Introduction to ATE PCB
Automated Test Equipment (ATE) is a crucial component in the manufacturing and testing of Printed Circuit Boards (PCBs). ATE PCB refers to the specialized circuit boards that are designed and used in ATE systems to facilitate the testing process. These boards play a vital role in ensuring the quality, reliability, and functionality of electronic devices and components.
In this article, we will delve into the world of ATE PCB, exploring its significance, design considerations, manufacturing processes, and best practices. We will also discuss the challenges and future trends in ATE PCB technology.
What is ATE?
Automated Test Equipment (ATE) is a system that is used to test electronic devices, components, and assemblies automatically. ATE systems are designed to perform a wide range of tests, including functional testing, in-circuit testing, boundary scan testing, and more. The primary goal of ATE is to ensure that the manufactured products meet the required specifications and are free from defects.
ATE systems consist of various components, including:
-
Test head: The test head is the main interface between the ATE system and the device under test (DUT). It houses the pin electronics, which are responsible for applying stimuli and measuring responses from the DUT.
-
Pin electronics: Pin electronics are the circuits that generate and measure signals at the individual pins of the DUT. They are designed to handle a wide range of voltages and currents, and they can be programmed to perform various test functions.
-
Fixture: The fixture is a mechanical device that holds the DUT in place during the testing process. It ensures proper alignment and connection between the DUT and the test head.
-
Test software: The test software controls the ATE system and defines the test sequences, parameters, and limits. It also analyzes the test results and generates reports.
The Role of ATE PCB
ATE PCB is a specialized circuit board that is designed to interface with the ATE system and the DUT. It serves as a bridge between the test head and the fixture, providing the necessary connections and signal routing. ATE PCB is essential for several reasons:
-
Signal integrity: ATE PCB is designed to maintain signal integrity between the test head and the DUT. It minimizes signal distortion, crosstalk, and noise, ensuring accurate and reliable test results.
-
Adaptability: ATE PCB can be customized to accommodate various types of DUTs and test requirements. It allows for flexible pin assignments, signal conditioning, and power distribution.
-
Cost-effectiveness: By using a well-designed ATE PCB, manufacturers can reduce the cost of test fixtures and minimize the need for expensive custom-built solutions.
ATE PCB Design Considerations
Designing an ATE PCB requires careful consideration of several factors to ensure optimal performance and reliability. Some of the key design considerations include:
Signal Integrity
Signal integrity is a critical aspect of ATE PCB design. The board must be designed to minimize signal distortion, crosstalk, and noise, ensuring that the test signals remain accurate and reliable. This is achieved through proper trace routing, impedance matching, and shielding techniques.
Trace Routing
Trace routing refers to the placement and routing of conductive traces on the PCB. In ATE PCB design, trace routing must be optimized to minimize signal degradation and interference. This involves:
- Keeping trace lengths as short as possible to reduce signal attenuation and delay.
- Avoiding sharp bends and corners in traces to minimize reflections and impedance discontinuities.
- Providing adequate spacing between traces to reduce crosstalk.
- Using differential pairs for high-speed signals to cancel out electromagnetic interference (EMI).
Impedance Matching
Impedance matching is the process of ensuring that the characteristic impedance of the traces on the ATE PCB matches the impedance of the test head and the DUT. This is essential for preventing signal reflections and maintaining signal integrity. Impedance matching is typically achieved through careful control of trace width, thickness, and spacing, as well as the use of termination resistors.
Shielding
Shielding is a technique used to protect sensitive signals from EMI and crosstalk. In ATE PCB design, shielding is often implemented using ground planes, which are conductive layers that provide a low-impedance path for return currents. Ground planes also help to reduce the loop area of signals, minimizing the radiation of EMI.
Power Distribution
Power distribution is another critical aspect of ATE PCB design. The board must provide stable and clean power to the DUT and the various components on the board. This involves:
- Using appropriate voltage regulators and power supply decoupling capacitors to minimize voltage fluctuations and noise.
- Providing adequate current-carrying capacity in power traces to prevent voltage drops and overheating.
- Implementing proper grounding techniques to prevent ground loops and ensure a low-impedance return path for currents.
