The printed circuit board (PCB) substrate provides the fundamental platform upon which conductive copper traces mount to route signals between components in an electronic product. This base laminate material insulates conductive paths protecting against shorts while mechanically supporting interconnects.
With demands for higher density PCBs integrating more functionality continually growing across applications, selecting appropriate substratesoptimized for target budgets, signal types, operating environments and manufacturing capabilities proves essential translating circuit designs successfully into fielded systems.
This article explores key technical considerations around PCB substrates to demystify materials decisions enhancing reliability and performance. We’ll examine popular base material types, properties impacting layouts and examine how application needs guide substrate selections in practice.
Substrate Defined
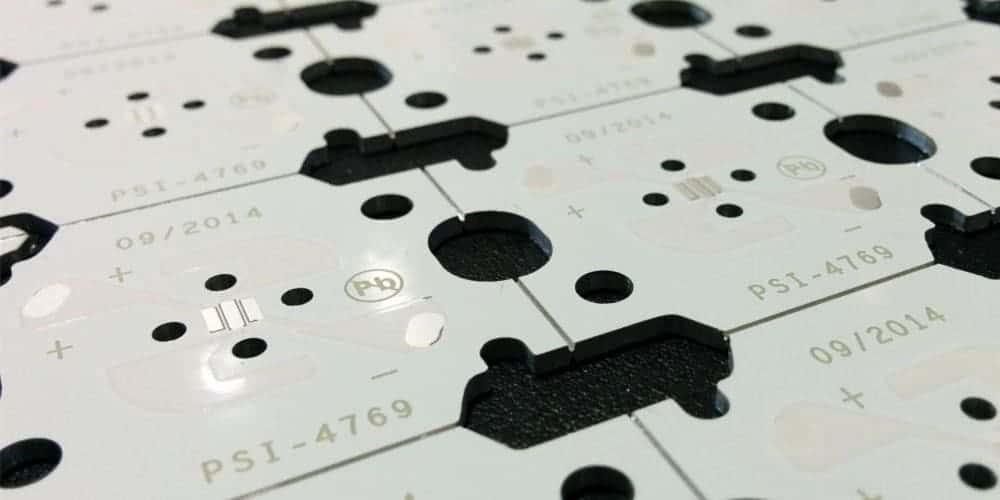
The PCB substrate specifically refers to the layered dielectric insulating material forming the foundational building block laminates which make up a completed multilayer board stackup across inner and outer layers.
Substrates provide:
- Mechanical support securing conductive traces
- Electrical insulation between conductors
- Protection shielding copper from environmental degradation
- Structural rigidity against physical bending stresses
- Thermal conductivity heatsinking generated loads
On substrates, additional conductive layers later pattern etch lay out planned connectivity before final protective solder mask coatings complete boards.
Functions of Substrates in PCBs
To fulfill design goals reliably, properly specified base substrates influence resulting PCB performance across key metrics:
Electrical Functionality
The substrate dielectric defines conductive signal line impedances and propagation delays by shaping EM field interactions with currents through tightly coupled traces.
Signal Integrity
Base material dissipation factors and dielectric constants govern transmission line high frequency behaviors affecting signal quality at route endpoints.
Thermal Loads
Laminate thermal conductivity and permeability determine overall temperature maps across PCBs during operation as substrates dissipate collected heating.
Environmental Survival
Substrate material inherit moisture absorption traits and chemical resistances dictate barrier protections required for operation in humid, corrosive deployment environments.
Manufacturability
Fabrication capabilities around substrate dimensional stability, coefficient of thermal expansion (CTE) and chemical affinities impact manufacturing yields.
In combination, base laminate selections establish foundations enabling design intent transfer through downstream implementation processes into purpose-built PCB platforms.
Next we survey popular substrate types available for common layout needs.
Overview of Major PCB Substrate Categories
Over decades of electronics innovation, reliable substrate material recipes evolved targeting essential applications with specialized function/cost formulations. While new exotic blends continue emerging, primary PCB substrates fall into three mature classes:
FR-4
The ubiquitious FR-4 epoxy/woven glass laminate variant withstands over 80% of rigid printed circuit boards across consumer and commercial designs worldwide due to proven longevity and economical mass production scalability.
High Frequency FR-4
Enhanced epoxy composites improve electrical characteristics for higher signal quality focusing on lowered dissipation factors with tighter dielectric constants at higher frequencies versus traditional FR-4.
High Performance Exotics
Proprietary dielectric material innovations from major substrate manufacturers offer targeted performance gains on individual metrics like thermal conductivity, tight impedance tolerances, reduced losses, moisture resistance etc. needed in specialized applications.
We will now contrast popular options across each substrate category in more detail…
FR-4 Substrates
Since earliest days of printed wiring, the baseline FR-4 designation encompasses broad general purpose laminate materials composed of:
- Woven fiberglass cloth reinforcement
- Flame resistant epoxy resin binders
While many formulation variants exist, common traits include:
Cost – Inexpensive, starting under $10/ft2 in volume
Dielectric Constant – Typically from 3.9 to 4.5
Dissipation Factor – Ranges 0.015 to 0.025
Water Absorption – Up to 0.15% over 24hrs
Flexible Variants – From 1 to 30 degrees Z-axis expansion
The dependable thermal and electrical characteristics, excellent fabrication yields and low costs solidified FR-4 as the default substrate choice interconnecting over a trillion manufactured devices across countless applications.
