Understanding Solder Escape and Its Impact on PCB Assembly
Solder escape, also known as Solder Wicking, is a common issue encountered during the Reflow Soldering process in PCB assembly. It occurs when molten solder flows away from the intended joint, often along the component leads or traces, resulting in inadequate solder volume and potentially compromising the reliability of the solder joint. This phenomenon can lead to various problems, such as weak joints, open circuits, and even short circuits if the escaped solder bridges adjacent connections.
Causes of Solder Escape
Several factors contribute to the occurrence of solder escape during reflow:
-
Inadequate solder mask coverage: If the solder mask does not sufficiently cover the areas surrounding the solder pads, molten solder can flow along the exposed copper traces or component leads.
-
Inappropriate solder paste volume: Applying too much solder paste can cause excess solder to flow away from the joint during reflow.
-
Incorrect reflow profile: An improper reflow temperature profile, such as excessive peak temperature or prolonged time above liquidus, can exacerbate solder escape.
-
Contamination: Presence of contaminants like flux residues or oxidation on the PCB surface can hinder proper solder wetting and encourage solder escape.
Impact of Solder Escape on PCB Assembly
Solder escape can have several detrimental effects on the quality and reliability of PCB assemblies:
-
Weak solder joints: Insufficient solder volume at the intended joint due to solder escape can result in weak or unreliable connections.
-
Open circuits: If too much solder escapes from the joint, it may lead to an open circuit, preventing electrical continuity.
-
Short circuits: Escaped solder can bridge adjacent pads or traces, causing short circuits and potentially damaging the PCB or connected components.
-
Rework and repair: Solder escape often necessitates rework or repair, which can be time-consuming and costly, especially in high-volume production.
Preventive Measures to Minimize Solder Escape
To minimize the occurrence of solder escape during reflow, several preventive measures can be implemented:
1. PCB Design Considerations
Proper PCB design plays a crucial role in preventing solder escape. Consider the following design aspects:
-
Solder mask design: Ensure adequate solder mask coverage around the solder pads to prevent solder from flowing along exposed copper traces. Maintain appropriate solder mask clearance and alignment with the pads.
-
Pad size and shape: Optimize pad dimensions and shapes to promote proper solder wetting and containment. Avoid excessively large or irregularly shaped pads that can encourage solder escape.
-
Trace routing: Route traces away from the solder pads to minimize the risk of solder flowing along them. Maintain sufficient spacing between traces and pads.
-
Component selection: Choose components with lead styles and pitches that are compatible with the PCB design and reflow process to minimize solder escape risk.
2. Solder Paste Printing Process
The solder paste printing process significantly influences the occurrence of solder escape. Consider the following factors:
-
Stencil design: Use a well-designed stencil with appropriate aperture sizes and shapes to deposit the correct amount of solder paste on the pads. Avoid overly large or small apertures that can lead to excessive or insufficient solder volume.
-
Solder paste selection: Choose a solder paste with suitable rheological properties, such as viscosity and tackiness, to ensure proper deposition and minimize slumping or spreading.
-
Printer setup: Optimize the printer settings, including squeegee pressure, speed, and separation distance, to achieve consistent and accurate solder paste deposition.
-
Stencil cleaning: Regularly clean the stencil to prevent paste buildup and contamination, which can affect the print quality and contribute to solder escape.
3. Reflow Profile Optimization
An optimized reflow profile is essential to minimize solder escape. Consider the following aspects:
-
Peak temperature: Set the peak temperature according to the solder paste specifications and PCB assembly requirements. Avoid excessively high peak temperatures that can cause solder to become too fluid and escape.
-
Time above liquidus (TAL): Control the duration of time the solder remains in a molten state above its liquidus temperature. Prolonged TAL can increase the risk of solder escape.
-
Ramp rates: Adjust the ramp rates during heating and cooling to allow for proper solder wetting and solidification. Rapid ramp rates can cause uneven heating and encourage solder escape.
-
Atmosphere control: Use nitrogen or another inert atmosphere during reflow to minimize oxidation and improve solder wetting, reducing the likelihood of solder escape.
4. Cleaning and Contamination Control
Maintaining a clean PCB surface and controlling contamination are crucial for preventing solder escape. Consider the following practices:
-
Pre-assembly cleaning: Clean the PCB prior to solder paste printing to remove any contaminants, such as flux residues or oxidation, that can hinder proper solder wetting.
