Introduction to PCB Manufacturing
Printed Circuit Boards (PCBs) are the backbone of modern electronics. They are used in almost every electronic device, from smartphones and laptops to medical equipment and aerospace systems. PCB manufacturing is a complex process that involves several steps, each requiring precision and attention to detail. In this article, we will delve into the details of the PCB manufacturing process, exploring each step and its importance in creating high-quality, reliable PCBs.
What is a PCB?
A PCB is a flat board made of insulating material, such as fiberglass or plastic, with conductive pathways printed on its surface. These pathways, known as traces, connect various electronic components, such as resistors, capacitors, and integrated circuits (ICs), to form a complete electronic circuit. PCBs provide a stable and compact platform for electronic components, enabling the creation of complex electronic devices in a relatively small space.
Advantages of using PCBs
PCBs offer several advantages over traditional point-to-point wiring:
- Compact design: PCBs allow for the miniaturization of electronic devices by providing a dense, organized layout for components.
- Increased reliability: The stable, fixed connections provided by PCBs reduce the risk of loose connections and short circuits.
- Improved signal integrity: Properly designed PCBs minimize electromagnetic interference (EMI) and ensure clean, consistent signal transmission.
- Reduced assembly time: PCBs simplify the assembly process, as components can be easily soldered onto the board.
- Cost-effective: Mass production of PCBs is cost-effective, as the process can be largely automated.
The PCB Manufacturing Process
The PCB manufacturing process consists of several steps, each contributing to the creation of a high-quality, functional PCB. The main steps include:
- PCB Design
- PCB Fabrication
- PCB Assembly
- PCB Testing and Inspection
Let’s explore each of these steps in detail.
Step 1: PCB Design
The PCB manufacturing process begins with the design phase. This step involves creating a detailed layout of the electronic circuit, specifying the placement of components and the routing of traces. PCB design is typically done using specialized software called Electronic Design Automation (EDA) tools.
Schematic Capture
The first step in PCB design is schematic capture. This involves creating a diagram that represents the electrical connections between components in the circuit. The schematic serves as a blueprint for the PCB layout and helps ensure that the circuit functions as intended.
PCB Layout
Once the schematic is complete, the next step is to create the PCB layout. This involves determining the physical placement of components on the board and routing the traces between them. The layout must take into account various factors, such as:
- Component size and shape
- Required trace width and spacing
- Signal integrity
- Thermal management
- Manufacturing constraints
The PCB layout is typically created using EDA software, which provides tools for component placement, trace routing, and design rule checking (DRC). DRC ensures that the layout adheres to the manufacturing guidelines and constraints specified by the PCB fabricator.
Gerber File Generation
Once the PCB layout is finalized, the next step is to generate Gerber files. Gerber files are a standard format used by PCB Fabricators to describe the various layers of the PCB, including the copper traces, solder mask, and silkscreen. The EDA software generates a separate Gerber file for each layer of the PCB, which are then sent to the PCB fabricator for manufacturing.
Step 2: PCB Fabrication
PCB fabrication is the process of transforming the PCB design into a physical board. This step involves several sub-processes, each contributing to the creation of a high-quality PCB.
Material Selection
The first step in PCB fabrication is selecting the appropriate base material for the board. The most common base materials used in PCB manufacturing are:
- FR-4: A glass-reinforced epoxy laminate, FR-4 is the most widely used base material for PCBs. It offers good mechanical and electrical properties and is suitable for most applications.
- High-Tg FR-4: This material is similar to standard FR-4 but has a higher glass transition temperature (Tg), making it more suitable for high-temperature applications.
- Polyimide: Polyimide is a high-performance material that offers excellent thermal stability and mechanical strength. It is often used in aerospace and military applications.
- Aluminum: Aluminum PCBs are used in applications that require high thermal conductivity, such as LED lighting and power electronics.
The choice of base material depends on the specific requirements of the application, such as operating temperature, mechanical stress, and electrical performance.
Copper Clad Lamination
Once the base material is selected, the next step is to laminate it with a thin layer of copper on one or both sides. This is typically done using heat and pressure to bond the copper foil to the base material. The thickness of the copper layer can vary depending on the application, with common thicknesses ranging from 0.5 oz to 2 oz per square foot.
