Introduction to Solder Selection
Soldering is an essential skill for anyone working with electronics and circuit boards. Choosing the right solder is critical for creating strong, reliable connections that will stand up to use and environmental conditions. With the wide variety of solders available, selecting the best one for your specific application can seem daunting.
In this comprehensive guide, we’ll cover everything you need to know about solder selection for Circuit board assembly and electronics manufacturing. You’ll learn about the different types of solder alloys, flux cores, wire diameters, and other key factors to consider when picking a solder. Armed with this knowledge, you can select the optimal solder for your PCB project and achieve high-quality, long-lasting solder joints.
Understanding Solder Alloys
Tin-Lead (Sn-Pb) Solder
Traditionally, tin-lead (Sn-Pb) solders were the most widely used in the electronics industry. The most common Sn-Pb alloy is 63/37, which contains 63% tin and 37% lead by weight. This eutectic alloy has a melting point of 183°C (361°F) and provides good wetting, strong mechanical bonds, and reliable electrical connections.
However, due to health and environmental concerns over lead, many countries have implemented restrictions on the use of lead in electronics through RoHS (Restriction of Hazardous Substances) regulations. As a result, Lead-free Solders have largely replaced Sn-Pb solders in consumer electronics.
Lead-Free Solder Alloys
To comply with RoHS and other lead-free initiatives, the electronics industry has shifted to using lead-free solder alloys. The most common lead-free alloys are:
- Tin-Silver-Copper (SAC):
- SAC305 (96.5% Sn, 3.0% Ag, 0.5% Cu)
- SAC387 (95.5% Sn, 3.8% Ag, 0.7% Cu)
- Tin-Copper (SnCu):
- Sn99.3Cu0.7 (99.3% Sn, 0.7% Cu)
- Sn100C (99.25% Sn, 0.7% Cu, 0.05% Ni)
- Tin-Bismuth (SnBi):
- Sn42/Bi58 (42% Sn, 58% Bi)
- Sn57Bi42Ag1 (57% Sn, 42% Bi, 1% Ag)
Lead-free solders typically have higher melting points compared to Sn-Pb alloys, with SAC and SnCu alloys melting around 217-227°C (423-441°F). SnBi alloys have lower melting points, around 139°C (282°F), making them suitable for low-temperature applications.
When selecting a lead-free alloy, consider factors such as melting temperature, wetting ability, mechanical strength, and compatibility with PCB surface finishes and components.
Alloy Comparison Table
Alloy | Composition | Melting Point | Key Characteristics |
---|---|---|---|
63Sn37Pb | 63% Sn, 37% Pb | 183°C (361°F) | Eutectic, good wetting, strong bonds |
SAC305 | 96.5% Sn, 3.0% Ag, 0.5% Cu | 217-220°C (423-428°F) | Commonly used lead-free alloy, good reliability |
Sn99.3Cu0.7 | 99.3% Sn, 0.7% Cu | 227°C (441°F) | Lead-free, low cost, good mechanical strength |
Sn42Bi58 | 42% Sn, 58% Bi | 139°C (282°F) | Low melting point, suitable for heat-sensitive components |
Flux Types and Core Sizes
Solder wire typically comes in two forms: solid wire and rosin core wire. Rosin core wire has a hollow center filled with flux, which helps clean and prepare the surfaces for soldering, improving wetting and joint quality.
Flux Types
There are three main types of flux used in electronics soldering:
- Rosin (R): Rosin flux is naturally derived from pine tree sap and is available in three activity levels:
- Rosin (R): Mildest, minimal cleaning action
- Rosin Mildly Activated (RMA): Mild activity, leaves clear residue
- Rosin Activated (RA): Highest activity, leaves sticky residue
- Water-Soluble (WS): Water-soluble flux is more active than rosin flux and can be easily cleaned with water. It’s suitable for applications that require complete flux removal.
- No-Clean (NC): No-clean flux is designed to leave minimal, non-corrosive residue that doesn’t require cleaning. This type of flux is popular for PCB Assembly as it saves time and reduces the use of cleaning solvents.
When choosing a flux type, consider the cleaning requirements, PCB material, and environmental conditions the solder joints will be exposed to.
Flux Core Sizes
Rosin core solder wire comes in various flux core sizes, which indicate the percentage of flux by volume:
- Size 1: 1.1-1.7% flux
- Size 2: 1.8-2.5% flux
- Size 3: 2.6-3.3% flux
Larger core sizes provide more flux, which can be beneficial for soldering oxidized or hard-to-wet surfaces. However, excessive flux can lead to splattering and residue buildup. For most general-purpose electronics soldering, Size 1 or Size 2 core is sufficient.
