Advantages of Surface Mount Technology
SMT offers several advantages over traditional through-hole technology:
-
Miniaturization: SMT components are much smaller than their through-hole counterparts, allowing for more compact and lightweight electronic devices.
-
Increased component density: With SMT, more components can be placed on a single PCB, enabling more complex circuits and functionality.
-
Improved performance: SMT components have shorter lead lengths, reducing parasitic capacitance and inductance, which results in improved high-frequency performance.
-
Cost-effectiveness: SMT allows for automated assembly processes, reducing labor costs and increasing production efficiency.
-
Flexibility: SMT accommodates a wide range of component packages, from small chip resistors to large ball grid array (BGA) packages.
Equipment Used in Surface Mount Technology
The SMT process relies on specialized equipment to ensure precise and efficient assembly:
-
Solder paste printer: This machine applies solder paste to the PCB pads through a stencil using a squeegee.
-
Pick-and-place machine: Automated equipment that picks up SMT components from feeders and places them onto the solder paste-covered pads on the PCB.
-
Reflow oven: A conveyor oven that heats the PCB to melt the solder paste, forming a permanent connection between the components and the board.
-
Inspection systems: Automated optical inspection (AOI) and X-ray inspection systems are used to detect assembly defects and ensure quality control.
Surface Mount Technology Process Steps
The SMT process consists of several key steps:
1. PCB Design and Fabrication
The first step in the SMT process is designing the PCB using electronic design automation (EDA) software. The design includes component placement, routing, and the creation of solder paste stencils. Once the design is finalized, the PCB is fabricated using a combination of etching, drilling, and plating processes.
2. Solder Paste Printing
Solder paste, a mixture of tiny solder spheres and flux, is applied to the PCB pads using a solder paste printer. A stencil, which is a thin metal sheet with openings corresponding to the PCB pads, is placed over the board. A squeegee then moves across the stencil, forcing the solder paste through the openings and onto the pads.
Stencil Material | Thickness (µm) | Aperture Size (µm) | Solder Paste Type |
---|---|---|---|
Stainless Steel | 100-150 | 150-400 | Type 3, Type 4 |
Nickel | 100-150 | 150-400 | Type 3, Type 4 |
Polymer | 50-100 | 100-300 | Type 4, Type 5 |
3. Component Placement
The pick-and-place machine uses vacuum nozzles to pick up SMT components from feeders and place them onto the solder paste-covered pads on the PCB. Modern machines can place thousands of components per hour with high accuracy. The placement process is guided by fiducial markers on the PCB, which serve as reference points for the machine’s vision system.
4. Reflow Soldering
After component placement, the PCB is conveyed through a reflow oven. The oven applies a carefully controlled temperature profile, which typically includes the following stages:
- Preheat: The PCB is gradually heated to activate the flux and remove any moisture.
- Soak: The temperature is maintained to ensure even heating and flux activation.
- Reflow: The temperature is raised above the melting point of the solder, causing the solder paste to melt and form a permanent bond between the components and the PCB pads.
- Cooling: The PCB is cooled to allow the solder joints to solidify.
Reflow Stage | Temperature Range (°C) | Time (seconds) |
---|---|---|
Preheat | 100-150 | 60-120 |
Soak | 150-180 | 60-120 |
Reflow | 220-250 | 30-60 |
Cooling | 180-room temperature | 30-60 |
5. Inspection and Testing
After the reflow process, the assembled PCBs undergo inspection and testing to ensure quality and functionality. Automated optical inspection (AOI) systems use cameras and image processing algorithms to detect solder joint defects, component misalignment, and other assembly issues. X-ray inspection may be used for hidden solder joints, such as those under BGA packages.
Functional testing, such as in-circuit testing (ICT) or boundary scan testing, is performed to verify the electrical performance of the assembled PCBs.