Drilling
After the copper-clad laminate is prepared, the next step is to drill holes in the board for through-hole components and vias. Vias are small holes that allow traces to pass from one layer of the PCB to another. The drilling process is typically done using high-speed, computer-controlled drill machines that can accurately create holes of various sizes.
Plating
Once the holes are drilled, the next step is to plate them with a conductive material, typically copper. This is done using a process called electroplating, which involves immersing the board in a copper sulfate solution and applying an electric current. The copper ions in the solution are attracted to the surface of the board and the walls of the drilled holes, forming a thin layer of copper. This process ensures electrical continuity between the layers of the PCB.
Imaging and Etching
The next step in PCB fabrication is to transfer the PCB layout onto the copper-clad laminate. This is done using a photolithographic process, which involves applying a photosensitive resist material to the surface of the board and exposing it to light through a photomask. The photomask contains the PCB layout pattern, and the areas exposed to light become soluble in a developer solution.
After developing, the board is etched using a chemical solution, typically ferric chloride or ammonium persulfate. The etching process removes the unwanted copper, leaving behind the desired traces and pads. The remaining photoresist is then stripped away, revealing the final copper pattern.
Solder Mask Application
Solder mask is a protective layer applied to the surface of the PCB to prevent short circuits and improve the board’s appearance. It is typically a green or black color and is applied using a screen printing process. The solder mask covers the entire board except for the areas where components will be soldered, such as pads and through-holes.
Silkscreen Application
Silkscreen is a layer of text and symbols applied to the surface of the PCB to aid in assembly and provide information about the board. It is typically a white color and is applied using a screen printing process similar to solder mask application. The silkscreen layer includes information such as component labels, polarity markers, and company logos.
Surface Finish
The final step in PCB fabrication is to apply a surface finish to the exposed copper areas of the board. The surface finish serves several purposes, including:
- Protecting the copper from oxidation and corrosion
- Enhancing the solderability of the board
- Improving the electrical and mechanical contact between the components and the board
Common surface finishes include:
- Hot Air Solder Leveling (HASL): A tin-lead alloy is applied to the board and then leveled using hot air to create a flat, solderable surface.
- Immersion Silver (IAg): A thin layer of silver is chemically deposited onto the copper surface, providing good solderability and durability.
- Electroless Nickel Immersion Gold (ENIG): A layer of nickel is chemically deposited onto the copper, followed by a thin layer of gold. ENIG provides excellent solderability, corrosion resistance, and long shelf life.
- Organic Solderability Preservative (OSP): A thin, organic coating is applied to the copper surface to protect it from oxidation and enhance solderability. OSP is a cost-effective alternative to metallic finishes.
The choice of surface finish depends on the specific requirements of the application, such as solderability, shelf life, and cost.
Step 3: PCB Assembly
Once the PCB fabrication process is complete, the next step is to assemble the components onto the board. PCB assembly involves several sub-processes, each contributing to the creation of a functional electronic device.
Component Placement
The first step in PCB assembly is to place the components onto the board. This is typically done using automated pick-and-place machines, which use computer vision and precision robotics to accurately place components on the board. The placement process is guided by the PCB layout, which specifies the exact location and orientation of each component.
Soldering
After the components are placed, the next step is to solder them to the board. Soldering is the process of creating a mechanical and electrical connection between the component leads and the PCB pads. There are two main types of soldering used in PCB assembly:
-
Through-hole soldering: This method involves inserting the component leads through the drilled holes in the board and soldering them to the pads on the opposite side. Through-hole soldering is typically done using a wave soldering machine, which applies a wave of molten solder to the bottom of the board, creating a connection between the leads and the pads.
-
Surface-mount soldering: This method involves placing the components directly onto the pads on the surface of the board and soldering them in place. Surface-mount soldering is typically done using a reflow soldering process, which involves applying solder paste to the pads, placing the components, and then heating the board in a reflow oven to melt the solder and create a connection.
Inspection and Testing
After soldering, the assembled PCBs undergo a series of inspections and tests to ensure that they are functioning correctly and meet the required quality standards. Some common inspection and testing methods include:
- Visual inspection: A visual examination of the board to check for defects such as misaligned components, solder bridges, or missing components.