However, traditional FR-4 falls short meeting contemporary signal integrity and miniaturization needs in high complexity boards requiring specialized substrates instead…
High Frequency Capable FR-4
While ample for routing DC and moderate data rates across early single/double layer boards, inherent dielectric losses and permittivity variability in base FR-4 hamper multi-GHz signal transmission down lengthy routes between ball grid array (BGA) packages and memory modules in contemporary multilayer designs.
High frequency (HF) FR-4 evolved retaining economical epoxy/glass materials while tightening laminate manufacturing process variability to:
- Control dielectric constants tightly from ±0.05 across panels
- Reduce dissipation factors below 0.005 bringing behavior closer to distilled water
- Lower coefficient of thermal expansion (CTE) improving dimensional stability
- Enable increased circuit density packing traces/vias into the substrate
These incremental enhancements balance costs while vastly improving electrical performance enabling modern data interfaces replace traditional FR-4 to achieve signal integrity previously requiring costly exotic substrates.
So when does choosing higher performance alternatives make sense?
High Performance Non-FR4 Substrates
While HF FR-4 adequately serves majority of digital signaling below 25Gbps across computing and communication designs as the default lower cost workhorse material, ultra high speed optical interconnects beyond 50Gbps, precision analog sensing circuits and extreme environment applications still justify non-FR-4 designer substrate materials when benefits warrant premiums.
Such niche custom materials promise specific optimized enhancements on attributes like:
Thermal conductivity – Boron Nitride, ceramic additions dissipate heat
Dielectric constant – Tight Epsilon ratios for impedance targeting
Loss tangents – Lower Dks improve high frequency attenuation
Moisture absorption – Hydrophobic insulation protects airborne systems
CTE – Reduced expansion/contraction modulus stabilizes PCB dimensions
Major laminate manufacturers offer portfolio material choices balancing electrical performance and budget targets for engineers selecting ideal substrates meeting application connectivity needs from prototype through mass production scale up.
Now we examine real-world substrate selection considerations assessing appropriate choices across product lifecycles…
Navigating Substrate Selection Tradeoffs
Assigning viable material candidates follows assessing capabilities against design requirements and manufacturing capabilities. Key tradeoffs balance:
Performance – When do electrical enhancements justify substrate upgrades? At what frequency do base FR4 conductive/dielectric losses force rethinking? Are exacting impedance tolerances required for memory interfaces?
Environments – Will CTE drive instability hurt antenna array calibration over 20 year service lifetimes? Do hygroscopic concerns limit substrate viability without sufficient barrier coatings in humid deployment locales?
Design Margins – Do layout headroom constraints like maximizing layer route capacity outweigh substrate advances only benefiting incremental density gains?
Fabrication Factors – Can incumbent vendors reliably yield novel substrates requiring process tuning on production equipment? Do new substrates mandate costly service upgrades limiting sourcing flexibility?
Cost Savings – Even if high frequency materials enhance signal quality, what substrate delivers essential performance at scale pricing aligning with program budgets?
Collectively assessing key trade dimensions enables selecting optimum material pairings fulfilling performance duty cycles within budget.
Now we apply learnings examining hypothetical multilayer substrate selection scenarios highlighting practical considerations guiding decisions…
Application Substrate Selection Examples
Assume needing to lay out complex communications controller PCB scheduled for volume production with following known criteria:
Layer Count: 16 layers needed
Route Density: High – 20um lines / 20um spacing
Frequency: PCIe Gen 4 (32Gbps) small form factor connectors
Environment: Fan cooled enclosure operating up to 60C internal
Program Budget: Mid-range – Up to ~$35 base laminate/ft2
This example covers typical design complexity found in network switches and server class hardware leveraging high speed interfaces.
We will evaluate substrate selection considerations given application drivers:
Electrical Performance Needs
High speed 32Gbps PCIe and 25GbE interfaces demand dielectrics supporting multi-GHz signal eye quality through lowered losses and impedance consistency unattainable in conventional FR-4. This requirement alone filters material candidates.
Thermal Design Limits
While fan cooling governs temperature during operation, limiting substrate absorption and improving conductivity helps internally heatsink loads avoiding hot spots in epoxy increasing electrical leakage.
Cost Factors
Targeting mid-range infrastructure budgets caps laminate expenditures around $35/ft2 making premium >$60/ft2 PTFE/ceramic filled substrates unjustifiable.
Evaluating constraints points towards high frequency FR4 balancing GHz信号 integrity meeting 32Gbps data rates under 60C operating temps at moderate cost up to 2x traditional FR4 – appropriate for production needs.