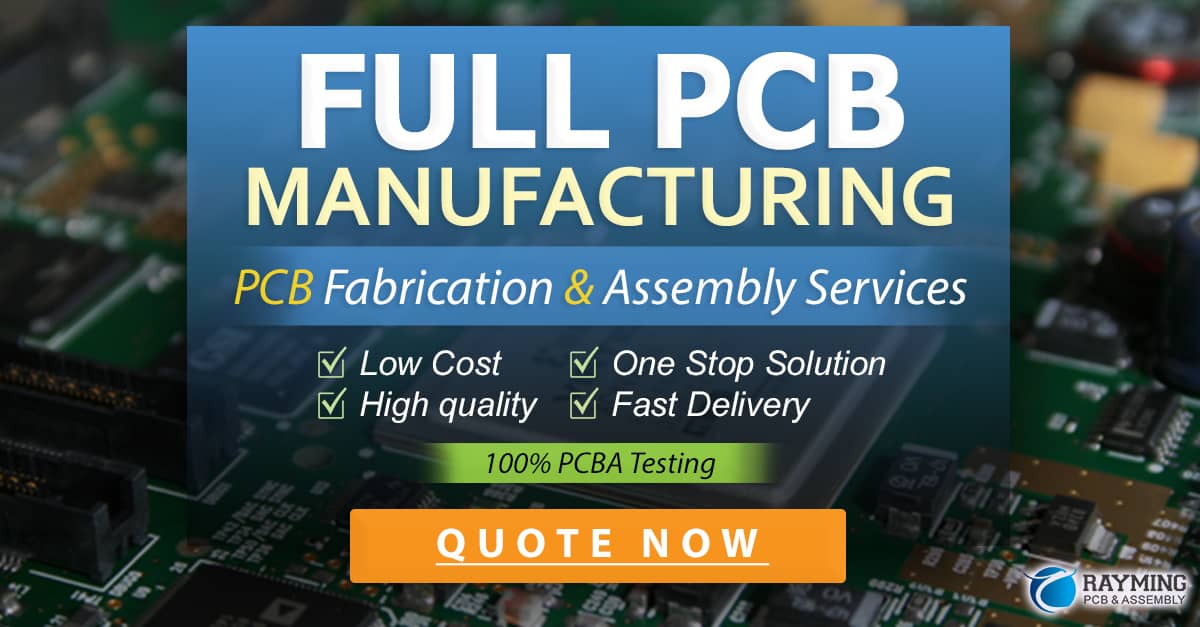
Frequently Asked Questions (FAQ)
-
Q: What are the most common SMT component packages?
A: Some of the most common SMT component packages include chip resistors, chip capacitors, small outline integrated circuits (SOICs), quad flat packages (QFPs), and ball grid arrays (BGAs). -
Q: Can through-hole components be used in SMT assembly?
A: Yes, through-hole components can be used in SMT assembly, but they require additional processing steps, such as wave soldering or selective soldering, after the SMT reflow process. -
Q: What is the role of flux in solder paste?
A: Flux helps to remove oxides from the surfaces of the PCB pads and component leads, promoting better wetting and bonding of the solder. It also helps to prevent oxidation during the reflow process. -
Q: What are the challenges associated with SMT assembly?
A: Some challenges in SMT assembly include managing component miniaturization, ensuring proper solder joint formation, dealing with thermal expansion mismatches, and handling moisture-sensitive devices (MSDs). -
Q: How can SMT assembly defects be minimized?
A: To minimize SMT assembly defects, it is essential to maintain proper process control, including stencil design, solder paste printing parameters, component placement accuracy, and reflow temperature profiles. Regular maintenance and calibration of equipment, as well as the use of inspection and testing systems, can also help to reduce defects.
Conclusion
Surface Mount Technology has transformed the electronics manufacturing industry, enabling the production of smaller, more complex, and more reliable electronic devices. By understanding the SMT process, including its advantages, equipment, and process steps, engineers and manufacturers can optimize their assembly lines for maximum efficiency and quality.
As electronic devices continue to evolve and become more sophisticated, SMT will remain a crucial technology in meeting the demands of the industry. Advancements in materials, equipment, and process control will further enhance the capabilities of SMT, allowing for even greater miniaturization and performance in the future.
0 Comments