What is Lead-free Solder?
Lead-free solder is an alloy used in electronic assembly that does not contain lead (Pb) as a primary constituent. The development of lead-free solders was driven by the need to reduce the environmental and health risks associated with lead exposure. Lead-free solders typically consist of tin (Sn) as the primary component, along with various other metals such as silver (Ag), copper (Cu), bismuth (Bi), indium (In), and antimony (Sb).
Advantages of Lead-free Solder
- Reduced environmental impact
- Improved health and safety for electronics workers
- Compliance with international regulations (e.g., RoHS, WEEE)
- Potential for better mechanical properties and reliability
Common Lead-free Solder Compositions
Tin-Silver-Copper (SAC) Alloys
SAC alloys are the most widely used lead-free solders in the electronics industry. The typical composition of SAC alloys is:
- Tin (Sn): 95.5-96.5%
- Silver (Ag): 3.0-4.0%
- Copper (Cu): 0.5-1.0%
Some common SAC alloy designations include:
Alloy | Tin (Sn) | Silver (Ag) | Copper (Cu) |
---|---|---|---|
SAC305 | 96.5% | 3.0% | 0.5% |
SAC387 | 95.5% | 3.8% | 0.7% |
SAC405 | 95.5% | 4.0% | 0.5% |
SAC alloys offer several advantages, including:
- Good mechanical strength and reliability
- Excellent wetting properties
- Wide availability and relatively low cost
However, SAC alloys have higher melting points (217-220°C) compared to traditional lead-based solders, which can present challenges in certain applications.
Tin-Silver (SnAg) Alloys
SnAg alloys are another common lead-free solder composition, typically consisting of:
- Tin (Sn): 96.5-97.5%
- Silver (Ag): 2.5-3.5%
SnAg alloys have a slightly lower melting point than SAC alloys (221-226°C) and offer good mechanical properties. However, they may be more expensive due to the higher silver content.
Tin-Bismuth (SnBi) Alloys
SnBi alloys are low-temperature lead-free solders, with compositions typically ranging from:
- Tin (Sn): 42-58%
- Bismuth (Bi): 58-42%
The most common SnBi alloy is eutectic Sn42Bi58, which has a melting point of 138°C. SnBi alloys are useful for low-temperature applications and are compatible with heat-sensitive components. However, they have lower mechanical strength and are more prone to brittleness compared to other lead-free solders.
Tin-Copper (SnCu) Alloys
SnCu alloys are cost-effective lead-free solders, with a typical composition of:
- Tin (Sn): 99.3%
- Copper (Cu): 0.7%
Eutectic Sn99.3Cu0.7 has a melting point of 227°C and offers good mechanical properties. However, SnCu alloys have poorer wetting properties compared to SAC and SnAg alloys.
Properties of Lead-free Solders
When selecting a lead-free solder for a specific application, several properties must be considered:
Melting Point
The melting point of a solder determines the temperature required for the soldering process. Lead-free solders generally have higher melting points than lead-based solders, which can present challenges in terms of energy consumption and potential damage to heat-sensitive components.
Solder Alloy | Melting Point Range (°C) |
---|---|
SAC305 | 217-220 |
SnAg3.5 | 221-226 |
Sn99.3Cu0.7 | 227 |
Sn42Bi58 | 138 |
Wetting Properties
Wetting refers to the ability of molten solder to spread and adhere to the surfaces being joined. Good wetting properties are essential for forming reliable solder joints. SAC and SnAg alloys generally have excellent wetting properties, while SnCu alloys have poorer wetting performance.
Mechanical Strength
The mechanical strength of a solder joint is critical for the reliability and durability of the electronic assembly. Lead-free solders should have sufficient strength to withstand the stresses and strains encountered during the product’s lifecycle. SAC and SnAg alloys offer good mechanical strength, while SnBi alloys are more prone to brittleness.
Thermal Fatigue Resistance
Electronic assemblies are subjected to thermal cycling during operation, which can lead to solder joint fatigue and failure. Lead-free solders must have adequate resistance to thermal fatigue to ensure long-term reliability. SAC alloys have demonstrated good thermal fatigue resistance in various studies.
Compatibility with Surface Finishes
Lead-free solders must be compatible with the surface finishes used on printed circuit boards (PCBs) and component leads. Common surface finishes include:
- Immersion tin (ImSn)
- Immersion silver (ImAg)
- Electroless nickel immersion gold (ENIG)
- Organic solderability preservatives (OSP)
SAC and SnAg alloys are generally compatible with most surface finishes, while SnBi alloys may have compatibility issues with some finishes.
