steps can be performed manually or with the help of automated equipment, depending on the production volume and available resources.
In conclusion, through-hole PCB assembly remains a reliable and cost-effective solution for many electronic applications, particularly those requiring high mechanical strength, ease of repair, or compatibility with high-power components. While surface-mount technology offers advantages in terms of component density and manufacturing speed, through-hole assembly continues to play a significant role in the electronics industry, especially for low-volume production, prototyping, and applications with specific requirements.
0 Comments