Mechanical Considerations
ATE PCB design must also take into account mechanical considerations, such as:
- Board size and shape: The ATE PCB must fit within the available space in the test fixture and accommodate the required components and connectors.
- Mounting holes and fasteners: The board should include appropriate mounting holes and fasteners to ensure secure and reliable attachment to the test fixture.
- Connector placement: Connectors must be placed in locations that facilitate easy assembly and maintenance while minimizing signal path lengths.
ATE PCB Manufacturing Process
The manufacturing process for ATE PCB involves several steps that are critical to ensuring the quality and reliability of the final product. These steps include:
PCB Fabrication
PCB fabrication is the process of creating the bare circuit board. It involves the following sub-steps:
- Material selection: The appropriate substrate material, typically FR-4, is selected based on the electrical and mechanical requirements of the ATE PCB.
- Copper cladding: Thin layers of copper are laminated onto the substrate to form the conductive layers of the PCB.
- Drilling: Holes are drilled into the substrate to accommodate through-hole components and vias.
- Patterning: The desired circuit pattern is transferred onto the copper layers using photolithography and etching processes.
- Plating: The holes and exposed copper surfaces are plated with additional copper, followed by tin or gold, to improve conductivity and protect against oxidation.
- Solder mask application: A protective solder mask is applied to the PCB surface, leaving only the areas intended for soldering exposed.
- Silkscreen printing: Text and symbols are printed onto the PCB surface using silkscreen printing for identification and assembly purposes.
PCB Assembly
PCB assembly is the process of populating the fabricated PCB with components. It involves the following sub-steps:
- Solder paste application: Solder paste is applied to the pads on the PCB using a stencil or screen printing process.
- Component placement: Surface mount components are placed onto the solder paste using pick-and-place machines, while through-hole components are inserted manually or with the aid of machines.
- Reflow soldering: The PCB is heated in a reflow oven, causing the solder paste to melt and form electrical connections between the components and the PCB.
- Inspection: The assembled PCB is inspected visually and with the aid of automated optical inspection (AOI) systems to identify any defects or misalignments.
- Testing: The assembled PCB undergoes functional testing to verify that it meets the required specifications and performs as intended.
Quality Control
Quality control is an essential aspect of the ATE PCB manufacturing process. It involves various techniques to ensure that the PCBs meet the required quality standards, such as:
- Automated optical inspection (AOI): AOI systems use cameras and image processing algorithms to detect surface defects, component placement errors, and solder joint issues.
- In-circuit testing (ICT): ICT systems use a bed-of-nails fixture to make electrical contact with the PCB and test the functionality of individual components and circuits.
- Flying probe testing: Flying probe testers use movable probes to make electrical contact with the PCB and perform tests on specific points or components.
- Boundary scan testing: Boundary scan testing uses built-in test circuitry in the components to test the interconnections between them, allowing for the detection of open circuits, short circuits, and other faults.
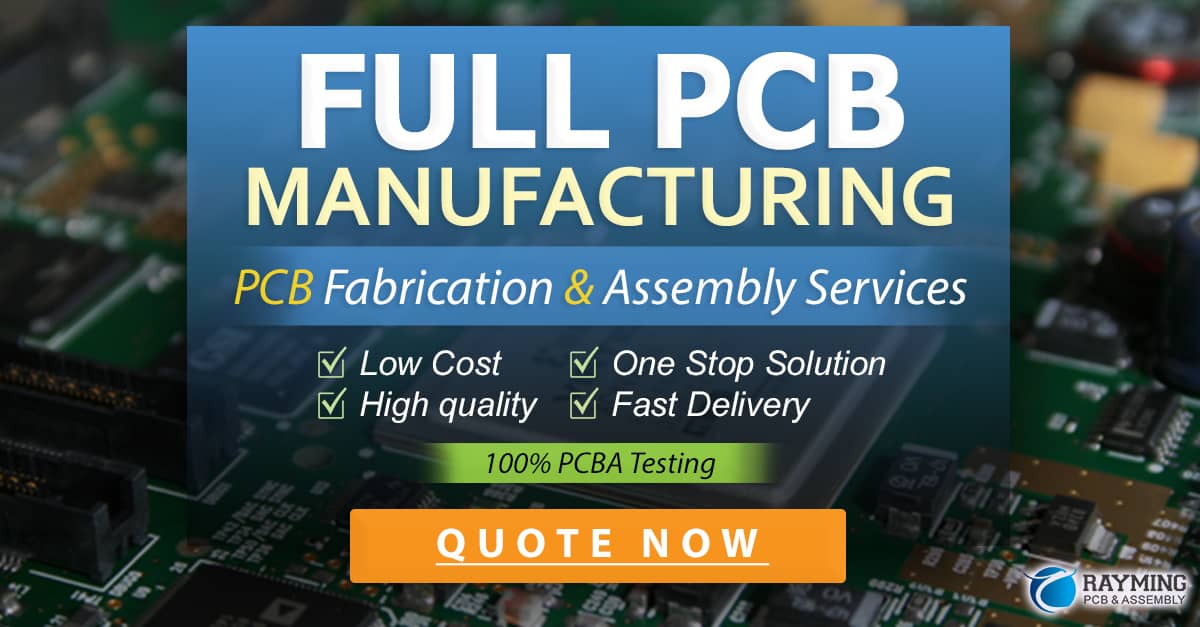
Best Practices for ATE PCB Design and Manufacturing
To ensure the success of an ATE PCB project, it is essential to follow best practices throughout the design and manufacturing process. Some of these best practices include:
