Introduction to SMT Stencils
Surface Mount Technology (SMT) has revolutionized the electronics manufacturing industry by enabling the production of smaller, faster, and more efficient electronic devices. One of the critical components in the SMT Assembly process is the stencil, which is used to apply solder paste onto the printed circuit board (PCB) before placing the components.
SMT Stencils are typically made of stainless steel or nickel alloy and contain precise openings that correspond to the pads on the PCB. The solder paste is applied through these openings, ensuring that the correct amount of paste is deposited on each pad. The accuracy and consistency of the solder paste deposition are crucial for the success of the SMT assembly process.
The Importance of Holes in SMT Stencils
While the openings in the SMT stencil are essential for applying solder paste, the holes in the stencil play an equally important role. These holes serve several purposes:
-
Alignment: Holes in the stencil are used for aligning the stencil with the PCB. They ensure that the stencil openings are precisely positioned over the corresponding pads on the PCB.
-
Support: The holes provide support for the stencil during the printing process. They help maintain the stencil’s flatness and prevent it from sagging or deforming under the pressure of the solder paste.
-
Cleaning: Holes in the stencil facilitate the cleaning process. They allow solvents and cleaning agents to reach the underside of the stencil, ensuring thorough cleaning and preventing solder paste buildup.
Methods for Making Holes in SMT Stencils
There are several methods for creating holes in SMT stencils, each with its advantages and limitations. The choice of method depends on factors such as the stencil material, the required hole size and shape, and the available equipment. Let’s explore some of the most common methods:
Laser Cutting
Laser cutting is a popular method for creating holes in SMT stencils. It involves using a high-powered laser beam to vaporize the stencil material, leaving a clean and precise hole. Laser cutting offers several advantages:
- Precision: Laser cutting can produce holes with very tight tolerances, ensuring accurate alignment and consistent solder paste deposition.
- Flexibility: Laser cutting allows for the creation of holes of various sizes and shapes, including round, square, and custom geometries.
- Speed: Laser cutting is a fast process, enabling the production of stencils with numerous holes in a short time.
However, laser cutting also has some limitations:
- Cost: Laser cutting equipment can be expensive, making it less suitable for low-volume production or prototyping.
- Material limitations: Some stencil materials, such as certain alloys or thicker stencils, may not be suitable for laser cutting due to their thermal properties or the laser’s power limitations.
Chemical Etching
Chemical etching is another method for creating holes in SMT stencils. It involves using a chemical solution to selectively dissolve the stencil material in the desired areas. The process typically follows these steps:
- The stencil is coated with a photoresist material.
- The photoresist is exposed to UV light through a mask that defines the hole pattern.
- The exposed photoresist is developed, revealing the areas to be etched.
- The stencil is immersed in an etching solution, which dissolves the exposed metal.
- The remaining photoresist is removed, leaving the etched holes in the stencil.
Chemical etching offers some advantages:
- Cost-effectiveness: Chemical etching is generally less expensive than laser cutting, making it suitable for larger production volumes.
- Precision: Chemical etching can produce holes with good accuracy and consistency, although not as precise as laser cutting.
However, chemical etching also has some drawbacks:
- Time-consuming: The chemical etching process is slower than laser cutting, as it involves multiple steps and requires time for the etching solution to dissolve the metal.
- Environmental concerns: Chemical etching involves the use of hazardous chemicals, which require proper handling, storage, and disposal to minimize environmental impact.
Mechanical Punching
Mechanical punching is a traditional method for creating holes in SMT stencils. It involves using a punch and die set to mechanically cut the holes into the stencil material. The punch is a hardened tool with the desired hole shape, while the die is a matching cavity that supports the stencil during the punching process.
Mechanical punching offers some advantages:
- Simplicity: Mechanical punching is a straightforward process that does not require complex equipment or specialized knowledge.
- Speed: Punching can be a fast process, especially for creating a large number of identical holes.
However, mechanical punching also has some limitations:
- Limited hole shapes: Mechanical punching is typically limited to simple hole shapes, such as round or square, and may not be suitable for complex geometries.
- Tooling costs: Each hole size and shape requires a specific punch and die set, which can be expensive for stencils with multiple hole sizes or custom shapes.
- Wear and tear: The punches and dies are subject to wear and tear over time, which can affect the accuracy and consistency of the holes.