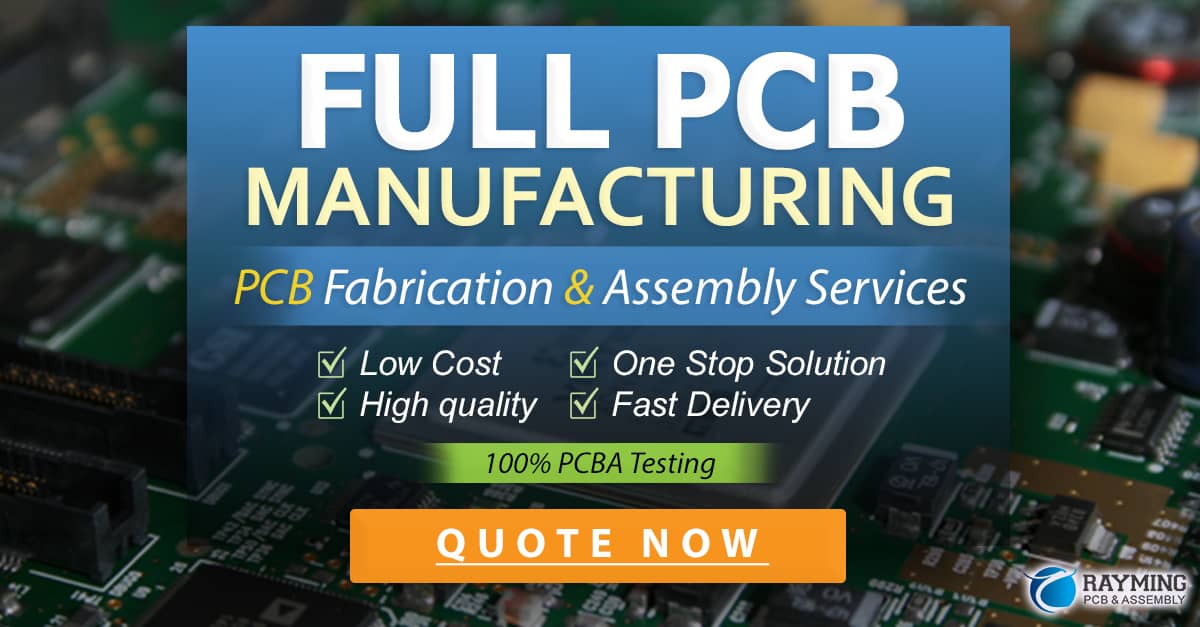
Solder Wire Diameters
Solder wire is available in a range of diameters, typically expressed in gauges (AWG) or millimeters (mm). Common diameters for electronics soldering include:
- 0.5mm (24 AWG)
- 0.6mm (22 AWG)
- 0.8mm (20 AWG)
- 1.0mm (18 AWG)
Thinner wire is ideal for precise soldering of small components and fine-pitch leads, while thicker wire is better suited for soldering larger components and ground planes. It’s a good idea to have a few different diameters on hand to accommodate various soldering tasks.
Solder Paste
Solder paste is a mixture of tiny solder spheres (powder) and flux, used primarily for surface mount assembly. The solder powder is available in various alloys and particle sizes, with Type 3 (25-45 µm) and Type 4 (20-38 µm) being the most common.
Solder paste is applied to PCB Pads using stencils or dispensing needles, and components are placed on top. During reflow soldering, the paste melts, forming solder joints between the component leads and pads.
When selecting solder paste, consider factors such as alloy type, powder size, flux activity, and printing or dispensing method.
Soldering Temperature and Iron Tips
Soldering Iron Temperature
Choosing the right soldering iron temperature is crucial for achieving quality solder joints. Generally, lead-free solders require higher temperatures than Sn-Pb alloys due to their higher melting points.
Recommended temperature ranges:
– Sn-Pb solder: 315-370°C (600-700°F)
– Lead-free solder: 370-425°C (700-800°F)
Always refer to the solder manufacturer’s guidelines for specific temperature recommendations. Setting the temperature too low can result in poor wetting and weak joints, while excessive heat can damage components and PCBs.
