Introduction to PCB Layers
Printed Circuit Boards (PCBs) are essential components in modern electronic devices. They provide a platform for mounting and interconnecting electronic components, ensuring efficient and reliable functionality. One crucial aspect of PCB design is the number and arrangement of layers within the board. Understanding PCB layers is vital for designing and manufacturing high-quality PCBs that meet your project’s requirements.
In this article, we will delve into the world of PCB layers, exploring their types, functions, and importance in PCB design. We will also discuss the factors to consider when choosing the appropriate number of layers for your project and provide insights into the manufacturing process.
What are PCB Layers?
PCB layers are the individual conductive planes that make up a printed circuit board. Each layer serves a specific purpose, such as carrying signals, providing power distribution, or offering shielding. The number of layers in a PCB can vary depending on the complexity and requirements of the electronic device.
Types of PCB Layers
There are several types of PCB layers, each with its unique characteristics and functions. Let’s explore the most common types:
-
Signal Layers: Signal layers are used to route electrical signals between components on the PCB. They are typically located on the outer layers of the board, allowing for easy access and modification. Signal layers are designed to minimize signal interference and ensure proper signal integrity.
-
Power Layers: Power layers, also known as power planes, are dedicated to distributing power throughout the PCB. They provide a stable and low-impedance power supply to the components, minimizing voltage drops and ensuring reliable operation. Power layers are usually placed in the inner layers of the board.
-
Ground Layers: Ground layers, or ground planes, serve as a reference point for electrical signals and help to reduce electromagnetic interference (EMI). They provide a low-impedance return path for currents and help to shield sensitive signals from unwanted noise. Ground layers are often placed adjacent to power layers to form a power-ground pair.
-
Dielectric Layers: Dielectric layers, also known as insulating layers, are non-conductive layers that separate the conductive layers in a PCB. They provide electrical insulation and help to prevent short circuits between adjacent layers. Common dielectric materials include FR-4, Rogers, and Polyimide.
-
Solder Mask Layers: Solder mask layers are applied to the outer surfaces of the PCB to protect the copper traces from oxidation and prevent solder bridging during the assembly process. They also provide a visual aid for component placement and improve the overall durability of the board.
-
Silkscreen Layers: Silkscreen layers are used to print text, logos, and component identifiers on the surface of the PCB. They help in the assembly process and provide important information for debugging and maintenance purposes.
Importance of PCB Layers
PCB layers play a crucial role in the overall performance and reliability of electronic devices. Here are some key reasons why PCB layers are important:
-
Signal Integrity: Proper layer arrangement and design ensure that electrical signals travel efficiently and reliably between components. By separating signal layers and providing appropriate shielding, PCB designers can minimize crosstalk, reduce electromagnetic interference, and maintain signal integrity.
-
Power Distribution: Dedicated power layers ensure that all components on the PCB receive a stable and adequate power supply. By using power planes, designers can minimize voltage drops, reduce power loss, and improve the overall power distribution network.
-
EMI Reduction: Ground layers and proper layer stacking techniques help to reduce electromagnetic interference (EMI) in PCBs. By providing a low-impedance return path for currents and shielding sensitive signals, ground layers minimize the impact of EMI on the board’s performance.
-
Heat Dissipation: PCB layers can also contribute to effective heat dissipation. By using thicker copper layers or incorporating dedicated thermal layers, designers can improve the board’s ability to dissipate heat generated by components, ensuring reliable operation and longevity.
-
Manufacturing Efficiency: Well-designed PCB layers facilitate the manufacturing process. By adhering to standard layer stackups and design guidelines, designers can ensure compatibility with manufacturing processes, reduce manufacturing time, and minimize the risk of defects.
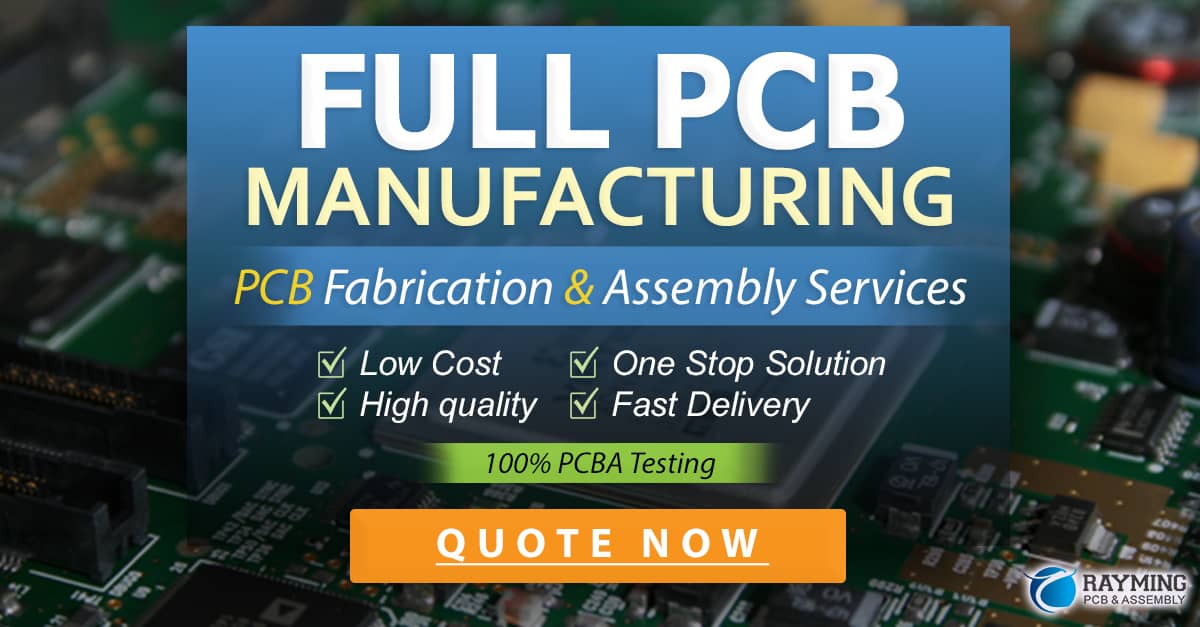
Factors to Consider When Choosing PCB Layers
When deciding on the number and arrangement of layers for your PCB project, several factors need to be considered. These include:
-
Circuit Complexity: The complexity of your electronic circuit directly influences the number of layers required. More complex designs with a higher component count and intricate routing may necessitate additional layers to accommodate all the connections and ensure proper functionality.