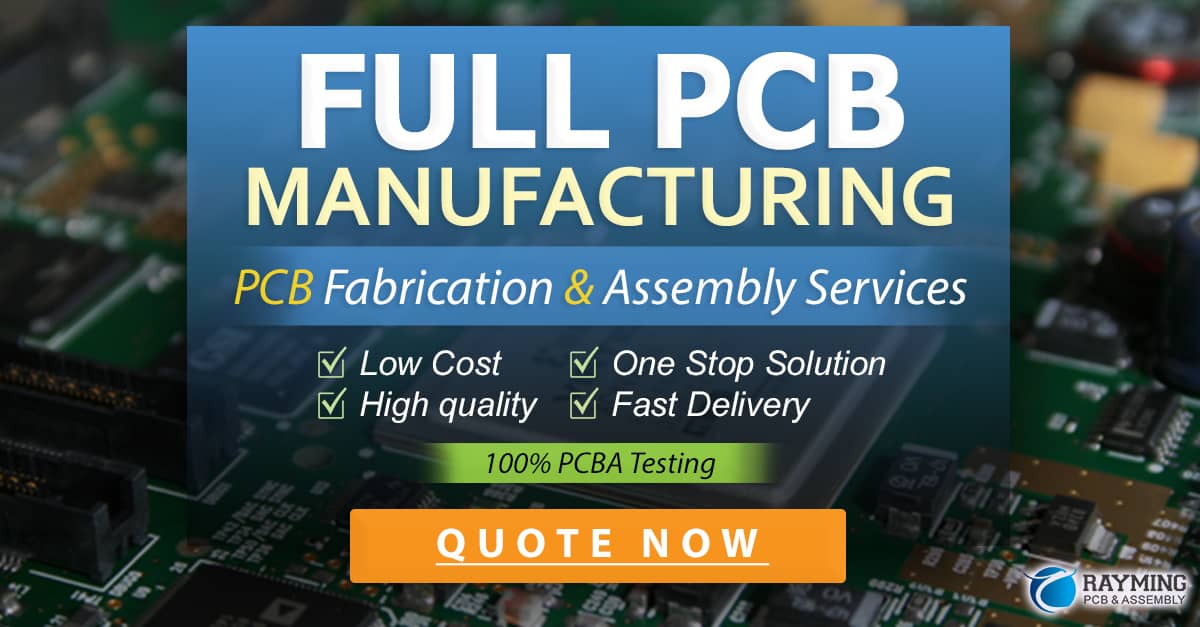
Applications of Lead-free Solders
Lead-free solders are used in a wide range of electronic applications, including:
- Consumer electronics (e.g., smartphones, laptops, televisions)
- Automotive electronics
- Industrial equipment
- Medical devices
- Aerospace and defense systems
The choice of lead-free solder composition depends on the specific requirements of the application, such as operating temperature, reliability, and cost constraints.
Challenges and Future Developments
Despite the widespread adoption of lead-free solders, several challenges remain:
- Higher processing temperatures and energy consumption
- Potential for tin whisker formation
- Compatibility issues with certain surface finishes and components
- Need for improved thermal fatigue resistance in high-reliability applications
Researchers and industry experts continue to develop new lead-free solder compositions and processing techniques to address these challenges. Some areas of focus include:
- Low-temperature lead-free solders for heat-sensitive components
- Doped SAC alloys with improved mechanical properties and thermal fatigue resistance
- Alternative soldering methods, such as laser soldering and ultrasonic soldering
- Advanced testing and reliability assessment techniques
As the electronics industry evolves, lead-free solder compositions will continue to play a crucial role in ensuring the performance, reliability, and environmental sustainability of electronic assemblies.
Frequently Asked Questions (FAQ)
-
Q: Why is lead-free solder important?
A: Lead-free solder is important because it reduces the environmental and health risks associated with lead exposure. Lead is a toxic metal that can cause adverse health effects, particularly in children. Additionally, lead-free solders help manufacturers comply with international regulations, such as the Restriction of Hazardous Substances (RoHS) directive. -
Q: What are the most common lead-free solder compositions?
A: The most common lead-free solder compositions are tin-silver-copper (SAC) alloys, tin-silver (SnAg) alloys, tin-bismuth (SnBi) alloys, and tin-copper (SnCu) alloys. SAC alloys, particularly SAC305 and SAC387, are the most widely used in the electronics industry. -
Q: What are the advantages of using SAC alloys?
A: SAC alloys offer several advantages, including good mechanical strength and reliability, excellent wetting properties, and wide availability. They have become the primary choice for lead-free soldering in many electronic applications due to their balance of performance and cost. -
Q: What challenges are associated with lead-free solders?
A: Lead-free solders present some challenges, such as higher processing temperatures and energy consumption compared to lead-based solders. They may also be more prone to tin whisker formation and have compatibility issues with certain surface finishes and components. Additionally, some lead-free solders may have lower thermal fatigue resistance in high-reliability applications. -
Q: How can I select the appropriate lead-free solder for my application?
A: When selecting a lead-free solder, consider the specific requirements of your application, such as operating temperature, reliability, and cost constraints. Evaluate the properties of different lead-free solder compositions, including melting point, wetting properties, mechanical strength, and compatibility with surface finishes. Consult with solder suppliers, industry experts, and refer to relevant standards and guidelines to make an informed decision.
0 Comments