Introduction to PCB Pads
PCB pads, also known as land patterns or footprints, are the exposed metal surfaces on a printed circuit board (PCB) where electronic components are soldered. They provide electrical and mechanical connections between the component leads and the copper traces on the PCB. Pads come in various shapes, sizes, and configurations to accommodate different types of components and mounting techniques.
Types of PCB Pads
There are several types of PCB pads, each designed for specific component packages and soldering methods:
- Surface Mount Pads: These pads are used for surface-mount devices (SMDs) such as resistors, capacitors, and integrated circuits. They are flat and have no drilled holes. Common surface mount pad shapes include:
- Rectangular pads for chip components
- Gull-wing pads for QFP and SOIC packages
- J-lead pads for PLCC packages
-
Ball Grid Array (BGA) pads for BGA packages
-
Through-Hole Pads: These pads have drilled holes that allow component leads to pass through the board. They are used for through-hole components such as axial and radial lead resistors, capacitors, and DIP packages. The holes are plated with copper to create a conductive path between the top and bottom layers of the PCB.
-
Mixed Technology Pads: Some PCBs use a combination of surface mount and through-hole components. In such cases, mixed technology pads are used, which have both flat surfaces for SMDs and drilled holes for through-hole components.
-
Castellated Pads: These pads are used for edge-connector applications, such as connecting a module to a main board. They have half-drilled holes along the edge of the PCB, allowing for easy soldering and mechanical strength.
-
Thermal Pads: These pads are designed to dissipate heat from power-hungry components such as voltage regulators and power transistors. They have a larger surface area and are often connected to copper pours or thermal vias to enhance heat transfer.
Pad Dimensions and Spacing
The dimensions and spacing of PCB pads are critical for ensuring proper component placement, soldering, and reliability. Some key considerations include:
-
Pad Size: The pad size should be large enough to accommodate the component lead and provide sufficient area for soldering. However, oversized pads can lead to increased capacitance and signal integrity issues. The pad size is typically specified in the component datasheet or land pattern recommendation.
-
Pad Spacing: The spacing between pads should be sufficient to prevent short circuits and allow for proper soldering. The minimum spacing depends on factors such as the PCB manufacturing process, solder mask alignment, and the type of components used.
-
Solder Mask Openings: Solder mask is a protective coating applied to the PCB, leaving only the pads exposed. The solder mask opening should be slightly larger than the pad to ensure proper solder wetting and prevent solder bridging.
-
Copper to Mask Clearance: This is the distance between the edge of the pad and the solder mask opening. It should be large enough to account for solder mask alignment tolerances and prevent the solder mask from encroaching on the pad.
Here’s a table summarizing typical pad dimensions and spacing for common component packages:
Package Type | Pad Width (mm) | Pad Length (mm) | Pad Spacing (mm) |
---|---|---|---|
0402 | 0.5 | 0.5 | 0.5 |
0603 | 0.7 | 0.9 | 0.8 |
0805 | 1.0 | 1.2 | 1.0 |
1206 | 1.5 | 1.8 | 1.2 |
SOIC-8 | 0.6 | 2.0 | 1.27 |
TQFP-44 | 0.4 | 1.2 | 0.8 |
PCB Pad Design Considerations
When designing PCB pads, several factors must be taken into account to ensure optimal performance, manufacturability, and reliability:
Solderability
Solderability refers to the ability of the PCB pads to form a strong and reliable solder joint with the component leads. To enhance solderability, consider the following:
-
Pad Finish: The pad surface finish affects solderability. Common finishes include hot air solder leveling (HASL), immersion silver, immersion tin, and electroless nickel immersion gold (ENIG). Each finish has its advantages and limitations in terms of cost, shelf life, and compatibility with different soldering processes.
-
Solder Mask Design: The solder mask opening should be larger than the pad to allow for proper solder wetting. However, excessive solder mask openings can lead to solder bridging and shorts. A typical solder mask expansion is 0.05 to 0.1 mm per side.