Next we’ll consider an RF subsystem selection scenario…
Aerospace Subsystem Substrate Selection Example
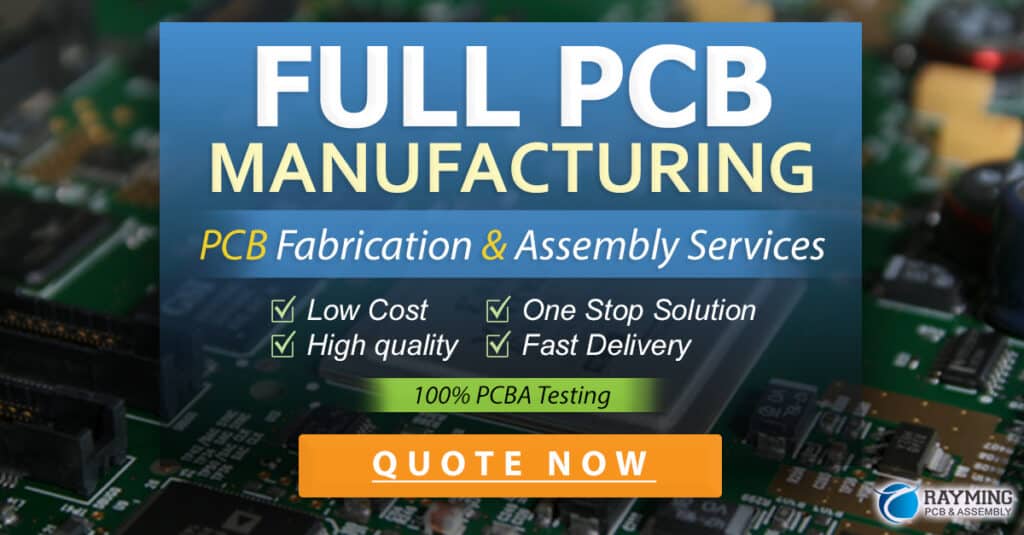
Enterprising small satellite startup aims launching constellation of communications nodes into low earth orbit with need to layout subsystem PCBs including:
Layer Count: 6 layer board
Routing Resolution: Standard 8mil lines
Frequency: Ku/Ka Band RF Frontends
Environment: Vacuum, -35C to 105C Operational Extremes Program Budget: Cost-conscious – Academic pricing
This space application environment stresses material selections. Lets revisit key considerations:
Orbital Thermal Stresses
With temperature swings from frigid darkness into blistering solar exposure, substrates warrant extremely low CTE and precision dielectric constants holding values against +/-70C changes protecting RF calibration. PTFE composites meet needs.
Material Degassing in Vacuums
Uncontrolled outgassing ruins optics so laminates pass maximally low Total Mass Loss percentage benchmarks rated for space vacuum conditions.
Academic Partner Pricing
Student Satellite budgets restrict boards pricing needing academic discounts sometimes limiting material availability.
Review shows radio complexity supports modest 6 layer stackup reachable with standard FR4 materials given simplistic routing needs. However, small sat environmental resilience and calibration require dimensionally stable, degassing resistant substrates like space rated cyanate ester or polyimide blends to survive missions.
Conclusion
This exploration across increasing design scenarios highlights how application demands guide PCB substrate selections balancing electrical, environmental, fabrication and cost considerations seeking optimal match between material traits and product sustainment responsibilities.
While reliable FR4 adequately supports general purpose boards, novel communications and extreme environment applications warrant upgraded dielectric, thermal, and resilience capabilities – scored against budget limits – to fulfill value delivery across product lifespans as substrate selections anchor overall electronics reliability.
Frequently Asked Questions
Q: Can you mount components directly onto bare substrates before adding copper layers?
A: Generally avoid placing components directly against base laminate dielectrics until after complete PCB fabrication given many fabrication steps subject boards to aggressive chemical baths degrading premature components. However some shielding, EMI filtering or high power elements bond directly when necessary.
Q: Do substrate requirements change for double sided vs multilayer boards?
A: Yes, as layer counts increase, parameters like dielectric transparency, dimensional stability, lamination processability and drilled hole reliability grow in importance for substrates to succeed supporting complex stacking. Multilayer designs scrutinize substrate electrical and physical traits much more closely.
Q: How to safely incinerate/dispose of FR4 and exotic PCB substrates?
A: Both traditional and exotic laminates require special handling given potential airborne hazards and combustion biproducts. FR4 in particular emits cyanide derivatives under heat. Disposal policies demand PCBs process through registered e-waste recycling centers with emissions treatment capabilities unlike general waste.
Q: Can fabricators bond different core and prepreg substrates combining properties?
A: Increasingly yes, advancements allow integrating dissimilar dielectric layers across stackups with intermediate bonding films enabling engineers tailoring laminate properties at microscale through the cross section matching specific embedded signal needs. However smoothing CTE transitions remains vital avoiding interface failures.
Q: Do substrates contribute substantial cost to finished boards?
A: In moderate layer count boards, raw substrates generally comprise 25-30% of fabrication costs – so material selection conservatively pays dividends. In high complexity boards with dense lamination processes, substrates directly contribute over 50% of end costs making choices disproportionately impactful.
0 Comments