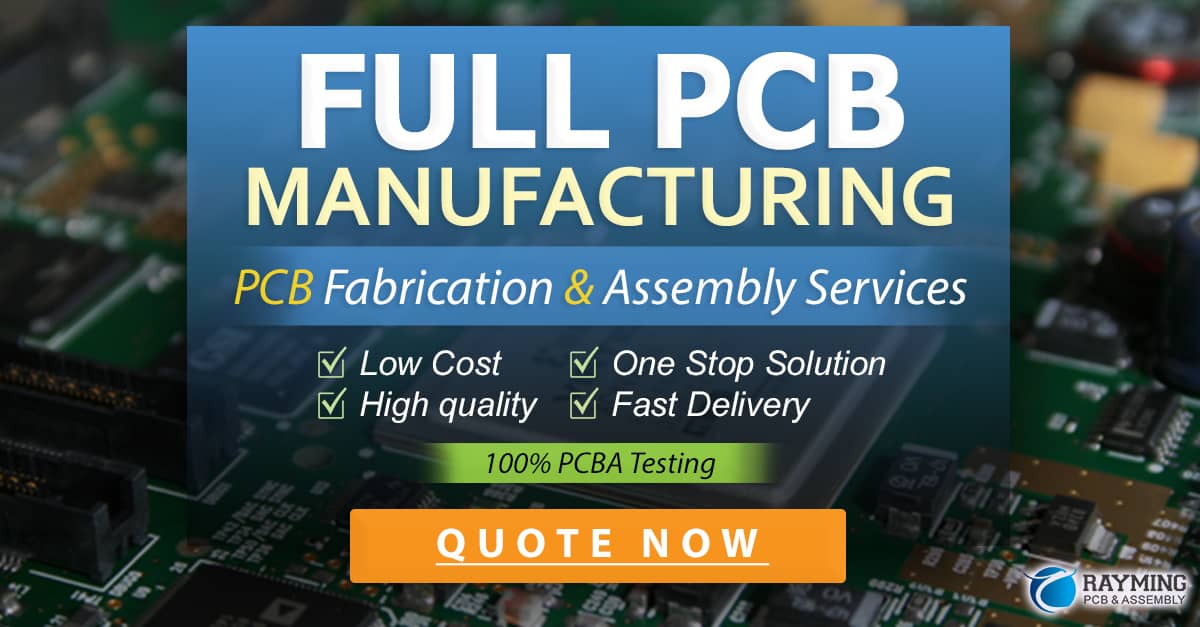
Factors to Consider When Making Holes in SMT Stencils
When creating holes in SMT stencils, several factors should be considered to ensure the best results:
Hole Size and Shape
The size and shape of the holes in the stencil should be carefully chosen based on the specific requirements of the PCB and the SMT assembly process. Some factors to consider include:
- Pad size: The hole size should be slightly larger than the pad size on the PCB to allow for proper alignment and solder paste coverage.
- Component pitch: The hole spacing should match the pitch of the components to be placed on the PCB.
- Solder paste viscosity: The hole size and shape may need to be adjusted based on the viscosity of the solder paste to ensure optimal paste release.
Stencil Thickness
The thickness of the stencil is another important factor to consider when making holes. Thicker stencils generally require larger holes to ensure proper solder paste release, while thinner stencils can accommodate smaller holes. The choice of stencil thickness depends on factors such as:
- Component height: Taller components may require a thicker stencil to provide sufficient solder paste volume.
- Solder paste viscosity: Higher viscosity solder pastes may require a thicker stencil to ensure proper paste release.
- PCB design: The PCB layout and pad sizes may dictate the required stencil thickness for optimal solder paste deposition.
Hole Placement and Alignment
The placement and alignment of the holes in the stencil are critical for ensuring accurate solder paste deposition and component placement. Some considerations include:
- Fiducial marks: Fiducial marks on the stencil and PCB are used for alignment purposes. The holes in the stencil should be positioned accurately relative to these marks.
- Hole-to-pad alignment: The holes in the stencil should be precisely aligned with the corresponding pads on the PCB to ensure proper solder paste coverage.
- Stencil registration: The stencil should be securely registered to the PCB during the printing process to maintain accurate alignment throughout the process.
Stencil Hole Design Guidelines
When designing holes in SMT stencils, following some general guidelines can help ensure optimal results:
-
Hole diameter: The hole diameter should be approximately 10-20% larger than the pad diameter on the PCB. This allows for proper solder paste coverage and accommodates any alignment variations.
-
Hole shape: Round holes are the most common and preferred shape for SMT stencils. They provide good paste release and are easier to clean compared to other shapes.
-
Hole spacing: The spacing between holes should be sufficient to maintain stencil strength and rigidity. A minimum spacing of 0.1 mm between holes is generally recommended.