-
Solder Paste Stencil Design: For surface mount components, solder paste is applied to the pads using a stencil. The stencil aperture size and shape should be optimized to deliver the right amount of solder paste and prevent bridging or insufficient solder joints.
Thermal Management
Power dissipation and thermal management are critical for PCBs with high-power components. Proper pad design can help dissipate heat and prevent component overheating:
-
Thermal Pad Size: Larger thermal pads provide more surface area for heat dissipation. The pad size should be calculated based on the component’s power dissipation and the PCB’s thermal properties.
-
Thermal Vias: Thermal vias are plated holes that transfer heat from the thermal pad to the opposite side of the PCB or to internal copper layers. They increase the effective thermal conductivity of the pad and help spread the heat more efficiently.
-
Copper Pour: Connecting the thermal pad to a large copper pour or plane can further enhance heat dissipation. The copper pour acts as a heat sink, spreading the heat over a larger area.
Signal Integrity
Pad design can impact signal integrity, especially for high-speed and high-frequency circuits. Some key considerations include:
-
Pad Capacitance: The pad-to-ground capacitance can affect signal quality and cause reflections. Minimizing the pad size and increasing the distance to ground planes can reduce pad capacitance.
-
Impedance Matching: For differential pairs and controlled impedance lines, the pad geometry should be designed to maintain the desired characteristic impedance. This may involve adjusting the pad width, length, and spacing.
-
Via Placement: Vias should be placed close to the pads to minimize the loop area and reduce inductance. However, vias too close to the pads can interfere with soldering and cause manufacturing issues.
Manufacturing Considerations
PCB pad design must also account for manufacturing tolerances and processes to ensure high yields and reliability:
-
Pad-to-Hole Ratio: For through-hole pads, the pad diameter should be larger than the hole diameter to allow for proper plating and solder wicking. A typical pad-to-hole ratio is 1.8:1 or greater.
-
Annular Ring: The annular ring is the copper area between the hole and the edge of the pad. It should be wide enough to account for drilling tolerances and prevent breakout. A minimum annular ring of 0.15 to 0.2 mm is common.
-
Solder Mask Alignment: The solder mask opening should be aligned with the pad to ensure proper solder wetting and prevent solder mask encroachment. A solder mask alignment tolerance of 0.05 to 0.1 mm is typical.
-
Pad Spacing: The spacing between pads should be sufficient to prevent solder bridging and allow for proper solder mask application. The minimum spacing depends on the PCB manufacturing process and the component package.
PCB Pad Layout Guidelines
When laying out PCB pads, follow these guidelines to ensure optimal performance and manufacturability:
-
Component Orientation: Orient components to minimize the trace lengths and avoid crossing traces. For polarized components, ensure the correct orientation to prevent reverse polarity.
-
Pad Placement: Place pads to allow for easy component placement and soldering. Avoid placing pads too close to the board edge or other components, which can interfere with assembly and inspection.
-
Trace Routing: Route traces to minimize the distance between the pads and the connected components. Avoid sharp angles and use smooth curves to prevent signal reflections and manufacturing issues.
-
Ground Planes: Use ground planes to provide a low-impedance return path for signals and to shield sensitive circuits from interference. Connect pads to the ground plane using vias where necessary.
-
Solder Mask and Silkscreen: Apply solder mask to the PCB to protect the traces and prevent solder bridging. Use silkscreen to label components and provide assembly instructions.
-
Design Rule Check (DRC): Perform a DRC to verify that the pad layout meets the manufacturing and design rules specified by the PCB fabrication vendor. This includes checking for minimum pad sizes, spacings, and solder mask openings.