Soldering Iron Tips
Soldering iron tips come in various shapes and sizes to suit different soldering tasks. Some common tip shapes include:
– Conical: General-purpose, suitable for most soldering tasks
– Chisel: Ideal for soldering larger components and ground planes
– Bevel: Angled tip for reaching tight spaces and SMD components
– Fine point: Precise tip for soldering small components and fine-pitch leads
Select a tip size and shape that matches the scale of your soldering work. Regularly clean and tin your tips to maintain good heat transfer and prolong tip life.
Solder Joint Inspection and Quality Control
After soldering, it’s essential to inspect the solder joints to ensure quality and reliability. Visually examine the joints for the following characteristics:
– Shiny and smooth surface
– Concave fillet shape
– Adequate wetting and coverage of component leads and PCB pads
– No bridging, icicles, or excessive solder
Use magnification aids like a microscope or loupe to closely inspect fine-pitch and SMD solder joints.
For critical applications, consider using automated optical inspection (AOI) or X-ray inspection to detect hidden defects like voids, insufficient solder, or poor wetting.
Implementing a quality control process that includes visual inspection, electrical testing, and periodic cross-sectioning of sample boards can help identify and correct soldering issues, ensuring consistently high-quality solder joints.
Soldering Safety and Best Practices
Soldering involves high temperatures and exposure to fumes, so it’s crucial to follow safety guidelines and best practices:
- Work in a well-ventilated area or use a fume extractor to minimize exposure to flux fumes.
- Wear protective eyewear to shield your eyes from solder splatter and debris.
- Use a soldering iron with an ESD-safe handle to prevent damage to sensitive components.
- Keep your soldering iron in a stand when not in use, and never touch the tip or leave it unattended.
- Clean your soldering iron tip regularly with a damp sponge or brass wool to remove oxidation and buildup.
- Apply heat to both the component lead and PCB pad simultaneously to ensure even heat distribution and good wetting.
- Use just enough solder to create a strong, reliable joint without excessive buildup.
- Allow solder joints to cool naturally; avoid blowing on them or moving the components prematurely.
By following these safety guidelines and best practices, you can create high-quality solder joints while minimizing the risk of injury or damage to your components and PCBs.
FAQ
-
Q: What is the best solder alloy for general-purpose electronics soldering?
A: For most general-purpose electronics soldering, lead-free alloys like SAC305 (96.5% Sn, 3.0% Ag, 0.5% Cu) or Sn99.3Cu0.7 (99.3% Sn, 0.7% Cu) are excellent choices. They provide good wetting, strong mechanical bonds, and reliable electrical connections. -
Q: Can I use lead-free solder on old PCBs designed for Sn-Pb solder?
A: Yes, you can use lead-free solder on PCBs originally designed for Sn-Pb solder. However, keep in mind that lead-free solders require higher soldering temperatures, so be cautious not to damage heat-sensitive components. Additionally, ensure that the PCB surface finishes and component coatings are compatible with lead-free solders. -
Q: What is the difference between rosin core and solid wire solder?
A: Rosin core solder wire has a hollow center filled with flux, which helps clean and prepare the surfaces for soldering, improving wetting and joint quality. Solid wire solder does not contain flux and is typically used with separate flux application or for solder and tinning applications that don’t require flux. -
Q: How do I choose the right solder wire diameter?
A: The choice of solder wire diameter depends on the scale of your soldering work. Thinner wire (0.5-0.6mm) is ideal for precise soldering of small components and fine-pitch leads, while thicker wire (0.8-1.0mm) is better suited for soldering larger components and ground planes. It’s a good idea to have a few different diameters on hand to accommodate various soldering tasks. -
Q: What should I do if my solder joints look dull or grainy?
A: Dull or grainy solder joints can indicate poor wetting, insufficient heat, or contamination. To correct this, ensure your soldering iron is set to the appropriate temperature for the solder alloy you’re using. Clean the component leads and PCB pads before soldering, and apply heat evenly to both surfaces. If the problem persists, check your solder for contamination or use a more active flux to improve wetting.
Conclusion
Selecting the best solder for your circuit board project involves considering factors like alloy composition, flux type, wire diameter, and soldering temperature. By understanding the properties and characteristics of different solder alloys, flux cores, and wire sizes, you can make an informed decision that ensures strong, reliable solder joints.
Remember to prioritize safety and follow best practices while soldering, such as working in a well-ventilated area, using appropriate personal protective equipment, and maintaining your soldering iron and tips.
With the knowledge gained from this comprehensive guide on solder selection, you’re well-equipped to choose the best solder for your specific application and achieve high-quality, long-lasting solder connections in your PCB assembly and electronics manufacturing projects.
0 Comments