- Automated Optical Inspection (AOI): A computer-based system that uses high-resolution cameras to automatically inspect the board for defects.
- X-ray inspection: A non-destructive testing method that uses X-rays to inspect the internal structure of the board, such as solder joints and vias.
- In-Circuit Testing (ICT): A test method that uses a bed-of-nails fixture to make electrical contact with the board and test the functionality of individual components and circuits.
- Functional testing: A test method that involves applying power to the board and testing its overall functionality and performance.
Step 4: PCB Testing and Inspection
In addition to the inspections and tests performed during the assembly process, PCBs also undergo a series of final tests and inspections to ensure that they meet the required quality and performance standards. Some common final testing and inspection methods include:
Burn-in Testing
Burn-in testing involves operating the PCB under elevated temperature and voltage conditions for an extended period to identify any early-life failures or defects. This process helps to weed out boards that may fail prematurely in the field, improving overall reliability.
Environmental Testing
Environmental testing involves exposing the PCB to various environmental conditions, such as temperature, humidity, and vibration, to ensure that it can withstand the intended operating environment. This testing helps to identify any design or manufacturing defects that may affect the board’s long-term reliability.
Functional Testing
Functional testing involves testing the overall functionality and performance of the PCB in its intended application. This may involve integrating the board into the final product and testing it under real-world conditions to ensure that it meets the required specifications.
Compliance Testing
Compliance testing involves testing the PCB for compliance with various industry standards and regulations, such as electromagnetic compatibility (EMC), safety, and environmental standards. This testing helps to ensure that the board can be legally sold and used in its intended market.
Advantages of Professional PCB Manufacturing
While it is possible to manufacture PCBs in-house, there are several advantages to outsourcing the manufacturing process to a professional PCB fabricator:
- Access to advanced equipment and processes: Professional PCB fabricators have access to state-of-the-art equipment and processes that may not be available in-house, such as high-density interconnect (HDI) technology and advanced surface finishes.
- Expertise and experience: Professional PCB fabricators have a team of experienced engineers and technicians who are experts in PCB manufacturing. They can provide valuable guidance and support throughout the manufacturing process, helping to ensure the best possible results.
- Scalability and flexibility: Professional PCB fabricators can handle large-scale production runs and can quickly scale up or down to meet changing demand. They can also accommodate a wide range of PCB designs and specifications, providing greater flexibility in product development.
- Cost-effectiveness: Outsourcing PCB manufacturing can be more cost-effective than in-house manufacturing, particularly for small to medium-sized businesses. Professional PCB fabricators can achieve economies of scale and can often provide lower unit costs than in-house manufacturing.
- Quality and reliability: Professional PCB fabricators have strict quality control processes in place to ensure that every board meets the required quality and reliability standards. They also have the necessary certifications and accreditations to demonstrate their commitment to quality, such as ISO 9001 and UL certification.