-
Flux selection: Choose a compatible flux chemistry that promotes good solder wetting and minimizes residues. Avoid overly active or corrosive fluxes that can contribute to solder escape.
-
Environment control: Maintain a controlled environment with appropriate temperature, humidity, and cleanliness levels to prevent contamination and ensure consistent reflow results.
-
Post-reflow cleaning: If necessary, perform post-reflow cleaning to remove any remaining flux residues or contaminants that may affect the solder joint quality.
Inspection and Quality Control
Implementing robust inspection and quality control measures helps identify and address solder escape issues promptly. Consider the following techniques:
1. Visual Inspection
Perform visual inspection of the PCB assembly after reflow to identify any instances of solder escape. Look for:
- Insufficient solder volume at the intended joints
- Solder bridging between adjacent pads or traces
- Solder flowing along component leads or exposed copper traces
Visual inspection can be performed manually or using automated optical inspection (AOI) systems for higher throughput and accuracy.
2. X-ray Inspection
For components with hidden solder joints, such as ball grid arrays (BGAs) or chip-scale packages (CSPs), X-ray inspection can provide valuable insights into solder escape issues. X-ray imaging allows for the examination of solder joint quality, including voids, insufficient solder, or solder escape beneath the components.
3. Electrical Testing
Perform electrical testing, such as in-circuit testing (ICT) or functional testing, to verify the electrical integrity of the solder joints. Solder escape can manifest as open or short circuits, which can be detected through comprehensive electrical testing.
4. Cross-Sectioning
In critical applications or for failure analysis, cross-sectioning of the solder joints can provide detailed information about the solder escape phenomenon. By examining the cross-sectioned samples under a microscope, the extent and nature of solder escape can be assessed, helping to identify the root cause and implement corrective actions.
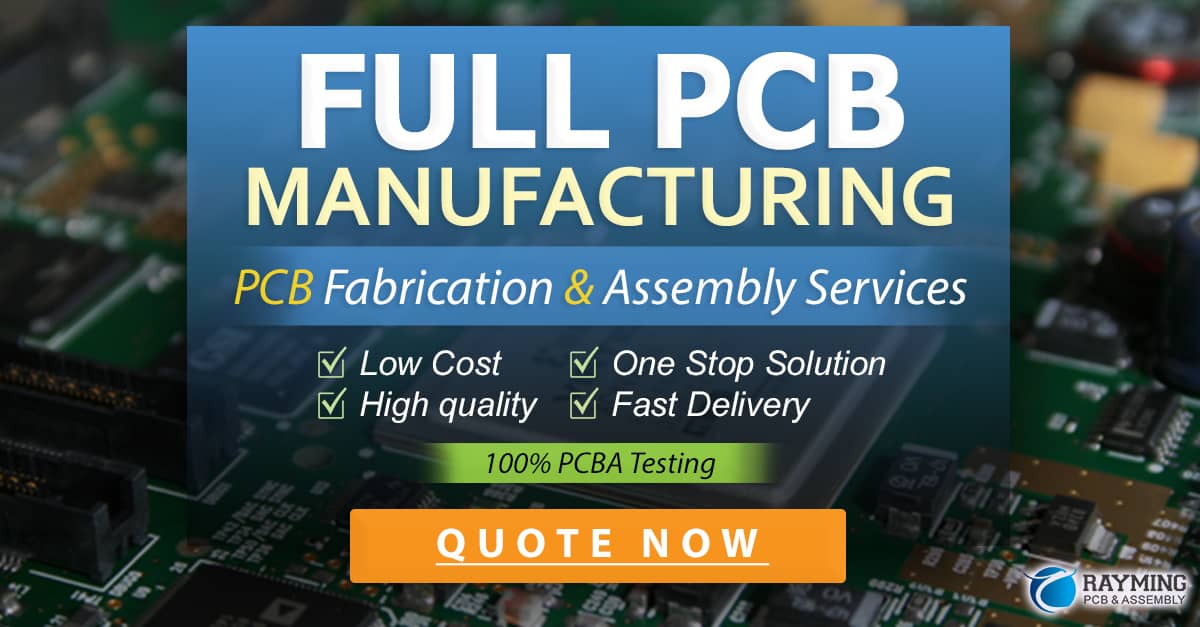
Rework and Repair Techniques
When solder escape is detected, rework or repair may be necessary to rectify the issue and ensure the reliability of the solder joints. Consider the following techniques:
1. Solder Wicking
Solder wicking involves using a soldering iron and copper braid or solder wick to remove the excess solder from the affected area. The soldering iron heats the wick, which then absorbs the molten solder through capillary action. This technique can be effective for removing solder bridges or excess solder from exposed areas.