-
Hole placement: Holes should be placed as close to the center of the pads as possible to ensure even solder paste distribution. Avoid placing holes too close to the edge of the pads, as this can lead to solder bridging or insufficient paste coverage.
-
Stencil thickness: The stencil thickness should be selected based on the desired solder paste volume and the specific requirements of the components and PCB. A typical stencil thickness range is 0.1 mm to 0.2 mm, but thicker stencils may be used for larger components or higher-volume applications.
Stencil Hole Inspection and Quality Control
After creating holes in the SMT stencil, it is essential to inspect the stencil to ensure that the holes meet the required specifications. Some key aspects to inspect include:
- Hole size and shape: Verify that the holes are of the correct size and shape, as specified in the stencil design.
- Hole placement and alignment: Check that the holes are accurately placed relative to the fiducial marks and are aligned with the corresponding pads on the PCB.
- Hole cleanliness: Ensure that the holes are free from debris, burrs, or any other contaminants that could affect solder paste release or cause defects in the assembly process.
Quality control measures should be implemented to maintain consistent hole quality across multiple stencils and production runs. This may involve regular inspections, measurements, and statistical process control (SPC) techniques to monitor and control the hole-making process.
Troubleshooting Common Issues with SMT Stencil Holes
Despite careful design and manufacturing, issues can sometimes arise with SMT stencil holes. Some common problems and their potential solutions include:
-
Insufficient solder paste deposition: If the holes are too small or not properly aligned, they may not allow enough solder paste to be deposited on the pads. This can be addressed by increasing the hole size or adjusting the alignment.
-
Excessive solder paste deposition: If the holes are too large, they may deposit too much solder paste, leading to solder bridging or other defects. Reducing the hole size or adjusting the stencil thickness can help mitigate this issue.
-
Solder paste clogging: If the holes are not cleaned regularly or are too small, solder paste can build up and clog the openings. Regular cleaning and maintenance of the stencil, along with proper hole design, can prevent this problem.
-
Stencil warping or damage: Improper handling, storage, or cleaning of the stencil can cause warping or damage, affecting the hole alignment and solder paste deposition. Following proper handling and maintenance procedures can help extend the stencil’s life and maintain its performance.
Conclusion
Creating holes in SMT stencils is a critical aspect of the stencil manufacturing process. The holes serve important functions, including alignment, support, and cleaning, and their accurate placement and design are essential for ensuring optimal solder paste deposition and SMT assembly quality.
Various methods can be used to create holes in stencils, including laser cutting, chemical etching, and mechanical punching, each with its own advantages and limitations. The choice of method depends on factors such as the stencil material, hole size and shape, and production volume.
When designing and manufacturing SMT stencil holes, several factors should be considered, such as hole size, shape, spacing, and stencil thickness. Following guidelines and best practices can help ensure consistent and reliable hole quality.
Regular inspection, quality control, and troubleshooting are also important for maintaining the performance of SMT stencil holes throughout the production process. By understanding the importance of holes in SMT stencils and implementing proper design, manufacturing, and maintenance practices, manufacturers can optimize their SMT assembly process and produce high-quality electronic devices.
Frequently Asked Questions (FAQ)
-
What is the purpose of holes in SMT stencils?
Holes in SMT stencils serve three main purposes: alignment of the stencil with the PCB, support for the stencil during the printing process, and facilitating the cleaning of the stencil. -
What are the most common methods for making holes in SMT stencils?
The most common methods for creating holes in SMT stencils are laser cutting, chemical etching, and mechanical punching. Each method has its own advantages and limitations, and the choice depends on factors such as the stencil material, hole size and shape, and production volume. -
What factors should be considered when designing holes in SMT stencils?
When designing holes in SMT stencils, several factors should be considered, including hole size and shape, stencil thickness, hole placement and alignment, and solder paste viscosity. Following general guidelines and best practices can help ensure optimal solder paste deposition and SMT assembly quality. -
How can I troubleshoot issues with insufficient or excessive solder paste deposition?
Insufficient solder paste deposition can be addressed by increasing the hole size or adjusting the alignment, while excessive solder paste deposition can be mitigated by reducing the hole size or adjusting the stencil thickness. Regular inspection and quality control measures can help identify and resolve these issues. -
What are some best practices for maintaining the performance of SMT stencil holes?
To maintain the performance of SMT stencil holes, it is important to follow proper handling, storage, and cleaning procedures. This includes regular inspection and cleaning of the stencil, as well as implementing quality control measures to ensure consistent hole quality across multiple stencils and production runs. Proper maintenance can help extend the stencil’s life and prevent issues such as solder paste clogging or stencil warping.
0 Comments