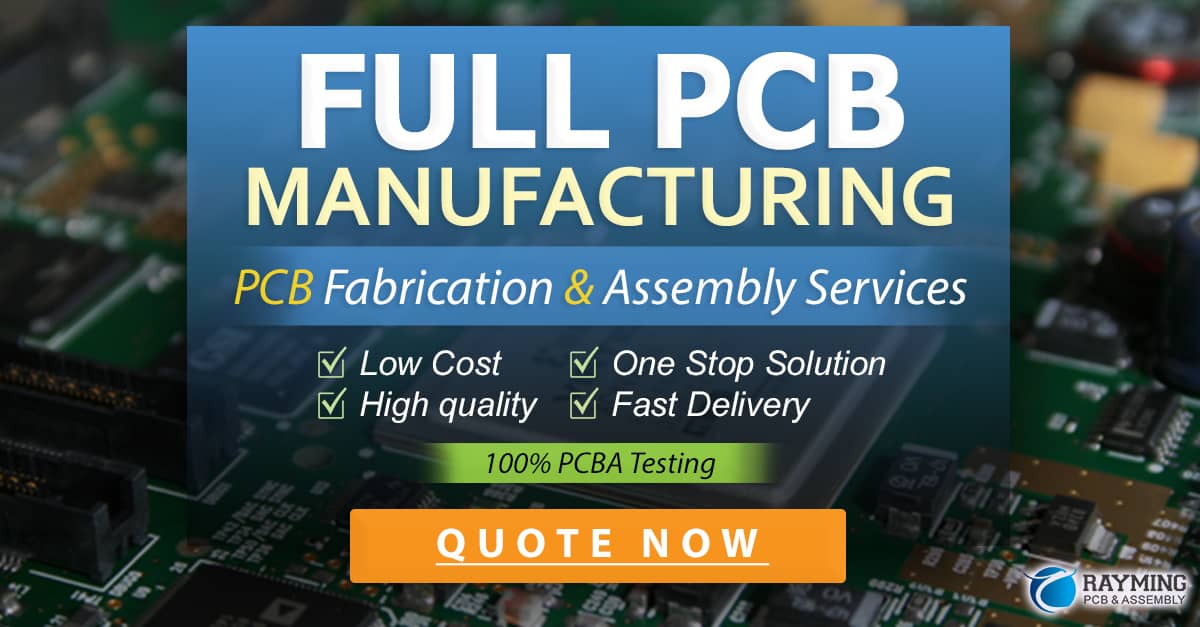
Conclusion
PCB manufacturing is a complex and multi-faceted process that requires precision, expertise, and attention to detail. From the initial design phase to the final testing and inspection, each step in the process plays a critical role in ensuring the quality, reliability, and functionality of the finished product.
By understanding the various steps and processes involved in PCB manufacturing, designers and engineers can make informed decisions about their PCB design and manufacturing strategy. Whether outsourcing to a professional PCB fabricator or manufacturing in-house, a deep understanding of the PCB manufacturing process is essential for creating high-quality, reliable electronic products.
As technology continues to advance and the demand for more complex and sophisticated electronic devices grows, the PCB manufacturing industry will continue to evolve and innovate. By staying up-to-date with the latest developments and best practices in PCB manufacturing, designers and engineers can ensure that their products remain at the forefront of innovation and performance.
Frequently Asked Questions (FAQ)
-
What is the difference between through-hole and surface-mount PCBs?
Through-hole PCBs have components with leads that are inserted into drilled holes in the board and soldered to pads on the opposite side. Surface-mount PCBs have components that are placed directly onto pads on the surface of the board and soldered in place. Surface-mount technology allows for smaller, more compact designs and is more commonly used in modern electronics. -
What is the purpose of solder mask on a PCB?
Solder mask is a protective layer applied to the surface of the PCB to prevent short circuits and improve the board’s appearance. It covers the entire board except for the areas where components will be soldered, such as pads and through-holes. Solder mask helps to prevent solder from bridging between adjacent pads and traces, improving the reliability of the board. -
What is the difference between HASL and ENIG surface finishes?
HASL (Hot Air Solder Leveling) and ENIG (Electroless Nickel Immersion Gold) are two common surface finishes used in PCB manufacturing. HASL involves applying a tin-lead alloy to the board and then leveling it using hot air to create a flat, solderable surface. ENIG involves chemically depositing a layer of nickel onto the copper, followed by a thin layer of gold. ENIG provides better solderability, corrosion resistance, and longer shelf life than HASL, but is more expensive. -
What is the purpose of burn-in testing for PCBs?
Burn-in testing involves operating the PCB under elevated temperature and voltage conditions for an extended period to identify any early-life failures or defects. This process helps to weed out boards that may fail prematurely in the field, improving overall reliability. Burn-in testing is particularly important for PCBs used in critical applications where reliability is paramount, such as aerospace, medical, and military equipment. -
What are the advantages of using a professional PCB fabricator?
Professional PCB fabricators offer several advantages over in-house manufacturing, including access to advanced equipment and processes, expertise and experience, scalability and flexibility, cost-effectiveness, and quality and reliability. They have strict quality control processes in place and have the necessary certifications and accreditations to demonstrate their commitment to quality. Outsourcing PCB manufacturing to a professional fabricator can help to ensure the best possible results for your electronic products.
0 Comments