2. Solder Paste Addition
If insufficient solder volume is present at the joint due to solder escape, adding solder paste can help restore the proper solder volume. Apply a controlled amount of solder paste to the affected area and perform localized reflow using a hot air pencil or soldering iron.
3. Component Replacement
In some cases, the component may need to be removed and replaced to address solder escape issues effectively. This involves desoldering the affected component, cleaning the pads, and soldering a new component in its place. Proper desoldering techniques, such as using a desoldering station or hot air rework system, should be employed to minimize damage to the PCB.
4. Selective Soldering
For localized solder escape issues, selective soldering can be used to reflow the affected area without disturbing the surrounding components. Selective soldering systems allow precise control over the heating and soldering process, enabling targeted rework of specific joints.
Best Practices and Process Improvement
To continuously improve the soldering process and minimize solder escape occurrence, consider the following best practices:
-
Regular equipment maintenance: Ensure that the reflow oven, solder paste printer, and other equipment are properly maintained and calibrated to ensure consistent performance.
-
Process monitoring and control: Implement process monitoring and control systems to track key parameters, such as reflow temperature profiles, solder paste printing quality, and component placement accuracy. Use statistical process control (SPC) techniques to identify trends and take corrective actions.
-
Training and skill development: Provide adequate training to operators and technicians involved in the soldering process. Ensure they are knowledgeable about solder escape prevention techniques and can identify and address issues promptly.
-
Continuous improvement initiatives: Foster a culture of continuous improvement by encouraging team members to identify opportunities for process optimization and implement changes that reduce solder escape occurrence.
-
Collaboration and communication: Promote collaboration and communication among design, process, and quality teams to address solder escape issues holistically. Regularly review and discuss solder escape data, root causes, and preventive measures to drive improvement across the organization.
Frequently Asked Questions (FAQ)
-
What is solder escape, and why is it a concern in PCB assembly?
Solder escape, also known as solder wicking, is a phenomenon where molten solder flows away from the intended joint along component leads or PCB Traces during the reflow soldering process. It is a concern because it can result in insufficient solder volume at the joint, leading to weak or unreliable connections, open circuits, or even short circuits if the escaped solder bridges adjacent connections. -
What are the main causes of solder escape?
The main causes of solder escape include inadequate solder mask coverage, inappropriate solder paste volume, incorrect reflow profile, and contamination on the PCB surface. These factors can contribute to molten solder flowing away from the intended joint and causing solder escape issues. -
How can PCB design help prevent solder escape?
PCB design plays a crucial role in preventing solder escape. Proper solder mask design with adequate coverage around solder pads, optimized pad sizes and shapes, strategic trace routing, and appropriate component selection can all help minimize the risk of solder escape. By considering these design aspects, the likelihood of solder flowing along exposed copper traces or component leads can be reduced. -
What are some preventive measures to minimize solder escape during the solder paste printing process?
To minimize solder escape during solder paste printing, consider the following measures: - Use a well-designed stencil with appropriate aperture sizes and shapes to deposit the correct amount of solder paste.
- Select a solder paste with suitable rheological properties to ensure proper deposition and minimize slumping or spreading.
- Optimize printer settings, including squeegee pressure, speed, and separation distance, for consistent and accurate solder paste deposition.
-
Regularly clean the stencil to prevent paste buildup and contamination.
-
How can the reflow profile be optimized to reduce the risk of solder escape?
Optimizing the reflow profile is essential to minimize solder escape. Key considerations include: - Setting the peak temperature according to solder paste specifications and PCB assembly requirements to avoid excessively high temperatures that can cause solder to become too fluid.
- Controlling the time above liquidus (TAL) to prevent prolonged exposure to molten solder, which can increase the risk of solder escape.
- Adjusting ramp rates during heating and cooling to allow for proper solder wetting and solidification.
- Using nitrogen or another inert atmosphere during reflow to minimize oxidation and improve solder wetting.
By understanding the causes, implementing preventive measures, and adopting best practices, the occurrence of solder escape can be significantly reduced, leading to improved PCB assembly quality and reliability.
0 Comments