-
Signal Integrity: If your design involves high-speed signals or sensitive analog circuits, you may need to incorporate dedicated signal layers and ground planes to maintain signal integrity and minimize interference.
-
Power Requirements: The power requirements of your components dictate the need for dedicated power layers. If your design includes power-hungry components or requires a stable power supply, incorporating power planes can ensure reliable power distribution.
-
EMI Considerations: If your device operates in an environment prone to electromagnetic interference or needs to comply with EMI regulations, additional layers for shielding and grounding may be necessary.
-
Manufacturing Constraints: The manufacturing capabilities of your chosen PCB fabricator can influence the number of layers you can incorporate. Some manufacturers may have limitations on the maximum number of layers they can produce or require specific layer stackups for compatibility with their processes.
-
Cost: Increasing the number of layers in a PCB directly impacts the manufacturing cost. More layers require additional materials, processing steps, and time, resulting in higher production costs. It’s essential to strike a balance between the required functionality and the cost constraints of your project.
PCB Layer Stackup and Manufacturing Process
The arrangement of layers in a PCB is known as the layer stackup. The layer stackup defines the order and orientation of the conductive and dielectric layers within the board. A well-designed layer stackup ensures proper signal integrity, power distribution, and manufacturability.
Here’s an example of a typical 4-layer PCB Stackup:
Layer | Type | Material | Thickness |
---|---|---|---|
Top | Signal | Copper | 1 oz |
2 | Ground | Copper | 1 oz |
3 | Power | Copper | 1 oz |
Bottom | Signal | Copper | 1 oz |
Dielectric | FR-4 | 0.2 mm | |
Solder Mask | LPI | 0.025 mm | |
Silkscreen | Epoxy Ink | 0.015 mm |
The manufacturing process for PCBs involves several steps, including:
-
Design and Layout: The PCB design is created using specialized software, defining the layer stackup, component placement, and routing.
-
Fabrication: The designed layout is used to create a photomask for each layer. The copper-clad laminate is then coated with photoresist, exposed to UV light through the photomask, and developed to create the desired pattern.
-
Etching: The exposed copper is etched away using a chemical process, leaving only the desired traces and pads.
-
Lamination: The individual layers are aligned and laminated together using heat and pressure to form the complete PCB stackup.
-
Drilling: Holes are drilled through the PCB to accommodate through-hole components and provide interconnections between layers.
-
Surface Finishing: The PCB undergoes surface finishing processes, such as applying solder mask and silkscreen, to protect the copper traces and improve solderability.
-
Quality Control: The manufactured PCBs are inspected for defects, continuity, and adherence to design specifications.
Frequently Asked Questions (FAQs)
-
Q: What is the minimum number of layers required for a functional PCB?
A: The minimum number of layers required for a functional PCB is two – a signal layer and a ground layer. However, the actual number of layers needed depends on the complexity of the circuit and the design requirements. -
Q: Can I mix different types of layers in a single PCB?
A: Yes, it is common to mix different types of layers in a single PCB. For example, a PCB can have a combination of signal layers, power layers, and ground layers based on the design requirements. -
Q: How does the number of layers affect the cost of PCB manufacturing?
A: Generally, increasing the number of layers in a PCB leads to higher manufacturing costs. Each additional layer requires more materials, processing steps, and time, which contributes to the overall cost. -
Q: What is the maximum number of layers that can be used in a PCB?
A: The maximum number of layers in a PCB is not strictly defined and can vary depending on the manufacturing capabilities of the PCB fabricator. Some advanced PCB designs can have 40 or more layers, but such high layer counts are rare and reserved for highly complex applications. -
Q: How do I determine the appropriate number of layers for my PCB project?
A: Determining the appropriate number of layers for your PCB project involves considering factors such as circuit complexity, signal integrity, power requirements, EMI considerations, manufacturing constraints, and cost. It’s recommended to consult with experienced PCB designers or manufacturers to assess your project’s specific requirements and arrive at an optimal layer count.
Conclusion
Understanding PCB layers is crucial for designing and manufacturing reliable and high-performance electronic devices. By carefully considering the types of layers, their functions, and the factors that influence layer selection, you can create PCBs that meet your project’s requirements while optimizing signal integrity, power distribution, and manufacturability.
When designing your PCB, it’s essential to collaborate with experienced professionals who can guide you through the layer selection process and ensure compliance with industry standards and best practices. By leveraging the expertise of PCB designers and manufacturers, you can overcome design challenges, minimize risks, and achieve a successful outcome for your project.
As technology continues to advance, the importance of PCB layers will only grow. Staying updated with the latest trends, techniques, and materials in PCB design will enable you to create innovative and reliable electronic products that push the boundaries of what’s possible.
0 Comments