Collaboration between Design and Manufacturing Teams
Close collaboration between the design and manufacturing teams is crucial for ensuring the manufacturability and reliability of the ATE PCB. The design team should consult with the manufacturing team early in the design process to identify any potential issues and ensure that the design is optimized for manufacturing.
Design for Manufacturability (DFM)
Design for Manufacturability (DFM) is a set of principles and guidelines that aim to optimize the design of the PCB for the manufacturing process. This includes:
- Adhering to the manufacturer’s design rules and guidelines, such as minimum trace widths, spacings, and hole sizes.
- Avoiding unnecessarily complex or dense layouts that may be difficult to manufacture or inspect.
- Providing adequate clearances and tolerances for component placement and soldering.
- Using standardized components and footprints whenever possible to simplify procurement and assembly.
Design for Testability (DFT)
Design for Testability (DFT) is a set of principles and techniques that aim to make the ATE PCB easier to test and debug. This includes:
- Incorporating test points and access points in the design to facilitate probing and testing.
- Using boundary scan compatible components and designing the board to support boundary scan testing.
- Providing clear and comprehensive labeling and documentation to aid in troubleshooting and maintenance.
Prototyping and Testing
Prototyping and testing are essential steps in the ATE PCB Development process. They allow for the validation of the design and the identification of any issues before mass production begins. Prototyping can be done using various methods, such as:
- Rapid prototyping: Rapid prototyping techniques, such as 3D printing or laser cutting, can be used to quickly create physical prototypes of the PCB and test fixtures.
- Bare board testing: Bare board testing involves testing the fabricated PCB before components are assembled to ensure that the board is free from manufacturing defects.
- Functional testing: Functional testing involves testing the assembled PCB to verify that it performs as intended and meets the required specifications.
Documentation and Version Control
Proper documentation and version control are essential for ensuring the quality and traceability of the ATE PCB. This includes:
- Maintaining accurate and up-to-date schematic diagrams, bill of materials (BOM), and assembly drawings.
- Using a version control system to track changes and revisions to the design files and documentation.
- Providing clear and comprehensive test plans and procedures to ensure consistent and reliable testing.
Challenges and Future Trends in ATE PCB Technology
ATE PCB technology faces several challenges and opportunities as the electronics industry continues to evolve. Some of the key challenges and future trends include:
High-Speed and High-Frequency Testing
As electronic devices and components become faster and more complex, ATE PCBs must be designed to handle higher speeds and frequencies. This requires advanced signal integrity techniques, such as:
- Using low-loss and high-frequency materials for the PCB substrate and components.
- Implementing advanced shielding and grounding techniques to minimize EMI and crosstalk.
- Employing simulation and modeling tools to optimize the design for high-speed performance.
Miniaturization and High-Density Packaging
The trend towards miniaturization and high-density packaging in electronic devices presents challenges for ATE PCB design and manufacturing. This requires:
- Using smaller and more compact components and packages, such as chip-scale packages (CSP) and ball grid arrays (BGA).
