Introduction to Through-Hole Technology
Through-hole technology has been a staple in printed circuit board (PCB) design and manufacturing for decades. Despite the rise of Surface Mount Technology (SMT) and its advantages, through-hole components and designs remain relevant in today’s electronics industry. In this comprehensive article, we will explore the reasons behind the continued relevance of through-hole technology and its applications in modern PCB designs.
What is Through-Hole Technology?
Through-hole technology refers to the method of mounting electronic components on a PCB by inserting their leads through drilled holes in the board and soldering them to pads on the opposite side. This technique has been used since the early days of PCB manufacturing and has proven to be reliable and robust.
Advantages of Through-Hole Technology
-
Mechanical Strength: Through-hole components provide superior mechanical strength compared to surface mount components. The leads passing through the board and being soldered on the opposite side create a strong physical connection, making the assembly more resilient to vibration, shock, and mechanical stress.
-
Ease of Manual Assembly: Through-hole components are easier to handle and manually assemble than their surface mount counterparts. This is particularly advantageous for prototyping, low-volume production, and hobbyist projects where automated assembly equipment may not be available or cost-effective.
-
Reliability in Harsh Environments: Through-hole components are known for their reliability in harsh environmental conditions. The robust mechanical connection and the larger size of through-hole components make them less susceptible to thermal stress, vibration, and other environmental factors that can affect the performance and longevity of electronic devices.
-
High Power Handling: Through-hole components, especially power devices such as transistors and Voltage Regulators, can handle higher power levels compared to surface mount components. The larger size and better heat dissipation properties of through-hole packages make them suitable for applications that require high power handling capabilities.
Applications of Through-Hole Technology
Despite the widespread adoption of surface mount technology, through-hole components and designs still find their place in various applications across different industries.
1. High-Reliability Electronics
In industries such as aerospace, military, and medical devices, where reliability is of utmost importance, through-hole technology is often preferred. The robust mechanical connection and resistance to environmental stresses make through-hole components a reliable choice for critical systems and applications.
2. Power Electronics
Power electronics, such as power supplies, Motor Controllers, and high-current circuits, often rely on through-hole components. The higher power handling capability and better heat dissipation properties of through-hole packages make them suitable for these applications.
3. Prototyping and Low-Volume Production
Through-hole technology remains relevant in prototyping and low-volume production scenarios. The ease of manual assembly and the ability to quickly modify or repair circuits using through-hole components make them a preferred choice for prototypes and small production runs.
4. Educational and Hobbyist Projects
For educational purposes and hobbyist projects, through-hole components are often preferred due to their ease of handling and assembly. Beginners and students can learn the basics of electronics and soldering using through-hole components, as they are more forgiving and easier to work with compared to surface mount components.
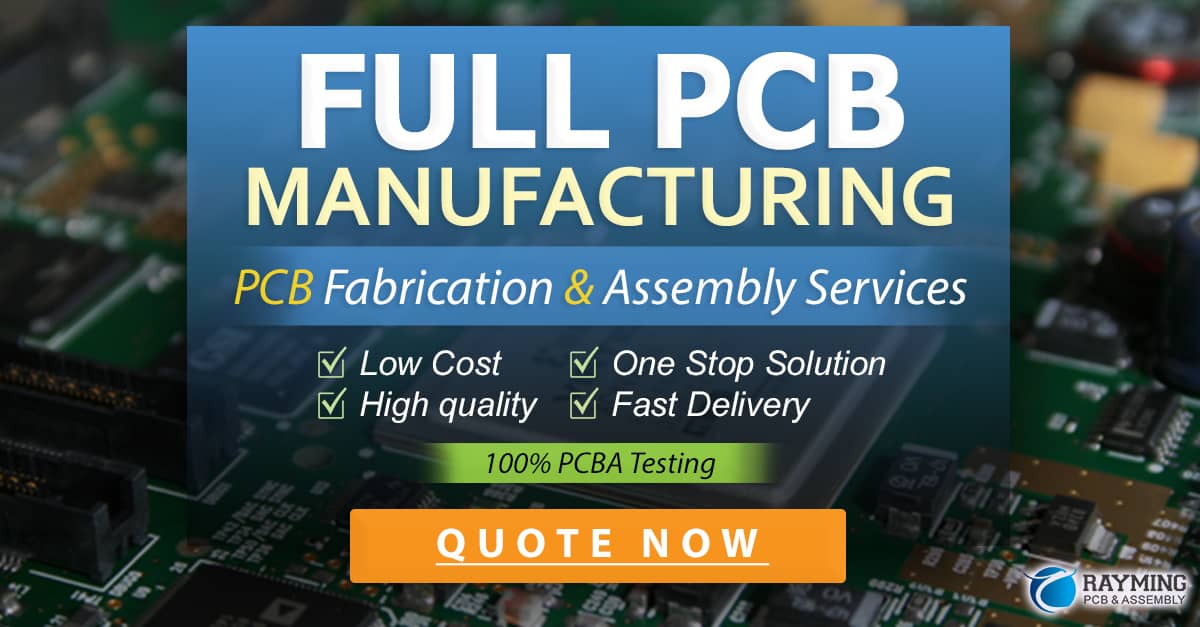
Combining Through-Hole and Surface Mount Technology
While surface mount technology offers advantages such as smaller form factors and higher component density, it is not always necessary or practical to completely eliminate through-hole components from a PCB design. In many cases, a combination of through-hole and surface mount components can be used to achieve the desired functionality, reliability, and manufacturability.