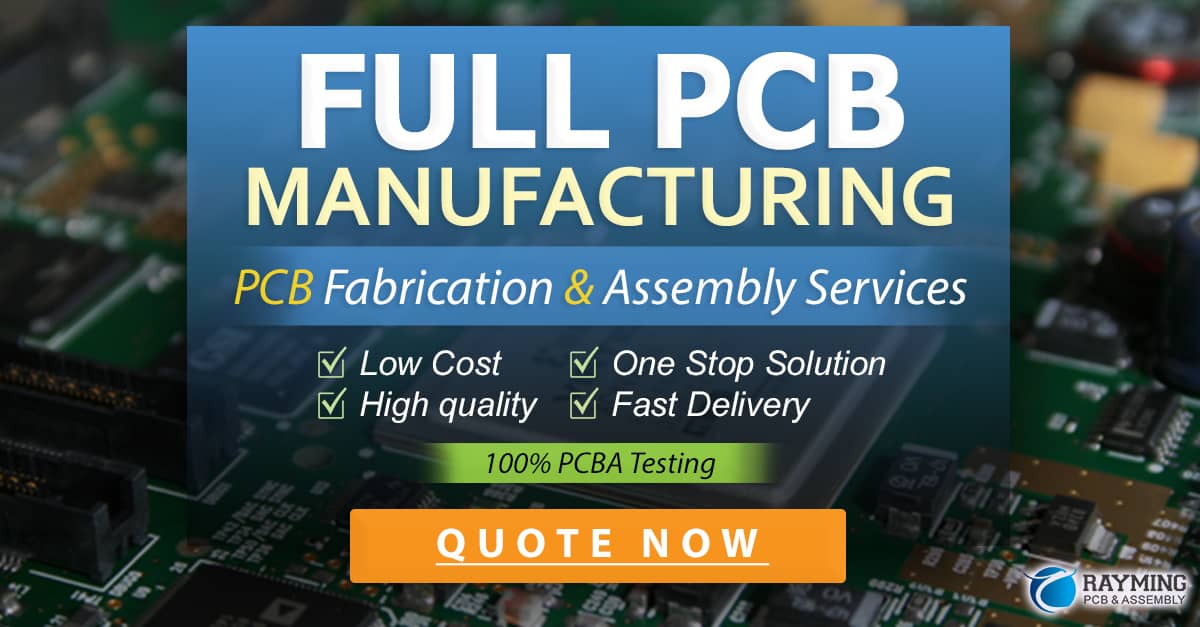
FAQ
1. What is the difference between a pad and a via?
A pad is an exposed metal surface on a PCB where components are soldered, while a via is a plated hole that connects traces on different layers of the PCB. Pads are used for component mounting, while vias are used for electrical connections between layers.
2. Can I use the same pad size for all components?
No, pad sizes vary depending on the component package and the PCB manufacturing process. Consult the component datasheet or land pattern recommendation for the appropriate pad size and spacing.
3. What is the purpose of solder mask on PCB pads?
Solder mask is a protective coating applied to the PCB that leaves only the pads exposed. It prevents solder bridging, protects the traces from oxidation and corrosion, and provides electrical insulation between adjacent pads.
4. How do I determine the thermal pad size for a power component?
The thermal pad size depends on the component’s power dissipation and the PCB’s thermal properties. Use the component datasheet and thermal resistance calculations to determine the required pad size for efficient heat dissipation.
5. What is the minimum pad spacing for a typical PCB?
The minimum pad spacing depends on the PCB manufacturing process and the component package. For standard PCBs, a minimum spacing of 0.2 to 0.3 mm is common. However, consult with your PCB fabrication vendor for their specific design rules and tolerances.
Conclusion
PCB pads are essential elements in electronic circuit design, providing electrical and mechanical connections between components and the PCB. Proper pad design ensures optimal performance, manufacturability, and reliability of the assembled PCB.
When designing PCB pads, consider factors such as solderability, thermal management, signal integrity, and manufacturing tolerances. Follow the component datasheets and land pattern recommendations, and adhere to the design rules specified by the PCB fabrication vendor.
By understanding the types, dimensions, and layout guidelines for PCB pads, designers can create robust and efficient PCBs that meet the requirements of their electronic products.
0 Comments