- Implementing advanced manufacturing techniques, such as micro-via drilling and embedded components, to achieve higher density and reduce board size.
- Adopting 3D packaging technologies, such as through-silicon vias (TSV) and package-on-package (PoP), to enable vertical stacking of components.
Adaptability and Flexibility
As the variety and complexity of electronic devices continue to increase, ATE PCBs must be designed for adaptability and flexibility. This involves:
- Using modular and reconfigurable designs that can accommodate different types of DUTs and test requirements.
- Incorporating programmable and software-defined features, such as field-programmable gate arrays (FPGA) and software-defined instruments, to enable rapid adaptation to new test scenarios.
- Designing for scalability and upgradability to accommodate future changes and enhancements in test capabilities.
Cost and Time-to-Market Pressures
The increasing cost and time-to-market pressures in the electronics industry pose challenges for ATE PCB development. To address these challenges, manufacturers and designers must:
- Adopt lean and agile development methodologies to streamline the design and manufacturing process and reduce waste.
- Leverage automation and digitalization technologies, such as computer-aided design (CAD), computer-aided manufacturing (CAM), and machine learning, to improve efficiency and accuracy.
- Foster close collaboration and communication among stakeholders, including design teams, manufacturing partners, and customers, to ensure alignment and minimize delays.
Frequently Asked Questions (FAQ)
1. What is the difference between an ATE PCB and a regular PCB?
An ATE PCB is a specialized circuit board designed specifically for use in automated test equipment (ATE) systems. It is optimized for signal integrity, adaptability, and reliability to ensure accurate and consistent testing of electronic devices and components. In contrast, a regular PCB is a general-purpose circuit board used in various electronic products and may not have the same level of performance and features required for ATE applications.
2. What are the key design considerations for an ATE PCB?
The key design considerations for an ATE PCB include signal integrity, trace routing, impedance matching, shielding, power distribution, and mechanical factors such as board size, shape, and connector placement. Designers must carefully balance these factors to ensure optimal performance, reliability, and manufacturability of the ATE PCB.
3. What are the main steps in the ATE PCB manufacturing process?
The main steps in the ATE PCB manufacturing process include PCB fabrication, PCB assembly, and quality control. PCB fabrication involves creating the bare circuit board, while PCB assembly involves populating the board with components. Quality control encompasses various techniques, such as automated optical inspection (AOI), in-circuit testing (ICT), and boundary scan testing, to ensure that the PCBs meet the required quality standards.
4. What are some best practices for ATE PCB design and manufacturing?
Some best practices for ATE PCB design and manufacturing include close collaboration between design and manufacturing teams, adherence to design for manufacturability (DFM) and design for testability (DFT) principles, prototyping and testing, and proper documentation and version control. These practices help ensure the success of an ATE PCB project by optimizing the design for manufacturing, facilitating testing and debugging, and maintaining quality and traceability throughout the development process.
5. What are some of the challenges and future trends in ATE PCB technology?
Some of the challenges and future trends in ATE PCB technology include the need for high-speed and high-frequency testing, miniaturization and high-density packaging, adaptability and flexibility, and cost and time-to-market pressures. To address these challenges, designers and manufacturers must adopt advanced technologies, such as low-loss materials, 3D packaging, programmable and software-defined features, and automation and digitalization tools, while fostering close collaboration and communication among stakeholders.
Conclusion
ATE PCB technology plays a vital role in ensuring the quality, reliability, and functionality of electronic devices and components. By understanding the design considerations, manufacturing processes, and best practices associated with ATE PCBs, designers and manufacturers can optimize their development efforts and overcome the challenges posed by the ever-evolving electronics industry.
As the demand for faster, smaller, and more complex electronic products continues to grow, ATE PCB technology must adapt and innovate to keep pace. This requires a commitment to continuous learning, collaboration, and innovation among all stakeholders involved in the development process.
By embracing the future trends and opportunities in ATE PCB technology, such as high-speed and high-frequency testing, miniaturization and high-density packaging, adaptability and flexibility, and cost and time-to-market optimization, the electronics industry can continue to push the boundaries of what is possible and deliver increasingly advanced and reliable products to consumers worldwide.
0 Comments