Hybrid PCB Designs
Hybrid PCB designs incorporate both through-hole and surface mount components on the same board. This approach allows designers to leverage the strengths of both technologies and optimize the PCB layout based on the specific requirements of the application.
For example, a hybrid design may use surface mount components for the majority of the circuit, benefiting from their smaller size and higher packaging density. However, certain components that require high power handling, mechanical strength, or are not available in surface mount packages can be mounted using through-hole technology.
Design Considerations for Hybrid PCBs
When designing hybrid PCBs, there are several considerations to keep in mind to ensure optimal performance and manufacturability:
-
Component Placement: Careful placement of through-hole and surface mount components is crucial to minimize the impact on the overall PCB layout. Through-hole components should be placed in areas where they do not obstruct the routing of surface mount components or create manufacturing challenges.
-
Solder Joint Reliability: Ensuring reliable solder joints is important when combining through-hole and surface mount components. Proper solder joint design, including the size and shape of solder pads, is essential to achieve good solder fillets and minimize the risk of solder joint failures.
-
Manufacturing Process: The manufacturing process for hybrid PCBs should be carefully planned to accommodate both through-hole and surface mount assembly. The assembly sequence, Soldering Methods, and inspection procedures should be optimized to ensure the quality and reliability of the final product.
FAQ
1. Is through-hole technology becoming obsolete?
No, through-hole technology is not becoming obsolete. While surface mount technology has gained prominence in modern PCB designs, through-hole components and designs still have their place in various applications where mechanical strength, reliability, and power handling are critical.
2. Can through-hole and surface mount components be used together on the same PCB?
Yes, through-hole and surface mount components can be used together on the same PCB. This is known as a hybrid PCB design, where the strengths of both technologies are leveraged to achieve the desired functionality and performance.
3. What are the advantages of through-hole technology over surface mount technology?
Through-hole technology offers several advantages over surface mount technology, including:
– Superior mechanical strength and reliability
– Ease of manual assembly and prototyping
– Better power handling capabilities
– Resistance to harsh environmental conditions
4. In which industries is through-hole technology commonly used?
Through-hole technology is commonly used in industries where reliability and robustness are critical, such as:
– Aerospace and military applications
– Medical devices
– Power electronics
– Automotive electronics
5. Is through-hole technology suitable for high-volume production?
While through-hole technology can be used in high-volume production, it may not be as efficient or cost-effective as surface mount technology. Surface mount components and automated assembly processes are generally preferred for high-volume manufacturing due to their faster assembly times and lower costs.
Conclusion
Through-hole technology continues to be relevant in PCB designs despite the widespread adoption of surface mount technology. Its superior mechanical strength, reliability in harsh environments, and ease of manual assembly make it a preferred choice for certain applications and industries.
By understanding the strengths and limitations of through-hole technology and leveraging hybrid PCB designs, engineers and designers can create robust and reliable electronic products that meet the specific requirements of their applications.
As the electronics industry evolves, through-hole technology will likely continue to coexist with surface mount technology, each serving its purpose in the diverse landscape of PCB design and manufacturing.
0 Comments